
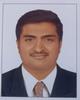
- Open Access
- Authors : Shreetej Govind Chandanshive, Dr. Prashant Prakash Powar
- Paper ID : IJERTV14IS020093
- Volume & Issue : Volume 14, Issue 02 (February 2025)
- Published (First Online): 20-03-2025
- ISSN (Online) : 2278-0181
- Publisher Name : IJERT
- License:
This work is licensed under a Creative Commons Attribution 4.0 International License
Significance of Printing Elements on Surface Roughness of 3D Printed Tensile Specimen using Taguchi Method
Shreetej Govind Chandanshive – U. G. Student Dr. Prashant Prakash Powar – Professor Department of Mechanical Engineering,
KITs College of Engineering (Autonomous) Kolhapur
Abstract In realm of manufacturing, 3D printing has demonstrated transformative potential, enabling the creation of intricate three-dimensional objects at the production level. Achieving the desired technical properties in the final printed product requires optimizing process parameters effectively. This research paper delves into additive manufacturing and process parameters optimization to identify the ideal settings for 3D printing. By systematically experimenting with parameters such as infill density, extruder temperature & print speed. The study aims to determine conditions that maximize the performance of the printed output. The research primarily focused on evaluating the surface roughness of tensile specimen using a surface roughness tester. Findings reveal that infill density significantly impacts the surface finish of 3D-printed specimens, while print speed has minimal influence.
Keywords3D Printing; Printing Parameters; Specimen; ANOVA
-
INTRODUCTION
A process of fabricating a part by layering materials based on 3D model data, contrasting with traditional subtractive manufacturing methods is 3D printing. This technology enhances the speed and flexibility of design and manufacturing processes. Producing complex shapes with traditional manufacturing often involves significant time and cost, whereas 3D printing efficiently creates custom parts, making it a valuable tool during the design phase in various industries. The rapid advancement of this technology has extended its application to production of final parts.
3D printing minimizes substance waste, simplifies operational steps, and reduces production costs and time. The final product is shaped directly from CAD file, allowing easy design modifications. As a key component of the Industrial 4.0, 3D printing reduces the need for physical movement in manufacturing processes.
This versatile technology has applications in numerous industries, including automotive, aerospace, medical, food, textiles, electronics, education, prototyping, architecture, chemicals, and construction. Additive manufacturing encompasses several techniques as Fused Deposition Modeling (FDM), Fused Filament Fabrication (FFF) to name a few. Among these, FDM is the most commonly adopted due to its various benefits and the wide availability of raw materials. It is
also known for its flexibility and ease of material handling, making it suitable for continuous production.
FDM printers uses various thermoplastics. PLA is a preferred material due to its various advantages. It does not require a heated bed, reducing energy consumption. Researchers often focus on PLA because its mechanical properties, such as tensile strength, are more significantly affected by process parameters compared to materials like ABS.
In this study, the surface finish of PLA parts printed using an FDM printer was investigated. The 3D model was designed using CATIA V5R16 software, then sliced and exported as G- code using Cura software. A Taguchi fractional factorial design was employed and an ANOVA was conducted for analysis. As highlighted by Shinde and Powar, optimizing FDM printing parameters is critical to achieving superior surface finish and overall quality in 3D-printed components. Additionally, the influence of process parameters on the final output has been a subject of extensive research, including studies like Powar and Raval's work on hard turning using Minimum Quantity Lubrication (MQL), which underscores the importance of parameter control in modern manufacturing methods. Organization of paper in the following section is represented as follows: Literature Review, Methodology, Results and Discussion, Summary and Conclusion.
-
LITERATURE REVIEW
Various researchers studied the impact of printing elements on the surface finish and quality. Alafaghani et al. [1] explored the optimization of fused deposition modelling (FDM) parameters, focusing on build orientation, nozzle diameter & infill density, and highlighted their significance in achieving desired surface qualities. Similarly, Medellin-Castillo and Zaragoza-Siqueiros
[2] reviewed strategies in FDM that influence surface properties and emphasized parameter optimization for enhanced surface finish. The effect of extruder temperature on characteristics of 3D-printed parts were investigated by Spoerk et al. [5]. They concluded that die temperature significantly influences surface smoothness. Dawoud et al. [6] demonstrated effect of air gap and raster orientation on dimensional accuracy and surface finish of ABS parts, reinforcing the importance of temperature and print settings. Garcia-Leon et al. [7] examined the role of various printing parameters on the impact strength of nylon +Published by :
carbon fiber materials and showed that high-density settings also contribute to improved surface smoothness. Liu et al. [8]
International Journal of Engineering Research & Technology (IJERT)
ISSN: 2278-0181
Vol. 14 Issue 02, February-2025
Physical Properties
Testing method
Typical Value
Table 1
applied the Taguchi method to analyze the effects on mechanical behaviour, concluding that these parameters
Density
GB/T 1033
1.23 g/cm3
Mechanical Properties
significantly influence surface properties. Iyibilgin et al. [9] evaluated various infill patterns and densities, finding that higher densities result in smoother surfaces due to reduced voids. Sai et al. [10] highlighted how infill density and print
Melt Flow Index GB/T 3682
5 (1900C/2.16kg)
speed affect surface roughness and compressive strength of PLA thermoplastic, demonstrating their critical influence on surface finish.
