
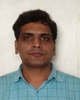
- Open Access
- Authors : Jaslok Pandey , Pranav Solanki
- Paper ID : IJERTV10IS060021
- Volume & Issue : Volume 10, Issue 06 (June 2021)
- Published (First Online): 07-06-2021
- ISSN (Online) : 2278-0181
- Publisher Name : IJERT
- License:
This work is licensed under a Creative Commons Attribution 4.0 International License
Scope of Smart Materials in Future
Mr. Jaslok Pandey
Professor and HOD,
Mechanical Department Saraswati Institute of Technology, Navi Mumbai, Kharghar
Mr. Pranav Solanki
Saraswati institute of Technology, Navi Mumbai, Kharghar.
Abstract- Future developments of smart materials for domains such as self-sustainable wireless sensor networks, self-tuned vibration energy harvesting devices, seismic applications etc. is the need of an hour. Such smart materials have the potential to build smart structures and materials. Smart materials are stimuli-responsive which constituted a broad range of materials to exploit vibration control such as piezoelectric, shape memory alloys, electro-rheological fluid and magneto-rheological fluid. Smart materials show a certain amount of analogy with respect to biological systems. For instance, piezoelectric hydrophones that show similarity as that of ears with which fish senses vibrations, piezoelectric with an amalgamation of electromechanical coupling, shape-memory materials with a potential to recollect the original shape and electro-rheological fluids with manipulative viscosity strength etc. Such potential grabbed the attention of research and allow them to think and integrate varied advanced technologies into compact, diverse functional packages with an ultimate aim to develop advanced smart materials and revolutionize the research field of smart materials. This review initially discusses a brief summary of the aforementioned stimuli-responsive smart materials following a complete description of some of the smart materials
Index Terms- About four key words or phrases in alphabetical order, separated by commas. Keywords are used to retrieve documents in an information system such as an online journal or a search engine. (Mention 4-5 keywords)
-
INTRODUCTION
Thousands of years ago humans used materials for different causes due to which there was an enhancement in their living standards. Even civilizations were divided on the basis of their discovery of materials like the first age was the Stone Age. The most revolutionary age was the Bronze Age because bronze was more durable and harder. The discovery of bronze was the beginning of new metallurgy era after that many materials discovered. From the past two decades, science and technology have made great improvements in synthesizing the new materials. They are divided mainly into four categories which are polymers, ceramics, metals, and smart materials. Among them, smart materials are becoming more popular because they have various applications as compared to standard materials. The special materials that can change their properties such as materials which can change its shape just by adding some heat or can change its phase instantly when placed near magnet are called smart materials. This new era of smart materials will have a great impact on mankind, for example, some of them can change their properties according to the environment and some of them have sensory capabilities some of them can repair automatically and some of them have self-degradation, these extraordinary capabilities of smart materials will have an impact on all aspects of
civilization. Various smart materials already exist like piezoelectric materials, shape memory alloys, magneto- rheological materials, and electro-rheostat materials and many more to be discovered.[1] This paper concentrates on the introduction to different types of smart materials and their potential applications in various areas.
-
CLASSIFICATION OF SMART MATERIALS Smart materials are also known as advanced materials or intelligent materials. They cannot be defined by a single specific definition. They can be defined as materials that can recoil their original shape to specific stimuli, or it can be defined as advanced materials that can respond smartly to environment changes. Smart materials are categorized on the basis of their properties such as active and passive, passive smart materials have ability to transfer a type of energy e.g. optical fibers are able to transfer electromagnetic waves. Active materials are also divided in two categories first type which cannot change their properties when exposed to external stimuli e.g. photo chromatic glasses when place in sunshine they only change their colour.
The other types can alter one form of energy (thermal, electrical, chemical, mechanical, and optical) to another form
e.g. piezoelectric materials can produce an electric charge when placed to external strain[2]. They have some amazing properties that distinguished them from other materials, such as transiency: they can respond to various types of external stimulus, immediacy: the response time very less, self- actuation: this is the ability to change their appearance and shape, selectivity: the response is divided and expected, directness: response is restricted to the activating even, shape changing: material can change its shape with respect to external stimuli, self-diagnostic: they are able to detects crack on material surfaces automatically and self-healing: when damaged are capable of autonomous repair or can be repaired.
-
PIEZOELECTRIC MATERIALS
The term piezoelectricity is a blend of two terms: piezo which is a Greek term meaning pressure, and electricity, referring to electrical charges. By the application of stress or strain piezoelectric material changes the mechanical energy into electric energy and vice-versa. Similarly, piezoelectric actuators convert electrical signals into a mechanical movement which is used for adjusting mirrors, lenses and various automotive parts. The piezoelectric materials can improve the performance of the existing products [8]. The piezoelectric effect takes place in all directions and can be divided into two main effects: the direct piezoelectric effect and the inverse piezoelectric effect.
-
MAGNETO-RHEOLOGICAL FLUIDS Magneto-rheological fluids (MRFs) will change their rheological properties like stress and viscosity on the application of the magnetic field. MRFs are also called magneto-sensitive smart materials [13]. Magneto-rheological elastomers (MREs) are a rubber-like soft particle whose mechanical properties can be changed on the application of a magnetic field. MREs contain basic components: magnetic particles, nonmagnetic elastic matrices, and additives. Viscous properties of these materials can be altered by changing the magnetic field. MRFs are used in damper, clutch and buffer etc. MREs are widely used in adaptively tuned vibration absorber. Carbonyl iron is used to prepare MRF due to high saturation magnetization. Some of the properties of MRFs are: visco-elastic in nature, magnetic property, light in weight, controllable modulus and excellent sound-absorbing.
-
ELECTRO-RHEOLOGICAL FLUIDS {ERF} This Electro-rheological fluid (ERF) is the suspension of very small particles in electrical insulating fluid when the electric field is applied, they will rapidly form a solid-like structure in the direction of field. They will form return from one state to another i.e., gel state to liquid and vice versa on the application of an electric field. There are various applications of ERFs in vibration isolators, the automotive industry, shock absorber, clutch. They are also used in building base-isolation and electro-active actuators due to their ability to overcome defects caused by particle aggregation and sedimentation that affects the electro-rheological performance of ERFs building base-isolation and electro-active actuators because they can overcome the defects due to particle aggregation and sedimentatio that adepts the electro-rheological performance
of ERFs. Some properties of electro-rheological fluids are: they are stiff, damping coefficient is changed in the electric field, high dielectric constant, interfacial bond strength, constable rheology and dielectric in nature.
