
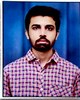
- Open Access
- Authors : Rajesh M C , Dr. Jyothi P Koujalagi
- Paper ID : IJERTV10IS010245
- Volume & Issue : Volume 10, Issue 01 (January 2021)
- Published (First Online): 01-02-2021
- ISSN (Online) : 2278-0181
- Publisher Name : IJERT
- License:
This work is licensed under a Creative Commons Attribution 4.0 International License
Simulation of BLDC Drive for Low Voltage Electric Vehicle Application
Vol. 10 Issue 01, January-2021
Vol. 10 Issue 01, January-2021
Rajesh M C Dept. of Electrical and Electronics Engineering, Dr. Ambedkar Institute of Technology Mallathally, Bangalore-560056 |
Dr. Jyoti P Koujalagi Dept. of Electrical and Electronics Engineering, Dr. Ambedkar Institute of Technology Mallathally, Bangalore -560056 |
AbstractThis paper presents simulation of low voltage electric vehicle system with BLDC drive powered with Battery. A boost converter is used for stepping up of battery voltage to motor voltage. A synchronous generator of low stator voltage coupled with BLDC drive for power generation required for vehicle loads such as Cooling/Heating system, lights, music system, etc. A single phase AC/DC converter provides supply to battery when the supply from charging station is connected. The model of electric vehicle is also presented in MATLAB/Simulink environment.
KeywordsVehicle, BLDC, Converter, controller
-
INTRODUCTION
In past, there are different types of drive applications in which the induction motor is mostly utilized due to its merits such as its different kind of speed control strategies, durability under adverse conditions, productive nature, widely accessible, less operating cost, availability of vast power ratings and capacity to operate in adverse conditions. But there are few disadvantages such prone to heating effects due to low input voltage, complex control, and sudden variations in torque, when combined with renewable energy sources. Hence various researches are ongoing in order to find a motor which will replace the induction motor so that the limitations in induction motor drive can be avoided. The brushless DC (BLDC) motors have the properties like easy to control, less EMI interference, high reliability, robust operation, highly efficient, less maintenance, and wide operating range of voltage, maximum weight to torque ratio and high range of speed [1].The conventional control strategy for BLDC motor with diode rectifier and VSI provided in figure.1. In this method, high frequency pulses (PWM) are used for the VSI which converts DC to three phase AC quantity provided to BLDC motor. Due to this high frequency pulses, the switching losses is increased in inverter switches. Also, this technique involves in higher harmonic currents from the AC Voltage source which leads to increase in THD index of source current associated with poor power factor [2].
Fig.1. Conventional Control of Brushless DC drive
The international standards of power quality such as IEC61000-3-2 rejects such power quality issues in three phase source. The switching losses and power quality issues is increases at supply side is rectified by the planned strategy of control in BLDC motor with varying DC link voltage fed to voltage source inverter[3-4]. This results in the inverter operation with only electronic commutation which is much required for BLDC motor process in low frequency. Brushless DC motor with dc-dc converters such as Luo, modified-Zeta converter, etc, are presented to vary the dc voltage in order to control the BLDC motor speed in [5-9] respectively; but, due to the placement of power electronic switches with the supply results in higher EMI issues and needs higher order filtering.
In this paper, a BLDC drive is presented for electric vehicle application with speed controlled by dc voltage control using the boost converter. The dc voltage reference is generated with speed control loop and by controlling dc voltage, motor speed is controlled. A synchronous generator is coupled with BLDC motor and generates power for other vehicle loads such as lights, music system, etc., so that the stress on battery can be reduced. The physical model of electric vehicle is included and vehicle speed was measured.
-
SYSTEM DESCRIPTION
The simulation of electric vehicle system is provided
in Fig.2.
running state. The generatedVolp. o1w0 Iesrsueis01, pJraonvuiadreyd-202to1 uncontrolled diode rectifier which provides DC supply to other electronic vehicle loads such as Cooling/Heating system, Music system, Lighting system, etc.
