
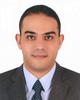
- Open Access
- Authors : Ali R. A , Abdelaziz M. F , Anis A. R
- Paper ID : IJERTV10IS080147
- Volume & Issue : Volume 10, Issue 08 (August 2021)
- Published (First Online): 21-08-2021
- ISSN (Online) : 2278-0181
- Publisher Name : IJERT
- License:
This work is licensed under a Creative Commons Attribution 4.0 International License
Simplified Analysis Method of 3D Sandwich Composite Panels Subjected to Flexure
Ali R. A., Abdelaziz M. F.
Construction Engineering Department
Misr University for Science and Technology (MUST) 6th of October, Egypt
Anis A. R.
Structural Engineering Department Cairo University
Giza, Egypt
AbstractBehavior of 3D Sandwich Composite Panels (3DSCP) subjected to flexure is studied using Finite Element Analysis. Modeling input and results of this analysis are described. The model results are verified by comparing its results with experimental data. Several 3DSCP with different aspect ratios are studied. Behavior of solid concrete slabs that has thickness equals to sum of both concrete layers and the same length of 3DSCP are studied. Deflections at the same load for both 3DSCP and the corresponding solid panel are obtained. At the same load and having the same length, Deflection ratio is considered stiffness ratio that correlates behavior of both samples. A simplified analysis of 3D sandwich composite panel by any structural software using shell element is discussed. Shell element has the thickness of the solid section. Stiffness ratio is proposed to be used as stiffness modifier for the shell element to yield the same behavior of 3D sandwich composite panel. Value for stiffness modifier is proposed.
KeywordsSandwich Panels; Shear Connectors; Precast Concrete; Slab
-
INTRODUCTION
3D Sandwich Composite Panel (3DSCP) consists of two concrete layers reinforced with steel wire meshes. Concrete layers are separated by Expanded Polystyrene Foam layer. Diagonal steel shear connectors are used to achieve a composite action between both concrete layers. Typical 3DSCP cross section is shown in Figure 1.
3DSCP is used as walls and floors to form structural system mostly for low to medium rise buildings. This structural system provides insulated and rapidly constructed buildings. Prefabricated walls and floors 3DSCP are arranged and assembled using reinforced connections. Shotcrete is then used to form both concrete layers and to fill solid connections [1].
Fig. (1): 3D Sandwich Composite Panel-Cross Section
Most of the research regarding the 3D panels construction is experimental oriented work on series of panels loaded using several techniques to simulate various loadings [2-6]. Experimental work on mockup buildings considering
interaction among different elements of the building (Floor panels, wall panels and connections) is rarely found. Experimental work is usually associated with numerical simulation by modeling the specimens using a commercial analysis software [2, 5].
3DSCP is usually produced in standard forms regarding thicknesses and wire mesh reinforcement. Researchers mainly choose test samples like those commercially produced panels to reflect reality. Others tested samples with different details like a study used orthogonal shear connectors for easier construction [4], and a study used corrugated foam to increase interaction with concrete layers [5]. Behavior of samples reinforced with additional rebar in tension concrete layer was investigated in [6].
As shear connectors dominate the behavior of 3DSCP, Samples with double shear connectors to increase panel's capacity were presented in [7]. Theoretical analysis of 3DSCP is presented in limited studies like [8]. Tests on samples using Fiber Reinforced Polymers (FRP) instead of steel are performed in [9,10].
3DSCP exhibits semi composite behavior that lies between two extremes, one extreme is the fully composite behavior like that of a solid concrete panel and the other extreme represents the zero-composite behavior in which each concrete layer behaves independently. Shear connectors determine the degree of the composite action achieved in the panel.
3DSCP structural behavior is complex due to both material and geometric non-linearities, interaction among panel components and the effectiveness of the shear connectors. Analysis of 3DSCP using finite element method requires software with sophisticated features like ABAQUS or similar programs.
Global three-dimensional analysis of buildings is mandatory to study behavior of the building against lateral load cases like earthquakes and wind load cases.