-
OPTICAL FIBRES
A flexible and transparent fiber which is made by drawing glass/plastic to a diameter slightly thicker than the diameter of the human hair is called the optical fiber. Optical fibers are used quite often to transmit the light between the ends of the fiber. They are used widely in fiber-optic communications. Mechanical blades, shafts, and civil structures are some of the structures which are to be monitored for the variations in strain due to cracks and damages. The most used smart materials for structural health monitoring (SHM) are fiber- optic sensors and piezoelectric wafer active sensor. Fiber Bragg grating (FBG) and fiber-optic polarimetric sensor (FOPS) are the two fiber-optic sensors which have been researched the most in the last around 20 years. FBGs are used for local strain measurement. FBG sensors are the one which can be easily can be easily embedded into the composite structures for structural health monitoring. The small-diameter FBG has been developed recently in order to measure the internal strain fields which are non- homogeneous. Strain in the whole length of a structure measured by FOPS. The increased strain Due to the damage/crack in a structure, the strain increases which is sensed by FOPS regardless of the location of the damage in the in the structure. Damages in various structures are monitored by the FOPS globally. However, FOPS is not able to find the location of the damage. Optical fiber can be used to transmit the power with the help of a solar cell. Optical fibers can be used in medical and other applications as light guides. For illumination in decorative applications such as signs toys etc., optical fiber lamps can be used.
-
SHAPE MEMORY ALLOY {SMA}
Shape memory alloy (SMA) is a very common example of smart material. These materials can change in any shape with variation in temperature, the one specification which makes it different from other materials is that it can remember its original shape when subjected to external stimuli i.e., stress. They are also referred to as intelligent materials. These shape
changes occur between two phase marten sites to austenite. Martensite phase is stable at lower temperature and the austenite phase is stable at a higher temperature. Occurrence of these thermo mechanical properties of SMAs is due to reversible solidsolid phase transformation governed by temperature and mechanical stress. The phases are austenite and marten site with reference to the phase transformation occurring in steels. Super elasticity can recover from large elastic strains (up to 8%) also permits the material to resist large cyclic deformations, without residual strains. due to these immanent wonderful properties. Nickel-titanium alloy is the most effective and common type of shape-memory alloy which has the titanium content of 45 50%. The commercially available nickel-titanium alloys are traded under the brand- name of Nitinol. Some of the most notable nontitanium alloys which also have the shape-memory properties are copper zincaluminium and copperaluminiumnickel alloys. However, they have the lower shape-memory performance and mechanical properties as compared to those of the nickel titanium alloys. SMAs are a class of novel materials that display two effects: shape memory effect and pseudo elasticity.
-
-
COMPARISON OF SMART MATERIALS
In this section, advantages, disadvantages and applications of some smart materials are discussed. Firstly, piezoelectric material is discussed. Its structure is very simple; generate an electrical signal on the application of load. But there is a lot of wear and heat generation, manufacturing is difficult, its working stroke is limited up to a few micrometers. These materials can also be used at high temperatures. They are used in electronic devices, power generation in automobiles, tire pressure sensors and piezo fuel injectors. Magnetostrictive materials have higher energy density and intrinsic robustness. These materials increase the complexity of the system. They are used in tuned vibration absorber, damper, engine mounting and sensors. Shape memory alloys have high damping capacities, high strength and are corrosion-resistant. They are very expensive and temperature-sensitive; the design of these materials is also complicated. Electro-rheological fluid has a more stable system performance, acts as a power amplifier. The fluid becomes thick after prolonged use needs replacement after some time. Its applications are vibration dampers, shock absorber, clutches and hydraulic valves. Table 1 presents the advantages, disadvantages and applications of different smart materials.
-
3D/4D BIOPRINTING
The rise in four-dimensional (4D) printing can largely be attributed to a widely broadcast 2013 TED (Technology, Entertainment, Design LLC, a non-profit company devoted to idea dissemination) talk in which shape-changing 3D printed structures were presented. Since that day, the concept of 4D printing has rapidly developed and expanded its breadth and depth leading to an increase of high-impact original research introducing novel manufacturing approaches/materials. Unfortunately, few follow-up publications have extended the understanding of these materials in depth or evaluated reproducibility and up-scaling on these techniques and approaches.
Dynamic shape changing materials are typically fabricated by multi-material 3D printing techniques, but the definition of 4D printing has quickly become ambiguous and broad. As a result, a more detailed definition specifically stating the constraint of requiring shape or functional change be inducible directly after printing. Other criteria have also been established as reported by The Atlantic Council of the United States where 4D printing is defined as: 3D printing of objects which can self-transform in form or function when exposed to a predetermined stimulus, including osmotic pressure, heat, current, ultraviolet light, or other energy sources. Even so acclaimed by the early publications it needs to be shown if the technology holds great potential in a myriad of industries and applications including TE&RM. Hence, in the following we will critically review, highlight and discuss novel programmable matter formulations and 3D printing strategies in the context of what is defined as bioprinting for potential use in TE&RM.
-
OSMOTIC PRESSURE-DRIVEN HYDROGEL-BASED
BIOINKS
A simple mechanism facilitating 4D temporal shape transformation of 3D printed materials is the utilization of the intrinsic swelling characteristics of hydrogels. A pioneering example demonstrating this fundamental principle was the fabrication of bi-layered constructs composed of photocrosslinkable polyethylene glycol (PEG) of varying molecular weights. When placed into an aqueous environment, pre-designed folding of the constructs was induced by the differential swelling of the bonded hydrogel layers (Figure 1a), resulting in a well-predictable and controllable curvature to form micropatterned spheres, helices, or cylinders. This principle was later adapted for 4D printing applications via the stimulus-initiated shape transformation of printed planar structures upon immersion in water.
-
THERMAL ACTUATION OF SMART MATERIALS In addition to hydrogel-based soft programmable matter,
the shape memory properties of thermoplastics can be used to impart the fourth dimension in 3D-printed structures. Similar to osmotically-driven shape change in composite hydrogel bioinks, shape memory thermoplastics are typically polymers with temperature mediated behavior predicated on the materials intrinsic transition temperature(s) (introduced and reviewed in Complex and intricate origamitype foldng transitions have been demonstrated by utilizing the conventional properties of shape memory polymer. Here a cube structure has been printed in its folded, permanent shape using a 3-layered laminate of two commercially (Stratasys, Minnesota, United States) available polymers e one layer of VeroWhite sandwiched between two layers of TangoBlack. Upon completion of printing, the structure was unfolded at a temperature above the glass transition temperature of the hinge, then cooled while in the flattened state. When the temperature is raised above the transition temperature, the structure reverts to its permanent, folded shape. This approach has been further developed to demonstrate the potential for 4D printing of more complex structures, such as an interlocking clasp and a replica UPS mailing box.
-
ADDITIVE MANUFACTURING (AM)
The fourth industrial revolution, namely Industry 4.0, is the recent movement on intelligent automation technology. In this new era, the utilization of modern manufacturing skills within the context of integrating novel information technologies plays an important role on economic competitiveness [1]. As illustrated in Fig. 1, Industry 4.0 offers cyber and physical systems to cooperate profitably, aiming to build smart factories by redefining the role of humans.