-
BOOST CONVERTER & OPERATIONAL MODES
The boost converter circuit configuration is provided in Fig.3 as follows.
Fig.2. Model of Electric Vehicle system
At this time the BLDC motor fed from Boost converter which is fed by battery. The variable output voltage controller of Boost converter is applied in to BLDC motor through VSI. The boost converter controlling the DC link voltage results in the speed of BLDC motor controller. The inverter process is only for electronic commutation at low frequency to minimize the switching losses in inverter. The performance parameters like speeds, torque and operating is evaluated at various loads. Different parts of the model are
as follows:
-
Bridge Rectifier
The Bridge rectifier is used to be rectifying the 1- AC voltage for charging the batteries which is to be supplies the BLDC motor through DC-DC converter and inverter among pure as well as steady DC magnitude of supply voltage.
Fig.3. Boost Converter Circuit
The boost converter provides the step up load voltage than that of the input voltage using duty ratio of the gate signals provided for the boost converter switch. The boost converter consists of an inductor, diode, capacitor and switch. The operational modes of the boost converter are provided below:
Mode 1:
-
Boost converter
The Boost converter is used to be step up the battery voltage to the required voltage necessary to maintaining the BLDC motor speed at reference speed. The yield of the boost converter is connected to the inverter.
-
VSI and BLDC motor
The 3- inverter is used to convert the dc supply from boost converter to three phase ac and provides it to stator of the BLDC motor so that it can be controlled. At this point, the Insulated Gate Bipolar Transistor (IGBT) based VSI is used to designed for feeding the BLDC motor with dc link charge through converter. It can be able to controlled with two methods such as by controlling the dc supply voltage, the speed can be controlled or by using the PWM control in three phase inverter operation. The inverter is used for only dc-ac conversion and thereby energizing the stator coils in appropriate manner so that the BLDC motor will run smoothly. The hall sensors is mounted on the motor which provides the hall signals which in turn is converted to EMFs for each phase and the switching of the inverter will be done accordingly.
-
Synchronous Generator
The synchronous generator is coupled with BLDC motor so that it can generate power when the vehicle is in
The equivalent circuit for operational mode 1 of is given in Fig.4. Initially, switch Q is ON and the inductor get to charge during this period of time.
The voltage of inductor and load are provided below:
Fig.4. Mode 1, VL=Vin
Mode 2:
The equivalent circuit for operational mode 2 of boost converter is provided in Fig.5. Here, the switch Q is OFF and the inductor gets discharged during this period of time and connected in series with battery voltage in order to get boosted voltage at load side.
The voltage of load is provided below:
Vol. 10 Issue 01, January-2021
The reference DC voltage () with the measured output voltage () and the error signal () is obtained as
The error geneated by the voltage is provided to PI controller, which is provide the reference controlled voltage given as
Fig.5. Mode 2, Vo= Vin+VL
Design Procedure of the parameters of Boost Converter:
The boost converter parameters are designed with the help of following equations:
The pulse width of the gate pulse provided to the power electronic switch of boost converter is provided as
The inductor of the boost converter is designed using the following equation:
The inductor ripple current is calculated with the help of equation provided below:
The load side capacitance of the boost converter is provided as follows:
The load side capacitor ripple voltage is calculated using the equation provided below:
-
-
CONVERTER AND MOTOR CONTROLLER
The strategy for control the BLDC motor associated by a boost converter involves 2 different parts such a since the control of boost converter to vary the DC voltage and next is the BLDC motor controller.
-
strategy of Boost converter Controller
In this, the controlled pulses are generated for the boost converter switch Q. The voltage track relation is used which is in voltage control loop in order to control the output voltage boost converter is as shown in figure 6. The reference DC voltage () is provided below as
Where k is denotes the present sampling instance. Generate the pulses are used for the boost converter switch (Q) by comparing the PI controller output () with high frequency triangular signal as follows:
{If < then the pulse is HIGH}
{If then the pulse is LOW}
Fig.6. Control loop for the boost converter and BLDC motor
-
BLDC motor Controller and commutation
In brush DC motor, the commutation occurs at brushes in which the reverse current flows but In BLDC motor, the commutation occurs with the help of switching sequences of three phase inverter and hence this termed as Electronic Commutation. So as to hall sensors are mounted on the motor for each 60 degrees and the generated Hall signal are processed with the help switching table shown below as Table-I and hence the inverter operates under proper sequence in order to operate the BLDC motor.
