
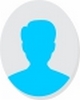
- Open Access
- Authors : Samoil Samak, Svetlana Risteska, Vladimir Dukovski, Sase Trajkoski
- Paper ID : IJERTV9IS090509
- Volume & Issue : Volume 09, Issue 09 (September 2020)
- Published (First Online): 12-10-2020
- ISSN (Online) : 2278-0181
- Publisher Name : IJERT
- License:
This work is licensed under a Creative Commons Attribution 4.0 International License
Some Experimental Investigation of Products from Thermoplastic Composite Materials Manufactured with Robot and LAFP
Samoil Samak, M.Sc1, Svetlana Risteska, Ph. D2, Vladimir Dukovski, Ph.D3, Sase Trajkoski, Postgraduate student1 1Mikrosam D.O.O Krusevski pat bb -Prilep R. N. Macedonia
2Institute of Advanced Composites and Robotics-Prilep, R. N. Macedonia
3Faculty of Mechanical Engineering Ss. Cyril and Methodius University Skopje, R. N. Macedonia
Abstract:- For successful avoiding of the irregularities and errors in the products from composite materials, it is important to manage the whole production process in real time. This applies to detecting certain irregularities (positioning defects, bonding defects), controlling the robot and process parameters.
This paper presents results from an experimental study of the influence of embedded defects created during in – situ laser automated fiber tape placement (LAFP), on the mechanical properties of carbon/PEEK composites. Three rings have been examined with different designs [(0/±45)n], [(0/±30)n] and [(0/±90)n], in which gaps and overlaps have been introduced during fiber placement. The microstructures were characterized by optic microscopy. ILSS tests were performed on samples from rings and showed that the presence of a gap/overlap and voids more than 3% affect mechanical behavior of pipes but does not affect degree of crystallinity.
Keywords: LAFP; defects; process parametrs, ILSS, void
-
INTRUDUCTION
Composite material is a combination of two or more materials which results with improved properties in comparison to the properties of individual application of the same materials. Recently, the thermoplastic matrix composites are nding new applications in different industrial area due to their intrinsic advantages related to environmental compatibility and process-ability [1-4].
he quality of the final composite thermoplastic part depends mostly on machine (robot) accuracy, the geometry of the object where the laying is performed and process parameters.
Robot accuracy research has long been a focal point not only for scientific institutions, but even more so for companies that make robots and those that use them. Samak et al. [5] described the influence of the calibration of the robot on the accuracy of ATL/AFP process. Hallander et al. [6] evaluated the effect of the layup sequence, ply thickness and ply pre- compaction on the wrinkle occurrence when forming a quasi- isotropic laminate made of unidirectional layers. For a double curved geometry, their results showed that the layup sequence had a dominant effect compared to other parameters. Haanappel et al. [7,8] have shown clear differences in terms of ply wrinkling, between a unidirectional CF/PEEK and a carbon/polyphenylene-sulde (CF/PPS) using a carbon fabric for the molding of complex part geometry. They observed that
the UD material had more difculties in conforming to 3D geometries, and they highlighted the fact that both types of composite cannot be deemed similar when considering the processing cycle. The challenge of automated ber placement is to completely lay down the laminate with a dened ber orientation without gaps or overlaps. Successful ber placement without gaps or overlaps is dependent on many parameters, such as mold geometry, tape width, and ber orientation. Study [9] has shown that the effect of overlaps can reduce in-plane shear strength (ILSS) by up to 13%. Overlapping is more important than the problem of gaps.
The void content of in-situ consolidated TPC parts depends on process parameters (the layup speed of fiber, temperature, part geometry and prepreg quality). Another key concern in- situ consolidated TPC part is crystallinity (the ordered molecular structure that forms in semi-crystalline polymers, such as PEEK, PEKK and PPS, as they cool from melt temperature to a solid). In general, slower cooling rates increase crystallinity, which results in higher mechanical properties and chemical resistance in the finished laminate [10-24]. Chen and Chung [10] studied the crystallization kinetics of CF/PEEK composites at 61% ber volume content, for both the isothermal and the non-isothermal crystallization approaches. They showed that a higher cooling rate causes the crystallization to start at a lower temperature and is obtained over a wider temperature range.
