
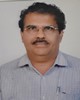
- Open Access
- Authors : P. Prakash , Dr. J. K. Kishore , C. S. Madhusudhana
- Paper ID : IJERTV10IS070080
- Volume & Issue : Volume 10, Issue 07 (July 2021)
- Published (First Online): 17-07-2021
- ISSN (Online) : 2278-0181
- Publisher Name : IJERT
- License:
This work is licensed under a Creative Commons Attribution 4.0 International License
Smart & Scalable Switched Capacitor (SaS-Sc) Li-Ion Cell Balancing Algorithm Implementation For Space Applications
P. Prakash |
Dr. J. K. Kishore |
C. S. Madhusudhana |
Scientist/Engr. |
Senior Scientist |
Senior Scientist |
UR Rao satellite Centre, |
UR Rao satellite Centre, |
UR Rao satellite Centre, |
ISRO, Bangalore-560017 |
ISRO, Bangalore-560017 |
ISRO, Bangalore-560017 |
Abstract:- Rechargeable batteries are used in a S/C to support power requirements during eclipse and other peak power requirement during sunlit. The introduction of Li-ion batteries with higher energy density represents a turning point for spacecraft and mission management to optimize weight and volume as compared to Ni-H2 and Ni-Cd Cells. Li-ion batteries have been successfully used in space missions with widely varying voltage / Ampere-hours capacity from small satellite, high power satellite, human flight missions and deep space missions. The GEO S/C undergoes 90 and a typical LEO S/C undergoes 5500 eclipses of varying duration per year. During eclipse, electric power must be supplied by batteries which are recharged by the solar panels when the spacecraft re-emerges into sunlight. In addition, there are some instances when batteries are called upon to provide peak power at the time of imaging and thruster firing etc.
The main disadvantage of Li-ion battery is its susceptibility for overcharge, under voltage and cell voltage dispersion. These limitations need to be monitored and corrected during cell balancing for safe operation of the battery. In this research work, a smart and scalable switched capacitor charge transfer algorithm across the cell using a microcontroller and super capacitor has been adopted which minimizes the power loss and associated thermal management problem compared to dissipative methods. Here, the cell balancing is done continuously, dispersion is minimized, and more power can be drawn from the battery pack. Hence longevity of the of the satellite can be improved by 5-10%, if other life determining factors are not altered. Li-ion batteries have been successfully used in space missions and can be scaled to other automotive and industrial applications.
Key words: Smart &scalable; switched capacitor; Low earth orbit; Geo stationary earth orbit; Battery management system; Lithium-ion cell balancing algorithm; Spacecraft batteries.
-
INTRODUCTION
To meet the requirement of large no. of satellites for various applications, significant change in power generation, distribution and storage is envisaged. Li-ion and Li-polymer cells are the most suitable storage cells [1] with low weight and volume to meet the eclipse and other peak power demands. The battery options available for a spacecraft are mentioned at table-1. From this table it can be deciphered that Lithium based cells are far superior compared to other electro chemistries [2].
-
Li-ion has a higher terminal voltage of 4.2V and hence requires lesser cells in series-parallel configuration for a particular power requirement.
-
They have low self-discharge, long cycle life, almost no maintenance, wide operating temperature and lower size compared to Ni-Cd/Ni-H2 batteries. [3]
TABLE-1: BATTERY OPTIONS FOR A S/C
BATTERY OPTIONS FOR AVAILABLE FOR S/C & COMPARISON
Specification
Load acid
NiCd
NiH2
Li-ion
Cobalt
Mang anese
phosphate
Specific energy density (Wh/Kq)
30-50
45-80
60-
120
150-190
100-
135
90-120
Internal resistance (m ohm)
<100 12V
Pack
100-
200
6V
pack
200-
300
6V
Pack
150-300
7.2V
25-75
per cell
25-50 Per
cell
Over charge/under charge capability
High
Mode rate
Low
Low cant tolerate
Self discharge/mo nth
(room temp)
10-
15%
20%
30%
<10%
Cell voltage (nominal)
2V
1.2V
1.2V
3.6V-4.2V
Maintenance requirement
3-6
mont hs (Char ge up to)
30-60
days (Need Disch arge)
60-
90
days (Disc harge
)
Not required
Safety requirements/ balancing
Ther mally stable
Thermally stable, fuse protection is commonly used
Protection circuit mandatory
-
Disadvantages of Li-ion cells
-
Sensitive to overcharge and discharge
-
Cell voltage dispersion at the time of manufacture and during field use
-
Persistent over charge and discharge may results in capacity fading.[3]
-
-
Energy density comparison
Fig.1 shows the plot of volumetric energy density in Wh/l vs. galvanic energy density in Wh/Kg. It can be inferred that Lithium based cells have highest volumetric energy density compared to other types of cells and hence it is preferred for space use.[4]
Fig.1. Energy density comparison
-
Size and weight comparison
Fig. 2 shows the plot of volumetric energy density in Wh/l vs. specific energy density Wh/Kg. It can be concluded that Li based batteries are lighter in weight and smaller in size for a specific power requirement [4].
