
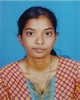
- Open Access
- Authors : Hemalatha T V , Dr. B Rajesh Kamath
- Paper ID : IJERTV11IS090005
- Volume & Issue : Volume 11, Issue 09 (September 2022)
- Published (First Online): 09-09-2022
- ISSN (Online) : 2278-0181
- Publisher Name : IJERT
- License:
This work is licensed under a Creative Commons Attribution 4.0 International License
Simulation of Vector Controlled Induction Motor Drive with 5 Level CHBMLI
Hemalatha T V
Student,
Sri Siddhartha Institute of Technology,
Dr. B Rajesh Kamath
Professor,
Sri Siddhartha Institute of Technology.
Abstract– Three-phase Induction motors are extensively used in industry for industrial drive application. These machines contain quite a lot of advantages of being strong, consistent and easy in construction. For this reason, these types of machines are now more used in variable speed application. They create part of vector commands. Precise control of induction machine with harmonic reduce of magnetic flux, minimization of torque pulses was constantly the goal of studies. The key disadvantage of induction machine control is harmonics, which is cause by the use of two-level inverter. So, in our work, we will incorporate cascaded H bridge multilevel inverter for the induction machine control to resolve this problem. In this paper, the approach for induction machine control is base on indirect field-oriented control and is fed by a cascaded 5-level. Alternate Phase Opposition Disposition multi carrier PWM method is used to control switching of multilevel inverter. The proposed system is simulated in MATLAB/Simulink software.
Keywords– Three-phase Induction motors, magnetic flux, multilevel inverter, PWM technique, MATLAB/Simulink.
-
INTRODUCTION
Traditionally, DTC is a type of dominant high performance control strategy to manage of induction motor drives. It features extremely rapid torque response with uncomplicated structure. Though, due to the utilize of hysteresis comparators and predefined switching table, there are large torque ripple and variable switching frequency. MPTC has in recent times emerged as an efficient option to usual DTC by predicting the upcoming system performance in the constraints of limited switching states of inverters. Compared to DTC, the heuristic switching table is replace by a correct system model, which can straight foresee the growth of variables concerned, such as torque and stator flux. By evaluating the power of every feasible voltage
able to be up to tens of kilohertz, so performance development is more of concern. The aim is typically forcing the control variables to follow the reference value in a fast and accurate fashion. Several study have been made on the application of MPTC in low power motor drives, together with weight optimization, sensor less operation and tentative comparison with filed orientation control (FOC), etc. For two level inverter-fed IM drives, as the quantity of voltage vectors is restricted (only 8 vectors), apply only one voltage vector in one control period (in a similar fashion to DTC) cannot decrease the torque ripple to the smallest amount value. To attain acceptable performance, the sample frequency of MPTC has to be far above the ground.
-
PROBLEM STATEMENT
In this, a easy but efficient torque ripple reduction scheme is projected in MPTC by separating the control period into 2 interval. Only a portion of period is applied for the vector selected from MPTC, as the rest time is owed for a null vector. The period of the active vector is obtained base on the standard of torque ripple minimization, which has been productively in DTC drives. The predefined switching tables are changed by a fixed system model. From which the electromagnetic torque and flux can directly predict. The influence of each possible voltage vectors is evaluated and the one dropping the torque and flux errors is engaged as the precise voltage vector. Therefore, the vector occupied from MPTC is exact and accurate than that of usual techniques.
-
METHODOLOGY
The fundamental version of the direct vector control technique for a PWM voltage fed inverter drive is
*
vector, the one minimize the torque and flux errors are
revealed below. The main vector control parameters, ids
and
chosen as the best voltage vector. Thus, it is clearly that the vector chosen from MPTC is added precise and efficient than that from conventional DTC. As a new branch of high performance control plan, MPTC can be functional to both high power and low/medium power drives. Along with the variations of MPC, several are intended particularly for high power medium voltage drives with extremely limited switching frequency (usually a few hundred hertz). As both switching frequency reduction and performance development (low deformation in current and torque) are of concern, the torque and stator flux are typically controlled to function inside a convinced hysteresis bounds. For small or medium power drives, the switching frequency of inverter is
qs
I *, which are the DC components used in synchronously
qs
rotating frame, are distorted into stationary frame with the help of a usual unit vector (cose & sine) generate from flux vector signals drs and qrs. Obtain stationary frame mechanism are then transformed to phase current commands for the inverter. The flux signals drs and qrs are generate as of the machine terminal voltages and currents with the assist of voltage model estimator. The torque component of current i * is generate as of the speed control loop through a bipolar limiter. The torque relative to iqs (with constant flux), be able to be bipolar. It is negative with negative iqs and likewise, the phase position of iqs become negative. An added torque control loop can be included inside the speed
loop, if preferred. From side to side programming the flux command can be extensive to field- weakening method so as to the inverter remains in PWM form.
