
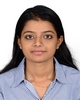
- Open Access
- Authors : Shannon Thankachan , Deepa Varkey
- Paper ID : IJERTV10IS070083
- Volume & Issue : Volume 10, Issue 07 (July 2021)
- Published (First Online): 14-07-2021
- ISSN (Online) : 2278-0181
- Publisher Name : IJERT
- License:
This work is licensed under a Creative Commons Attribution 4.0 International License
Seismic Response of Buildings with Non-Parallel System Irregularity using Pushover Analysis
1Shannon Thankachan, 2Deepa Varkey
1M. Tech student, 2Professor,
Dept. of Civil Engineering,
Mar Athanasius College of Engineering, Kothamangalam, Kerala, India
Abstract: The symmetry of the structure is the foundation of Structural Engineering. Non-parallel system irregularity exist where the vertical lateral force-resisting elements are not parallel to the major orthogonal axes of the seismic force- resisting system. Architects generally plan the structures according to the site orientation and shape. They adopt plans which have advantage in lighting and ventilation. This might result in the formation of non-parallel irregular structures at street intersections or other constricted spaces. Such buildings should be designed with the collaborative effort of architect and structural engineer as they experience torsion or local stresses concentrations. The present research is done to analyze the earthquake behaviour of several non-parallel irregular buildings with same floor area and comparing the result with similar models but by connecting the columns in plan by triangular module beams. Pushover analysis is done using SAP2000 software and the results are interpreted in terms of strength, stiffness and ductility.
Keywords: Non-parallel system irregularity; seismic; pushover analysis; strength; stiffness; ductility.
-
INTRODUCTION
The foundation of Structural Engineering lies on symmetry. Overall size, shape and geometry plays an important role in the performance of a building under earthquake forces and how the earthquake forces are carried to the ground. Hence, in order to avoid unfavourable situations architects and structural engineers should work together from the planning stage itself and select a good building configuration agreeable to both parties. If we start-off with a good configuration and symmetry which is compliant in the functional, structural and aesthetic point, there is less chance for conflict of interest and hence greater for possibility of improvement.
According to ASCE, non-parallel system irregularity exist where the vertical lateral force-resisting elements are not parallel to the major orthogonal axes of the seismic force- resisting system [1]. Architects generally begin planning according to the site conditions. Their main goal for doing this is to take advantage of the maximum area while considering owner requirements. This type of irregularity is commonly seen at complicated street intersections or due to the limitations and requirements of the space utilization in design. They are very difficult to change during design and causes the buildings to experience torsion or local stresses concentrations [2].
The importance of non-parallel irregularity is highly under looked. This negligence is what caused the damage of the
shopping centre located in the district of Erci, 102 km away from the city centre in the north of Van, Turkey in an earthquake that struck in 2011 [2]. The architectural plan of the building is shown in Figure 1.
Fig. 1 Architectural plan of the shopping centre [2]
In order to reduce the irregularity of the structure, the building was blocked and separated by dilatation, but from these three blocks A to C, block C have greater non-parallel irregular configurations than others. When the earthquake stroke, from the three blocks, block C was more severely damaged than blocks A and B because of the non-parallel irregular configuration in the two-way axes X and Y for block C compared to blocks A and B which is only on the X-axis, made a significant contribution to the severe damage of block C [2].
According to Teddy et al. (2017), the configurations responsible for the non-parallel system irregularity are 1) The building is regular, however as the walls of the room are tilted, or the beam arrangement is also tilted, 2) the building is regular, but column arrangement is not in one axis, making the beam connecting the column tilted and 3) the building is irregular, for adjusting to the shape of the site, or the building is deliberately tilted for architects aesthetic consideration [3]. He analyzed five rectangular models with non-parallel system irregularity and discovered that for regular buildings, the
target displacement for the x and y axes are generally relatively similar and the more irregular the building geometry, the larger the target displacement of both axes, x and y. He also proposed that the ratio (jr) of number of beams, columns and shear walls elements that do not follow the orthogonal axis to the total number of beams, columns and shear walls can be used to determine the quality of the building. If jr is less than 30%, the building is said to be of good quality, if 30% jr 50%, the building is said to be of moderate quality and if jr > 50%, the building is said to be of poor quality. It was also found that if it is inevitable to design a building with non-parallel system irregularity, make the structure more rigid by connecting the columns in plan by beams forming a triangle module. However, the percentage of increase in rigidity by using triangular module is not mentioned. It is mentioned that future research can be investigated on the effect of earthquake on geometry architecture with non-parallel system irregularity configuration in irregular form [3].