Most of commercial analysis software programs used by structural designers dont have sophisticated features like those available in ABAQUS to properly model 3DSCP. On the other hand, ABAQUS and similar programs cannot widely be used in real structural design projects because they will require extensive modeling time and will require special computer specifications regarding processing and running memory.
A proposed solution is to have an equivalent solid slab section that will result in similar behavior of the 3DSCP. Those equivalent solid sections are then can be used in global three- dimensional analysis of the building using any available software.
The simplified method is to use stiffness modifier option to model solid section panel that is equivalent in behavior to 3DSCP. Stiffness modifier option exists in most of analysis programs to account for cracking of concrete sections. Stiffness modifier can be used to insert a modification factor that correlates the behavior of equivalent solid section to the that of the 3DSCP.
In the current paper, several 3DSCP samples representing different aspect ratios ranging from 13.6 to 29.6 were modeled using ABAQUS. Solid samples having the same details were modeled with thickness equals sum of both concrete layers of the 3D panel after omitting the shear diagonals.
Results from analysis of 3DSCP and solid panels were compared to get the proposed stiffness modifiers. The aim is to simply model 3DSCP using shell element in any software. And to use the recommended stiffness modifiers to modify shell element behavior so that it yields similar behavior of 3DSCP.
-
ANALYSIS MODEL VALIDATION
-
Experimental Work
Benayoune, A.A. Abdul Samad, D.N. Trikha, A.A. Abang Ali, S.H.M. Ellinna [2] studied behavior of 3DSCP under flexure loading experimentally. Testing program included six specimens divided to two panels of size 2m x 0.75m, two panels of size 1.5m x 1.5m and two panels of size 1m x 0.5m. All panels were made of 40 mm thick reinforced concrete layers separated by 40 mm thick polystyrene layer. Concrete layers were reinforced by 6 mm wire mesh spaced by 100 mm both horizontally and vertically. Concrete layers were interconnected by 6 mm diameter zigzag shaped shear connectors spaced 250 mm. Concrete strength, at the day of the test, was 24.15 MPa, young modulus was 22.45 kN/mm2 and splitting strength was 2.51 MPa. Steel yield strength was 250 MPa and youngs modulus was 215 kN/mm2. Insulation layer was lightweight, low strength and low-density polystyrene. Samples were tested using four-point test. Results of sample P12 in this experimental program [2] is used for verification of the analysis model.
Fig. (2): Experiment sample P12 details
-
Analysis Model
The specimen used in the experimental work [2] were investigated by Finite Element analysis using ABAQUS. Experimental specimen details were used as the input data of the analysis model.
Model Parts
Concrete layers were modeled using Eight-node brick hexahedral elements C3D8R. The 8-node linear brick elements have reduced integration and hourglass control. Truss elements T3D2 are used to model reinforcing steel both mesh and diagonal shear connectors.
Concrete Properties
The concrete damage plasticity model (CDP) is utilized to model concrete. The DP model uses the yield function of Lubliner et. al. [11] that was based on Drucker-Prager strength hypothesis. These functions were later modified by Lee and Fenves [12] to cover several evolutions of strength against compression and tension loadings.
The model has many other unique features related to representing damage occurs in concrete beyond elastic range and how stiffness is degraded. Moreover, the model is extended to allow to control the stiffness recovery when load changes sign during cyclic loading and to define the effect of strain rate as well.
The CDP model assumes linear and isotropic behavior of the concrete during elastic range and that the material fails due two mechanisms which are cracking in tension and crushing in compression.
Steel Properties:
Steel bars used as reinforcement for concrete layers and used as shear connectors are assigned a bilinear stress strain curve characterized by two points representing yielding and failure points. The stress strain relationship describes the elastic range and beyond yielding behavior of steel.
Results of the numerical model were compared to experimental results regarding the load-displacement relationship. Figure (3) shows a plot of the load-displacement curve for the analysis model versus that of experimental specimen P12. The graph shows reasonable agreement as failure load in the numerical model is 26.2 kN while that of the test is 24.5 kN. The difference in the ultimate load is 6.9%.
