
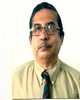
- Open Access
- Authors : A. K. Bandyopadhyay , S. K. Mazumder
- Paper ID : IJERTV10IS010191
- Volume & Issue : Volume 10, Issue 01 (January 2021)
- Published (First Online): 29-01-2021
- ISSN (Online) : 2278-0181
- Publisher Name : IJERT
- License:
This work is licensed under a Creative Commons Attribution 4.0 International License
Stability of Flexibly Supported Finite Oil Journal Bearing Considering Fluid Inertia Effect and Influence of Pressure Dependent Variable Viscosity
-
K. Bandyopadhyay1
Assistant Professor, Department of Mechanical Engineering,
DR. B.C Roy Engineering College, Durgapur, West Bengal, India
S. K. Mazumder2
Professor,
Department of Mechanical Engineering, DR. B.C Roy Engineering College, Durgapur,
West Bengal, India
Abstract- The aim of this study is to analyse the Nonlinear transient stability of finite oil journal bearing including the effect of fluid inertia and pressure dependent viscosity. The theoretical analysis is intended to show the effect of fluid inertia with pressure dependent variable viscosity on the journal bearing performance for three-dimensional bearing geometries. The average Reynolds equation is modified to include the fluid inertia effect and variable viscosity effect and is used to obtain pressure field in the fluid-film. The solutions of modified average Reynolds equations are obtained using finite difference method and appropriate iterative schemes. This investigation deals with the stability of flexibly supported finite oil journal bearing with fluid film inertia effect and pressure dependent viscosity. An attempt has been made to evaluate the critical mass parameter. A Nonlinear time transient method is used to simulate the journal centre trajectory to estimate the stability parameter, which is a function of speed.
In the present work, the modified average Reynolds equation considering the effect of fluid inertia along with the effect of pressure dependent variable viscosity is solved by finite difference method with successive over-relaxation scheme (Gauss-Siedel), while the equation of motion of both journal an bearing are solved by the fourth order Runge – Kutta method. It was observed that the stability increases with the increase in eccentricity ratio, viscosity parameter and modified Reynolds number and also increases with the increase of slenderness ratio.
Keyword: Modified Reynolds number, viscosity parameter, stability, critical mass parameter, fluid film inertia.
-
INTRODUCTION
The basic assumptions in the classical hydrodynamic theory include negligible fluid inertia forces in comparison to the viscous forces. Pinkus and Sterlincht [1], have shown that the fluid inertia effect cannot be neglected when the viscous and the inertia forces are of the same order of magnitude. In recent times synthetic lubricants, low viscosity lubricants, are used in industries and owing to high velocity it is possible to arrive at such a situation where flow is laminar but the fluid inertia effect cannot be neglected, the classical Reynolds equation is not valid in such case.
Keeping in view of the above, consideration of inertia effect of a lubricant flow may be one of the areas of recent extension of the classical lubrication theory. Among the few studies related to fluid inertia effects, Constatinescu and Galetuse [2] evaluated the momentum equations for laminar and turbulent flows by assuming the velocity profiles is not strongly affected by the inertia forces . Banerjee et.al [3] introduced an extended form of Reynolds equation to include the effect of fluid inertia, adopting an iteration scheme. Chen and Chen [4] obtained the steady- state characteristics of finite bearings including inertia effect using the formulation of Banerjee et al.[3]. Tichy and Bou-said [5] and Kakoty and Majumdar [7] used the method of average inertia in which inertia terms are integrated over the film thickness to account for the inertia effect in their studies. The above studies were mainly based on ideally smooth bearing surfaces.
The effect of fluid inertia has been studied by many researchers for turbulent flow using long and short bearing approximations. However, there are few publications which deal only with the intermediate regime for finite oil journal bearings. Reinhardt and Lund [6] studied the dynamic characteristics based on first-order perturbation solution starting from the Navier-stokes equation. Banerjee et al.[3] introduced an extended form of Reynolds equation to include the effect of fluid inertia adopting an iteration scheme.