Fig.2. Size and weight comparison
-
Causes of Cell imbalance
The cause of imbalance in the cell voltage is due the following reasons.
-
Difference in the internal resistance
-
Manufacturing tolerances
-
Uncertainty in the exact replication of electrochemistry across cells in a battery pack.
-
Hence balancing & protection circuit is mandatory for Li based high powered rechargeable cells used for space applications [5].
-
-
APPROACHES FOR CELL BALANCING Cell balancing can be accomplished by many methods. It
is critical for a space mission to reduce the power disipation since the power available is limited to the solar array strings being carried with the spacecraft mission. There is no room to spend energy sumptuously and hence shall be preserved and maintained. The balancing shall be accomplished by the following methods.[6]
-
Passive cell balancing Resistive method
-
Active cell balancing Analog/Digital approach
-
Passive balancing
In this method, removal of excess charge is done by using resistor, capacitors or inductors until the cell voltages matches with the low voltage cell. Some of the schemes used in a conventional battery management system is switched resistor method.
-
Active balancing
Active cell balancing methods remove charge from one or more high voltage cells and switch back the charge to one or more lower charged cells. It is difficult to provide independent charging for all the individual cells in a battery pack with state of charge control. Some active cell balancing scheme are designed to stop when it is fully charged and allowing other cells to reach the designated voltage. But this method is highly time consuming. Hence SaS-SC cell balancing algorithm is discussed and implemented in this paper.
-
Disadvantages of passive cell balancing
Traditionally, passive approaches have been used for balancing the cells of Li ion battery and it is done close to the peak value of 4.2V. This results in certain limitations like higher thermal dissipation in the spacecraft, poor efficiency, and hence more complex thermal management system [7].
-
-
SAS-SC BATTERY MANAGEMENT SYSTEM A smart and scalable switched capacitor (SaS-SC)
algorithm has been designed and implemented for cell balancing, monitoring and protection functions for battery Management System (BMS). This algorithm is scalable to any types of satellite [8][9], other Industrial applications and Electric vehicles. Depending on the series parallel configuration of cells in a battery pack, No. of stages in the cell switching network and the microcontroller programme can be altered to provide charge equalization. The basic
principle and algorithm remain the same. Hence it can be scaled up or scaled down depends on the battery pack very easily. In this algorithm, the cell with the highest SoC is selected using a microcontroller and switched to a super capacitor. In the next cycle, the super capacitor is switched back to the cell having the least SoC. The charge transfer is accomplished using a bidirectional MOSFET switching network with exceedingly small Rds-on from the cell to the super capacitor and vice versa [8].The charge transfer can be controlled by varying the duty cycle of PWM signal generated from microcontroller. Max switching frequency is set at 100 KHz with 40% duty cycle. Charge/discharge current during switched capacitor charge transfer is restricted to 3.0A. The charging current is monitored using Hall Effect current sensor [10].If the system faces an error, an error flag is raised and shifts to a disabled state. Here, the cell balancing is done continuously and thus the dispersion is reduced in the battery pack. Hence more power can be drawn from the battery pack and power dissipation is minimum compared to dissipative method. By balancing the cells in a battery pack, the overall life of the battery and hence the satellite mission can be increased by 5-10%, [9] [10] if all other life determining factors are adequate to meet the mission needs. Fig.3 shows the main constituent elements of the battery management system.
Fig.3. Constituent elements of SaS-SC BMS
-
Process flow algorithm
The process flow of the balancing algorithm is mentioned at Fig. 4.
Process: The cell with highest SoC is selected using a microcontroller through an analog multiplexer. These cell voltages are digitized and compared to find cell with largest SoC. The switching is done using a bidirectional MOSFET switch matrix. Initially the cells are charged to around 38V to reduce the switching current. The charge transfer current is controlled by varying the duty cycle of PWM signal generated by the microcontroller [11].
Fig.4. SaS-SC BMS Process algorithm
A voltage low flag is raised when the cell voltage goes below a set lower threshold or if all the cells attain same voltage, but less than 4.2V. Once the cells reaches with a dispersion less than 10mV, balancing process is terminated and the state changes to idle.