Its fundamental concepts associated with virtual environment comprises Internet of Things (IoT), Big Data, Cloud Computing etc., whereas its physical realm includes Autonomous Robots and Additive Manufacturing. With respect to the cyber-physical systems, IoT is described as the concept of gathering information from physical objects using computer networks or accelerated wireless connections. The extracted information from the products, machines, or production lines constitutes substantial amount of statistical data to be exchanged and analyzed. Other sources of data are design records, customers order, suppliers delivery, stock and logistic related information. As a whole, this large quantity of data is defined as Big Data, which is another major notion in Industry 4.0. Moreover, cloud computing, which is related to the processing of all the available information, can also be considered as one of the most significant terms in virtual industrial world. All of these cyber technologies help to ensure the effective utilization of existing information for smart manufacturing of future.
-
MATERIALS
Material science key for understanding of developments in AM technologies. Researchers in this field have keen interest in new materials suitable for 3D printing applications. Although a large number of plastic/polymer constituents are available for AM [5], some specific materials attract further attention of industry as illustrated in Fig. 2. In this section, the properties of
prospective materials that are likely to be developed in the age of Industry 4.0 are to be discussed in detail and their potential uses are to be identified.
Due to their favorable mechanical characteristics, metals are perhaps the most common materials in engineering. As a consequence, 3D printing industry seeks for novel solutions to create metallic parts that can substitute their conventionally- produced counterparts. The new developments in 3D printing technology give rise to the attempts towards the active research field: Metal additive manufacturing (MAM). Recently, many metallic components can be manufactured by AM techniques using aluminum, titanium, stainless steel, etc. as the main constituent in the process [6]. Most of the commercial metal 3D printers employ metal powders, whereas other suitable material
mixtures have also been scrutinized for MAM [7]. Furthermore, the microstructure resulting from AM have a great influence on the parts mechanical properties like tensile/fatigue behavior. Thus, issues related to microstructure, phase composition, heat treatment have attracted attentions of AM research community recently [8]. Tang et al. [9], for instance, have investigated some mechanical properties of components fabricated through a laser based MAM process, demonstrating the cracking mechanism. On the other hand, there is still much to develop, since the fabricated parts have not yet met the industrys expectations. Some issues that have to be resolved includes favorable cost, production speed, improved tensile/fatigue/hardness behavior, enhanced surface quality, and homogenous microstructure [10]. In the new era, MAM will probably become a key player for the realization of Industry 4.0 as long as it overcomes these current barriers via the improvements in both material science and MAM processes.
-
PROCESSES
In this section, novel AM processes are to be presented with a major focus on the ones related to MAM and hybrid manufacturing. Although the number of innovative AM processes are increasing substantially, they take their root from well-established fundamental technologies. Probably, more enhanced processes will be developed with the technical advancements in AM. However, most of these processes are developed for printing customary materials like polymers, which are generally used for non-industrial applications. Due to the needs for heavy engineering applications in the context of Industry 4.0, specific AM processes have confronted recently. Since metals are the most commonly preferred
material in the industry, the issue of MAM has received considerable attention in this new era.
In addition to this, it is expected that the future of manufacturing will steer the industry towards the utilization of these processes in combination. Being known as hybrid manufacturing, this new popular field offers a way to practice subtractive methods accompanying with additive ones so as to fabricate better products with increased surface quality, fatigue strength etc. Nowadays, the growing interest in hybrid manufacturing leads to various manufacturing process combinations beyond the conventional AM processes.
-
DESIGN RELATED ISSUES
As a relatively new manufacturing technology, engineers and designers have little experience and insufficient knowledge on the capabilities and limitations of AM. Evolving digitalization in the context of Industry 4.0 have created opportunities to overcome design related barriers on the novel production technologies. The developments on the new computational tools for simulation, visualization and instant analysis are directly related to the modern fabrication. In this section, the design related issues are to be addressed briefly. Due to the improvements in cyber technologies of Industry 4.0, designers are supplied with enhanced computational resources, which in turn lead to boosted productivity and efficiency in AM. Design for Additive Manufacturing (DfAM) have been recently introduced as one of the supplementary design tools for selecting the process parameters (such as cost, time, quality, reliability and CAD constraints) in an optimal manner. DfAM is in fact divided into two branches concentrating on the approaches for a general design framework and the methods yielding improved functionality for specific products [46]. The former one provides inexperienced designers a broad perspective for deciding on the best options at design and manufacturing stages of AM.
-
DRAWBACKS AND FUTURE DIRECTIONS In the last decade, Industry 4.0 have attracted the attention of both academia and industry since it is considered as the major paradigm shift in the factories of the future. AM, as a key technology in the context of the forthcoming revolution, offers great potential for the prospective developments in this new era provided that some current barriers are overcome in the near future. In this section, some foreseeable predictions about AM and its possible drawbacks are to be stated along with complementary recommendations.
Due to the major drawbacks on its manufacturing speed, accuracy, repeatability, and cost, AM may not be preferred in conventional industrial factories, especially for the mass production of reular parts. Nevertheless, it still has superiorities over conventional manufacturing methods in the fabrication of intricate and customized objects. In fact, AM provides manufacturing opportunity in a broad range in terms of its material (polymers to metals), size (nanoscale to large parts), and functionality (self-assembling to optimum heat transfer) [56]. Produced parts strength is another weakness of AM that may be promoted by novel materials/processes provoking enhanced microstructures, and proper design/topology optimization.
-
-
OPPORTUNITIES AND APPLICATIONS IN SOME
FIELDS
Nowadays, a considerable number of functional elements in technical processes (ie. actuators, control elements and others) are designed with complicated electrical, pneumatic or hydraulic drives. For these components, considerable simplifications and cost savings could be achieved by employing smart materials. First and foremost among those smart materials are shape memory alloys (SMAs) and piezoelectric ceramics. In recent years shape memory (SM) materials, in particular, have opened up a whole new range of applications: actuator and sensor functions could be mentioned here. The potential for applications is huge, but their practical realisation requires profound knowledge of the mechanisms at work within the materials. In the meantime, the field of smart materials covers a considerable variety of material groups and hence provides extensive areas of application in different technical contexts, as well as in the biomedical field.
-
TECHNOLOGICAL BACKGROUND TO THE
SM EFFECT
SM materials show the particular capacity to revert to their original form when heating if they are plastically deformed below a critical temperature before (Butera, 2001). This exceeding effect is the result of a solid state phase change of these special alloys (SMAs). Figure 2 shows this mechanism referred to as martensitic phase change. The high-temperature modification of the lattice (austenite) flips over into a twinned martensite structure (from top left to bottom). This martensite lattice can be de-twinned up to 8% (for NiTi). As long as the material remains below the phase change temperature, this deformation is lasting. Heating of the deformed martensite above the phase change temperature causes the reversion into the original space-lattice structure and therefore into the original shape of the material. This behaviour is the basis of the SM effect.
