
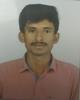
- Open Access
- Authors : P. Prashanth Reddy , A. Siva Naga Raju
- Paper ID : IJERTV10IS120068
- Volume & Issue : Volume 10, Issue 12 (December 2021)
- Published (First Online): 18-12-2021
- ISSN (Online) : 2278-0181
- Publisher Name : IJERT
- License:
This work is licensed under a Creative Commons Attribution 4.0 International License
Soil Stabilization of Base Layer by using Cement and Additive
P. Prashanth Reddy
PG student (Highway Engineering),
SVR Engineering College, Civil Department, Nandalal, Kurnool (Dist), A.P
Mr. A. Siva Naga Raju
Assistant Professor, SVR Engineering College, Civil Department, Nandalal, Kurnool (Dist.), A. P SVR Engineering College, Civil Department, Nandyala, Kurnool (Dist.) A.P.
Abstract–Pavements are major assets of highway infrastructure. Maintenance and rehabilitation of these pavements to the desired level of serviceability is one of the challenging problems faced by pavement engineers and administration in the highway sector. Nowadays, it is observed that flexible pavements deteriorate faster than their design period due to poor material characteristics, poor mix design characteristics, and poor construction design apart from traffic loading and environmental factors, etc. Typical Native soil was collected in the present study investigation. The basic engineering properties of the soil were determined in the laboratory. The optimal dosage of cement and the stabilizer was determined based on laboratory studies. The strength properties of stabilized soils were determined at optimum dosage. Using the results, alternative pavements were designed according to IRC guidelines and validated using IIT Pave software. The critical strains were found to decrease with stabilized subgrade as compared to natural soil as the subgrade. A cost comparison analysis is carried out to assess the financial benefit of using the additive.
Keywords—Native Soil, Cement, Additive, Unconfined compressive strength (UCS), IS 2720, IRC 37:2018, IRC 89 Part I & II, IITPAVE Software, Cost analysis, and MoRTH Specifications etc.
INTRODUCTION
Roads are the dominant mode of transportation in India today. But several problems are faced in the maintenance of roads, as they prematurely fail. The failures observed are rutting and cracking. Rutting occurs due to inadequate compaction of pavement materials, wrong choice of pavement materials as well as due to poor bituminous mixes. However, large wavelength rutting, which is caused due to poor subgrade and inadequate compaction of the lower layers is reported to be the cause of most of the failures of highway pavements. The pavement structure consists of wearing surface, binder, base and sub-base courses, and prepared subgrade layer. The service life and performance of the pavements depend to a considerable extent on the quality of the materials used in the construction. A long-lasting, economical, flexible pavement requires a subgrade layer with good engineering properties. The subgrade should possess adequate strength and drainage conditions to extend the service life of the roadway section and to reduce the required thickness of the flexible pavement structure. In the past, naturally available materials
like soil, stone aggregates, sand, etc., and some of the processed materials like bitumen and cement have been used for the construction of roads. So, the demand for excellent quality naturally occurring materials increased. But the aggregate sources are depleting fast, and its extraction is difficult due to mining restrictions in many of the states of the country due to environmental protection regulations which result in higher procurement and processing cost of such materials.
-
EXISTING WORK
The objective of the present study is to investigate the additive for stabilization of locally available soil and study the effectiveness in terms of improved performance of highway pavement and quantify the benefits of reduced virgin aggregate consumption.
-
Evaluation of the strength characteristics of soils by conducting UCS tests. Short-Time Fourier analysis
-
Pavement design using IRC 37-2018 and analysis IITPAVE software.
-
Assessment of economic and social benefits on the usage of Stabilization additive over the traditional material
-
-
PROPOSED METHODOLOGY
Soil stabilization is a process by which a soils physical property is transformed to provide long-term permanent strength gains. Stabilization is accomplished by increasing the shear strength and the overall bearing capacity of the soil. Once stabilized, a solid monolith is formed that decreases the permeability, which in turn reduces the shrink/swell potential and harmful effects of freeze/thaw cycles. The shrink/swell potential of soil is the amount that soil can change in volume depending on the moisture content. Some expansive soils can expand as much as ten percent! This drastic volume change can easily produce enough force to cause serious damage to a home, building, or roadway. Soil stabilization can improve in-situ, or natural state, soils eliminating the need for expensive remove-and- replace operations. Often soils that provide the structural base for roads, building pads, or parking lots are chemically treated to control engineering properties of a soil, such as moisture content. Soil stabilization is accomplished by using lime, lime-based products, or other chemicals such as
Portland cement. These chemicals rely on pozzolanic reactions to form permanent bonds between soil particles. Pre-project testing is essential to be sure that enough material is present to permanently stabilize the soil.
