
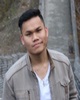
- Open Access
- Authors : Phongsavanh Sengaphone , Dr. Alvin Chua
- Paper ID : IJERTV10IS110051
- Volume & Issue : Volume 10, Issue 11 (November 2021)
- Published (First Online): 17-11-2021
- ISSN (Online) : 2278-0181
- Publisher Name : IJERT
- License:
This work is licensed under a Creative Commons Attribution 4.0 International License
Simulation of the bottle mold using the intelligent NX 10 system CAD/CAM and Finite Element Analysis
Phongsavanh Sengaphone Mechanical Engineering Department, De La Salle University
Dr. Alvin Chua
Mechanical Engineering Department, De La Salle University
Abstract: This article gives a finite element study of a novel bottle mold in order to determine its limitations. By using the NX 10 software, we were able to create and produce numerical control (NC) codes, as well as compare the stress analysis of various materials to better understand their behavior. Due to its programming and production efficiency, the software was able to reduce costs via simulation. The Unigraphics NX software was used to build the CAD/CAM design and to conduct the material stress analysis.
Keywords: NX 10 (CAD/CAM), Numerical Control, Finite Element Analysis.
-
INTRODUCTION
Modeling trendy engineering equipment requires a great level of complexity and infallibility. Additionally, utilizing software to design, simulate, and stress analyze materials is critical since it makes the designed engineering easier to work with and modify. For instance, the issue may be resolved by simulating the materials and doing analysis using a CAD/CAM system. NX software is comparable to CATIA, Pro Engineer, and Solidworks software in terms of high performance, functionality, and stability. Manufacture using NC machines and tool design are both components of assemblies and drawing from 3D models created with their software aids in product development and manufacturing. Additionally, the NX 10 software is the industry standard for several design automation systems at various levels, which means that the software may import and export data to and from another program. For instance, CATIA, Solidworks, and ProE, among others… [1].
The purpose of this project is to use the NX 10 software to design materials in three dimensions and then simulate manufacturing (CAM) and stress analysis on a variety of materials (Bottle molds) such as iron (Fe) and aluminum.
-
BLADE SHAPE PARAMETERS AND MATERIAL PROPERTIES
A block diagram of the Unigraphics NX CAD is presented below, followed by a simulation of the manufacturing mill (CAM) and material finite element analysis (FEA).
Fig. 1. Block diagram of the Unigraphics NX CAD/CAM and Finite element analysis system.
-
Computer Aided Design-CAD
Computer systems aid in the study, construction, optimization, and change of a design (CAD technology). Any software package that combines computer graphics and application software to promote engineering functionality in product models is considered CAD software [2]. The most innovative aspect of CAD is the assignment of design geometry – a tool assembly, machine equipment, architectural structure, electronic circuit, and construction plan. The greatest advantage of CAD systems is that they save time and eliminate certain inaccuracies produced by constantly resetting the geometry of the skate shot. Below that is the three-dimensional representation of the material seen in Fig 2 [3].
Fig. 2. The material 3D
-
Computer Aided Manufacturing-CAM
The management, planning, and control of manufacturing operations that are connected to the computer system's CAM technology through a machine interface with the factory's production. NC is a critical component of CAM [2]. Milling, cutting, and drilling all use similar approaches of programmed instructions to direct a machine tool to do tasks in accordance with the sequence. Robotic programming is critical because of the CAM function. The purpose of computer automation is to develop manufacturing processes. The following figure illustrates the program generation and verification process (a) with a cutting tool (b) with a finishing tool [3].
Fig. 3. The program generating and verification (a) with cutting tool (b)
finishing
-
Post Processing
In post-processing, there is an incidence generator, an incidence handling file, a definition file, and an output manager [5]. The TCL language, which was invented and is used by, enables the development of the post, which is a kind of the computer that was designed by John K Ousterhout. Manual programming and Post Builder are included [6, 7]. Post Builder is a tool for writing postcodes that makes it easy to develop and fix post-processing. By coordinating the visual interface with the post-processing constructor, users may easily specify and generate the output format for NC programs, including each incident processing option.
-
Finite Element Analysis (FEA)
Finite Element Analysis (FEA) is a technique for forecasting the reaction of structures and materials to external influences such as stresses, heat, and vibration. The method starts with the creation of a geometric model. The model is subsequently segmented (meshed) into tiny parts (elements) that are connected by unique node points of fundamental geometric shapes. This approach approximates the stress- strain relationships more accurately. Finally, the material behavior and boundary conditions are applied to each element. In a matter of minutes, applications such as NX 10 automate the mechanism and enable complex calculations to be solved. It will offer the engineer detailed insight into the behavior of the item [2]. This is followed by the finite element analysis process seen in Fig 4 [4].