The high-temperature modification of the lattice (austenite) flips over into a twinned martensite structure (from top left to bottom). This martensite lattice can be de-twinned up to 8% (for NiTi). As long as the material remains below the phase change temperature, this deformation is lasting. Heating of the deformed martensite above the phase change temperature causes the reversion into the original space-lattice structure and therefore into the original shape of the material. This behaviour is the basis of the SM effect.
-
AUTOMOTIVE APPLICATIONS
In a modern passenger car there are several electromagnetic actuators for different functions, including comfort systems for the driver and passengers, actuators for engine control or vehicle control, servo- microactuators for power systems and aerodynamics. New approaches based on smart materials, instead of the traditional electromagnetic motors, can simplify in most cases the actuation, performing the same function with reduced size, weight and cost, optimising the movement and also offering the opportunity to implement new functions (Butera, 2001). The use of SM actuators as an alternative to electromagnetic motors for automotive applications, particularly for comfort purposes, shows some main advantages: smooth direct movement with high torque or force, no additional mechanism, noiseless operation and intrinsic reliability, since the motion is related to the physical properties of the material.
-
BONNET LIFTING SYSTEM
A pedestrian protection system was developed by the consortium IPPS (Intelligent Pedestrian Protection Systems) (N, 2004). In this safety concept, the companies have cooperated together since 2001. The result is a drivable prototype in which the companies combined their know-how. To decrease the risk of leg injury, a design was developed with a soft foam that is situated between bumper cover and bumper cross beam. In addition to this, new sensors were also integrated into the bumper. The functional principle of these fibre-optical contact sensors acts in different stages. In parts the plastic sheath of the light wave conductor is removed. If the fibres are bent, a part of the light there reflects from the fibre. This reflection is depending on the bending intensity and therefore the light loss registers how strong the fibre was bent. By laying several preserved fibres horizontally about the bumper and removing different segments of the s heath, a distortion picture of the vehicle front arises.
-
Material
In the previous works concerning the development of a quick changing actuator that corresponded to the specified requirements, best results were achieved using a configuration with 30 NiTi wires that were plaited to a so-called SM muscle. This configuration was actuated via electrical discharge of a capacitor and was able to lift a weight of 20 kg (bonnet) over a lifting distance (stroke) of 12.5 mm within less than 35 ms. One single SM wire has a diameter of 0.254 mm and the following supplier specification MemoryMetalle
GmbH, data sheet: NiTi alloy Dy90, high temperature actuator alloy with AP 95 °C. For having the same starting material for the long-time stability tests and to achieve reproducible results, the wires were trained under a loading that corresponded to 135 N/mm2 . The wires were trained 80 times by electrical actuation in special devices that allow fixing and training of 90 wires at the same time.
-
AGEING
The long-time stability of the SM actuators is a significant point that has to be assured. Safety systems in general could be activated within the fi rst days of a cars lifetime or after several years, but the functionality of the whole system and especially the actuators should be reliable at any time. In practice, the long-time stability can be proved through a testing method upon stored specimens. By storing the SM specimens, a so-called ageing process occurs and a statement concerning the functionality of the specimens can be made. The test procedure is based on the well-known fact that the parameters time and temperature have a direct interrelationship. So it is possible to achieve artifi cial ageing when the factor time is replaced through the factor temperature in a certain range. In the case of SMA, this interrelation cannot completely be used because no phase change should occur during ageing. According to the requirements for parts in the engine compartment and to assure at every temperature that the pre-strained wires still have martensitic structure, the ageing temperatures were chosen between 60 and 140 °C.
-
THE TESTING FACILITIES
. The other sides of the specimens are connected over two pulleys to the weight that causes a specified tension of 135 N/mm2 in the SM wire. By heating and cooling the oil bath, the specimens are cycled, and through inductive distance sensors, the exact length of each specimen measured and plotted in a temperaturelength diagram. By means of graphical evaluation, the characteristic points of the phase changes, such as As , Af , Ms and Mf , can be determined. With the data of the phase change temperatures and the contraction value even the smallest behavior differences can be analyzed in the specimens. By comparing the data of the stored and aged specimens with a reference wire (kept at room temperature), possible ageing effects upon the SME can be noticed immediately. If no differences in the wire behavior of reference wire and aged wires at different temperatures and durations are observed, the SM effect of th actuator wires is probably not impaired.
-
-
MEDICAL APPLICATIONS
The major part of the existing applications of SM materials is located in the medical fi eld. In particular, materials of the binary nickel-titanium alloy system, the so-called NiTiNOL or NiTi SMAs, are used because of their exceptional properties. They offer mechanisms for in-vivo delivery of prosthetic devices that are unavailable to other biomedical materials, combined with physical properties that are not only well-matched to human tissue, but also to the requirements of many modern medical interventional procedures and imaging techniques (Friend, 1999). Nowadays medical applications of SMAs can be found in cardiovascular devices, gastroenterology and urology, as well as in the area of orthopaedic implants, orthodontic devices and clinical instrumentation. Their functional properties combined with excellent biocompatibility increase the possibility and the performance of minimally invasive surgeries. Overviews of existing applications can be found in Duerig (1999), Fischer (2002) and Friend (1999).
-
-
3D PRINTING FOR SOFT ROBOTICS
3D printing is an additive manufacturing (AM) process defined as the process of joining materials to make objects from 3D model data, usually layer upon layer, as opposed to subtractive manufacturing methodologies, such as traditional machining. 3D printing can deliver parts of very sophisticated and complex geometries with no need of post-processing, built from custom-made materials and composites with near-zero material waste, while being applicable to a diversity of materials, including smart materials such as shape memory polymers and other stimulus-responsive materials. One of the main example of the design freedom offered is that conventional assemblies can be restructured in a single complex structure that could not be manufactured with the current manufacturing processes. Another driver of the 3D printing technology is that it is environmentally and ecologically favourable. 3D printing technologies and methods are growing frequently in terms of application and market share, spreading into various manufacturing divisions, such as robotics, motorized,
health and aerospace and are expected that this substantial growth will continue over the next few years.
-
Relation between 3D printing & soft robots Soft robots do not require fluidics, pneumatics or inflation instead of which they need tendons, shape memory coils, muscle-like actuators, etc. [42]. Hence, they can be built from commercially available soft materials and 3D printers, with a drawback that such materials cannot be transformed in every desired way. Furthermore, 3D printing has a limitation of speed and difficult scalability so currently the work on soft robotics is going on within the technological constraints of currently available 3D printers. 3D printing is a very slow process, but this is not a major issue, as no-one at this initial stage is looking for the mass production of soft robots. Yet the high specificity and ability to print the most complex shapes makes 3D printing an extremely attractive choice for the fabrication of soft robots. Power sources are an integral part in most of the newly developed soft robots [43] and 3D printing is an extremely useful technique to intelligently place them inside soft structures. However, one fundamental concern in using 3D printing technology for developing soft robots is that 3D printable soft materials have a large tendency to deform under the normally used forces during the building process due to their own weight so a support material becomes a necessity.