TABLE-I Truth Table for BLDC drive with Hall Sensor
-
-
SIMULATION RESULTS
The simulation parameters are provided in the following Table-II:
In this, the single phasVe orl.e1c0tifIisesruep0ro1,vJidaensuatrhye-2D02C1 voltage which charges the battery when the vehicle is connected with charging station. When the battery is charged sufficiently, then the supply from charging station disconnects and the vehicle starts moving. The boost converter output is provided to BLDC motor drive and the circuit simulation of BLDC motor drive is provided below in Fig 8.
TABLE II SIMULATION PARAMETERS
Parameters
Values
DC-DC CONVERTER
Output Voltage
400 V
Power
1.5 KW
BOOST CONVERTER
Inductor
0.2mH
Capacitor
110F
Switching Frequency
5KHz
Battery
Voltage
48 V
Capacity
10.5
Ah
Grid
Voltage
220 V
Frequency
50 Hz
Electric Vehicle Loads
Lighting system
110W
Cooler/Heater
250W
Load Arrangements
Music system
55W
Wiper Motor
100W
The simulation circuit for BLDC drive based electric vehicle model coupled with synchronous generator is shown in Fig.7. This supplies the power required for electric and electronic loads such as lighting, music system, heater or cooling system, etc., used in the vehicles.
Fig.7. Simulation circuit of Electric Vehicle system
Fig.8. Simulation circuit of BLDC drive
In this, the gate pulses are derived from the Back EMF which in turn is calculated based on the hall sensor output signals. The controlling the speed loop of BLDC drive is provided below in Fig.9.
Fig.9. Simulation circuit for BLDC motor closed loop speed control
In this, the reference speed and measured speed are compared and the error speed is provided towards the PI controller. The PI controller generates the DC voltage reference is compared with measured DC voltage and the error voltage is provided to next PI controller. This PI controller generates the duty ratio which is required for generation of gate pulse for boost converter. The pulses will be provided to the boost converter switch only if the vehicle starts moving.
The BLDC motor is coupled with the synchronous generator of 20V, 750W so that it can supplies the loads such as heater/cooler, lights, wiper motor, etc., without drawing the power from battery and hence the BLDC motor is left undisturbed. The simulation circuit for synchronous generator setup is provided below in Fig 10.
Vol. 10 Issue 01, January-2021
Fig.10. Synchronous generator coupled with BLDC drive The mechanical power from BLDC is transferred to
the synchronous generator and excitation is controlled by simple voltage regulation circuit. The load voltage is maintained at 12V for different loads with the help of this regulation circuit.
The simulation circuit of electrical and electronic load setup is provided below in Fig.11.
Fig.11. Electric & Electronic loads in Electric Vehicle system The step signals are used to turn ON the loads. The
power consumed by each load is measured along with total power consumption. The torque from the BLDC is provided to the Generic engine which in turn coupled with the vehicle body and when the BLDC motor starts, the engine also starts to operate and hence the vehicle starts to move. The simulation circuit for the Engine along with gear setup is provided below in Fig.12.a.
Fig.12.a. Simulation diagram for Physical modeling of Electric Vehicle
The engine is shafted with the gear box which multiplies the rotational speed of the engine and transfers to the tyres of the vehicles. The simulation circuit of the vehicle body model is provided below in Fig.12.b.
Fig.12.b. Electric Vehicle body structure
In this setup, the front end tyres and rear end tyres are connected to the engine shaft and the rotational motion of engine causes the tyres to rotate and the vehicle starts to move. In this, the wind velocity is provided as 5m/s.
