
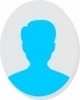
- Open Access
- Authors : Hemant Kumar , Amit Kumar Jha , G R Kesheorey
- Paper ID : IJERTV12IS040018
- Volume & Issue : Volume 12, Issue 04 (April 2023)
- Published (First Online): 07-04-2023
- ISSN (Online) : 2278-0181
- Publisher Name : IJERT
- License:
This work is licensed under a Creative Commons Attribution 4.0 International License
Static and Dynamic Analysis of Fiber Reinforced Angle Ply Laminated Composite Beam
Hemant Kumar1, Amit Kumar Jha2, G R Kesheorey3
1 M. tech Student, Department of Mechanical Engineering, Vindhya Institute of Technology & Science Indore (MP)
2 Senior Manager, Hindustan Aeronautics Limited, Bengaluru
3 Professor, Department of Mechanical Engineering, Vindhya Institute of Technology & Science Indore (MP)
Abstract – Composite materials are widely used in a wide range of industries, including aerospace, marine, vehicle, manufacturing, and sports. They are utilized because of their outstanding mechanical qualities, low density, and ease of producing components of any shape and size ranging from very small to very large. In the present study, a fiber reinforced angle ply laminated composite beam analysis performance is evaluated by computational method (MATLAB R2015a) and finite element analysis (MSC. PATRAN/NASTRAN). The analysis is approximated to one dimension angle ply laminated beam using classical beam theory. Three different method approximation like General Theory, Vinson and Sierakowski approximation, and Rios and Chan approximation are considered in the MATLAB 2015a programming code. Results of finite element static analysis of two different angle ply laminate composite beams [302/602] and [452/452] with simply and fixed supported boundary conditions have similar agreement as calculated in MATLAB 2015a for Vinson and Sierakowski and Rios and Chan approximations than General Theory. Similarly, results of finite element dynamic analysis (non-dimensional frequency) of angle ply laminate beams with simply supported boundary conditions have similar agreement with MATLAB 2015a for Vinson and Sierakowski and Rios and Chan approximations than General Theory. In addition, the results of static and dynamic analysis of a composite beam with different angle plies ([302/602], [452/452]) also showed that [302/602] has more stiffness than [452/452].
Keywords- Angle ply; Composite Beam; Static Analysis; Dynamic Analysis; Non dimensional frequency.
-
INTRODUCTION
Since modern composite materials are increasingly being used in many engineering applications due to their outstanding characteristics, many researchers have focused on static and dynamic analysis of laminated composite beams comprised of such materials [1, 2]. In the present environment, many researchers are focusing on increasing efficiency by reducing the weight of the components while maintaining overall strength. Composite materials outperform most metallic materials in terms of strength and stiffness to weight ratio [2].
A composite is a material composed of two or more macroscopic phases, the mechanical performance and characteristics of which are intended to outperform those of constituent materials functioning separately [2]. One of the phases is usually discontinuous, stiffer and stronger, and is referred to as reinforcement, whilst the other is continuous, less stiff and weak, and is referred to as matrix. Composites provide distinct advantages over monolithic materials, including high stiffness, long fatigue life, low density, and adaptability to the structure's intended function [2, 3].
Corrosion resistance, wear resistance, appearance, temperature-dependent behaviour, environmental stability, thermal insulation, conductivity, and acoustic insulation are all significant features [2, 3]. The best part is that the composite's properties can be changed as needed by changing the reinforcing and matrix materials [2].
Additionally, carbon-reinforced composites are currently being utilized extensively in sports and recreational equipment, like golf clubs, filament-wound rocket motor cases, pressure vessels, aircraft structural components, and both military and commercial aviation, such as aircraft wings and helicopter rotors [4, 5]. In the case of aircraft, composite materials can be used in various parts of aircraft [5] such as fuselage, wings, flaps, empennage etc. to increase strength and reduce weight as shown in Fig. 1. Furthermore, angle ply laminates are commonly used during the design of structures [4, 5].
A. Fiber Reinforced Angle Ply Laminated Composite Beam In composite laminates, angle ply laminates have a very high resistance to through thickness fracture. Angle-ply laminates have an arbitrary number of layers. Each ply has the same thickness and is the same material. The plies have alternating fiber orientations of + and [2, 3, 6].
An angle-ply laminate can be either symmetric or anti-symmetric. A simple example of the antisymmetric angle-ply laminate is shown in Fig. 2. Angle ply laminates, which include not only unidirectional layers but also random staple fiber sections with a much lower fiber fraction, are extensively utilized in the manufacture of aviation and Formula One car brake discs.
-
LITERATURE REVIEW
Composites are one of the best materials nowadays because you can adjust the qualities to meet your needs by changing the components of composites. It can be used in critical areas due to its wide range of property variability. It possesses a high strength-to-weight ratio and a high stiffness- to-weight ratio, as well as excellent corrosion and wear resistance. Several authors researched composite materials and their properties.