-
3D-PRINTED BIOMIMETIC SOFT
STRUCTURES
3D printing technology gives much freedom to designers and also simplifies the execution of effective robotic design principles, such as separation of control and power actuators. It also enables the investigation of mechanically complex designs. Wehner et al. reported the fabrication of an integrated design strategy for an entirely soft and autonomous robot inspired by the octopus. They used a hybrid fabrication technology including moulding, soft lithography and multi-material embedded 3D printing. The rapid fabrication approach and integrated design proposed in this study facilitates the programmable assembly of several materials within a single body to realize an entirely soft robot. Mosadegh et al. developed a pneumatic network for the rapid actuation of soft robots fabricated through hybrid technique of 3D printing and lithography using elastomeric materials. A new design of pneumatic networks was proposed in this study. The advantage of their design is the reduction in the required level of gas needed for inflation of such networks resulting in much faster actuation. The fabricated actuators can be operated for more than a million cycles without any noticeable degradation in the obtained results [48]. Martinez et al. designed and fabricated the soft tentacles using the 3D printing technology of additive manufacturing for the fabrication of moulds for elastomeric casting. These soft tentacles were based on micro-pneumatic networks spatially distributed at the interface of two different elastomers with the ability of complex 3D motion. The range of
motion and the ability of these tentacles to grip different objects with arbitrary shapes was successfully demonstrated in this work [49]. Song et al. reported the use of soft pneumatic actuators for the purpose of providing a physical support that would help in healing the spinal cord injuries of penalized animals by providing support to hip joint movement.
-
3D PRINTING TECHNOLOGIES
In this section, we will present introduction of diverse fabrication techniques based on additive manufacturing to show its ability to produce simple and complex soft robots with various applications. In additive manufacturing, a computer-controlled transformation stage typically changes a pattern-generating device, either in the form of an ink-based print head or laser optics to fabricate the desired objects in a layer by layer pattern. During the process of additive manufacturing, patterned regions composed of powders, inks or resins are solidified to produce the desired 3D shapes. These 3D- printed objects are a physical realization of the digital designs. Several basic additive manufacturing printing techniques have been presented since the introduction of 3D printing. The technology has advanced from making basic prototypes to fabricating finished products. The explicit solidification and patterning method used by a given additive manufacturing technique exhibits the minimum feature size that can be achieved and the sort of printable soft materials that can be used.
-
Photo-curable inkjet printing
Inkjet printing is similar to SLA in many ways with a difference that a movable inkjet head is used in this technique to apply a photopolymer being activated by a UV lamp. The liquid photopolymer is printed on a build platform and the deposited layers are activated by UV lights followed by printing of additional layers in a similar manner. Both additive manufacturing printing techniques of SLA and SLS are light-based methods that are dependent upon laser. Although these techniques have superior feature resolution but they have the limitation of yielding rigid thermoset polymers by patterning with either only thermoplastic polymer powders or photopolymerizable resins. Comparatively the second classification of printing techniques i.e. ink-based additive manufacturing methods have the added advantage of printing patterns using numerous soft materials in the form of printable and formulated inks
using a wide variety of molecular, particulate or polymeric species.
-
SELECTIVE LASER SINTERING Primarily metals are used as the deposition material in additive manufacturing through SLS to form desired 3D objects but post-processing such as sintering, infiltration and finishing is required for completing device fabrication The powder of metal material is rolled across a build platform and a laser is directed into the powder followed by rolling the powder over the top of as- deposited layer and this process keeps on repeating till the desired 3D object is completely fabricated. The unused powder that does not form into the fabricated part of the 3D object remains in the build platform to support the object. Apart from metals, polymers are also used in SLS. Local treatment of polymer particles is carried out in a powder bed through heat by fusing them together with the help of rastering laser. Local sintering of the subsequent powder layer is carried out after printing a layer across the bed. Granulated powders with a typical diameter in the range of 10 100 m are used to facilitate the spreading. During the building process of the desired 3D object, the non-fused sections in the powder bed play the role of support material. In order to reduce material consumption, the unattached powder is detached and reused after completing the fabrication of chosen 3D model and removing it from the powder bed.
-
DIRECT INK WRITING
DIW is an alternative printing technique to FDM for additive manufacturing of desired objects under ambient conditions in which ink passes through a nozzle in a controlled manner. It is layer by layer addition technique in which materials are added both in planer and 3D form. The ink selection depends on its flowing parameters such as viscosity, surface tension, shear stress and shear elastic modulus. Currently, the DIW technique offers the widest spectrum of printable materials such as electrical, biological and structural materials [58]. Different ink materials used are a colloidal suspension, hydrogels, thermoset polymers and fugitive inks [67]. The distinguishable advantage of DIW printing method is its ability to print fugitive organic, filled epoxy inks and concentrated polymers with the fluid properties essential for the deposition of complex 3D designs. Characteristic values for the various ink parameters for DIW technique include printing speed (1 mm s1 to 10 cm s1), ink viscosity (102 106 mPa s) and minimum filament diameter (1250 m) respectively. The magnitude of yield stress must be greater than the applied stress in the print head in order to induce flow through the printing nozzle.
-
SHAPE DEPOSITION MODELING Shape deposition modelling technology is used for fabrication of complex geometries with heterogeneous materials mainly for the application of rapid prototyping. This is a cyclic process that consists of several steps including a deposition. The material in heterogeneous
deposition is changed between each deposition process. Although this method was much better than traditional manufacturing processes used for fabrication; however, there were some certain limitations in using this methodology as well such as high control is required, proper bonding among materials and imperfect machining of plastic leads to fatigue failure due to imperfection of surfaces. Xu et al. have reported the fabrication of cockroach limbs for the first time using a soft, viscoelastic polyurethane material fabricated through SDM technology. They studied the damping and stiffness of these legs and their obtained model results were inspiring at low frequencies; however, they were not that appealing at higher frequencies. This study can inspire researchers to develop a novel material to further enhance the viscoelastic movement of the cockroach leg in a wide frequency spectrum.