For this research, three building models with non-parallel system irregularity in plan is chosen. Namely, buildings with Y, V and X shaped floor plans and they are compared with a square building as standard. These building shapes are widely adopted by architects because of their advantage in ventilation and lighting. They are modelled in SAP2000 software before and after connecting the columns in plan by triangular module beams and their seismic performance is evaluated using non- linear static pushover analysis. The results are interpreted using strength, stiffness and ductility parameters.
-
METHODOLOGY
-
Description of Structures
Four RCC buildings (G+4), one without and three with complex shapes are chosen to compare the effect of plan shape on elastic behaviour of buildings. These buildings have approximately the same plan area of about 200m2 in each floor. The models are typical beam-column RC frame buildings with no shear walls, located in a high-seismicity region. A square shaped building is modelled for reference. The floor plan of the buildings are depicted in Figure 2.
Fig. 2 Building plans (a) Square shape (b) Y shape (c) V shape (d) X shape
In order to study the performance of buildings with triangular module beams, three more models with columns in
plan connected by triangular module beams were generated. They are named YT, VT and XT respectively for Y, V and X shapes with triangular module. The structural specification of buildings are shown in Table 1.
TABLE I. SPECIFICATIONS OF MODELS ANALYSED
Model
S, Y, V, X, YT, VT, XT
No. of floors
5 floors each 3m height
Dimension of beams (mm)
300 × 400
Dimension of columns (mm)
300 × 300
Thickness of slab (mm)
120
Materials
M30 concrete, Fe500 Steel
-
Modelling and Analysis
Modelling and analyses have been performed using SAP2000, which is a general-purpose structural analysis program for static and dynamic analyses f structures. In this study SAP2000 v.20.2.0 is used. Two-dimensional plans were drafted in AutoCAD 2021 and is imported to SAP2000 which converts the lines into frames. Columns are assigned at all joints. Three-dimensional structures were modelled within SAP2000 and loads were assigned.
Loads assigned are based on IS codes. They are calculated as follows.
(a) Dead load of walls = 19×0.230×(3-0.4) = 11.362kN/m
-
Dead load of parapet = 19×0.230×1.20 = 5.244kN/m
-
Floor finish = 1kN/m2 [4]
-
Live load = 3kN/m2 [5]
-
Roof live = 1.5kN/m2 [5]
Load combinations and seismic loads are assigned as per 1893 (Part 1):2016 [6]. As for the seismic loads to be considered for the analysis, seismic zone was taken and the zone factor is 0.36. Medium soil and importance factor 1 were adopted [6]. Floor plans of the models and their corresponding 3D in SAP2000 are given in Figure 3.
Analysis were done and sections were finalized. Response spectrum and pushover load cases were defined to conduct pushover analysis. Base shear v/s displacement curve was obtained from pushover analysis.
(a)
(b)
(g)
Fig. 3 Building floor plans and 3D in SAP2000 (a) Square shape (b) Y shape
(c) V shape (d) X shape (e) YT (f) VT (g) XT
-
-
RESULTS AND DISCUSSIONS
The readings obtained from the base shear v/s displacement graph are yield displacement (Dy), ultimate displacement (Du), yield base shear (Fy) and ultimate base
(c) shear (Fmax). The results are interpreted with respect to strength, stiffness and ductility.
Strength, R is the ultimate base shear. Stiffness, K is the ratio of yield base shear by yield displacement and ductility demand factor, is the ratio of ultimate displacement to yield displacement [7]. The values of strength, stiffness and ductility are given in Table 2.
Building model
Strength, R (kN)
Stiffness, K (kN/m)
Ductility,
S
5167.878
73586.786
5.477
Y
7199.019
106679.16
4.607
V
7812.983
114890.11
4.364
X
6259.709
90391.959
3.415
YT
7754.242
121316.85
3.056
VT
7515.672
119839.19
2.964
XT
6631.405
106898.14
2.297
Building model
Strength, R (kN)
Stiffness, K (kN/m)
Ductility,
S
5167.878
73586.786
5.477
Y
7199.019
106679.16
4.607
V
7812.983
114890.11
4.364
X
6259.709
90391.959
3.415
YT
7754.242
121316.85
3.056
VT
7515.672
119839.19
2.964
XT
6631.405
106898.14
2.297
TABLE II. SPECIFICATIONS OF MODELS ANALYSED
(d)
The values of strength, stiffness and ductility for the models are then compared with the corresponding values of square model so that the difference can be easily understood.
(e) Figure 4 shows the graph for strength, stiffness and ductility for building models S, Y and YT and their percentage
difference with square model.
(f)
Fig. 4 Building model v/s percentage difference with square building for S, Y and YT models in terms of strength, stiffness and ductility
Figure 5 shows the graph for strength, stiffness and ductility for building models S, V and VT and their percentage difference with square model.