Fig.3. Direct vector control with rotor flux orientation [23]
By the assist of stationary frame rotor flux vectors drs and qrs, the subsequent equations are obtain
-
Advantages:
-
The projected controller provides less torque ripples amd lower harmonic contents.
-
The pace reaction of the projected MPTC is also
smoother than that of conservative MPTC even at lower speeds.
-
The dynamic performance of the proposed control is better than conventional control when external
load disturbance is suddenly applied.
-
-
Applications:
-
Due to Low torque ripples, it can be used in Electric Vehicles.
-
It can also be used in Compressors, Conveyors, Crushers, Bulldozers, etc.,
-
Three Phase Induction Machine:
The mainly common type of AC machine being used all through the work nowadays is the "Induction Machine". Application of three-phase induction machines of dimension varying from half a kilowatt to thousands of kilowatts is numerous. They are originating all over from a tiny workshop to a big manufacturing industry.
The advantages of three-phase AC induction machine are listed below:
-
Effortless design
-
Strong construction
-
trustworthy operation
-
Low initial cost
-
Simple operation and easy maintenance
-
Simple control gear for starting and speed control
-
High competence.
Induction machine is originate in the year 1891 with crude construction (The induction machine theory was made-up by NIKOLA TESLA in 1888.). Then an enhanced construction with dispersed stator windings and a cage rotor was built.
The slip ring rotor was developed after a decade or so. Since then a lot of development has in use place on the design of these two types of induction machines. Lot of study work has been caried out to get better its power factor and to attain appropriate method of speed control. Types and Construction of Three Phase Induction Machine
Three phase induction machines are constructed into two main types:
-
Squirrel cage Induction Machines
-
Slip ring Induction Machines
-
-
Modeling of Induction Machine:
The Asynchronous Machine block gear a three- phase asynchronous machine (wound rotor, single squirrel- cage, or double squirrel-cage). It operates in either generator or machine mode. The method of process is dictating by the sign of the mechanical torque:
-
If Tm is positive, the machine acts as a machine.
-
If Tm is negative, the machine acts as a generator.
The electrical part of the machine is represent by a fourth-order (or sixth-order for the double squirrel-cage machine) state-space model, and the mechanical part by a second-order system. All electrical variables and parameter are referred to the stator; indicate by the key symbols in the subsequent machine equations. All stator and rotor quantity are in the random two-axis reference frame (dq frame).
-
Where
-
Rs, Lls – Stator resistance and leakage inductance
-
Lm – Magnetizing inductance
-
Ls – Total stator inductance
-
Vqs, iqs – q axis stator voltage and current
-
Vds, ids – d axis stator voltage and current
-
qs, ds – Stator q and d axis fluxes
-
m – Angular velocity of the rotor
-
m – Rotor angular position
-
P – Number of pole pairs
-
r – Electrical angular velocity (m × p)
-
r – Electrical rotor angular position (m × p)
-
Te – Electromagnetic torque
-
Tm – Shaft mechanical torque
-
J – Combined rotor and load inertia coefficient. Set to infinite to simulate locked rotor.
-
H – Combined rotor and load inertia constant. Set to infinite to simulate locked rotor.
-
F – Combined rotor and load viscous friction coefficient
-
-
-
-
Five-level Cascaded H-Bridge Inverter
distortion and able to function at low switching frequency. The projected a single phase 5-levelCHB MLI in this thesis is shown below:
The single phase 5-level CHB MLI has generate five step of output as increase of it input voltage source (Vdc), such as 2Vdc, Vdc, 0, -Vdc and -2Vdc. The resultant AC output power swing from +2Vdc to -2Vdc through zero level.
Process of MLI is determined base on the state of the switch-closed and switch-open state of each semiconductor plans. Pattern of the switch state will decide output value of the inverter. In the five -level CHB-MLI there are five potential pattern of the switching state. The output voltage of each prototype can be give details as follow:
State-1:
In this process the IGBT-1, IGBT-2, IGBT-5, IGBT-6, are closed, therefore the output voltage is 2 time of Vdc.