Fig. (3): Analysis model verification
-
-
PARAMETRIC STUDY
In order to get reasonable stiffness modifiers to correlate behavior of solid section panels to those similar of 3DSCP, Finite Element analysis of several samples was carried out. Samples were modeled on ABAQUS using the same procedure of the described verified model.
-
3DSCP Models
Samples were chosen to represent different aspect ratio h/t. Table (1) lists details of 3DSCP samples [1]. Samples program is limited to samples in which thicknesses of both concrete layers are equal to intermediate foam thickness. This case reflects reality as it represents the common case in manufacturers products catalogues and data sheets.
Table (1): Details of 3DSCP Samples
-
Solid Sections Models
Equivalent solid sections samples are listed in Table (2). Each sample has thickness equals to sum of concrete layers in 3DSCP samples. All other details are the same as 3DSCP samples except omitting shear diagonals.
Table (2): Details of solid section Samples
-
Models Description
Elements types are like that used in verification model. Materials input data in analysis model include: Concrete compressive strength 30 MPa, Concrete mass density 2.5E-09 N/mm3, Concrete young's modulus 26,600 MPa, Poisson's ratio 0.2, Steel yield stress is 420 MPa, Steel Density 7.8E-09 N/mm3, Steel young's modulus 210,000 MPa.
Meshing of concrete and steel elements is made using partition cells as indicated in Figures (4) to (6). The bond between steel meshes and the surrounding concrete is guaranteed by embedment constraint feature. Boundaries conditions are hinged at both ends.
Fig. (4): 3DSCP sample PB-A4-Model Mesh-3D View
Fig. (5): 3DSCP sample PB-A4-Model Mesh -Elevation
Fig. (6): Solid sample PB-A4-S-Model Mesh -3D View
Loads applied on slabs samples as uniform surface pressures. Load is increased by increments till failure load.
-
Analysis Models Results
All samples for both 3DSCP and solid panels exhibit normal deformed shape for simply supported panels. Figures (7), (8) and (9) show deformed shape for sample PB-A4, PB- A5-S and PB-A1 for instance.
Fig. (7-a, b): 3DSCP Sample PB-A4-Deformed Shape
Fig. (8-a, b): Solid Sample PB-A5-S-Deformed Shape
-
Results Discussion
If both concrete layers in 3DSCP behave in complete composite action, Moment of inertia (I) of the cross section shall be greater than that of solid panel. Generally, 3DSCP exhibits only partial composite action. Degree of composite action achieved in 3DSCP depends on shear transfer capacity of shear connectors.
Figures (7-a, b) show that deflection pattern for both concrete layers is nearly similar, that indicates that shear connectors provide shear transfer between both concrete layers. However, results of the analysis model show that deflection of 3DSCP is greater than that of the corresponding solid panel at the same load. That means that flexural rigidity (EI) of 3DSCP is less than that of solid panel. This can be attributed to the fact that 3DSCP behaves in partial composite action so moment of inertia of 3DSCP is less than that of solid panel. Moreover, pattern of changing concrete young's modulus in both 3DSCP and Solid panel is different.
For simply supported 3DSCP and solid panel subjected to uniform load, Mid-span deflection equals:
(1)
and
Fig. (9): 3DSCP Sample PB-A1-Displacement Curve
Mid-span deflection at ultimate load for each 3DSCP sample is listed in Table (3).
Table (3): Mid-span deflection for 3DSCP samples
Mid-span deflection of each solid sample at ultimate load of the corresponding 3DSCP sample is listed in Table (4).
Table (4): Mid-span deflection for solid samples
3DSCP samples failed due to yield of shear connectors while solid samples failed due to yield of tension reinforcement.
(2)
Having the same length and at the same load, the flexural rigidity of a 3DSCP can be written as:
(3)
Considering Equation (3) and results in Tables (3) and (4), Flexural rigidity of the solid panel can be modified to yield similar behavior of 3DSCP by multiplying it by the deflection ratio. For samples from 1 to 6, deflection ratios were 0.51, 0.53, 0.64, 0.71, 0.72 and 0.68 respectively.
Global three-dimensional analysis of the building is required in real design projects to get straining actions of lateral loads cases. In buildings where the structural system is formed using 3DSCP, global three-dimensional analysis is also needed to design solid connections tying walls and floors panels.