Many authors [20-35] today work to improve the in – situ laser assisted AFP process. Some work [25] on intimate contact and heat transfer, some work [26-30] on fixing and removing defects that occur in the whole process and some work [30-35] on technological processes that require the appropriate technological parameters to improve product quality.
The present paper reports on studies for possible defects and process parameters during robotized LAFP process. One of the primary objectives of this phase of the study is to identify the dominant processing parameters and establish their influence on the quality of final composite materials.
-
LAFP PROCESS
The laser-assisted tape/fiber placement (LATP/LAFP) process is an automated composite manufacturing technique often quoted for its potential ability to produce composite parts with an in-situ consolidation, which avoids an expensive time and energy consuming step of post- consolidation. But, in order to be competitive this process
needs to ensure a certain level of quality of the fabricated parts. There are 3 key reasons for the occurrence of irregularities in the final product from composite material:
-
machine accuracy,
-
the geometry of the object where the laying is performed and
-
process parameters.
Thus, this paper focuses on the positioning defects and bonding defects (second reasons). The rest of this paper is organized as follows. In Section B are described the positioning and bonding defects during the LAFP process, mainly gaps and overlaps. Section C focuses on the modeling method of void defects for the thermoplastic composites made by the LAFP process from gap/overlap or process parameters.
-
Machine accuracy
Tool possiton – how precisely the roller of LAFP/LATL head follows the laying and orientation path; deviation from the predicted orientation of the head can cause separaton of the material from the background where the laying is performed (the robot accuracy). Each from them directly affects the quality of the final products. This section is not the subject of study in this paper.
-
The geometry of the object where the laying is performed
The most common irregularities (possible defects) that occur in the process of laying during LAFP process are shown in Table I
Gap between courses is inadmissible magnitude of the distance between two adjacent courses. Gap between tows is inadmissible magnitude of the distance between two adjacent tows. Overlap is a defect in which two adjacent tows overlap. Missing tow is an empty space where in the reference state there should be a tow. Early add / late cut is early applying of tow at the beggining of a course or delayed cutting of a tow at the end of a course. Late add / early cut is late applying of tow at the beggining of a course or early cutting of a tow at the end of a course.
TABLE I. DEFECTS DURING LAFP PROCESS
Lay-up uniformity features
Placement features
Topical features
Gaps
Start and end placement position
Splices
Overlaps
Ply edge angulaity Ply orientation
Wrinkles, twists, folds
Missing tows
Curvature of the center line of a tow
Bridging, crowning
Splitting of a tow
Foreign Object Detection (FOD)
Splitting of a tow is a defect that occurs when a tow is ripped and it is laid up with a width smaller than the reference width. In figures 1-5 shows some of the possible errors of the laid tapes, of the possible errors of start and end placement position and possible defects during LAFP process
Fig. 1. Laminate missing tow / gaps and overlaps
-
Boundary and ply tolerance, late add of a tow
-
Splitting of a tow
Fig. 2. Possible errors of start and end placement position
Splice – a defect that occurs when two tows are joined together, and the sticker is laid up on the composite part
Splice – a defect that occurs when two tows are joined together, and the sticker is laid up on the composite part
Fig. 3. Wrinkle, twist, fold – a defect indicating different forms of deformations of a tow
Fig. 4. Bridging and crowning – defects that occur as a lack of contact between the tow and the surface.
Fig. 5. Fuzzballs – a tangle of fibers dropping on the laid-up part, which accumulate on some parts of the machine during AFP as a result of abrasion of fiber material.
-
-
Process parameters
The mechanical performance of the final parts depends on many factors. Final product from LAFP should be void-free and well consolidated for reliable use in structure. Thermal degradation induced during processing should be minimal in order material to retain its properties. Its crystallinity should be within the recommended range for the material to attain the optimal properties.
