
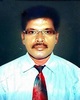
- Open Access
- Authors : Dr. M. V. Mallikarjuna , Zeeshan Ali , J R Priya , M Tejaswini , Soumya , Rohit
- Paper ID : IJERTV10IS040111
- Volume & Issue : Volume 10, Issue 04 (April 2021)
- Published (First Online): 27-04-2021
- ISSN (Online) : 2278-0181
- Publisher Name : IJERT
- License:
This work is licensed under a Creative Commons Attribution 4.0 International License
Smart Finger Millet Seed Extracting Machine
Dr. M. V. Mallikarjuna Zeeshan Ali
Professor, Assistant Professor
Department of Mechanical Engineering, Department of Mechanical Engineering Navodaya Institute of Technology, Navodaya Institute of technology
Raichur-584101, Karnataka, India. Raichur-584101, Karnataka, India
M. Tejaswini, J R Priya, Rohit, Soumya
UG Scholar,
Department of Mechanical Engineering Navodaya Institute of technology Raichur-584101, Karnataka, India.
Abstract The machine was being designed to replicate the manual beating method of ragi for threshing. Power was driven from an AC motor and was transmitted to a central shaft carrying the crushers via a belt drive. The key ideology of this project is by design the prototype with a cost-efficient threshing machine of ragi, which would cater the needs of people in the rural society.
Keywords AC motor, Belt drive,Finger millet threshing, Safe working.
-
INTRODUCTION:
Finger millet is harvested manually and transported to threshing yard, where it is threshed either by beating the crop manually with sticks or by treading under bullock feet, a practice followed by small and marginal farmers. In case of large scale threshing, bullock stone roller or a tractor with or without a stone roller is passed over the crop spread uniformly on the floor. Spreading of the finger millet crop on the tar road and waiting for transport vehicles to pass through is also a common practice followed by the villagers near the main roads for threshing the finger millet. These practices are time consuming, labor oriented, tedious and -uneconomical but also leading to considerable amount of loss of grain during the threshing process. Further, ultimately rains cause damage to the threshed crop if it is not cleaned, dried and stored quickly. This crop basically requires impact force for detachment of grain from ear heads and rubbing and shearing action to remove the husk/outer coating (glumes) of the grain. Finger millet is a highly vulnerable crop, once it reaches maturity any delay in harvesting means serious losses in volume as well as quality. The threshers, which available in market for other crops, have played an important role as forerunners of labour saving techniques.
A threshing machine or thresher is a piece of farm equipment that threshers grain, that is, it removes the seeds from the stalks and husks.it does so by heating the plant to make with flails: such hand threshing was very laborious and time-consuming, taking about one quarter of agricultural labour by As Hand beating manually, Passing stone roller over the finger millet, Threshing on tar roads are time
consuming, labour oriented, tedious and uneconomical but also leading to considerable amount of loss grain during the threshing process
The thresher should use non-polluting resource, Easy to operate, safe working and should easily customize the need of farmers of Indian society the 18th century. Mechanization of this process removed a substantial amount of drudgery from farm labour. The first threshing machine was invented circa 1786 by the Scottish engineer Andrew Meikle, and the subsequent adoption of such machines was one of the earlier examples of the mechanization of agriculture. During the 19th century, threshers and mechanical reapers binders gradually became widespread and made grain production much less laborious. Separate reaper-binders and threshers have largely been replaced by machines that combine all of their functions that are combine harvesters or combines. However, the simpler machines remain important as appropriate technology in low-capital farming contexts, both in developing countries and in developed countries on small farms that strive for especially high levels of self-sufficiency.
-
LITERATURE REVIEW
ANKIT DAS et.al The machine was being designed to replicate the manual beating method of ragi for threshing. Power was driven from an AC motor and was transmitted to a central shaft carrying the crushers via a V-belt drive. The central shaft is supported via pillow block bearings from the frame. When the central shaft rotates, the crusher arrangement also rotates inside a closed drum, and the unprocessed ragi is threshed on the obstructers, Hence separating the seed from its husk. However there are still some problems to be ironed out like the winnowing mechanism, better efficiency and refinement of the model.
PARMANAND et.al This paper deals with the development of a pedal operated domesticated cereal grain. Pedal operated thresher for minor millets with spike-tooth type threshing cylinder was designed, fabricated and tested.