Kakoty and Majumdar [7- 8] carried out a first order perturbation technique in modified Reynolds number as was done by Reinhardt and Lund [6] for isoviscous fluid, to study the stability of an oil journal bearing.
In the present work, a modified average Reynolds equation and a solution algorithm are developed to include fluid inertia and pressure depended variable viscosity effects in the analysis of lubrication problems. The solutions of modified average Reynolds equations are obtained using finite difference method with appropriate iterative schemes.
An attempt is being made here to study the effect of fluid inertia with pressure dependent variable viscosity on the
stability of oil film journal bearings under unidirectional constant load. The governing equations are deduced starting from the Navier-Stokes equation and flow continuity equations. These equations are identical (except for time dependent terms) to the ones developed by Constatinescu and Galetuse [2] which also include turbulent flow regime. In the present study the authors are particularly concerned with the laminar flow regime. An attempt is made to solve the system of nonlinear partial differential equation using Gauss-Siedel iteration method in a finite difference scheme.
A nonlinear time transient method is used to simulate the journal centre trajectory and to estimate the stability parameters.
-
BASIC THEORY
The modified average Reynolds equation for fully lubricated surfaces is derived starting from the Navier- Stokes equations and the continuity equation with few assumptions. The schematic diagram of flexibly supported oil Journal Bearing is shown in Figure.1
The non-dimensional form of the momentum equations and the continuity equation for a journal bearing may be written as
Fig.1 The schematic diagram of flexibly supported oil Journal Bearing
Here the variation in the density with time is considered to be negligible. The momentum equations may be presented in the following form using equation of continuity. However, the second momentum equation is not used any further because there is no variation in pressure across the
D
2
(1)
film.After Constantinescu and Galetuse [2] the velocity
R e
u u
u v
u w
u p u
components are approximated by the parabolic profiles.
L
_ 2
y
_
z y
The velocity components may be expressed in non- dimensional form as follows:
_
_
p 0 (2)
y
_
y
y
_
u _
_ 2
2
2
-
Q y
_
_
y
_
(7)
h h h
R w u w v w w D w
e 2
y
L
z
_
_ y
_
y
(8)
w Qz _ 2 _
D p
2 w
(3)
h
h
y
y
2
_
u
_
v
_
D w 0
L z _
(4
_
Q and Qz are dimensionless flow parameter in and z
_
L _
direction respectively. Substituting these two into
y
z
momentum equations and integrating give
Where, _
z ,
.t ,
p ,
2
_ y , x ,
_ y , x ,
z y
L 2 c R
p
Q h
2
p
e
-
I X
(9)
-
R
-
R
_ u _ v
_ w _
pc 2
u R ,
v c
w R
p R 2 and
2
h D p
(10)
c c2
Qz 2 L Re
-
-
I Z
Re Re . R
z
where,
The fluid film thickness can be given as
h c e cos
(5)
h 1
_
h
h
1
1 _ Q 1 1
1
2
h
2
h
_ I X
1
Q h
1
Q
Q
h 1 cos
(6)
2 2
3 6
3 2
10
where, h e
(11)
h , , 1 h 1 Q 1 Q 1 D h Q Q 1 D h 1 Q 1 Qz
c c 3 5 2 30 L z 6 L 5 2
z
z
_ _
I h 1 Q h 1 h Qz 1 Q 1 Q 1 h
Z 2 6
z 6
6
z 5
2
1 1
1 Qz
1
Q
1 D
Qz
(12)
Where, viscosity parameter,
0R
h Q
-
h Qz
h Qz
2
2
2
2
6 5
2 30
15 L
z c
Considering case of variable viscosity it has been observed oils viscosity increases with pressure and the following relationship is assumed similar to Majumdar et.al. [9],
The equations (6), (11), (12),(15), (16) and (17) are first expressed in finite difference form and solved using Gauss- Siedel method in a finite difference scheme.