Experimental studies were performed with constants process parameters laser temperature, temperature of tool, compaction force, the angles of laying, the angles of laser beam, dimension of compaction roller, mechanisms for cutting tapes and layup speed. In this paper the impact of the technological parameters of the final product, is not studied. The technological parameters for experiments are taken from trial tests and the experience with LAFP technology.
-
-
EXPERIMENTAL INVESTIGITION
-
Materials and equipement
This study investigated the thermoplastic prepregs: UD pre-preg material Suprem T with Carbon-fibre (AS4 carbon fibre) and matrix PEEK (Vitrex 150 PEEK) supplied by Suprem (Switzerland). Specimens were manufacture with thickness 0.14 mm of TPC prepreg.
The laminates were obtained by using a laser-assisted fiber placement head (LAFP), produced by Mikrosam, RN Macedonia. Head is attached to a robot arm (Kuka), as it is shown in Fig. 1. The tape head consists of: (1) a consolidation roller (outer diameter of 60 mm); (2) a tape feed, guidance, tensioning, and cutting system for UD tape; (3) an optic lens connected via a fibre-optic cable to a remotely-located 3 kW diode-laser heat source; and a temperature sensor (pyrometer). On the way to the consolidation roller, the tape is heated up to polymer melt temperature using a laser. The tape is then placed on the tool and consolidated with a temperature- controlled roller (about 190C).
Fig. 6. In situ consolidation with LAFP head (Mikrosam D.O.O.).
As a mandrel for the ring specimens a specific cylindrical mandrel was used. The diameter of the mandrel is 400mm, and the length is 500mm.
-
Mechanical analysis
Short beam strength tests were performed for inter-laminar bond strength characterization. In this study, the ASTM D2344 standard was followed.
Samples were prepared using flats from the center where the process had reached steady state. The samples were cut carefully using precision diamond saw. The nished dimensions of the samples were within the tight tolerances of size according standard ASTM D2344. SBS tests were performed with an Universal testing machine. Load was applied with a rate of 1 mm/min. UTM and sample with used test fixture are given in figure 7.
Fig. 7. UTM (universal test machine) and ILSS test (samples No.1 mounted on two supports)
Interlaminar shear strength M, expressed in megapascals was calculated as per the standard (Eq.1)
M = 0.75 (FM / (b x h)).(1)
Where FM is the maximum force observed during the test in newtons, b and h are the measured specimen width and thickness in millimetres respectively.
-
Optical microscope
The void content of composite product is very important parametar that characterizes the quality of the produced composite part. The samples was extracted from each rings. Ten images capture and analysis were performed and they were evaluated for the void content for each of the laminates (rings) manufactured by LAFP process. Seperation of the bres, resin and voids were performed on selected regions using image analysis software Image J (NIH).
-
DSC
A commonly used method for measuring crystallinity in polymeric materials called Differential Scanning Calorimeter (DSC) is used in this study to validate model predictions with experimental results.
The degree of crystallinity of CF/PEEK laminates was measured by a differential scanning calorimetry (DSC) technique according to ISO 11357-3 [37]. DSC tests were conducted by means of calibrated DSC Instrument equipment from METTLER TOLEDO. The weights of samples extracted from each laminate were in the range of 715 mg. Dynamic tests were performed with a heating rate of 10 °C/min from room temperature up to 400 °C. A cooling rate of 10 °C/min was then performed. For the calculation of the degree of crystallinity Xc, the expression (2) was used:
(2)
where Hm is the enthalpy of fusion at melting point, Hc is the enthalpy of cold crystallization, which is observed in some cases, Hf is the enthalpy of the completely crystalline polymer (130 J/g for PEEK). Wf refers to weight fraction of carbon fibre within the laminate. At least four samples were tested from each laminate(ring), and the averaged data was considered to represent the final degree of crystallinity Xc of each laminate (ring).
-
-
RESULTS AND DISSCUSION
-
Manufacture of ring specimens
In these trials was utilized conformable silicone consolidation roller with outer of diameter 60 mm. Consolidation load was applied via pneumatic cylinder, adjusted to provide a 600 N load.