-
SaS-SC Flow diagram
Fig.5. SaS-SC BMS Flow diagram
Fig. 5(a) and (b) shows the SaS-SC flow diagram. Initially the cells and the capacitors are charged to 3.8V before the balancing action to reduce the charge/ discharge inrush current. The cells are charged from solar array string continuously and at predetermined level, charging action will be discontinued and balancing action will be initiated. When the microcontroller programme initialised, it will read out all the cell voltages. These cell SoCs are compared and cell with highest SoC is identified. This high SoC cell is switched to the super capacitor. Then the additional charges in Super capacitors are switched to the cells having low SoC.
Fig.5b SaS-SC BMS Flow diagram contd…
This action continues till all the cells are balanced [14]. Protection scheme is enabled whenever the set levels like cell upper voltage, Lower voltage, charge/discharge currents and temperature etc exceeds the set value to protect the cells from damage. The cell voltage, battery voltage etc can be monitored through telemetry signals. End of balancing SoC levels of battery can be set by tele- command signal [15] from ground stations.
-
SaS-SC CB Development stages
Fig.6. SaS-SC BMS development stages
The development cycle consists of battery interface circuit, control circuit, protection circuit and Monitoring circuit design and programming the microcontroller to execute the switched capacitor algorithm as shown in Fig.7.
-
Features of SaS-SC BMS
This technique is designed for controlling the charge and discharge currents going in to and out of the battery pack. The primary feature of this algorithm is to limit the overcharge, over discharge and balance the cells in the pack. Other important feature of this algorithm is cell voltage monitoring, battery voltage monitoring and cell bypassing.
-
Simulation of algorithm
-
The designed SaS-SC Li-ion cell balancing algorithm is simulated using the MATLAB and Simulink software and the results are encouraging.
-
The prototype has been realized and tested. It can be scaled to industrial and electric vehicles applications, which also make extensive use of Li- ion batteries.
-
-
Proof of concept using Simulink Model
Fig. 7 shows the Simulink model for SaS-SC cell balancing algorithm in a BMS [14][15].
Fig.7. Simulink Model of BMS
-
Cell SoC convergence plot
Cells with random SoC are considered for simulation. Simulink model is activated by Matlab s/w. Initially the cell voltage values are read by the software and are compared with the end of charge (EoC) voltage. If any cell voltage is more than the EoC voltage level set, that cell voltage is replaced with EoC voltage. If the cell voltage is less than EoC voltage level set, the program finds the cells with lowest and the highest cell voltage. The algorithm connects the cell with highest cell voltage to a super capacitor through an array of MOSFET switches. After a pre-determined cycle time, the capacitor gets connected to the cell having the lowest voltage. The cycle time is programmable through a delay subroutine.
If the current through the MOSFET switch is above a predetermined level, the discharge of highest cell voltage to the super capacitor is terminated to the maximum allowable current level during switched capacitor charge equalization process. In the next cycle, a small incremental voltage is added with the initial cell voltage randomy to simulate constant current charging process of the spacecraft solar array charger string. The upper and lower limits of the incremental charge addition to the cells randomly can be altered as desired. This programmability is added to simulate battery charging process with different rates. The highest cell voltages are found in each cycle and are replaced with the cell having the lowest voltage until all the cell voltages reach the tele-command controlled EoC value. The discharge time, typically 1msec duration is programmed by calling a delay subroutine [16] in the MATLAB S/W. The cell voltage and SoC convergence are plotted graphically as shown in Fig 8 and 9 respectively.
Fig.8. Battery SoC convergence plot
The voltage build-up of each cell can be plotted by varying the incremental voltage to simulate the PWM control of the MOSFET switch array. The limitation of the switched capacitor algorithm is its low balancing speed [19];however, this method is highly efficient and the hardware requirement is very minimal.
-
Cell Voltage convergence plot
Cells with random voltage are considered initially. Simulink model is generated/activated by Matlab S/W. Cell voltage convergence is a function of Initial cell voltage, switching frequency, delay time and the set charge current [20]. The cell voltages are fed from a cell simulator for simulation purpose. The cell simulator consists of 10 cells whose voltage can be varied from 2.5 to 4.5 volts. A solar array simulator is used for charging the battery module at a constant current of 1.6 Amp as used in a typical satellite programme [2]. The transfer pulse (TP), clock (CLK) and data are fed from a Telemetry and tele-command simulator (TM/TC) to set End of charge (EoC) voltage. The TP pulse is set at 64ms duration and the CLK pulse is set at 1 KHz. To set the EoC voltage at 39V, a data setting of C0 is fed from the simulator [10].