-
SHAPE DEPOSITION MODELING SDM is a solid freeform fabrication process which means it
is built from start to finish rather than by removing excess materials from a given object. It does this by layering support material and the desired finished material. In this technology, support material is laid down as a base for the final material, final material is laid on top of the support material and computer numerical control (CNC) mills the part to the desired shape. Soft materials are printed in the form of a continuous filament in FDM method with a single layer being deposited at a time. 3D FDM provides the luxury of a wider range of printable geometries, their feature size and variety of ink designs. Thermoplastic filaments are fed by heating the extrusion head followed by solidifying them through cooling below their glass transition temperature in FDM. The famous printable plastic filament materials used in this method are polycarbonate, polylactic acid (PLA) and butadiene styrene (ABS).
-
-
3D PRINTABLE MATERIALS FOR SOFT
ROBOTICS
Smart materials are the active materials that can undergo some observable change in one domain in response to external stimuli through another domain; the external stimuli may be thermal, chemical, mechanical, optical, moisture, pH, pneumatic and electric or magnetic field. Additive manufacturing or 3D printing of smart materials has been an astounding boost for researchers in the form of 4D printing and soft robotics. When smart materials fabricated by 3D printing in a particular shape have the potential to alter their given shape or properties with respect to time under the influence of some external stimuli, this phenomenon is called 4D printing [30]. Whereas, soft robotics is a broad term that includes actuators, artificial muscles, soft stretchable sensors, soft energy harvesting, pneumatic nets, electroactive polymers and soft electronics. The soft robotics is the field of mimicking of a natural organism using smart materials. This artificial organism paradigm has not only mimicked the shape and motion of some natural organism but now it is also going to exploit all the traits of a natural organism. The revolution in 3D printing has accelerated the progress in soft robotics; it involves two types of contributions: direct printing of smart
materials, and 3D printing of moulds for soft robotics.
-
DIELECTRIC ELASTOMERS
3D printing of DEAs for soft robotics was first reported by Rossiter et al. [80]. DEAs are the class of EAPs that undergo a change in strain upon applying the electric field. DEA can be used as artificial muscle because it has the ability to mimic mammalian muscles due to its large strain, high energy density and light weight. In that work, authors presented the two-membrane antagonistic actuator having electrodes on both sides of each membrane. Upon applying the electric field to the upper membrane the actuator moved upward and vice versa. In another work, DE was fabricated through 3D printing and a soft robot has been presented [81]. They 3D printed silicone films (Thickness 300 m) and carbon grease films. The authors fabricated rectangular and circular DEAs, and through simulations and experiment they proved that rectangular DEA had larger actuation then circular.
-
SHAPE MEMORY POLYMERS
SMPs are thermally activated memory polymers that have a tendency to change their original shape when they are triggered by heat. SMP has been reported for actuation that was printed through 3D digital light processing printer. Polycaprolactone (PCL) cross-linked by methacrylate was used as SMP; the printed structure of SMP was rigid at room temperature, having wax-like surface; when heated above the Tm (55 °C), it becomes pliant and elastomeric. At this state, any deformation can be fixated by cooling below Tm whereas by heating again the structure regains its original shape. The 3D printing of SMP was also reported through FDM technique. SMP based on thermoplastic polyurethane elastomer (TPU) family was used in this study that was processed into filament to make it compatible for FDM to fabricate SMPs can lead to the fabrication minimal invasive medical devices, sensors, wearable electronics and soft robotics
-
HYDROGELS
3D printing of hydrogels have been studied for applications spanning from medical devices to soft robots. There are many hydrogel materials and hydrogel soft actuators that can be 3D printed and stimulated based on their respective stimuluse.g. thermal, electrical, pH, magnetic and light. The common hydrogels include pluronic, alginate, chitosan, polyethylene oxide (PEO), polyethylene glycol (PEG), agarose and methylcellulose. Recently, hydraulic actuation of hydrogels has been reported: most hydrogels consist of physically crosslinked dissipative polymer networks and covalently cross-linked stretchy polymer networks; physically cross- linked part of hydrogel was fabricated using a 3D printer by cross-linking the dissipative networks in pre-gel solutions [86]. A set of hydrogel actuators and robots composed of polyacrylamide (PAAm)-alginate hydrogels based on hydraulic actuation were fabricated.
-
SHAPE MEMORY ALLOYS
SMAs are the smart alloy materials that deform and regain their original shape when stimulated by heat and more common SMAs are (CuZn, CuZnAl, CuAl Ni, NiTi,
NiTiFe, FePt) [87]. A 3D-printed soft robot has been presented based on SMA-based actation; the body of the soft robot was printed by multimaterial printable 3D printer using two materials: one is soft rubber-like material at room temperature, i.e. TangoBlackPlus polymerized by monomers containing urethane acrylate oligomer, Exo-1,7,7- trimethylbicyclo [2.2.1] hept-2-yl acrylate, methacrylate oligomer, polyurethane resin and photo initiator [88]. The other is rigid plastic at room temperature, i.e. Verowhite is a rigid plastic at room temperature polymerized with ink containing isobornyl acrylate, acrylic monomer, urethane acrylate, epoxy acrylate, acrylic monomer, acrylic oligomer and photo-initiators. For actuator installation, SMA (nitinol) wires were used in the form of coils to mimic the muscle as nitinol has the ability to deform when stimulated by heat. The SMA coils were tactfully embedded into the 3D-printed soft robot body and were electrically actuated. This soft body robot embedded with SMAs produced complex and robust gaits including inching and crawling.
-
FLUIDIC ELASTOMERS
FEAs are the relatively new class of smart materials having characteristics like low power actuation, highly extensible and adaptable. These elastomers consist of synthetic elastomer films that operate by the expansion of embedded channels under pressure and when pressure is applied, the FEAs will keep their position with little or no additional energy consumption; they can be powered hydraulically or pneumatically but powered pneumatically has advantage because it provides a low viscosity power transmission medium [89,90]. Using FEAs, a work has been reported which demonstrates a highly extensible sensing skin integrated with soft, pneumatic actuators (FEAs) using DIW 3D printing technique [91]. The rheological properties of FEAs were tailored by preparing the homogeneous blend of silicones with high and low molecular weights.
-
-
3D-PRINTED BIOLOGICAL SOFT ROBOTS There is a vast variety in soft robots and actuators that are being developed to target the current biological issues. The robots can range from active implants to surgical and diagnosis robots depending on the target application. The two main categories in which the biological soft robots can be divided are in vitro robots (operating outside the body) and in vivo robots (operating inside a living organism). Just like the term soft robot refers to at least one major soft component of the robot, the term 3D printed refers to at least one component of the system fabricated through the help of additive manufacturing technology. 3D printing is usually used to only fabricate the soft robotic parts that are either not possible or are very difficult to fabricate through conventional techniques. In this section, we will specifically discuss the 3D-printed soft robots for in vitro and in vivo applications.