p
p
0e
(13)
-
-
METHOD OF SOLUTION
-
Where = piezo viscosity co-efficient, 0 Viscosity of oil at the inlet condition
Assuming modified pressure function q we get
To find out steady-state pressure all the time derivatives are set equal to zero and Equations. (6), (11),(12),(15),(16)and(17) are solved simultaneously.
q 1 (1 e p )
(14)
For 0.2 the pressure distribution and flow parameters Q
Considering time dependent terms one can obtain the following form of modified Reynolds equation for dynamic condition considering fluid inertia effect.
and Qz are evaluated from inertia less (i.e, R 0 ) solution, i.e., solving classical Reynolds equation. These values are then used as initial value of flow parameters to solve
e
e
_ _ D 2 _ _
equations (16) and (17) simultaneously for Q and Qz using
h 3 q h 3 q
L
_
Gauss-Siedel method in a finite difference scheme. Then
z
z
update
I & I and then again calculate
Q and
Q with
_ _ x z z
h
h
(15)
modified value
I & I for use to solve Equation (15) for
12 61.0 2.0 x z
Where,
qc 2
q
_
new modified pressure q considering inertia effect with
0
0
R 2
and
_ 2 _
pressure dependent variable viscosity by using a successive over relaxation scheme. The latest values of Q and Qz and
_
Q h q R I
(16)
q are used iteratively to solve the set of equations until all
2 e X
_
_
variables converges. The convergence criterion adopted for
_ 2 _
pressure is
1 _
105
and also same
Q h
D q R I
(17)
qnew qold
z 2 L e Z
z
Where, I x and I z are same as equation (11) and (12) above.
Boundary conditions for equation (15) are as follows
-
The pressure at the ends of the bearing is assumed to be zero (ambient): q , 1 0
-
The pressure distribution is symmetrical about the mid-
criterion for Q and Qz .
For higher eccentricity ratios ( 0.2 ) the initial values for the variables are taken from the results corresponding to the previous eccentricity ratios.
Very small increment in is to be provided as Re* increases. The procedure converges up to a value of Re*=1.4 which should be good enough for the present
_
plane of the bearing:
q , 0 0
z
study. After getting
q solving the above equations
_ _
-
Cavitation boundary condition is given by:
simultaneously the
q is then converted to
p using
q ,
q ,
z 0 and q , z 0 for
equation (18) to calculate fluid film pressures for a
particular value of viscosity parameter.
2 2
_
Where 2 is the angular coordinate at which the film cavitates.
Since the bearing is symmetrical about its central plane ( z
=0),only one half of the bearing needs to be considered for
the analysis, Once the pressure distribution is evaluated
Now from equation (14) p can be written in terms of q as
ln(1 q)
_
fluid film forces and the load bearing capacity Wo
and
p
After non-dimensionalised the relation can be given as
_
attitude angle () are calculated as follows:
-
Fluid film forces
_ ln(1 q) p
(18)
The non-dimensional fluid film forces along line of centers and perpendicular to the line of centers are given by
_ F C 2
1 2 _ _
3
Fr r p cos d d z
(19)
R L
0 1
_ F C 2
1 2 _ _
F 3 p sin d d z
(20)
R L
0 1
where1 and 2 are angular coordinates at which the fluid film commences and cavitates respectively.
-
Steady state load
The steady state non-dimensional load and attitude angle are given by
W0
2
F r0
0
0
F 2
(21)
Fig. 3: Hydrodynamic fluid film forces in circumferential & radial
_
1 F
0
0
direction
2
o tan
_
(22)
M . d Xr F sin F cos
(23)
F
F
r
r
0
r dt2 r
d 2Y
Since the steady state film pressure distribution has been obtained at all the mesh points, integration of equations
Mr . r Fr cos F sin W0 dt2
(24)
-
and (20) can be easily performed numerically by using d 2 X dX
b b
b b
-
Mb . F cos F sin B. KX
-
(25)
Simpsons 1/ 3 rd. rule to get F r
and F . The steady state
dt2
Mb . F sin F cos B. KY
Mb . F sin F cos B. KY
d 2Y
r dt b
dY
load and the attitude angle are calculatd using
b b
r b
(26)
W 0 0
dt2 dt
equations (21) and (22). The relation between rotor & bearing motion are given by,
-
-
Equation of Motion
Xr Xb esin
Yr Yb ecos
(27)
(28)
The figure 2 shows the Coordinate system in oil journal bearing and figure 3 shows the hydrodynamic fluid film forces in circumferential & radial direction of the bearing
The above two equations are substituted in equations of motion. Finally the equations of motion are expressed in non-dimensional form as follows,
geometrics.