If the stabilized soil layer is incorporated into the structural design of the pavement, the subsequent layers will be thinner resulting in suitable cost savings. Lime Stabilized soils over-perform non-stabilized soils when, materials, design, and construction are properly considered.
The methodology followed is as follows
-
Determine the physical properties of soil.
-
Examine the compaction characteristics of native soils mixed with additive and cement evaluate the resistance characteristics of mixed materials.
-
Design the pavement using cement and additive in the base layer.
-
Carry out cost analysis and asses, the benefits achieved by using the stabilization over the conventional pavement construction.
-
-
EXPERIMENTAL ANALYSIS
Laboratory testing was conducted to characterize the soils. The testing program was conducted at the Laboratory. Laboratory testing included determination of physical properties, unconfined compressive strength and CBR tested as per IS & IRC code provisions.
The varied materials used for the research study are Native soil, ordinary Portland cement, additive. The additive is a mineral-based powder that is having rich in silicates.
Figure 1: Native Soil
Figure 2:Cement
Figure 3: Additive
Physical Properties of Native Soil
Table 1: Physical Properties of native soil
Description of Test
Native Soil
Atterberg's Limits
LL (%)
28.0
PL (%)
21.5
PI (%)
7.5
Grain Size Analysis
Gravel (%)
39.2
Sand (%)
35.6
Silt & Clay (%)
25.2
Modified Proctor Compaction Test
OMC (%)
9.5
MDD (g/cc)
1.98
California Bearing Ratio Test
CBR (%)
8.7
MDD & OMC for Stabilization of Native soil withcement.
The Native soil is considered for stabilization with OPC-43 grade cement 3.0 %, 4.0 %, 5.0 % & 6.0 % was added to the dried soil and thoroughly mixed to attain uniformity. Then, water was added at different percentages and compacted using modified proctor compaction according to the IS 2720 (part 8).
Figure 4: Soil-Cement Compaction Curves
The MDD and OMC of the soil-cement mix were increased slightly as compacted to the native soils, which is due to the density of cement is more as compared to the soil and
adding extra cement required extra water, keeping with this the optimum dosage of cement content was considered as
-
%. The change in compaction curves is shown in figure 4.
Optimum Dosage of Additive in Stabilization.
The optimum dosage of additive content in the mixtures was determined using a trial test by mixing an added component with different concentrations of 2%, 4% & 6 % of the soil- cement sample. The Optimum dosage of the additive was obtained at 4 %. The maximum dry density and optimum water content and compaction curves of the different dosages are presented shown in Figure 5.
Figure 5:Optimum dosage of additive percentage
Unconfined compressive strength of stabilized Soil
To find the Unconfined compressive strength of the stabilized soils, cylindrical samples of 100 mm DIA 200 mm height were prepared and tested as per IRC SP:89-2010. The strength of the mix was determined by varying percentages of cement and optimum dosage of additive (4 % by weight of cement). All the stabilized soil specimens are cured under moist conditions covered with wet gunny bags for 7-days and 28 days and tested to determine the UCS.
Figure 6: Specimens are curing in progress
The UCS results of the stabilized soil samples obtained from the test were multiplied with the equivalent strength of 1.25 as per Table 12 of IRC SP 89-2010 to calculate the approximate equivalent strength of the cube of 15 cm x 15 cm x15 cm. With the increase in the percentage of stabilizers, the UCS values are also increased. The UCS value of samples contained with cement & Additive satisfies
the IRC specified range for UCS (i.e., 4.5 to 7.0 Mpa in 7/28 days curing period). The results are presented in Table 2.
Figure 7: UCS Specimens are test in progress
Table 2: UCS Specimens results (7 days & 28 days)
S.No
Blend Proportions
Unconfined Compressive strength (MPa)
7-Days
28-Days
1
Soil + Cement (3.0 %)
1.65
1.73
2
Soil + Cement (4.0 %)
2.04
2.17
3
Soil + Cement (5.0 %)
2.15
2.33
4
Soil + Cement (6.0 %)
2.43
2.98
5
Soil + Cement (3.0 %) + Additive (4.0%)
2.49
2.79
6
Soil + Cement (4.0 %) +Additive (4.0%)
3.15
3.90
7
Soil + Cement (5.0 %) + Additive (4.0%)
3.50
4.52
8
Soil + Cement (6.0 %) + Additive (4.0%)
3.60
5.04
Figure 8: Variation in UCS results at 7 days curing period.