-
3D-PRINTED IN VITRO ROBOTS
In vitro means anything that operates outside the body of a living organism in a controlled environment. 3D-printed soft robots have started to find their way in solving biological problems involving procedures carried outside the body of organisms. The edge soft robotics have over the rigid
equipment is their flexibility, accuracy, degrees of freedom and ability to mould themselves according to the target body shape for applications in surgery, exoskeletal active implants, therapeutic systems, diagnosis, artificial skin and so on. A soft robotic glove has been developed by scientists at Harvard [94] for combined assistance and at-home rehabilitation. The robotic glove comprises soft actuators with moulded elastomeric chambers to induce the specified motion through fluid pressurization. The glove is fabricated in multiple stages with the mould for the elastomers fabricated by 3D printing. The 3D printing enables to fabricate the soft robots size and shape exactly according to the patients requirement. The soft robotic glove can help in restoring movement for the disabled by providing specific physiotherapy
-
3D-PRINTED IN VIVO ROBOTS Anything operating inside the body of a living organism and performing its functions is known as an in vivo system. 3D- printed soft robots are being used for in vivo surgeries, organ implants, targeted drug delivery, diagnosis of various disease and conditions and also in the treatment of certain medical conditions. For in vivo applications, there is a huge potential for soft robotics as the internal body structure is too complicated to reach using rigid materials. Also, most of the internal body organs and tissues, except bones, are soft structures and require similar structures for their repair and replacement. 3D-printed soft and smart robotic implants called tracheobronchial splints have been developed to automatically adjust their shape and size inside the blood vessels to treat tracheobronchial collapse in tracheobronchomalacia [112]. The major advantage of this active implant is its personalization for every pediatric patient. A soft 4D bio-material is printed by 3D SLS printing using the 3D model based on patient-specific design. A number of active internal organ implants and repairs have been targeted using 3D-printed soft robots.
-
-
-
SMART GRID AND NANOTECHNOLOGIES: A SOLUTION FOR CLEAN AND SUSTAINABLE
ENERGY
For the first time in recorded history, more people worldwide are living in urban areas than in rural. The urbanization trend picked up pace in the 20th century and has accelerated since. Urbanization manifests itself in two ways: expansion of existing cities and creation of new ones.1 Cities are already the source of close to 80% of global CO2 (carbon-dioxide) emissions and will account for an ever-higher percentage in the coming years. Too much CO2 in the atmosphere has been linked to climate change. If humanity continued with the same solutions that have been used to address urban development needs in the past, the resulting urban ecological footprint will not be sustainable: we would need the equivalent of two planets to maintain our lifestyles by the 2030s. The challenge is to meet the demands of urbanization in an economically viable, socially inclusive, and environmentally sustainable fashion. According to a World Energy Council study,3 global demand for primary energy is expected to increase by between 27% and 61% by 2050. Climate change is expected to lead to changes in a range of climatic variables, most notably temperature levels. Since electricity demand is closely
influenced by temperature, there is likely to be an impact on power demand patterns.
-
CO2 EMISSIONS
Economic development involves the increased use of highly energy intensive materials, such as steel, cement, glass, and aluminum. These materials are necessary for the construction and development of transport, energy, housing, and water management infrastructure. Coal is the most widely used source of energy in energy-intensive industries and is important in the development of modern infrastructure in growing economies.12 According to the United States Greenhouse Gas Inventory (2006), the top five sources of C2 emissions are: fossil fuel (coal, oil, and natural gas) combustion, non-energy use of fuels (construction of modern infrastructure such as transport), iron and steel production, cement manufacturing, and natural gas systems.13 Coal generates the most CO2 emissions of any fossil fuel and yet remains the worlds dominant energy source. On May 9, 2013, the Earths atmosphere crossed an alarming threshold, when the concentration of CO2 in the atmosphere reached 400 parts per million (ppm), up from 355 ppm in 1990.
-
OVERVIEW OF SMART POWER GRID
The electric grid is traditionally divided into three stages: generation, transmission, and distribution. Generation is the stage where the electricity is created, for example, a power plant. Transmission is the stage that transfers the electricity across great distances from the generation location to an area of demand, and is comprised of high-voltage cables, step-up substations and step-down substations. The distribution stage includes transferring electricity from a substation to the end consumer. The electric grid has an interconnected mesh structure whereas major populated areas and generation plants are interconnected via more than one path, creating necessary redundancies. Rather than replacing existing infrastructures, new smart capabilities are made possible by integrating new applications into transmission and distribution grids.21 While the task of the existing energy infrastructure to deliver energy remains unchanged in a Smart Grid, communication between the consumer and provider will be much more efficient and effective, and therefore less expensive and more reliable.
-
CLOUD SYSTEMS AND MACHINE-TO- MACHINE (M2M) COMMUNICATIONS
Energy utilities, including transmission and distribution providers, are beginning to generate massive volumes of data in Smart Grids. This data, when applied effectively with analytics, can help energy companies evaluate the returns being generated against the sizable investments in Smart Grid
technologies. In addition, big data analytics can help power providers evaluate the areas within their Smart Grid networks that can be refined or improved and help assess the business benefits being achieved as a result of Smart Grid.29 Cloud based solutions are assisting utilities with the management and merging of Smart Grid data with other forms of data to deliver information that can help a utility save money or improve operations ranging from grid controls to customer engagement. Cloud also provides a scalable solution, unlimited data access, computation systems to analyze raw data and cost savings, in addition to the reduced need for data storage and server configurations. Combined with an online interface, cloud computing gives utilities and customers access to accurate consumption data at any time via smart phones, tablets, desktops, and laptops. Cloud also provides computational power for complex Smart Grid projects.
-
POWER ELECTRONICS AND SMART GRID Power electronics (PE) can be broadly defined as solid-state energy conversion technology that enables efficient and fully controllable conversion of electrical power.43 Existing silicon (Si)-based PE enable conversion from direct current to alternating current and the movement of electricity from higher voltage transmission to lower voltage distribution. However, Si-based semiconductor technology cannot handle the power levels and switching frequencies anticipated by next generation utility applications. The generated power output from renewable energy is often difficult to control, and if adopted in large quantities, may cause frequency fluctuations throughout the entire power system and local voltage fluctuations may occur. With a Smart Grid, a compensating high-speed high-accuracy power supply system must be used to connect renewable energy, for which the generated output power is difficult to control, to the power system, and PE technology play an important role in the realization of such a system. In particular, many types of distributed power sources generate direct current power, and PE technology for performing power conversion is one of the most important technologies for Smart Grids.45 From a green angle, the use of advanced PE not only enables the effective integration of renewable resources through generation, but it also eliminates the need for building conventional generation in reactive power deficient load pockets a net positive impact on reducing carbon emissions.
-
HOW CAN NANOTECHNOLOGY REDUCE
CO2 EMISSION?