The equation of motion for a rigid rotor supported on four identical flexibly supported bearings are given by,
Xb
dXb
d
dY
(29)
Yb
b
d
1
F cos Fr sin
(30)
(31)
Xb _ _
.
m. M .W .2 .W .B. X b W .K .X
0 0 0 b
1
F sin Fr cos
(32)
Yb _
.
m.M .W .2 .W .B.Y b W .K .Y
d
d
0 0
0 b
(33)
Fig. 2: Coordinate system in oil journal bearing
d
d
d
d
A3.F A4 .E A2 .A3 A1.A4
A2 .E A1.F A2 .A3 A1.A4
(34)
(35)
(36)
where,
2
C 2 . cos .sin .
1 F sin F cos
r
0
0
M .W .2
2
D 2 . .sin .cos .
1 F cos F sin W
r 0
0
0
M .W .2
A1 sin , A2 cos , A3 .cos ,
A4 .sin
G X b
H Yb
E C G
F D H
-
Solution Scheme:
For stability analysis, a non-linear time transient analysis is carried out using the equations of motion to compute a new
set of ,, Xb ,Yb & their derivatives for the next time step
Stability analysis
_
for a given set of. Re *, L / D, ,
(Mass parameter) for a
There are limited publications which deal only with the non
0 M linear stability analysis for finite oil journal bearings with
particular Viscosity parameter . The forth order Runge- Kutta method is used for solving the equations of motion. The hydrodynamic forces are computed for every time step
by solving the partial differential equation for pressure
satisfying the boundary conditions.
Stability Analysis
To study the effect of fluid inertia with pressure dependent variable viscosity on journal center trajectory of flexibly supported bearings a set of trajectories of journal center and bearing has been studied and it is possible to construct the trajectories for numbers of complete revolution of the journal the plots shows the stability of the journal when the trajectory of journal and bearing center ends in a limit cycle. Critical mass parameter for a particular eccentricity ratio, slenderness ratio, modified Reynolds number, viscosity parameter and roughness pattern is found when the trajectories ends with limit cycle (Fig. 18 & Fig.19 ) or it changes its trend from stable to unstable.
IV RESULTS AND DISCUSSION
Steady state analysis
The steady-state analysis was done and its results are compared to the results of Kakoty et.al., [7] and Chen and Chen [4], for (for L/D = 1.0) as given in Table 1. These two results are in good agreement. A slight decrease in load capacity with modified Reynolds number (Re*) is observed in the present study. In the present study it is observed that the attitude angle increases slightly for most of the eccentricity ratios up to 0 0.8 .
Table 1: Comparison of Steady – state characteristics of a finite iso-viscous oil journal bearings for L/D=1 with fluid Inertia Effect.
flexibly support. Kakoty and Majumdar [7] studied the nonlinear stability of flexibly supported oil journal bearing with the effect of fluid inertia only with isoviscous fluid but did not provide any tables for comparison. Observed the nature / trend of the curves are quite similar with present study. Below figure shows in both the cases with same parameter values the trend of the trajectory is towards Point stability.