Figure 9:Variation in UCS results at 28 days curing period.
PAVEMENT DESIGN AND ANALYSIS
For this study, two alternatives are considered. They are Conventional Design & Stabilized base design treated (5.0
% cement + 4% additive by weight of cement). The different alternate combinations of layers are designed as given in IRC-37 2018. The subgrade CBR=8%. These were designed for the same traffic loads and service life. The design, traffic is taken as 50 msa for 20 years.
-
Pavement Design Life
-
Design Traffic
-
Effective CBR of subgrade
-
Pavement Materials and their properties
Design Options
Option 1: Conventional Pavement design as per IRC 37 2018, which comprises the following Pavement layers.
-
Bituminous layers- Bituminous Concrete (BC) & Dense Bituminous Macadam (DBM)
-
Base Layer Wet Mix Macadam (WMM)
-
Granular Subbase Granular Subbase (GSB) Option 2: As the recent MoRTH circular (dated 14th December 2020) encourages the use of New/alternative materials and technology in the construction of roads, the alternate pavement design option with Stabilization technology has been considered as per IRC SP 89 2018, which comprises the following pavement layers.
-
Bituminous layers – BC with VG-40
-
SAMI Interface with Geosynthetic Paving Fabric
-
Stabilized base layer with Cement & additive.
-
Subgrade & Pavement Material Properties
Resilient Modulus: – For Bituminous layer -BC & DBM: 3000 MPa with VG-40 (Table 9.2 of IRC 37:2018,
considered for Average Annual pavement temperature of 350 C)
Stabilized Base Layer: 900 MPa (IRC SP (Part -II) 2018) The Empirical formula is given in the IRC SP 89 (Part-II) – 2018, Clause 4.2, page 7, E=1000*UCS was applied. The minimum UCS will be 4.5. 1000*4.5 = 4500 Mpa. For Design purpose 20% E value may be considered, thus the result received is E = 20%*4500 = 900 MPa.
Granular Layers:
MRGRAN=0.2 ()^0.45 *MRSUPPORT
Granular Layers: 0.2*(400) ^0. 45 * 66.60 = 197.45 Mpa (Option1)
Subgrade layer: 66.60 MPa (Eq.6.2, page No.19 of IRC 37:2018, =17.6*(8) ^0. 64 = 66.60)
Poissons Ratio ():
Poisson's Ratio of stabilized Base: 0.25
Poisson's Ratio of BC layers, Granular subbase, and Subgrade: 0.35
Contact Stress:
The IRC 37 -2018. Table 3.1 has specified Tire Contact Stress of 0.56 MPa for tensile strain in Bituminous Layer/ compressive strain for Subgrade and 0.80 Mpa for Stabilized base Layer.
Performance Models
As per IRC: 37 – 2018, fatigue life in a number of standard axles is given below.
-
Fatigue Model
Nf = 0.5161 x C x 10-04 x [1/t]3.89 x [1/MR]0.854 (90%
reliability)
-
Rutting Model
Nr = 1. 41×10-8× (1/v) 4.5337 (90% reliability)
-
Fatigue cracking in Stabilized Layers
N = RF x [(113000/E 0.804 + 191)/t]12
Design Calculations
Based on the above design inputs, IIT PAVE analysis has been carried out to obtain the pavement crust as per IRC SP 89-2018 and IRC 37: 2018. The results of the IITPAVE program and the summary of proposed pavement crust thickness for option 1 & option 2 are mentioned in Table 3. The schematic diagram is shown in figure 10.
Table 3: Conventional Vs Stabilized Base Pavement crust composition.
Pavement Composition (mm)
Traffic -50 msa & CBR -8 %
Conventional Design
Stabilized Base Design
Bituminous Concrete (BC) VG-40
50 mm
40 mm
Dense Bituminous Macadam (DBM) VG-40
110 mm
60 mm
Wet Mix Macadam (WMM)
250 mm
–
Stabilized Base (SB)
–
280 mm
Granular Subbase (GSB)
150 mm
–
Figure 10: Schematic diagrams of Conventional pavement Vs Stabilized Base Pavement
-
-
SUMMARY
- li>
Laboratory experiments were conducted on the native soil taken and found that soil has less plasticity index and is classified as low compressible silt (ML).