CO2 emission? Nanotechnology is a platform whereby matter is manipulated at the atomic level. There are various ways that nanotechnology can be applied along the Smart Grid to help reduce CO2 emissions. The major impact of nanotechnology on the energy sector is likely to improve the efficiency of current technologies to minimize use of fossil fuels. Any effort to reduce emissions in vehicles by reducing their weight and, in turn, decreasing fuel consumption can have an immediate and significant global impact. It is estimated that a 10% reduction in weight of the vehicle corresponds to a 10% reduction in fuel consumption, leading to a proportionate fall in emissions. In recognition of the
above, there is growing interest worldwide in exploring means of achieving weight reduction in automobiles through use of novel materials. For example, use of lighter, stronger, and stiffer nano-composite materials is considered to have the potential to significantly reduce vehicle weight.9,49 Nanotechnology is applied in aircraft coatings, which protect the materials from the special conditions of the environment where they are used (instead of the conventional bulk metals such as steel). Since the amount of CO2 emitted by an aircraft engine is directly related to the amount of fuel burned, CO2 can be reduced by making the airplane lighter. Nanocoatings are one of the options for aerospace developers, but also for automotive, defense, marine, and plastics industries.
-
-
CONCLUSIONS
Cyber-physical integration facilitates smart factories with high efficiency that are capable of fabricating high quality customized products. On one side, the advancement of information technology has accelerated the transition to forthcoming industrial era. In fact, the existence of the fourth industrial revolution substantially depends on the capabilities of AM. These issues were summarized in three specific topics in this paper, namely material, processes and design issues. In the future, it is likely that more interdisciplinary research efforts should be expended. On the other hand, the role of designers, factories, and customers will be redefined remarkably since the manufacturing business will be distributed to many separate locations like small workplaces or homes. In other words, the current barrier of mass production on location will be overcome with personal- and customized fabrication. Another popular trend aims at creating functional parts/machines in just a single step of fabrication. Due to the opportunities provided by the novel AM technologies, the design- and production challenges are only restricted by the imaginations of the individuals.
REFERENCES
-
P. Zawadzki, K. Zywicki, Manag. Prod. Eng. Rev. 7 (2016) 105112.
-
M.K. Thompson, G. Moroni, T. Vaneker, G. Fadel, R.I. Campbell, I. Gibson, A. Bernard, J. Schulz, P. Graf, B. Ahuja, F. Martina, CIRP Ann. – Manuf. Technol. 65 (2016) 737760.
-
Tibbits S: The emergence of 4D printing. TED talk. 2013. http:// www.ted.com/talks/skylar_tibbits_the_emergence_of_4d_ printing/transcript?language=en.
-
Dawson JI, Oreffo ROC: Bridging the regeneration gap: stem cells, biomaterials and clinical translation in bone tissue engineering. Arch. Biochem. Biophys. 2008, 473(2): 124131.
-
Raviv D, et al.: Active printed materials for complex selfevolving deformations. Sci. Rep 2014, 47422. 8. Raviv D, et al.: Active printed
materials for complex selfevolving deformations. Sci. Rep 2014, 4:7422.
-
M. Maheshwari, A.K. Asundi, S.C. Tjin, Effect of the location and size of a single crack on first fundamental frequency of a cantilever beam using fiber optic polarimetric sensors and characterisation of FBG sensors, in: J.A. Epaarachchi, A.K. Lau, J. Leng (Eds.), Fourth Int. Conf. Smart Mater. Nanotechnol. Eng., SPIE, 2013: pp. 114121. https://doi.org/10.1117/12.2027726.
-
R.A. Silva-Muñoz, R.A. Lopez-Anido, Structural health monitoring of marine composite structural joints using embedded fiber Bragg grating strain sensors, Compos. Struct. 89 (2009) 224234, https://doi.org/10.1016/ j.compstruct.2008.07.027
-
] D. Coric, M. Lai, J. Botsis, A. Luo, H.G. Limberger, Distributed strain measurements using fiber Bragg gratings in small-diameter optical fiber and low-coherence reflectometry, Opt. Express. 18 (2010) 26484 26491, https:// doi.org/10.1364/OE.18.026484.
-
V.M. Murukeshan, P.Y. Chan, O.L. Seng, A. Asundi, On-line health monitoring of smart composite structures using fiber polarimetric sensor, Smart Mater. Struct. 8 (1999) 544548, https://doi.org/10.1088/0964-1726/8/5/303.
-
X. Dong, C. Niu, M. Qi, Enhancement of electrorheological performance of electrorheological elastomers by improving, (2016) 68066815. https://doi. org/10.1039/c6tc01447j.
-
Baumgart, R. 1997, A Fully Implantable Motorized Intramedullary Nail for Limb Lengthening and Bone Transport, Clinical Orthopaedics and Related Research, No. 343, pp. 135-143.
-
Butera, F. 2008, Shape Memory Actuators, Advanced Materials & Processes, pp. 37-40
-
Duerig, T. M. 1999, An overview of Nitinol medical applications, Materials Science and Engineering, Vol. A, No. 273-275, pp. 149-160.
-
Fischer, H. 2002, Applications of Shape-Memory alloys in Medical Instruments, Materials Science Forum, Vols. 394-395, pp. 9-16.
-
Duda T, Raghavan LV. 3D metal printing technology. IFAC- PapersOnLine 2016;49:103110. DOI:10.1016/ j.ifacol.2016.11.111.
-
Bikas H, Stavropoulos P, Chryssolouris G. Additive manufacturing methods and modeling approaches: a critical review. Int J Adv Manuf Technol. 2016;83:389 405. DOI:10.1007/s00170-015-7576-2.
-
Gul JZ, Yang B-S, Yang YJ, et al. In situ UV curable 3D printing of multi-material tri-legged soft bot with spider mimicked multi-step forward dynamic gait. Smart Mater Struct. 2016;25:115009. DOI:10.1088/0964-1726/25/11/115009.
-
Gul JZ, Yang YJ, Young Su K, et al. Omni directional multimaterial soft cylindrical actuator and its application as a steerable catheter. Soft Robot. 2017;4(3):224240. soro.2016.0042. DOI:10.1089/ soro.2016.0042.
-
. Harter G, Sinha J, Sharma A, Dave S. Sustainable urbanization: the role of ICT in city development. Booz and Company; 2010. Available from: http://www.strategyand.pwc.com/global/home/what-we-think/ reports-white-papers/article-display/sustainable-urbanization-role- citydevelopment. Accessed August 25, 2014.
-
Giraud PN, Benard M, Lefèvre B, et al. Energy and Urban Innovation. World Energy Council 2010. Available from: http://www.world energy.org/wp-content/uploads/2012/10/PUB_Energy_and_urban_ innovation_2010_WEC.pdf. Accessed September 16, 2014.
-
United Nations Environment Programme (UNEP). The Emissions Gap Report2013. United Nations Environment Programme (UNEP), Nairobi; 2013. Available from: http://www.unep.org/emissionsgapreport2013/. Accessed March 5, 2014.