SOC of Battery(%)
SOC of Battery(%)
The %SOC waveform of the battery is provided below in Fig.13.
Time in Sec
Fig.13. % SOC waveform of Battery
Initially, the vehicle is idle condition and at t=0.05s, Vol. 10 Issue 01, January-2021
Load voltages in V
Load voltages in V
the vehicle starts. The battery is charging during idle condition and starts to discharge when the vehicle starts. The boost converter output voltage is provided in the following graph in Fig.14.
Output voltage in V
Output voltage in V
Time in Sec
Fig.16. DC Load Voltage waveforms
Time in Sec
Fig.14. Boost Converter output voltage
Power in W
Power in W
The input battery voltage of 48V is boosted up to 400V and this boost converter output voltage varies depending on the reference speed of the BLDC motor. The BLDC motor drive speed is provided below in Fig.15.
The DC voltage is maintained at 12V when additional loads are connected at different intervals of time. The powers consumed by te electrical and electronic loads are provided in the following graph in Fig.17.
Speed in rpm
Speed in rpm
Time in Sec
Fig.17. Power Consumption of Electronic loads in EV
Time in Sec
Fig.15. BLDC motor Rotor speed
When different loads are turned ON at different times, the power consumption will vary with time. The power consumption of each loads and total power consumption is also provided.
The speed is zero until t=0.05s during the idle state in which the battery gets charged from charging station and then the BLDC motor gains speed once the vehicle get started and then the speed increases and reached 1500 rpm.
The DC voltages of the various electrical and electronic loads are provided in the following graph in Fig.16.
-
CONCLUSION
In this paper, a BLDC drive is designed and simulated for electric vehicle application with speed controlled by dc voltage control using the boost converter. The dc voltage reference is generated with speed control loop and as the dc voltage is controlled, motor speed is also controlled. A synchronous generator is coupled with bldc motor and the power generated is utilized for other vehicle loads such as lights, music system, etc. The physical model of electric vehicle is included and vehicle speed was measured.
REFERENCES Vol. 10 Issue 01, January-2021
-
R.Krishnan: Electric motor drives: modelling, analysis and control (Pearson Education, India, 2001)
-
B.Singh, V.Bist.: A BL-CSC converter fed BLDC motor drive with Power factor correction, IEEE Trans. Ind. Electron., 2015, 62, (1), Pp.172183
-
T.Gopalarathnam, H.A .Toliyat.: A new topology for unipolar brushless DC motor drive with high power factor, IEEE Trans.
Power Electron.,2003, 18, (6), pp. 13971404
-
V. Viswanathan., V. Jeevananthan,: Approach for torque ripple reduction For brushless DC motor based on three-level neutral- point-clamped Inverter with DCDC converter, IET Power Electron., 2015, 8, (1), Pp.4755
-
B.Singh, V.Bist: Power quality improvements in PFC Luo converter fed BLDC motor drive , Int. Trans. Electr. Energy Syst. (ETEP), 2014, 24,(5), pp.12224
-
B.Singh, V.Bist.: Reduced sensor configuration of brushless DC motor drive using a power factor correction-based modified-zeta converter, IET Power Electron., 2014, 7, (9), pp. 23222335
-
B.Singh, V.Bist: Reduced sensor configuration of a power factor Correction based single-ended primary inductance converter fed brushless DC motor drive, IET Power Electron., 2015, 8, (9), pp. 16061615
-
D.S.L.Simonett, J.Sebastian, J.Uceda.: The discontinuous conduction Mode Sepic and Cuk power factor pre regulators: analysis and design, IEEE Trans. Ind. Electron., 1997, 44, (5), pp. 630637
-
H.Y.Kanaan, , Al-Haddad, A.Hayek, I.Mougharbel.: Design, study, Modelling and control of a new single-phase high power factor rectifier Based on the single-ended primary inductance converter and the SheppardTaylor topology, IET Power Electron., 2009, 2, (2), pp. 163177