-
Then the further investigation was conducted on native soil to determine the compaction properties (OMC, MDD) by modified proctor compaction test, strength properties by Unconfined compressive strength, and CBR.
-
Stabilized mix proportions of Native Soil (ML) with cement & Additive at different dosages are tested by modified proctor compaction test. Based on OMC & MDD
the dosage of 5% cement and 4 % Additive by weight of cement was found to be optimum as per strength and durability requirement suggested by IRC-37 for stabilized soils.
-
As the strength of the stabilized soils increases with curing time, the UCS is carried out at different periods 7& 28 days and tabulated for comparison.
-
Pavement thickness for conventional pavement is found to be 560 mm, and stabilized is 380 mm
-
The aggregate consumption for stabilized layer pavement is five times lesser than conventional pavement.
CONCLUSIONS
-
Can use a range of local soils with minimum to NIL requirement of outsourcing aggregate.
-
Higher Unconfined Compressive strength, durability, and reduced permeability.
-
Reduces pavement thickness requirements.
-
Reduce construction costs, enhancement of pavement life with minimal maintenance costs.
-
Stabilized base can accept lower CBR and hence subbase compaction is seldom required.
-
Reduce CO2 emissions & Carbon Footprints during construction and maintenance of road projects.
ACKNOWLEDGMENTS
The authors would like to thank Vishwa Samudra engineering Pvt Ltd, Hyderabad, India for providing the StabilRoad® Additive used in the present study.
I am thankful to my technical supporters Mr. T Pavanram,
-
Tech (IIT Roorkee) and M. Nagendra Babu Reddy, M. Tech (IIT Bombay), [Ph.D. (IIT Hyderabad)] for support and encouragement in this project.
REFERENCES
-
IRC-37:2018 Guidelines for the Design of Flexible Pavements.
-
IRC: SP: 89 (Part-II):2018 Guidelines for the Design of Stabilized Pavements.
-
IRC: SP: 72:2015 Guidelines for the Design of Flexible Pavements for Low Volume Rural Roads.
-
IS 2720: Part 10: 1991 (2 Revision) Methods of test for soils: Part
10 determination of unconfined compressive strength (Second Revision)
-
IS 2720 (Part 4)-1985: Indian Standard code of practice for Method of test for soils Grain size analysis.
-
IS 2720 (Part 40)-1977: Indian Standard code of practice for Method of test for soils Determination of Free Swell Index of Soils.
-
IS 2720 (Part 5)-1985: Indian Standard code of practice for Method of test for soils Determination of liquid and plastic limit.
-
IRC:9-1972 Traffic Census on Non-Urban Roads (First Revision
-
IRC:10-1961 Recommended Practice for Borrow pits for Road Embankments Constructed by Manual Operation
-
IRC:16-2008 Standard Specifications and Code of Practice for Prime and Tack Coat (Second Revision)
-
IRC:17-1965 Tentative Specification for Single Coat Bituminous Surface Dressing (Amalgamated with IRC:110-2005)
-
IRC:19-2005 Standard Specification and Code of Practice for Water Bound Macadam (Third Revision)
-
IRC:115-2014. Guidelines. For. Structural Evaluation. And. Strengthening of Flexible. Road Pavements Using. Falling Weight Deflectometer (FWD).
-
ASTM E2583 – 07(2020) Standard Test Method for Measuring Deflections with a Light Weight Deflectometer (LWD).
-
IRC:81-1997. Guidelines. For. Strengthening Of Flexible. Road Pavements Using. Benkelman Beam Deflection. Technique.
-
AASHTO T 307 Standard Method of Test for Determining the Resilient Modulus of Soils and Aggregate Materials
-
Theyse, H. L., De Beer, M., & Rust, F. C. (1996). Overview of South African Mechanistic Pavement Design Method. Transportation Research Record, 1539(1), 6 17. https://doi.org/10.1177/0361198196153900102
-
International Journal of Earth Sciences and Engineering ISSN 0974-5904, Vol. 06, No. 01, February 2013, pp. 194-203
-
Spencer, W. Base Stabilization. Proc. Kentucky Highway Conf., Feb. 1962, Univ. of Kentucky College of Engineering, Bull. 64, 1962, pp. 61-73.
-