Figure 4: Comparison the nature of curve
-
Effect of modified Reynolds number with eccentricity ratio.
e
e
Figure 5 shows the variation of critical mass parameter with eccentricity ratio for different modified Reynolds number. It is observed that critical mass parameter increases with the increase in eccentricity ratio and increase of modified Reynold's number. The increasing trend is high for 0.5 and R 1.40
-
Effect of eccentricity ratio with modified Reynolds number
Figure 6 shows the variation of critical mass parameter with the modified Reynolds number for different eccentricity ratio. It is observed that critical mass parameter increases with the increase of modified Reynold's number for eccentricity ratio ( 0.5 ) and variation remain almost constant for 0.3
-
Effect of slenderness ratio with eccentricity ratio.
Figure 7 shows the variation of critical mass parameter with eccentricity ratio for different slenderness ratio. It is observed that critical mass parameter increases with eccentricity ratio and also as the slenderness ratio increases and the variation nature can be observed from the figure 7.
-
Effect of eccentricity ratio with slenderness ratio
Figure 8 shows the variation of critical mass parameter with slenderness ratio for different eccentricity ratio. It is observed that critical mass parameter increases with the increase of slenderness ratio and also with the increase of eccentricity ratio.
-
Effect of modified Reynolds number with slenderness ratio
Figure 9 shows the variation of critical mass parameter with slenderness ratio for different modified Reynolds number. It is observed critical mass parameter increases with slenderness ratio and also with the increase of modified Reynold's number. The nature of variation can be observed from the figure 9.
-
Effect of slenderness ratio with modified Reynold's number.
R
R
e
e
Figure 10 shows the variation of critical mass parameter with modified Reynolds number for different slenderness ratio. It is observed critical mass parameter remain almost
constant with
L D 1.0
-
although slight increase is noticed for
G.Effect of viscosity parameter with eccentricity ratio
Figure 11 shows the variation of critical mass parameter with eccentricity ratio for different viscosity parameter .It is observed that critical mass parameter increases with the increase of eccentricity ratio and also with increase of viscosity parameter.
H. Effect of viscosity parameter with modified Reynold's number
R
R
e
e
Figure 12 shows the variation of critical mass parameter with modified Reynolds number for different viscosity parameter. It is observed that critical mass parameter
-
Effect of damping coefficient with eccentricity ratio
Figure 14 shows the variation of critical mass parameter with eccentricity ratio for different damping coefficient. It is observed that the variation of critical mass parameter is
_
insignificant for different damping coefficient B
K Effect of slenderness ratio with viscosity parameter
Figure 15 shows the variation of critical mass parameter with viscosity parameter for different slenderness ratio. It is observed that critical mass parameter increases linearly with viscosity parameter and with the increase of slenderness ratio.
ncreases linearly with viscosity parameter .
-
and with the increase of
-
-
Effect of viscosity parameter with slenderness ratio
I. Effect of stiffness coefficient with eccentricity ratio
Figure 13 shows the variation of critical mass parameter with eccentricity ratio for different stiffness coefficient. It is observed critical mass parameter increases with increase of eccentricity ratio. The trend of increase is more prominent for 0.5 and K 0.1
Figure 16 shows the variation of critical mass parameter with slenderness ratio for different viscosity coefficient. It is observed that critical mass parameter increases linearly with slenderness ratio and with the increase of viscosity parameter .
-
comparison of variable viscosity and iso-viscous lubricants.
Figure 17 shows the comparison of critical mass parameter between pressure dependent variable viscosity and iso- viscous lubricant for different viscosity parameter for Re*=1.4 and L/D=1.0. It is observed that the critical mass increases with the increase in eccentricity ratio for all the viscosity observed for all the viscosity parameter compared to iso-viscous lubricants and the increase is more for
0.5 and = 0.09.
-
Journal centre trajectory (Limit cycle)
Figure 20 shows the variation of whirl ratio with eccentricity ration for different viscosity parameter . It is observed that whirl ratio decreases with increase of eccentricity ratio and also with the increase of viscosity
parameter .
V CONCLUSIONS
-
Stability increases with the increase of eccentricity ratio and with the increase of modified Reynolds number and with the increase in slenderness ratio and also increase of viscosity parameter.
-
Stability increases with the increase in eccentricity ratio and decrease with the increase in stiffness coefficient.