This machine basically consists of four major components: feeding, threshing, cleaning and power
transmission mechanism. The developed millet thresher has the ability to winnow the premature grains and leaves, which are often lighter, thus, leaving aside the massy grains that, will be collected.it is beneficial for farmers with reduced time of operation, reduction in breakage of the grains and separation of the stalk from the grains. This machine is economically viable.
metal which is formed in the shape that is shown in the fig below. The bottom square outlet directs the crops to the roller and the width of it is as same as the width of the first set of rollers. The hopper can also be used as storage unit as well as the feeder to direct the crops.
PRASANNA KUMARet.alThe research was conducted on evaluation and testing of threshing methods for finger millet. More mechanical damage occurs during threshing process. At present there is a little information available regarding mechanical threshers. In ragi threshing method, theraspbar thresher has given the
max grains output of 140.5 kg/hr for variety MR1 and
130.3 kg/h for variety for HR911.The raspbar type thresher showed the least cost for MR1 Rs.18.4 and HR911 Rs.19.5/q for threshing operation compared to other three threshing methods. There was not much difference in threshing cost between varieties. Even though the mechanical damage to grain was high and germination of seed was less when threshed at lower (10%) grain moisture content. The output of the threshed grain, threshing efficiency and cost of threshing
-
ROLLER
FIG 1: Hopper
operation were lower. So threshing of ragi crop at 10 to 13 % grain moisture content is recommended for adoption.
Methodology Flow chart:
Raw material
Raw material
The drive roller is powered by the V belt assembly which
is connected to an Alternating current motor. Pair of identical rubber coated rollers of the same mechanism with smaller dimensions and lesser offset distance is placed below the first set of rollers. The second sets of rollers are provided for further effective threshing. Since rubber material is coated upon the roller it gives the rubbing action as same as the tar road threshing when a vehicle tire pass on it .
hopper
hopper
Passing through rollers
Passing through rollers
. Vibrating machine to separate grain particles
-
VIBRATING TRAY
FIG 2 : ROLLER
Collector
Collector
-
-
COMPONENTS OF MACHINE
A. HOPPER
The tapered hopper which is place at the top. The hopper is tapered at an angle of 60 degree to 65degree which helps the crop to slide easily. The hopper is made up of a sheet
The threshed ragi will be accumulated at the first stage sieving assembly which is inclined at an angle of 15degree while it will be further threshed by the second stage fine mesed vibrator of same angle inclination.Although some tiny foreign particles which are mixed with ragi will be collected in this second stage.A bin will be placed below the second stage fine meshed vibrator to collect the fine grained ragi,which is ready for the commercial usage.
FIG :3 Vibrating try
-
WORKING PRINCIPLE OF SEED EXTRACTING MACHINE:
Threshing mechanism is provided to separate the grains from the straws. The finger millet earheads are fed to the rollers via hopper from the top, the rollers are driven by AC motor through belt drives. The earheads of the finger millet flows into the first set of rollers, which is coated by the rubber material to avoid damaging to the grains. In the first set of rollers earheads partially crushed, the crushed grains are further crushed to obtain finger millet in second set of rollers. The outcome of the second set of rollers consist both finger millet and earheads which are separated by a sieving mechanism, which are reciprocated in the horizontal direction. The finger millet falls to the tray directly from the sieve whereas the earheads comes out from the runner which is aligned proportional to the first set of sieves.
The counter motion of the rollers is obtained in the parallel axis of the roller by using the cross belt drive for the counter clockwise motion .The conceptual sketch had been modelled The finger millet earheads are fed to the rollers via hopper from the top, the rollers are driven by 0.5HP AC motor through v-belt drives. The earheads of the finger millet flows into the first set of rollers, which is covered by the rubber material to avoid damaging to the grains. The distance between the first set of rollers is around 5mm where the earheads are partially crushed, the crushed grains are further crushed to obtain finger millet in the second set of rollers, where the distance between the rollers is around 3mm.The outcome of the second set of rollers consist both finger millet and earheads which are separated by a sieving mechanism
,which are reciprocated in the horizontal direction with the aid of slider crank assembly which is driven a secondary DC motor. The finger millet falls to the tray directly from the sieve whereas the earheads comes out from the runner which is aligned proportional to the sieve.