To perform global analysis using any structural analysis software, one can use shell element to model 3DSCP with thickness equals sum of both concrete layers. Modifiers can be used to modify flexural rigidity of shell element to yield similar behavior of corresponding 3DSCP.
For aspect ratios h/t less than 20, Analysis model results indicate that modifier value 0.5 can reasonably correlate flexural rigidity of both 3DSCP and solid panels. For aspect ratios h/t greater than 20, The modifier may be used as 0.65.
-
-
CONSLUSION
Behavior of 3D Sandwich Composite Panel (3DSCP) is studied using Finite Element Analysis (FEA). Analysis model is validated using experimental results of Benayoune, A.A. Abdul Samad, D.N. Trikha, A.A. Abang Ali, S.H.M. Ellinna [2]. Study on series of samples of 3DSCP and solid panels was performed. The following conclusions can be made:
-
Deformation pattern of 3DSCP samples shows that Shear connectors provide the required shear transfer for panels to exhibit composite behavior.
-
3DSCP may be modeled using shell element in analysis software programs and modifiers may be used to calibrate the flexural rigidity of that shell element so that it behaves like 3DSCP.
-
Modifier value 0.5 is proposed for panels with aspect ratios h/t less than 20, while modifier value 0.65 is proposed for those with aspect ratios h/t greater than 20.
REFERENCES
-
Ali R. A. Flexural Behavior of 3D Sandwich Composite Panels. Ph.D. Thesis, Department of Structural Engineering, Cairo University, Giza 2021.
-
Benayoune, A., A. A Abdul Samad, D. N. Trikha, A. A Abang Ali, and
S. H M Ellinna. 2008. Flexural Behaviour of Pre-Cast Concrete Sandwich Composite Panel – Experimental and Theoretical Investigations. Construction and Building Mterials 22 (4):58092.
-
BUSH, T. D.; Stine, G. L. 1994. Flexural Behavior of Composite Precase Concrete Sandwich Panels With Continuous Truss Connectors. PCI Journal 39:11221.
-
Carbonari, G., S. H P Cavalaro, M. M. Cansario, and A. Aguado. 2012. Flexural Behaviour of Light-Weight Sandwich Panels Composed by Concrete and EPS. Construction and Building Materials 35. Elsevier Ltd:79299.
-
Gara, Fabrizio, Laura Ragni, Davide Roia, and Luigino Dezi. 2012. Experimental Behaviour and Numerical Analysis of Floor Sandwich Panels. Engineering Structures 36. Elsevier Ltd:25869.
-
Jaeger, Thomas. 2013. Extended Sandwich Model for Reinforced Concrete Slabs in Flexure. Engineering Structures 56. Elsevier Ltd:222939.
-
Mohamad, Noridah, A. I. Khalil, A. A. Abdul Samad, and W. I. Goh. 2014. Structural Behavior of Precast Lightweight Foam Concrete Sandwich Panel with Double Shear Truss Connectors under Flexural Load. ISRN Civil Engineering 2014.
-
Daniel Ronald Joseph, J., J. Prabakar, and P. Alagusundaramoorthy. 2017. Precast Concrete Sandwich One-Way Slabs under Flexural Loading. Engineering Structures 138. Elsevier Ltd:44757.
-
Salmon, David C, Amin Einea, Maher K Tadros, and Todd D Culp. 1998. Full-Scale Testing of Precast Concrete Sandwich Panels. ACI Structural Journal 94 (4):35462.
-
Tomlinson, Douglas G., and Amir Fam. 2014. Experimental Investigation of Precast Concrete Insulated Sandwich Panels with Glass Fiber-Reinforced Polymer Shear Connectors. ACI Structural Journal 111 (3):595605.
-
J.LublinerJ.OliverS.OllerE.Oñate 1989. " A plastic-damage model for concrete" International Journal of Solids and Structures 25, 3, 299-326
-
Lee J., Fenves G. L. 1998. " Plastic-Damage Model for Cyclic Loading of Concrete Structures" Journal of Engineering Mechanics 124, 8