Fig.9. Battery voltage convergence plot
The data setting is altered to different level to verify the balancing action till End of charge (EoC) level. Initially the cell voltage is set between 3.8 to 4.1V for simulation purpose. Random voltage between 0.01 to 0.02V, corresponds to an SoC of 0.476% is generated and added to the cell TM to simulate different cell voltage condition and the program is run to find the convergence to the end of voltage. It is found that the cell voltage convergence time depends on the initial and final cell voltages, frequency of operation, cell series resistance, MOSFET series resistance and equivalent series resistance of the super-capacitor and the harness path resistance. The capacitor switching is also simulated using SIMULINK S/W [15]. The proposed balancing techniques reach the convergence within a differential of 10mVafter a balancing time of 2.3hrs, under the assumed initial and final SoC.
-
-
PROTOTYPE DEVELOPMENT
Proto-types development of battery management system is shown at Fig10. It consists of small 4 PCBs.
Fig.10. SaS-SC BMS Prototype
PCB#1: Consist of Battery, battery charging unit and voltage sensing circuit.
PCB#2: Consists of input buffers, Dual rail multiplexers, switching circuit and cell voltage amplification scheme.
PCB#3: Consists of Microcontroller circuit, LED display schemes and other peripherals.
PCB#4: Consists of Super capacitor, Bidirectional switching circuit
capacitor based on the SoC levels [19]. The switching frequency is 100KHz with 40-45% duty cycle. A delay of 100µsec is introduced before connecting the capacitor to cell and vice versa.
Fig.11. Configuration of Battery management system
-
Cell configuration in GEO S/C BMS
Fig.12. Battery configuration for a typical GEO spacecraft
Cells are connected to series & parallel to meet the vol. & AH requirement (10sx4p). To get a typical 42V bus voltage, 10 cells are configured in series as sown in Fig.11. Since we need 128AH battery for a typical high-power satellite [10],4 Nos. of 32AH battery is paralleled. Since analog mux cannot take more than 32V, voltage divider as shown in Fig. 12 is used.
-
-
SaS-SC BMS CONFIGURATION
Fig. 11 shows the configuration of SaS-SC Battery management system. It consists of a battery pack in 10Px4S configuration. An analog multiplexer is used to read the cell voltage. The A/D converter converts this analog signal into digital format. A microcontroller is used to perform the balancing action. The switching matrix is developed by an array of MOSFET switches. Demux selects the cells/super
Fig.13. Battery interface circuit
-
Cell voltage buffering &lification circuit
The divided voltages from the resistive network will be V1 to V11 as shown in Fig.13. This voltage is fed to an analog multiplexer through a voltage follower. Here op-amp, LM324, is used as a buffer, which adds an additional protection for the analog multiplexer. Buffer is used to isolate multiplexer from the cell division circuit and helps to reduce the voltage drop due to loading effect. The LM324 is a quad operational amplifier with true differential inputs. This op-amp can work for a supply voltage of 3.0 to 32V with minimum quiescent current. The cell voltages are divided with reference to the ground [20] so that the final range of voltage will be shifted to negative rail, so the bias voltage range of the op-amp should be in dual rail (+/- 21V).The buffered outputs are fed directly to the inputs of the analog dual rail multiplexer [21].
Fig.14. Cell amplification scheme
-
Control circuit design
The control circuit is shown in Fig. 14. Parallel Interfacecontroller (PIC) 18F 4520 is used in the design having 5 Bidirectional Ports [22],10-bit ADC etc. Cell vol. measurement is done through ADC Channel No. 0, Cell temp. is monitored through ADC channel No. 1, Input current from Solar array is fed to ADC Ch. No. 2, Cell balancing current is measured through ADC Ch No. 3, CCP: capture/compare/protect is used for handling timers, interrupts and PWM generation. 128Kb Flash memory is used for processing the cell SoC data [23][24].
Fig.15. Control circuit for BMS
Fig.16 shows the cell voltage switching matrix [25]. Depending upon the selection of odd or even MOSFET, the biasing shall be changed to select the appropriate switching matrix to transfer the charges from the cells to the super capacitor and vice versa. MOSFETs witp6m Rds-on is used to reduce the power dissipation in the switching matrix.
Energy transferred to the switched capacitor can deduced as [27]:
E_ cap_SC. = C. Vdiff. {[ Vdiff./2.e 2D/ F Vf .e e2D/ F] [ Vdiff./2 – Vdiff }} * F.(Wh/h )
Energy transferred to the cell can be deduced as:
E_ cell= C. Vdiff. {[ Vdiff./2.e 2D/ F + Vi.e2D/ F] [ Vdiff./2 + Vdiff]}* F (Wh/h).
E. Cell charging scheme
SPST
Charge/Di scharge
Charge/Di scharge
Fig.16. Charge transfer network
Action: Fig.15 shows the cell voltage switching network [26]. Assume, V1 is selected by the controller for transferring charge from the cell to super capacitor. Then the switching action for the charge transfer from V1 is as follows.