Finally, Popescu et al. [11] provided a comprehensive review of FDM process parameters, identifying print speed, infill density, and extruder temperature as primary factors influencing surface finish and mechanical properties. This study aligns closely with the present research, which focuses on optimizing infill density, extruder temperature, and print speed for enhanced surface smoothness.
-
METHODOLOGY
-
Printing Material
Tensile Strength GB/T 1040 63 MPa Elongation at Break GBT/ 1040 20 % Flexural Strength GBT/ 9341 74 MPa
Flexural Modulus GBT/ 9341 1973 MPa
Thermal Properties
-
IZODImpact Strength GBT/ 1843 9 kJ/m2
Heat distortion Temperature
GB/T 1634 53 0C
Continuous Temperature
Service
IEC 60216 N/A
Fig.1 showing 3D Printing of Tensile Specimen
PLA+ of Ø 1.75 mm diameter, from eSun 3D Printer Filament as material is shown in Table 1.
-
Eqipment
The FDM 3D printer with size of 220 × 220 × 270 mm is used in experimentation (Fig 1). Mitutoyo surface measurement is used to record the surface finish. as shown in Fig 2.
Maximum (short term) Use Temperature
Fig.2 surface finish test on dial
N/A
Fig.4 showing drawing of tensile specimen
Factor
Type
Levels
Values
Infill Density Fixed
3
60
70%
80%
Extruder Temperature
Fixed
3
200
2100C
2200C
Print Speed
Fixed
3
30
50
mm/sec
70
mm/sec
Table 2
-
Preparation of Specimen
The tensile specimens were designed on CATIA V5R16 software and then exported ensure compatibility with Cura software. Cura was used to slice the model based on the selected parameters and later saved as a G-code file. This G-code was then utilized by the 3D printer to fabricate the physical 3D shapes. Fig. 5 illustrates the printed samples. The surface finish of the printed components was measured using a Mitutoyo dial gauge with a range of 0 to 1 mm and a least count of 0.001 mm.
Fig. 5 Tensile Specimen
Table 3
Table 4
Source |
DF |
Seq SS |
Contri bution |
F- Valu e |
P- Value |
Infill Density |
2 |
0.00047 |
40.27% |
1.58 |
0.387 |
Extrude r Temper ature |
2 |
0.00021 8 |
18.67% |
0.73 |
0.577 |
Print Speeed |
2 |
0.00018 2 |
15.59% |
0.61 |
0.62 |
Error |
2 |
0.00029 7 |
25.46% |
||
Total |
8 |
0.00116 7 |
100.00 % |
-
RESULTS AND DISCUSSION
Post experimental values were obtained as mentioned in the Table 3. In order to get the best possible combination of printing parameters, means and S/N ratios were determined. MATLAB software was used to evaluate the experimental data ,as shown in Fig. 6. On the basis the results shown in the fig.6,it could be stated that surface roughness of the specimen was affected by the fill density preceded by
Infill Density
Extruder Temp
Print Speed
S/f finish
1
s/f finish
2
s/f finish
3
Avg s/f finish
60
200
30
0.076
0.06
0.07
0.068667
60
210
50
0.06
0.045
0.055
0.053333
60
220
70
0.08
0.06
0.058
0.066
70
200
50
0.06
0.04
0.12
0.073333
70
210
70
0.075
0.07
0.07
0.071667
70
220
30
0.08
0.085
0.07
0.078333
80
200
70
0.07
0.06
0.055
0.061667
80
210
30
0.12
0.07
0.065
0.085
80
220
50
0.06
0.11
0.11
0.093333
Fig. 6 S/N ratios where A is Infill Density B is Extruder Temperature C is Print Speed
extrusion temperature and printing speed. Figure shows the main effect plot for S/N ratios. As shown in ,i.e. fill density (A) at 75%,extrusion temperature(B) at 225 ,and printing speed(C) at 30mm/sec are the most optimal printing parameters to obtain better surface roughness in FDM process. The ANOVA results are shown in Table 4, where it is discovered that fill density, printing speed and extrusion temperature have
the greatest effects on the surface roughness of FDM manufactured components.Table 4 illustrates how fill density, extrusion temperature, and printing speed contributed in f-value and p-value terms to surface roughness
In the Taguchi method, understanding of S/N ratio provides the performance of system. is used to make the process less sensitive to variations in noise factors, thereby achieving a robust system. There are three types of S/N ratios based on the desired outcome: smaller is better, nominal is better, and bigger is better. For scenarios where minimizing a response is critical such as reducing surface roughness, defect rates, or processing timethe 'smaller is better' S/N ratio equation is used. The equation for 'smaller is better' is given as:
-
CONCLUSION
In this study, the three primary printing parametersfill density, printing speed and extrusion temperaturewere used to experimentally and analytically analyze the surface roughness of the 3D printed component. Using the Taguchi approach, nine experiments were conducted.