Fig. 5 Building model v/s percentage difference with square building for S, V and VT models in terms of strength, stiffness and ductility
Figure 6 shows the graph for strength, stiffness and ductility for building models S, X and XT and their percentage difference with square model.
Fig. 6 Building model v/s percentage difference with square building for S, X and XT models in terms of strength, stiffness and ductility
Y, V and X models has non-parallel system irregularity in x or y or both axis. But in the case of Y, the bottom wing which is perpendicular to x axis joins to the two oblique wings thereby providing additional strength and stability. For X
building, the building itself is symmetric in x and y axis and the four wings joins at the centre which contributes to the stability. This is evident from Figures 4, 5 and 6, the strength value of YT increased 10.75% compared to Y, and the strength of XT increased 7.19% compared to X but in the case of VT, the strength decreased 5.75%. This is because in the case of V building, there are only two wings which are joined at an angle making it less stable. Also, in the case of Y and X shapes, the centre of gravity is within the structure. This adds to stability. Whereas for V shape, centre of gravity is outside the structure and the angle between the wings can hugely affect the overall stability. If the initial structure itself is not stable, joining the columns with triangular module beams will not have any advantage over the conventional method and might even have the opposite effect due to additional members as in the case of VT model.
In the case of stiffness, the stiffness of YT increased 19.89% compared to Y, the stiffness of VT increased 6.72% compared to V and the stiffness of XT increased 22.43% compared to X. Stiffness being a material property increased in the case of all three models with triangular module beams compared to their conventional models because for models with triangular module beams, the number of columns and beams are more. The total number of beams and columns in each model is given in Table 3.
TABLE III. TOTAL NUMBER OF BEAMS AND COLUMNS
Building model
No. of Beams
No. of Columns
S
360
216
Y
504
312
YT
738
330
V
474
294
VT
678
306
X
432
270
XT
672
294
For models with triangular module beams, the total number of beams increased average 48.34% and the total number of columns increased average 6.24% compared to conventional models. The increase in members caused the increase in stiffness of the structure.
When stiffness increases, ductility reduces. Hence the ductility of YT reduced 28.32% compared to Y, the ductility of VT reduced 25.56% compared to V and the ductility of XT reduced 20.41% compared to X. The reduction in ductility is due the increase in total number of members in the structure.
-
CONCLUSIONS
The important inferences obtained from the present study are,
-
After connecting the columns by triangular module beams, the seismic performance of a structure with non-parallel system irregularity increased with respect to strength and stiffness and decreased with respect to ductility.
-
If the initial structure itself is not stable, joining the columns with triangular module beams will not have any advantage over the conventional methodand might even have the opposite effect due to the additional members.
-
As the triangular module models possess more number of members, it contributes to the increase in stiffness and thereby decrease in ductility.
-
Triangular module method was efficient in the case of regular shaped buildings as discovered by Teddy L. et al, but for irregular buildings with complex geometry, this method is suitable only if the structure itself is stable and the centre of gravity is within the floor plan of the building.
REFERENCES
-
American Society of Civil Engineers, Minimum Design Loads for Buildings and Other Structures (ASCE Standard ASCE/SEI 7-10), American Society of Civil Engineers.
-
Murat Bikçe and Tahir Burak Çelik, Failure analysis of newly constructed RC buildings designed according to 2007 Turkish Seismic
Code during the October 23, 2011 Van earthquake, Engineering Failure Analysis, Science Direct, Vol. 64, pp.67-84, 2016.
-
Livian Teddy, Gagoek Hardiman, Nuroji and Sri Tudjono, The effect of earthquake on architecture geometry with non-parallel system irregularity configuration, IOP Conference Series: Earth and Environmental Science, Vol. 99, Article No. 012004, 2017 .
-
IS 875 (Part I) (1987), Indian Standard Code of Practice for Design Loads (Other than earthquake) for Building and Structures. Part I: Dead Loads, Bureau of Indian Standards, New Delhi.
-
IS 875 (Part 2) (1987), Indian Standard Code of Practice for Design Loads (Other than earthquake) for Building and Structures. Part 2: Imposed Loads, Bureau of Indian Standards, New Delhi.
-
1S 1893 (Part 1): 2016, Criteria for earthquake resistant design of structures – Part 1: General Provisions and Buildings
-
M. Mahmoudi, S. Montazeri and M. Jalili Sadr Abad, Seismic Performance of Steel X-knee-Braced Frames Equipped with Shape Memory Alloy Bars, Journal of Constructional Steel Research, Vol.147, pp.171186, 2018.