The surface temperature of the tape and substrate in this study were measured for all trials with a thermal camera. Initial experiments were carried out to understand the relationship between process parameters and the quality of the ring obtained in order to optimize the process. Three ring samples were manufactured with different design shown in Figure 8. The process settings are presented in Table II.
Fig 8. The samples with different design (Ring 1, Ring 2 and Ring 3)
Fig 9. The positioning defects during the LAFP process
Constants parameters
Variables process parameters
Lay-up speed
7 m/min
Programmed gap
1.4mm for angles
±30/±45/0°
Laser temperature
430°C
1.6mm for angles
±90°
Compaction force
600N
The design of the specimens
Ring 1 (0/90)n
Lead angle
10°
Ring 2 (0/±30)
Total angle
17°
Ring 3 (0/±45)n
td>
1.4mm for angles
±30/±45/0°
Constants parameters
Variables process parameters
Lay-up speed
7 m/min
Programmed gap
Laser temperature
430°C
1.6mm for angles
±90°
Compaction force
600N
The design of the specimens
Ring 1 (0/90)n
Lead angle
10°
Ring 2 (0/±30)
Total angle
17°
Ring 3 (0/±45)n
TABLE II. PARAMETERS DURING LAFP PROCESS
Constants parameters
Variables process parameters
Lay-up speed
7 m/min
Programmed gap
1.4mm for angles
±30/±45/0°
Laser temperature
430°C
1.6mm for angles
±90°
Compaction force
600N
Ring 1 (0/90)n
Temperature mandrel
22 °C (RT)
-
ILSS
Figure 10 shows a typical force-time diagram at ambient temperature for samples No3(1-5). ILSS of composite rings were determined for five specimens for each ring according to equation (1). The average values for each experiment are shown in Table III.
Fig. 10. Force-time diagram of No.3 sample for LAFP (with 5 repeated)
TABLE III. THE RESULTS FOR ILSS TESTS SHEAR STRENGTH FOR EACH RING
sample
ILSS
sample
ILSS
sample
ILSS
Ring1-1
34.2
Ring2-1
33.1
Ring3-1
53.1
Ring1-2
35.3
Ring2-2
39.9
Ring3-2
46.9
Ring1-3
31.7
Ring2-3
42.4
Ring3-3
51.9
Ring1-4
33.1
Ring2-4
26.3
Ring3-4
46.2
Ring1-5
33.2
Ring2-5
42.3
Ring3-5
42.9
Average
33.5
Average
36.8
Average
48.2
From the results shown in table 3 can be observed that ring specimen No3-1 with ILSS 48.2MPa had the best results. This sample No3 was with 1.4 gap and design (0/±45o) n. In contrary, specimen No1 with gap 1.6mm and angle 90o had shown the worst results, 38% lower value than ILSS from sample No3. The influence of gap/overlap parameters during manufacturing of full section composite parts is reported in [27-30].
If comparison is made between specimens No2 and No3, it can be seen that design has an influence in mechanical properties ILSS of ring specimens.
Considering the LAFP processing parameters were not optimised in the current study and that the tool temperature was only RT (22 0C), ILSS can be improved if the mandrel is heated, with ageing or with smaller layup speed in LAFP [27,36]. The results demonstrate that optimisation of mechanical properties using the LAFP process is an complex problem. Processing parameters must be tuned for each material system and each lay-down speed.
Further work will focus on optimising the LATP process.
-
Optical images and calculate porosity
From the results shown by optical microscopy can be observed that ring specimen No3 had the best results and voids <2%.
X200
Fig. 11. Cross-section optical micrographs of lamina UD prepreg Suprem T 60% AS4 / PEEK-150 0.14 x 150 (void
~1%)
Fig. 12. Cross-section optical micrographs of ring No.3 manufactured in LAFP with in-situ consolidation (voids
~1.6%)
Figure 13. Cross-section optical micrographs of ring No.1 manufactured in LAFP with in-situ consolidation (voids 4%)
Fig. 14. Cross-section optical micrographs of ring No.1 manufactured in LAFP with in-situ consolidation (voids 4%)
-
Degree of crytalinity DOC (%)
Fig. 15. shows the DSC heating traces of the LAFP Ring 3-1. The laminate LAFP Ring 1 shows a cold crystallization peak at 150-173 °C.