Fig.4. The finite element analysis molds
-
-
RESULT AND DISCUSSION
-
Design the bottle mold
Figure 5. In the NX 10 software, display an image of the newly designed bottle mold.
Fig. 5. The bottle mold
-
Simulation Manufacturing Mold
The most widely used and popular approach, and the foundation of CAD/CAM integration, is to create program codes for CNC machines to mill the component. This technological development reduces the amount of human intervention in the generation of CNC codes. This also simplifies the process of designing complicated structures. The manufacturing bottle mold and post-processing are shown in Figs. 6, 7 are below.
Fig. 6. Manufacturing Bottle Mold
Fig. 7. The post processing
-
Finite Element Analysis Between Aluminum and Iron
The following table summarizes the mechanical characteristics of iron.
Iron (Fe) [8]
Density: 7.87 g/cm3
Poissons ratio: 0.291
Modulus of elasticity: 200 GPa
The value for Pressure: 100 psi
Fig. 8. Finite Element Analysis Iron Fe (a) Displacement – Nodal (b)
Stress Elemental
Finally, complete content and organizational editing before formatting. Please take note of the following items when proofreading spelling and grammar:
Additionally, the investigation indicates that the bottle mold's (Iron Fe) maximum deformation is less than.
Displacement Nodal is 2.019×10-4 mm Stress Elemental is 1.122 MPa
Aluminum mechanical characteristics are listed below.
Aluminum [9]
Density: 2.6898 g/cm3
Poissons ratio: 0.34
Modulus of elasticity: 68.3 GPa
The value for Pressure: 100 psi
a b
Fig. 9. Finite Element Analysis Aluminum (a) Displacement – Nodal (b)
Stress Elemental
Additionally, the investigation indicates that the greatest deformation encountered at the bottle mold (Aluminum) is less than.
Displacement Nodal is 0.606 mm Stress Elemental is 1.108 MPa
-
-
CONLUSION
Through simulation of the bottle mold utilizing the sophisticated NX 10 system CAD/CAM and finite element analysis, I discoverd how useful this tool is for designing and determining material stress. As a result, I created a bottle mold and compared it to other materials such as iron and aluminum using Siemens NX 10's finite element analysis. To begin, the bottle mold (Iron Fe) experiences a maximum deformation of 2.019×10-4 mm for displacement nodal and 1.122 MPa for stress elemental. Second, the study shows that the greatest deformation experienced at the bottle mold (Aluminum) is 0.606 mm for nodal displacement and 1.108 MPa for elemental stress. Thus, when it comes to creating the bottle mold, iron is superior to aluminum.
REFERENCE
-
Application of NX Siemens PLM software in educational process in preparing students of engineering branch, Cite as: AIP Conference Proceedings 1797, 030015 (2017), Published Online: 05 January 2017,
G. M. Sadchikova.
-
NX 10 for Engineering Design, By Ming C. Leu Amir Ghazanfari Krishna Kolan, Department of Mechanical and Aerospace Engineering, Missouri University of Science & Technology, page 5.
-
Blow Mould Tool Design and Manufacturing Process for 1litre Pet Bottle. K. GiridharReddy, K. Rajagopal M.Tech, Ph.D. Volume 8, Issue 1 (Jul. – Aug. 2013), PP 18.
-
What is Finite Element Analysis and how is it done. Bill McPhee, Scott Melvin. September 17, 2020.
-
The NC Machining Post-Processing Technology Based on UG. International Journal of Science and Research (IJSR), India Online ISSN: 2319-7064, Sharifa Magambo, Liu Ying, Tianjin University of Technology and Education Department of Mechanichal Manufacturing and Automation, Tianjin,China.
-
J.Xia, Q.J.Ge.An exact representation of effective cutting shapes of 5- axis CNC machining using rational Bezier and B-spline toll motions. International Conference on Robotics & Automation Seoul Korea.2001 (21-26).
-
Shitian Zhao,Dianzhu Sun. Processing center special post-processor research and application based on the UG/Post [J].Journal of Shandong university of science and technology .2005(5): (56-60). In Chineseyouth. UG-based CNC programming and machining process simulation [J]. Inner Mongolia University of Technology, 2007.
-
Iron (Fe) – Properties, Applications. Written by AZoM. Jul 11 2013.
-
Aluminium: Specifications, Properties, Classifications and Classes. Sponsored by Aalco – Ferrous and Non-Ferrous Metals Stockist. May 17 2005.