-
Stability is unaffected due to increase in eccentricity ratio and damping coefficient.
-
whirl ratio decreases with increase of eccentricity ratio and also with the increase of viscosity parameter
VI NOMENCLATURE
c = Radial clearance (m)
D = Diameter of Journal (m)
e = eccentricity (m)
Fr , F
= Steady state hydrodynamic film forces (N).
Figure 18. Journal Center trajectory (Limit cycle)
-
-
Bearing centre trajectory(Limit cycle)
0
_ _
r
r
F , F
0 0
0
= Dimensionless steady state hydrodynamic film forces
h = Film thickness, (m)
_
h = Dimensionless film thickness, h/c
L = Length of the bearing in m
p = Film pressure in Pa
p
p
_ = dimensionless film pressure =
pc2
R2
R = radius of journal in m
Re = Reynolds number, c R
Figure 19. Bearing Center trajectory (Limit cycle)
-
Variation of whirl ratio with eccentricity ratio for different viscosity parameter
Re = Modified Reynolds number, c R
R e
R e
t = time in s
u, v w
= velocity components in x, y, z directions in m/s.
_ _ _
u,v, w
= dimensionless velocity components
W0 = steady-state load bearing capacity in N
0
0
W = Dimensionless steady-state load W c2
0 R3 L
x, y, z
= coordinates
_ _
_ _
,Y , Z = Dimensionless coordinates,
x R , y c , z L 2
, 0 = Eccentricity ratio c (dimensionless),steady-state eccentricity ratio
= Density of the lubricant (kg m-3)
= Angular velocity of journal(rad s-1)
p = Angular velocity of whirl (rad s-1)
p
= Whirl ratio,
0 = Absolute viscosity of lubricating film at inlet condition (N s m-1)
= Attitude angle
Q = Dimensionless flow parameter in direction
_
Qz = Dimensionless flow parameter in z direction
_
Q = Dimensionless side leakage
1 , 2
= Angular coordinates at which film commences and cavitates.
0
0
R2 = Viscosity Parameter
c2
VII REFERENCES
-
Pinkus, O. and Sternlicht, B., Theory of Hydrodynamic Lubrication, New York, McGraw-Hill (1961).
-
V. N. Constantinescu and S. Galetuse On the Possibilities of Improving the Accuracy of the Evaluation of Inertia Forces in Laminar and Turbulent Films J. Tribol. Vol 96 (1), 69-77 (Jan 01, 1974) (9 pages), ASME, Journal of Tribology , Volume 96,Issue 1.
-
Banerjee Mihir B.,Shandil R.G.,and Katyal S.P.A Nonlinear Theory of Hydrodynamic LubricationJournal of Mathematical Analysis and Applications 117,48-56(1986)
-
Chen, C.H. and Chen, C.K., The influence of fluid inertia on the operating characteristics of finite journal bearings, Wear, Vol. 131, (1989), pp. 229-240.
-
Tichy, J., and Bou-Said, B., 1991, Hydrodynamic Lubrication and Bearing Behavior with Impulsive Loads, STLE Tribol. Trans., 34, pp. 505512.
-
E. Reinhardt and J. W. Lund The Influence of Fluid Inertia on the Dynamic Properties of Journal Bearings, Journal of Lubrication Technology, Volume 97 , Issue 2, 159-165, 1975.
-
Kakoty S. K. and Majumdar B. C., Effect of Fluid Inertia on Stability of Oil Journal Bearing. ASME Journal of Tribology, Vol 122, pp 741-745, October 2000.
-
Kakoty, S.K., Majumdar, B.C.: Effect of fluid inertia on the dynamic coefficients and stability of journal bearings, Proc. Inst. Mech.
Engrs., Vol. 214-J, (2000) 229-242
-
B.C.Majumder, D.E.Brewe and M.M.Khonsari, Stability of a rigid rotor supported on flexible oil Journal bearings, Journal of Tribology Trans Vol 110, 1988, pp 181 – 187.