Fig. 15. DSC curves from LAFP Ring 3-1, in two steps
In Table IV are presented values of degree of crystallinity (Xc) calculated from DSC diagrams for all examined specimens: Ring1 (1-4), Ring2 (1-4), and Ring3 (1-4).
TABLE IV. THE RESULTS FOR DOC FOR EACH RING
sample |
Xc (%) |
sample |
Xc (%) |
sample |
Xc (%) |
Ring1-1 |
52.47 |
Ring2-1 |
37.71 |
Ring3-1 |
39.62 |
Ring1-2 |
34.32 |
Ring2-2 |
30.74 |
Ring3-2 |
41.74 |
Ring1-3 |
34.92 |
Ring2-3 |
34.90 |
Ring3-3 |
35.17 |
Ring1-4 |
37.44 |
Ring2-4 |
37.55 |
Ring3-4 |
37.94 |
Average |
39.79 |
Average |
35.23 |
Average |
38.62 |
A DSC analysis also conrmed that the Ring1, Ring 2 and Ring 3 laminate reached average crystallinity with a value of Xc =35.23-39.79 %. Crystallinity of 35-36% is good enough, but values below this range can cause significant reduction of mechanical properties [10-24].
V CONCLUSION
The experimental procedure described in the present work is suitable to study the influence of the most common irregularities (defects) that occur in the process of laying during LAFP process, on mechanical characteristics of final product.
From conducted mechanical testing can be concluded that the best results in shear strength were obtained with Ring 3. It is assumed that the lower mechanical properties of Ring 1 samples are caused by voids and gaps in the final composite, because process parameters are constants for all investigated samples in this study.
Void contents are within the allowed void tolerance for thermoplastic manufactured with LAFP; however, in further studies targets will be focused to manufacture composite materials with LAFP method with less voids contents and better consolidated laminates.
DOC (Xc) of all rings laminate reached average crystallinity with a value of Xc =35-39% and below these levels mechanical properties would drop off significantly.
Combining dierent sensors – systems for detection of defect in LAFP process, will become the focus of studying the online detection and controlling defects in the future research.
ACKNOWLEDGMENT
The authors would like to acknowledge the support of the research team from Institute for advanced composites and robotics- Prilep and engineering team from Mikrosam D.O.O. Prilep (N. R. Macedonia).
REFERENCES
-
F.N.Cogswell, Thermoplastic aromatic polymer composites: a study of the structure, processing, and properties of carbon fibre reinforced poly ether ether ketone and related materials. Oxford [England]; Boston: Butterworth-Heinemann, 1992.
-
De Gennes, P. G., Reptation of a Polymer Chain in the Presence of Fixed Obstacles, J. Chem. Phys. 55, 572 (1971)
-
Svetlana Risteska, Samoil Samak, Zlatko Sokoloski and Dimitar Bogdanoski, Integrated production solutions for thermoplastic materials, 6-th International Scientific Conference Space Technologies: Present and Future completed its work on May 26, 2017
-
Svetlana Risteska, Samoil Samak, Zlatko Sokoloski and Dimitar Bogdanoski Solutions for prduction and properties of thermoplastic Composites, The 10th Asian-Australasian Conference on October 16 – 19, 2016, Bexco in Busan, Korea
-
Samoil Samak, Igor Dimovski, Mirjana Trompeska, Vladimir Dukovski, Avoiding heavy computations in inverse calibration procedure for 7
DOFf robot manipulator, Journal of Electrical Engineering and Informatin Technologies, 2016, Vol. 1, No. 12, pp. 3743.
-
Hallander P, Akermo M, Mattei C, Petersson M, Nyman T. An experimental study of mechanisms behind wrinkle development during forming of composite laminates. Compos A Appl Sci Manuf 2013;50:pp.5464.