Solar array
DPST
load
load
Isolator
Li-ioncell bank
Li-ioncell bank
-
M1, M2, M3 and M4 will be switched ON
-
V1 voltage will reflect across POS-1 and NEG-1
-
Since V1 is odd cell, M23, M24, M25 and M26 will be turned ON using the gate pulse of M1, M2, M3 and M4.
Hence effectively V1 gets connected to Super capacitor. Assume V4 is the cell with low SoC. The charge transfer path is CAP +ve, M30, M29, NEG, M8, M7, V4, M9, M10,
POS3, M27, M28, CAP ve. Table2 shows the main components used in the switching Matrix
TABLE-2. LIST OF COMPONENTS USED
Sl. No
Component
Value
M1 M33
Mosfet
140NF55
D1 D20
Diode
1N5806
V1 V10
Li-ion cells
18650
T1
Transformer
55206
SC
Super capacitor
5.4V,50F
-
-
SaS-SC modeling
Using the charge transfer model, the time needed for SaS-SC balancing time can be determined. The balancing time is decided by the on-time of the switching MOSFET, frequency of switching, duty cycle of the switching elements, initial state of charge of capacitor and cells and series resistance of the connecting harness [26].
Capacitor charging current [27],
IC = C.dVc/dt, Which is equal to, C.1/. Vdiff.e1/ Hence Imax = Max. value of Ic = Vdiff/Rs (eqv).e1/
Where Rs(eqv) depends on frequency of operation of MOSFET and duty cycle. This current Ic is needed to
design the optimum switched capacitor network. is the time constant, equal to (R cell + ESR) C RS (eqv) = 1/fC. (1+ e-DT/ )/ (1- e-DT/ )
SaS-SC
Balancing Scheme
SaS-SC
Balancing Scheme
Isolator
Fig.17. Cell charging scheme
Bought down to around 3.5V. Before balancing, the cells are charged to 3.8V using solar array charger string [9] as shown in Fig. 16& 17.Cell balancing is undertaken if the battery voltage reaches 38V.This method is adopted to reduce the cell balancing current
Fig.18. Charge control circuit
-
Operation of the Overall Circuit
The End of charge(EOC) voltage, under voltage protection limit (UVP), over charge protection limit (OCP) voltages and battery voltage is initially read by the controller and stored into the memory. The cells are charged continuously by 1ampere constant current solar array charger strings [10].The cell voltages are monitored through a two- stage differential amplifier with an overall gain of unity using LM 124.The output of the differential amplifier is fed to a dual rail multiplexer circuit. The Mux address is selected and issued by the PIC microcontroller 18F4520. The cell voltages are digitized by the controller ADC and converted
in to an 8-bit digital data.The sample and hold circuit hold the cell voltage until conversion is completed.The start of conversion signals is issued by the controller [22]. The controller reads the converted signal once the End of conversion is available.
The high and low voltage cells are identified,and the high voltage cell is switched to the super capacitor through an array of MOSFETs.Then the controller switches the super capacitor to the low voltage cell.This process continues till the cells are perfectly balanced within an acceptable dispersion level. The super capacitor charge and discharge current is controlled by PWM method [28]. The cell OVP, UVP, charge and discharge current are monitored continuously, and interrupts are invoked, if it exceeds above the predetermined levels. The Li-ion cells degrade over its lifetime due to cell chemistry and temperature. Hence different data commands are needed to set the bypass voltage level for the entire life of the mission. The end of charge pre- set operation is done through tele-command signal issued from the ground station. This is monitored and controlled by the microcontroller.
-
-
BATTERY MONITORING SCHEME
A satellite requires continuous monitoring of cell and battery health parameters as shown in Fig 19 as part of its monitoring of health management routine [29]. Based on this data, automatic abortion of charge and discharge function can be initiated. It consists of the following.
-
Cell voltage monitoring
-
Battery voltage monitoring
-
Cell temperature monitoring
-
Charge current monitoring.
16×2 Character LCD is used to display all the needed information at ground level.
-
-
BATTERY PROTECTION SCHEMES
Fig 19 shows the summary of recoverable battery protection scheme.
Fig.19. Battery protection scheme
-
Overvoltage protection
In this scheme, the cell voltage is compared with a reference voltage equivalent to the maximum cell voltage of 4.2V. If the cell voltage reaches this set level, Interrupt service routine (ISR) will be invoked and hence further charging of the cell is prevented by disconnecting the charger string from the battery [30][31]. Fig. 20.0 shows the block schematic of OVP scheme.