-
DESIGN PROCEDURE:
For manufacturing finger millet threshing machine, after arriving to the final concept design the 3D assembly design along with the individual part drawing with dimensioning are
generated using software. While designing the following considerations are made:
*The height ,width and length of the attachment are fixed to (1341.12 *370*830)mm as the attachment is to be compact and of less weight.
*wherever it is possible standard elements are used in the design in order to reduce the cost and to make the assembly as simple.
*The body is made of sheet metal of gauge 11, L angle structural member can for additional support.
*For the threshing roller the standard seamless steel tube of diameter 160mm for the first set of rollers and 110mm for the second set of rollers is used.
*Mostly fasteners are used for assembling wherever its possible for easy dismantling, maintenance and to carry out correction works.
*For conveyer belt food grade PVC standard belt is selected.
*For roller AC 230v standard motor with 0.5HP capacity is selected and fixed in the attachment.
*In order to transmit power to the various mechanisms like threshing roller, cam For transmission of power V belts are used in the attachment.
* A slider crank mechanism is used to transmit the power for vibrating tray assembly.
*The containers for grain collection and the straw collection designed in such a way that can be easily detached from the attachment whenever it is filled.
FIG 4 : POWER TRANSMISSION
TABLE I. PERFOMANCE ANALYSIS OF SEED EXTRACTING MACHINE
METHODS OF THRESHING
OUTPUT CAPACITY
BROKEN (%)
UNTRESHED GRAIN
THRESHING EFFICIENCY
STONE ROLLER WITH BALL
164.95
2.47
3.35
96.65
THRESHING ON ROADS
253.50
1.56
2.69
97.31
THRESHING USING MASSIVE MACHINES
230.00
2.90
0.80
99.18
FINGER MILLET THRESHER
240.0
1.50
2.00
98.00
CHART: 1
*From the above comparison graph we can say that stone roller, threshingonthar roads, massive machines having lessoutput capacity
*Broken grains are high in the stone roller compare to finger millet thresher
*Broken grains are less in the finger millet thresher compare to the other methods
CHART:2
*In this above graph threshing efficiency is higher in massive machine compare to the stone roller and threshing on tar roads.
-
ENVIRONMENTAL IMPACT:
The entire machine runs on electric power hence it is eco- friendly no dust or pollutants are emitted by this machine. Accidents that occur in the road fed methods are been
eliminated hence the roads are the high way environment are kept clean in the country side and makes way for vehicles to travel easily. Animal are not harmed as it is traditional way for threshing in villages. It occupies very little space and hence separate threshing land or parking land for machines is not necessary.
-
HUMAN SAFETY ASPECTS:
Since there will be no use of sharp edge blades for cutting the ear heads into tiny pieces human safety is much concerned. Since the entire machine movable parts are covered with the sheet metal no bare fingers are stuck into the machine. Since there is a hopper for loading and storage threshing will not damage human eyes or hands.The noise of the machine is minimum
-
COST CONSIDERATIONS:
We can clearly analyze that the cost of the massive machines is maximum that is starting from 200000.whereas the second max is the stone roller with bull is 50,000 .when considering the finger millet thresher that is fabricated costs up to 21,000 which stands the second cheapest method of threshing of the finger millet, standing the lowest is the threshing technique on tar roads which cost nil as investment for the farmers.
The cost of the entire machine might see affordable to the poor farmers but, a much deduced amount of cost of the same machine can be manufactured when it is mass manufactured.
-
SCOPE:
We can use multiple set of rollers in series for more efficient threshing instead of repeating the feed
Integrating a blower for blowing the tiny parts of dust can be a good idea to improve the cleaning process
Polishing process of the ragi can also be included in the same machine by using more vibrating power
Same mechanism can also be used in a larger scale for more input of the crop
We can use many types of grains to thresh of ragi
By removing the rubber coating and using steel roller with minimum gap between those parallel rollers we can also get flakes of grains.
FIG 5: Finger Millet Treshing Machine
-
CONCLUSION:
The fabricated finger millet thresher is an affordable machine for the poor farmers of the Indian society, whereas this is not the ultimate equipment or a method for finger millet threshing, while it is very much needful machine for the farmers, who holds very less capacity of land who cannot afford the rent or the labour of the massive machines.