-
Haanappel SP, Sachs U, Ten Thije RHW, Rietman B, Akkerman R. Forming of thermoplastic composites. Key Eng Mater 2012:5046.
-
Haanappel SP, ten Thije RHW, Sachs U, Rietman B, Akkerman R. Formability analyses of uni-directional and textile reinforced thermoplastics. Compos A Appl Sci Manuf 2014;56:8092.
-
Croft, K.; Lessard, L.; Pasini, D.; Hojjati, M.; Chen, J.; Yousefpour, A. Experimental study of the effect of automated ber placement induced defects on performance of composite laminates. Composites 2011, 42, 484491.
-
Chen M, Chung CT. Crystallinity of isothermally and nonisothermally crystallized poly (ether ether ketone) composites. Polym Compos 1998;19(6):pp. 68997.
-
Di Francesco, M., Giddings, P. F., Scott, M., Goodman, E., Dell'Anno, G.,Potter, K. Influence of laser power density on the mesostructure of thermoplastic composite preforms manufactured by Automated Fibre Placement. In International SAMPE Technical Conference. (Vol. 2016- January). Soc. for the Advancement of Material and Process Engineering.
-
J.E. Spruiell and C. J. Janke, A review of the measurement and development of crystallinity and its relation to properties in neat poly (phenylene sulde) and its ber reinforced composites. Technical report, Oak Ridge National Laboratory, 2004.
-
Andrew Herrod-taylor, The crystallization of poly (aryl ether ether ketone) (peek) and its carbon fibre composites, Master of research in the science and engineering of materials, University of Birmingham February 2011.
-
A.J. Comer, D. Ray, W.O. Obande, D. Jones, J. Lyons, I. Rosca, R.M. O Higgins, M.A. McCarthy, Mechanical characterization of carbon brePEEK manufactured by laser-assisted automated-tape-placement and autoclave, Composites Part A: Applied Science and Manufacturing, 2015, Volume 69, pp. 10-20.
-
Gao SL, Kim JK, Cooling rate inuences in carbon bre/PEEK composites, Part 1. Crystallinity and interface adhesion. Compos A, 2000; 31:51730.
-
Wouter Grouve, Weld strength of laser-assisted tape-placed thermoplastic composites, Grouve, Wouter Johannes Bernardus PhD Thesis, University of Twente, Enschede, the Netherlands, August 2012
-
Xiao Cai, Determination of Process Parameters for the Manufacturing of Thermoplastic Composite Cones Using Automated Fiber Placement, Master of Applied Science (Mechanical Engineering) at Concordia University Montreal, Quebec, Canada June 2012.
-
MSC. Muhammad Amir Khan, Experimental and simulative description of the thermoplastic tape placement process with online consolidation, Doctor tessis, Institut für Verbundwerkstoffe GmbH, Kaiserslautern 2010
-
Mehran Eimanlou, Investigation of the effect of process parameters on bond strength of thermoplastic composite rings manufactured using fiber laser, Master of Applied Science (Mechanical Engineering) at Concordia University Montréal, Québec, Canada February 2018
-
Samoil Samak, Zlatko Sokoloski, Svetlana Risteska, Dimitar Bogdanoski, Improving the final properties of thermoplastic composites manufactured with laser automated tape placement (LATP) The 13th SAMPE CHINA Conference & Exhibition May 16-18, 2018, Shanghai,
P. R. China.
-
Danning Zhang, Void consolidation of thermoplastic composites via non- autoclave processing, A dissertation submitted to the Faculty of the University of DelawareSummer 2017
-
B. S. Hayes and L.M., Gammon Optical Microscopy of Fiber- Reinforced Composites – Chapter 1 Introduction Composite Materials and Optical Microscopy, Copyright © 2010, ASM International, www.asminternational.org
-
Muhammad Amir Khan, Peter Mitschang and Ralf Schledjewski, Parametric study on processing parameters and resulting part quality through thermoplastic tape placement; Journal of Composite Materials 2012, Vol. 47(4) pp. 485499.