Fig.20. Overvoltage protection scheme
-
Under voltage Protection
UVP scheme is like over voltage protection as shown in Fig.20. Here the comparator compares the cell voltage with a UVP reference voltage, and if the cell voltage falls below the set value due to any reason, ISR will be invoked and all user subsystem/loads will be disconnected from the bus [32]. In this scheme, the reference voltage is set in such a way that the temperature of the overall battery pack shall not exeed the set level of 30C as shown in Fig.21. Temperature sensing as shown in Fig.22 is provided using a Hall Effect sensor [2]. The output of the sensor is calibrated and adjusted to 0V when the battery temperature is 25C. If the
temperature is exceeded by 1C, the output of the sensor is changed to 10mV.
Fig.21. Under voltage protection scheme
If the temperature goes beyond 40C, ISR will be invoked, which will eventually disconnect the battery from charging/discharging [33][34].Similarly, battery charge current, battery balancing current etc is also being monitored and if it exceeds the set level, ISR will be invoked,and the intended function will be terminated [35] instantaneously.
Fig.22. Over temperature protection scheme
-
-
RELIABILITY MODELING AND ANALYSIS Using the component hazard rate model as mentioned in
table-3, balancing circuit failure rate has been calculated by considering a mission life of 15 years for GEO programme [10][37][38].The total number of components used for implementing this algorithm is around 170. Some of the main component Hazard rate model [39] mentioned below is used to estimate the reliability figure of this circuit.The base failure rate and factors/multipliers for each device is selected based on the style of the component, stress factors, maturity of the components in the field of operation, expected worst case environment etc [40].All these
reliability models are considered in series and the overall hazard rate is estimated.
Reliability of the SaS-SC circuit using part stress method has been estimated as per MIL-HDBK-217 notice-2 and MIL- STD-883 as 99.25% for a mission life of 15 years [41][42] and 99.42% for a mission life of 5 Years [2].
TABLE-3 HAZARD RATE MODEL AND PART F.R OF COMPONENTS
Sl. N
o
Part Name
Qty.
Component model
/Hr
.
1.
CMOS
Analog MUX/DEMU X- CD4067B
2
= (1
+ 2)
=4.05* 10-5
2.
IC-LM324
12
= (1
+ 2)
=0.487
2
3.
Transistor- 2N3019
1
=
=2.610 7*10-4
4.
Power MOSFET- 1RF540N
2
=
=0.021
74
5.
MAX232
1
= (1
+ 2)
=2.975
*10-5
6.
Ultralow Offset Voltage OP- AMP- OP07
6
= (1
+ 2)
=3.195
*10-4
7.
OPTO817
26
= (1
+ 2)
=1.342 25*10-3
8.
EEPROM- PIC18F2420
1
= (1 + 2
+ )
=2.682 5*10-5
9.
Resistor- RM1206
100
=
=0.015
4512
10.
Capacitor- CWR06
1
=
=1.058 4*10-5
11.
Capacitor- CDR35
16
=
=4.438 804*10-3
12.
Connector- DAM-15P- NMB-9015- MB
1
=
=0.126
0
13.
Connector- DSUBN-15S- PCB-9015
1
=
=2.976
*10-4
-
CONCLUSION
As Li-ion cells have higher energy density they have been successfully used in various spacecraft missions. Li- ion cells have a higher cell voltage of around 4.2V and hence require lesser cells in series-parallel configuration for a specific mission requirement as compared to other battery configurations. In addition, Li-ion cells have slow self- discharge, long cycle life, no maintenance, wide operating
temperature and lower size compared to Ni-Cd/Ni-H2 batteries. However, they also have certain limitations related to operational aspects as they are sensitive to overcharge and discharge of cells. Traditionally, analog passive approaches have been used for balancing the cells of Li ion battery and it is done close to the peak value of the S/C bus-voltage. This results in certain limitations like higher thermal dissipation, poor efficiencyand hence more complex thermal management. Cell balancing is needed to extract all the advantages of Li-ion cells and to minimize its shortcomings/ disadvantages.
In this research paper, an SaS-SC cell balancing algorithm has been implemented as part of the Battery Management system. The cell balancing is done continuously and thus the dispersion is minimized. Hence more power can be drawn from the battery pack. The SaS- SC charge transfer algorithm across the cells eliminates the power loss and associated thermal management problem compared to dissipative methods. By balancing the cells in a battery pack, the overall life of the battery and hence the satellite can be increased by 5-10%, if other life determining factors are kept constant.