The maintenance of the machine is also not complicated so the farmer himself can do it with some minimum labour or equipment for the service of this machine. Since this is powered by the electric motor the farmers get some subsidiary in the electric supplies in Indian villages henceno need to travel miles to carry the fuel to drive the machine
.The further development of this method can completely eliminate the use of the traditional methods like stone roller using bulls and threshing on tar roads which leads to plenty of problems to the environment and society as said so
REFERENCES
-
Design and Fabrication of a Prototype Of Ragi (Finger Millet) Threshing and Winnowing Machine [1] Ankit Das, [2] Mukul Kumar, [3] Dechamma K.S, [4] Kishore Kumar, [5] Lokesh G Reddy [1][2][3][4][5] Department of Mechanical Engineering,
Vemana Institute of Technology
-
Parmanand, Verma, Ajay, Verma, P.D. and Guru, Prabhat Kumar (2015). Development of pedal operated thresher for finger millets. Internat. J. Agric. Engg.,8(2) : 175-180.
-
Hanumantharaju. K.N., Development of Power Operated Thresher for Finger Millet, Department of Agricultural Engineering, University of Agricultural Sciences, Bangalore, 2012.
-
A. Sreenatha, G.P. Jayapalaiah and N. Indrakumar, Finger millet harvesting and threshing in Karnataka, International Journal of Agricultural Engineering, Vol. 3 No. 2 (October, 2010).
-
Adikant Pradhan, SK Nag, SK Patil, Traditional technique of harvesting and processing of small millets in tribal region of Bastar, Indian Journal of Traditional Knowledge Vol. 9(4), October 2010.
-
Prasanna Kumar and D. B. Naveen Kumar, Performance evaluation of threshing of finger millet by mechanical method, International Journal of Agricultural Engineering, Volume 5 Issue 2, October, 2012.
-
Agidi Gbabo, Ibrahim Mohammed Gana and Matthew Suberu Amoto, Design, fabrication and testing of a millet thresher, Net Journal of Agricultural Science Vol. 1(4), pp. 100-106, October 2013
-
Abo El-Naga, M.H.M., El-Gendy, H.A. and Mosa, E.H. (2015). Evaluation of locally threshing machine performance for threshing lentil crop. Misr Journal of Agricultural Engineering, 22(2): 376- 388.
-
Ajav, E.A. and Adejumo, B.A. (2005). Performance evaluation of an Okra thresher. Agricultural Engineering International: the CIGR Ejournal. Manuscript PM 04006, Vol. VII, October.
-
Bansal, N.K. and Lohan, S.K. (2009). Design and development of an Axial flow thresher for seed crops. Journal of Agricultural Engineering, 46(1):1-8
-
Baryeh, E.A. (2002) Physical properties of millet. Journal of Food Engineering, 51: 39-46.
-
Crawford, G.W. and Lee, G. (2003). Agricultural origins in the Korean Peninsula. Antiquity, 77(295):87-95.
-
Goyal, R. K., Vishwakarma, R. K. and Wanjari, O.D. (2008). Optimization of pigeon pea dehulling process. Biosystems Engineering, 99(1): 5661.
-
Kamble, H.G., Srivastava, A.P. and Panwar, J.S. (2003). Development and evaluation of a pearl millet thresher. Journal of Agricultural Engineering, 40(1): 18-25.
-
Kushwaha, H.L., Srivastava, A.P. and Singh, H. (2005). Development and performance evaluation of Okra seed extractor. International Commission of Agricultural Engineering, 7: 1-13.
-
Singh, K.P., Mishra, H.N., and Saha, S. (2011). Design, development and evaluation of Barnyard millet dehuller. Journal of Agricultural Engineering, 48 (3): 17-25.
-
Singh, S.K., Agarwal, U.S. and Saxena, R.P. (2004). Optimization of process parameters for milling of green gram (Phaseolusaures). Journal of Food Science and Technology, 41(2): 124-30.
-
Sinha, J.P., Dhaliwal, I.S., Sinha, S.N. and Dixit, A. (2007). Studies on machine crop parameters for chickpea seed crop threshing. International Commission of Agricultural Engineering, 26 (7): 1-9.
-
Tiwari, B.K., Jagan Mohan, R. and Bhasan, B.S. (2007). Effect of heat processing on milling of black gram and its end product quality. Journal of Food Engineering, 78: 356-60.
-
Ushakumari, S.R., Rastogi, N.K. and Malleshi, N.G. (2007). Optimization of process variables for the preparation of expanded finger millet using response surface methodology. Journal of Food Engineering, 82: 35-42.
.