Multi Level Inverters (MLI) has developed into extensive and immense arrangement of technology. Day by day, there are hundred thousand of inverters accessible all over the globe although multilevel inverters appear with great advantages and abilities. One of them is Cascaded H Bridge inverter (CHB). briefly, the reward of CHB multilevel inverter are focus in the development of output
State-2:
In this process the IGBT-1, IGBT-2, IGBT-6,
signal quality and beat the high risk injure of power device damage for being unsuccessful to attain preferred voltage and current rating. Multilevel inverter are developed in way to conquer some boundaries of the conventional inverter with a number of inspiring features which is excellent with able to produce output voltage and draw current with lowest
IGBT-8, are closed, therefore the output voltage is Vdc.
State-3:
In this process the IGBT-2 IGBT-4, IGBT-6 IGBT- 8 are closed, therefore the output voltage is 0 volt.
State-5:
In this process when IGBT-3 IGBT-4, IGBT-7 IGBT-8, are closed, therefore the output voltage is 2 time of
Vdc (negative polarity).
-
PI Control
First of all, control in this sense means closed-loop control. That is, the controller has a number of feedbacks or idea of the response of the machine being controlled. An instance is a motor being controlled as the controller is using a sensor to decide its speed. Below is a plan of a conventional PI controller. P stands for proportional and I stand for integral.
State-4:
In this process when IGBT-3 IGBT-4, IGBT-6
Each of the part has a steady coefficients Kp and Ki. These constants are the modification values and
IGBT-8, are closed, therefore the output voltage is Vdc
(negative polarity).
represent how much the course control relies on the P and I. The PI controller equation is provided below:
The simulation circuit for the svpwm base vector control of induction motor is provided below:
In this, the induction motor of 10 HP, 400V, 50 Hz, 1500 rpm is power-driven by voltage source converter among SVPWM based vector control. The speed reference is changed from 150 rad/s to 100 rad/s at t=5s and torque is diverse from 10Nm to 20Nm at t=3s. The vector control circuit with speed, flux and torque view is provided below:
In this, the reference speed is compare with predictable speed and the mistake in pace is provide to PI controller which generate reference torque. It is then comparing with predictable torque and the fault in torque is providing to PI controller which generate Vq. likewise for flux control, Vd is generated from PI controller using fault in flux. It is then subjected to park transformation which provides 3 phase reference signals from Vd and Vq.
The calculated speed and torque waveforms with corresponding references are provided below:
The speed and flux waveforms are provided below:
At first, there is variation in flux and it steadily settled at reference flux.
The Vd and Vq waveforms along with reference voltages are provided below
CONCLUSION
Five level Inverter fed induction motor drive are simulated using the blocks of Simulink. It is observed That the total harmonics distortion produced by the five level inverter is more. The Simulation results of Voltage ,current, speed and spectrum are presented. This drive system can be used in industries where adjustable speed drives are required to produce output with reduced harmonic content.
REFERENCES
[1] N. Mittal, B. Singh, S.P. Singh, R. Dixit and D. Komar,Multi-level inverter: a literature survey on topologiesand control strategies, ICPCES, 2nd InternationalConference on Power, Control and Embedded Systems,2012. [2] M.G.H. Aghdam, S.S. Fathi and A. Ghasemi, Theanalysis of conduction and switching losses in threephaseOHSW multilevel inverter using switchingfunctions, IEE PEDS 2005, Vol. 1, pp. 209- 218, 2005. [3] Jagdish Kumar, Biswarup Das and Pramod Agarwal,selective harmonic elimination technique for amultilevel inverter, 15th National Power SystemConference (NPSC), December 16-18, 2008, paper no.168, pp. 608-613, IIT Bombay, December, 2008. [4] Jagdish Kumar, THD analysis for different levels ofcascaded multilevel inverters for industrialapplications, International Journal of EmergingTechnology and Advanced Engineering (IJETAE),Vol.2, Issue 10, pp.237-244, October 2012
[5] J. Holtz, Sensorless control of induction machines – with or without signal injection?, IEEE Transactions on Industrial Electronics, Vol.53, No.1, Feb. 2006, pp.7-30. [6] J. Holtz, J. Quan, Sensorless vector control of induction motors at very low speed using a nonlinear inverter model and parameter identification, IEEE Transactions on Industry Applications, Vol.38, No.4, July/August 2002, pp.1087-1095. [7] M.P. Kazmierowski, L.G. Franquelo, J. Rodrigues, M.A. Perez, J.I. Leon, High-performancemotor drives, IEEE Industrial Electronics Magazine, September 2011, pp.6-26. [8] Lazhar Ben-Brahim, Susumu Tadakuma, Alper Akdag, Speed control of induction motor without rotational transducers, IEEE Transactions on Industry Applications, Vol.35, No.4, Jul/Aug 1999, pp.844-850.