Proposed battery management scheme significantly aids to miniaturize the existing hardware being used in a spacecraft and integrates individual cell voltage monitoring, battery voltage monitoring, Cell balancing function etc. using a microcontroller and super capacitor. This algorithm has been simulated using the MATLAB and Simulink software and the results are encouraging. The prototype of this algorithm has been realised, tested and validated. The main advantage of SaS-SC circuit compared to the existing conventional techniques is low hardware requirement, less weight and volume. This circuit is variably pre-settable for the end of balancing voltage through ground command, since the li-ion cell In this circuit simulation of different cell voltages with a dispersion of 0.1V, correspond to an SoC of around 2% are fed to the circuit and a balancing action/run is carried out. The number of cycles needed for convergence will be typically around 18×105-20×105 cycles under a particular initial condition of the cells, state of charge of super capacitor, switching frequency, duty cycle of the switching signal and overall path resistance of the charge transfer path. The designed circuit can be used across all types of space mission and can be scalable for other application like DC homes and Electric vehicles.
REFERENCES
-
V Etacheri, R marom, R Elazari, et.al; Challenges in the development of advanced Li-ion batteries: a review published in the journal-Energy & Environmental Sciences, 2011.
-
Mukund. R Patel, Introduction to electrical power and power electronics, CRC Press, first edition, 2013.
-
David Andrea, Battery management system for Large Li-ion battery packs, Artech House, edition 2010, ISBN-13 978-1- 60807-104-3, British Library cataloguing in publication Data.
-
W.H.Bently, Benchmark Microelectronic.Inc., Dalls, TX,USA,Cell balancing considerations for lithium-ion battery systems,IEEE Explore:2006
-
Kong. Z; Zhu.C; Lu.R; Cheng.S, Comparison and evaluation of charge equalization techniques for series connected batteries. In proceeding of the 13th IEEE Power electronics
Specialists Conference (PESC06), Jeju, South Korea, 18-22- June 2006; pp.1-6.
-
DorinCadar, DorinPetreus, TomaPatarau, NiculaiePaladhita; Active balancing method for battery cell equalization, Technical University of Cluj-Napoca, faculty of electronics, Telecommunications and information Technology, Cluj- Napoca, Romania.
-
Dr.Sam Nork and Kevin Scott; advantages and disadvantages of passive cell balancing; technical article, Analog device.Inc.
-
Tom Hoeger, Battery management system-Design for Li-ion batteries-A holistic approach, Advanced power and energy group, NSWC cardeorock, Spectrum technology group, Inc..
-
B.N Agarwal,Design of Geosynchronous Spacecraft, Prentice Hall publication 1986.
-
Dr.Dharma P. Agrawal and Dr.Qing-An Zeng, Satellite Systems, McGraw-Hill publication,3rd Edition-2002.
-
Lindemark, B. Individual Cell Voltage equalizers (ICE) for reliable battery performance. In proceedings of the 13thinternational telecommunications energy conference (INTELEC91), Kyoto, Japan, 5-8 November 1991; pp.196- 201.
-
Phillip Weicker,A system approach to Li-ion battery management;Artech house;ISBN 13:978-1-60807-659-8
-
Stuart, T.A; Wei, Z.Fast equalization for large batteries.IEEE Aerospace Electronics System Magazine-2009, 24, 27-31.
-
Rolland Priemer; MATLAB for electrical and computer Engineering students and professionals: with Simulink,Sci- Tech publishing Inc,University of Chicago,2013.
-
RudraPratap, Getting started with MATLAB 7, A quick introduction for scientist and Engineers, first edition, 2006, Oxford University Press.
-
Daowd.M.;Omar,N.;van den Bossche,P.;van Mierlo,J.A review of passive and active battery balancing based on MATLAB/Simulink Int.Rev.Electrical Engineering.2011, 6, 2974-2989.
-
William Bobber, Chi-Tay Tsai, Orean masory; Numerical and analytical method with MATLAB, CRC press publication, 2009.
-
Daowd, M.; Omar, N.; van den Bossche, P.; van Mierlo, J Ain the paper review of passive and active battery balancing based on MATLAB/Simulink.j.int.Rev.electrical Eng.2011,2974- 2989.
-
Xiujuan Zhang, Peide Liu, Darui Wand; The design and implementation of smart battery management system balance technology, Journal of convergence information technology, Volume 6, Number 5. May 2011.
-
Sang chom,Jon Beall,Intelligent Battery management and charging of electric vehicle, Taxas Instruments, Dallas, United states.
-
Technology overview of Li-ion EV.: http://www.nissan- global.com/en.
-
Ajay Deshmukh; Microcontrollers- Theory and applications,
Mc-Graw Hill publication, First edition, 2005
-
Muhammad Ali Mazidi, Rolid.D. Mckinlay, Danney Causey; PIC Microcontroller and embedded systems; Pearson India publication, 2012.
-
John R Peatman; Design with PIC Microcontroller , First edition, person education publication, India, 2002.
-
ParkH.S;Kim,C.H.;Park;K.B.;Moon,G.W.;Lee,J.H.,Design of charge equalizer based on battery modularization, IEEE Trans. On Vehicle technology 2009, 58, 3216-3223.