DOI: 10.1177/0021998312441810
-
Muhammad Amir Khan, Peter Mitschang and Ralf Schledjewski,Parametric study on processing parameters and resulting part quality through thermoplastic tape placement process, 2012,
Journal of Composite Materials Vol 47(4) pp 485499, DOI: 10.1177/0021998312441810
-
Arthur Levy, Dirk Heider, John Tierney and John W Gillespie, Inter- layer thermal contact resistance evolution with the degree of intimate contact in the processing of thermoplastic composite laminates, Journal of Composite Materials 2014, Vol. 48(4) 491503 The Author(s) 2013 Reprints and permissions: sagepub.co.uk/journals Permissions. nav DOI: 10.1177/0021998313476318 jcm.sagepub.com
-
Belnoue, J.P., Mesogitis, T., Nixon-Pearson, O.J., Kratz, J., Ivanov, D.S., Partridge, I.K., Potter, K.D., Hallett, S.R., Understanding and predicting defect formation in automated fibre placement pre-preg laminates, Composites: Part A (2017),
doi: http://dx.doi.org/10.1016/j.compositesa.2017.08.008
-
Mohammad Rakhshbahar, Michael Sinapius, A Novel Approach: Combination of Automated Fiber Placement (AFP) and Additive Layer Manufacturing (ALM), J. Compos. Sci. 2018, 2, 42; doi:10.3390/jcs2030042
-
Shouzheng Sun, Zhenyu Han, Hongya Fu, Hongyu Jin, Jaspreet Singh Dhupia and Yang Wang, Defect Characteristics and Online Detection Techniques During Manufacturing of FRPs Using Automated Fiber Placement: A Review, MDPI, Journal Polymers June 2020, 12, 1337; doi:10.3390/polym12061337
-
Xiangqian Li*, Stephen R. Hallett and Michael R. Wisnom, Modelling the effect of gaps and overlaps in automated fibre placement (AFP)- manufactured laminates, Sci Eng Compos Mater 2015; 22(2): 115129
-
Lan Marine , Cartié Denis , Davies Peter , Baley Christophe , Influence of embedded gap and overlap fiber placement defects on the microstructure and shear and compression properties of carbon-epoxy laminates, Composites Part A: Applied Science and Manufacturing March 2016, Volume 82, pp198-207
-
Minh Duc Hoang, Procedure for making flat thermoplastic composite plates by Automated Fiber Placement and their mechanical properties, A Thesis, Montreal, Quebec, Canada, April 2015
-
Thomas Weiler , Thermal Skin Effect in Laser-Assisted Tape Placement of Thermoplastic Composites, Thesis · January 2020 DOI: 10.18154/RWTH-2019-06638
-
Tjitse K. Slange, Rapid manufacturing of tailored thermoplastic composites by Automated lay-up and stamp forming, PhD Thesis, University of Twente, Enschede, the Netherlands March 2019 DOI 10.3990/1.9789036547284
-
Marta Perez, Anais Barasinski, Benoit Courtemanche, Chady Ghnatios and Francisco Chinesta, Sensitivity thermal analysis in the laser-assisted tape placement process, AIMS Materials Science, 05 November 2018,Vol. 5(6): 10531072. DOI: 10.3934 / matersci.2018.6.1053
-
Hugues Lessard, Gilbert Lebrun, Abdelhaq Benkaddour, Xuan-Tan Pham, Inuence of process parameters on the thermostamping of a [0/90] 12 carbon/polyether ether ketone laminate, Composites: Part A 70 (2015) 5968, http://dx.doi.org/10.1016/j.compositesa.2014.12.009
-
Khan MA, Mitschang P, Schledjewski R. Identication of some optimal parameters to achieve higher laminate quality through tape placement process. Adv Polym Technol 2010;29(2):98111.
-
ISO 11357-3: 2018(E), Plastics Differential scanning calorimetry (DSC), Part 3: Determintion of temperature and enthalpy of melting and crystallization; 2018. https://convert.town/image-dpi