The conclusions drawn from the data:
-
The best printing settings for improved surface finish are 50 mm/s, 210°C for the printing speed and extrusion temperature, and 60% fill density.
-
In terms of Ra value, the average surface finish at these settings is 0.053333 µm.
The study shows that, with a contribution of 40.27%, infill density has the largest impact on surface finish, while print speed has the least impact, contributing only 15.59%. This study addressed the impact of three different characteristics on surface roughness: extruder temperature, infill density, and print speed. It is possible to research how these factors affect tensile strength, hardness, dimensional accuracy, and other factors. Additionally, it is possible to explore how different printing settings, including layer height, orientation, material, etc., influence the properties of 3D-printed objects.
-
-
REFERENCES
-
Alafaghani, A. Qattawi, B. Alrawi, A. Guzman, Experimental optimization of fused deposition modelling processing parameters: a design-for-manufacturing approach, Procedia Manuf. 10 (2017) 791
803
-
H.I. Medellin-Castillo, J. Zaragoza-Siqueiros, Design and manufacturing strategies for fused deposition modelling in additive manufacturing: a review, Chin. J. Mech. Eng. 32 (1) (2019) 116
-
Jyotiraditya Vijay Shinde, Prashant P. Powar: Significance of Fdm Printing Parameters on the surface roughness of 3d printed component, International Journal for Multidisciplinary Research,
IJFMR23068918, E-ISSN: 2582-2160, Volume 5, Issue 6
-
Powar Prashant P., Raval Harit K , 2016, A study on process parameters effect in hard turning of EN24 steel using Minimum Quantity Lubrication (MQL), International Journal of Modern Manufacturing Technologies, ISSN 20673604, Vol. VIII, No. 2
-
M. Spoerk, F. Arbeiter, H. Cajner, J. Sapkota, C. Holzer, Parametric optimization of intra- and inter-layer strengths in parts produced by extrusion-based additive manufacturing of poly ( lactic acid ), J. Appl.
Polym. Sci. 134 (41) (2017) 115
-
M. Dawoud, I. Taha, S.J. Ebeid, Mechanical behaviour of ABS : an experimental study using FDM and injection mouldig techniques, J.
Manuf. Process. 21(2016)3945
-
R.A. GarcÃa-Leo´n, M. RodrÃguez-Castilla, W. Quintero-Quintero, Experimental analysis of impact resistance of 3D polycarbonate and nylon + carbon fiber specimens, J. Mater. Eng. Perform. (2021) 111
-
X. Liu, M. Zhang, S. Li, L. Si, J. Peng, Y. Hu, Mechanical property parametric appraisal of fused deposition modeling parts based on the
gray Taguchi method, Int. J. Adv. Manuf. Technol. 89 (5) (2016) 23872397
-
O. Iyibilgin, C. Yigit, M.C. Leu, Experimental investigation of different cellular lattice structures manufactured by fused deposition modeling, in: Proceedings of Free Form Fabrication Symposium, 2013, pp. 895907.
Eng. 42 (12) (2020) 119
[11] D. Popescu, A. Zapciu, C. Amza, F. Baciu, R. Marinescu, FDM process parameters influence over the mechanical properties of polymer specimens: a review, Polym. Test. 69 (2018) 157166