-
Sizing of Ultra capacitors and battries: http//www.academia.edu/2423391.
-
http://www.mdpi.com/journal/energies; an open access journal; SOC Based Battery Cell Balancing with a Novel Topology and Reduced Component Count.
-
Mehmet Uzunoglu; implementation of a reliable load sharing strategy between battery and ultra-capacitor on a prototype electric vehicle, IEEE transportation electrification conference, 2012
-
Gregory Plett; Battery management system, Equivalent-circuit methods volume II:2(Power engineering), Artech house, London, First edition.
-
Wangbin Zhao, Wangbin Zhao, Jun Huang and Haitaochen; A Novel Space Active Balance System for Lithium-ion Battery
Packs, Shanghai Institute of Space Power-source, Shanghai, china, Journal of Physics conf.Ser.1176 062050, 2019.
-
Anders Sjostand, Development of a Battery Pack Container for an Electrical Vehicle, Department of Product and production Development, Chalmers university of technology,
Gothenburg,Sweden 2015
-
Yevgenbarsukov; jinrong Qian.Battery power management for portable device, Artech house ISBN 13;978-1-60807-491-4
-
I.Aizpuru,U.Iraola, J.M.Canales, M.Echeverria, I.Gil,Passive balancing design for Li-ion battery packs based on single cell experimental tests,IEEE Explore:International conference on clean electrical power (ICCEP).29 August 2013.
-
DorinCadar, DorinPetreus, TomaPatarau, NiculaiePaladhita; Active balancing method for battery cell equalization, Technical University of Cluj-Napoca, Faculty of electronics, telecommunications and information technology, Cluj-Napoca, Romania.
-
Johann Nussrrat, Gael Balondrade; Designing of a test bench battery management, Department of Electrical Engineering Linkoping University SE-581 813 Linkoping, Sweden
-
Song Ci, Dalei Wu; Reconfigurable Battery Techniques and systems: A Survey, University of Nebraska-Lincoln, Lincoln,
NE 68588, USA, IEEE access, April 2016
-
MLD-STD-883E, Test Method standard Microcircuits, Department of Defence,U.S.
-
Dr.AlasandroBirolini; Reliability Engineering-Theory and Practice, Fourth Edition, Springer Publication, Tuscany, Italy.
-
MIL-HDBK-217F (notice), Military handbook: reliability prediction of electronic equipment, Department of Defense, U.S.
-
Milton Ohring,Lucian kasprazak; Reliability and failure of electronic materials and devices, second edition, 2011,Elsevier publication.
-
MIL-STD-704A, Military Standard: electric power, aircraft, Characteristics, and utilization.
-
MIL-STD-1275A (notice 2), Military standard: Characteristics of 28-volt de electrical systems in military vehicles.
AUTHOR PROFILE
P. Prakash received M.E. in Electronics & communication engineering from Birla Institute of technology and science (BITS), Mesra, Ranchi, Jharkhand, India in 2008 with distinction and Master of Business Management (MBA)with specialization in Financial Management. I have authored more
than 8 papers in international conferences and Journals inthe area of Power electronics. I am a Life member of IE(I). Presently I am working in Systems engineering group at URSC, ISRO and responsible for realisation of Power electronics hardware for Indian space programmes.
Dr. J.K. Kishore did his B. Tech in Electrical Engineering at IIT Madras and M. Tech in Electronics at IIT Bombay before joining ISRO Satellite Centre in Jan 1990. He has also completed his Ph. D in applying Genetic Programming for Pattern Classification & Remote Sensing applications at Dept. of Aerospace in IISc in 2001. He was associated with
delivery of Avionics systems for both INSAT and IRS spacecraft. He was responsible for setting up the Avionics Production and Sub-system assembly line frameworks with
vendor support. He is also guiding Ph. D / PG students in the various dimensions of Satellite Programme and its applications. He is also the recipient of Team Award for success of Cartosat-2 from Chairman ISRO / President of India in June 2007. He is also a member of ISRS and fellow of IETE. Presently he is working in the Advanced Technology Development Group interfacing with Academia for research programmes to develop Space products and Services at Academia. Dr. J.K. Kishore has 60+ publications in National/International Journals and Conferences.
C.S. Madhusudhana has completed his Graduation in Instrumentation Engineering from Bangalore university,Post-Graduation in Electronics Design and Technology from CEDT, I.I.Sc and Master of Business Management (MBA)with specialization in Financial Management. He has authored more
than 15 papers in national and international conferences and journals, and a transaction paper is under consideration. He has a patent in Spacecraft Power Control and Management, and few more under processing. His area of interest includes 1) Micro Processor 2) Power Electronics 3) Analog Circuit and System 4) EMI and Noise Control 5) Mission Management.