The authors [6] discussed the significance of composite in our daily lives. According to the author's research, the fundamental goal of fiber- reinforced composites is to generate materials with high strength and increased elastic modulus. The applied load passing from the matrix to the fibers, the interfacial connection between the fiber and matrix, their relative
Fig. 1 Aircraft with components
Fig. 2 Anti-symmetric angle () ply laminate
alignment, and the nature of the fiber scheming the overall material characteristics all had an impact on the strength elevation. Rajpurohit [7] outlined many types of composite
manufacturing processes that have been employed up until this point in the composites industry. A consistent production process for composite materials cannot be established because
there are so many different manufacturing methods accessible. Component geometry, size, and the necessary mechanical performance are the main determinants of the ultimate path. The classic hand lay-up method is the most straightforward and reasonably priced method of preparing composite material. Other procedures described included: a) hand layup/wet layup b) sprat lay-up c) filament winding d) pultrusion e) resin transfer molding, and f) infusion molding. Furthermore, bio-based fiber was discussed by A. Vinod [8] as a useful replacement for synthetic and harmful materials. The author's review of processing procedures, characterizations, future potential, and approaches to get over constraints in bio- fibers, biopolymers, biofilms, and bio composites were presented. Muhsin J. Jweeg [9] presented experimental and theoretical study of composite materials reinforcement fiber. Unidirectional fiber types in the longitudinal direction and woven reinforcement fiber types in the transverse direction had the best modulus of elasticity for reinforcement composites. The authors [10] reviewed most of the research done in recent years on the vibration analysis of composite beams.
The review focused on the theory being applied (thin, thick, layerwise), methods for solving equations (finite element analysis, differential transform, and others), experimental techniques, smart beams (piezoelectric or shape memory), complicating effects in both material and structur, and these issues were discussed in more detail in the section on smart beams (viscoelastic, rotating, tip mass and others).
M.S. Qatu [11] put all set of equations for the free and forced vibration analysis of laminated composite beams of shallow curvature. According to the author, the beam should be vibrating in its plane. Exact solutions were used to determine the natural frequencies for curved beams that were simply supported. Lamination-induced extension-bending coupling was separated from curvature-induced coupling. It also included information on how curvature, material orthotropy, and lamination sequence impacted natural frequencies. Using experimental research, Haider [12] discovered how to avoid stress concentration in fatigue design and that the stress level dominates the composite failure mode. A carbon fiber composite had the highest ultimate tensile strength, according to the study's findings.
The work of Mathapati Sudhir [13] on E-glass fiber reinforced composite was presented. On the constructed composite, tests for tensile and compression were performed. Finally, using analysis tools like ANSYS, the experimental results were contrasted with those of the finite element analysis. Based on the Euler-Bernoulli beam theory, the authors [14] offered a free vibration analysis of a laminated composite beam. The laminated composite beam's natural frequencies were determined for each case and displayed to show how these alterations affected the natural frequencies. The outcome demonstrated that, in all circumstances, natural frequencies for all modes drop with increasing length-to- thickness ratios. Using the Classical Laminate Theory, Akkerman [15] constructed a three-dimensional thermoelastic equation of quasi-isotropic laminates with in plane and out of plane properties. The goal of MESOTEX (Mechanical
Simulation of Textile), an analytical model established by the authors [16], is to predict the 3D elastic and failure properties of various woven fiber composite materials. A point-wise stiffness reduction technique was used to extend the analytical model in order to estimate failure strength under tensile load in woven-fiber composite materials. An overview of the impact response of woven fabric composite plates was presented by Cesim Atas [17]. The findings shown that by comparing the corresponding load-deflection curves, energy profile diagrams, and pictures of injured specimens, the damage process could be recreated. Using a doubly-tapered compact tension specimen, the authors [18] had experimentally determined the tensile intralaminar fracture toughness of the carbon/epoxy woven composite material. With the use of micromechanical analyses and a two-scale asymptotic homogenization theory, Dasgupta [19] was able to determine the thermo-mechanical and thermal characteristics of plain-weave fabric-reinforced composite laminates. Model outputs are compared to both experimental values and models to determine the results. Two-dimensional (2D) orthogonal plain weave fabric laminates were subjected to in-plane shear loading, and Ganesh V.K. [20] examined the impact of fabric geometry on the in-plane shear strength and in-plane shear modulus. In order to create three-dimensional woven composites, Haidar F [21] improved his precise numerical methods. To investigate the mechanical performance of carbon/epoxy, five specimens were created. The numerical results are validated by the experimental finite element analysis results for the carbon/epoxy composite, which agreed with each other with an error of 5.05 percentage. Sahoo S. [22] developed numerical models in the MATLAB environment based on the higher order shear deformation theory in conjunction with the finite element method to study numerically the static, free vibration, and transient behaviour of laminated structures with and without delamination. Moreover, a simulation model was created for analysis purposes using the finite element programme ANSYS 15.0. Mehdi Hajianmaleki [23] used modified ABD parameters in conjunction with a strict first order shear deformation theory to analyze the static and free vibration behaviour of typically laminated deep curved beams. The findings demonstrated that FSDT can accurately forecast the static and free vibration behaviour of composite deep beams of any lamination and boundary condition when taking into account more precise stiffness parameters.
The outcomes of a composite material made from knitted fabric and woven fabric were compared by the authors [24]. Because knitted fabrics are distinguished by the process of stitch overlapping that provided superior resistance, comparisons of composite materials made from knitted fabrics revealed that they had better mechanical qualities than woven fabrics. According to the authors [25], damping in structures made of various materials was estimated (steel, brass, aluminium). The study demonstrated the structural dampening effect of an impact hammer on beam vibration. Around 10% to 15% of the overall system damping is caused by structural damping. The major goal of the project was to use LabVIEW software to estimate the natural frequency and damping ratio of cantilever beams made of aluminium, brass, and steel. The
result was then verified using ANSYS for vibration analysis and harmonic analysis. The findings indicated that brass has a higher damping ratio than steel or aluminium. The behaviour of unidirectional glass fiber reinforced plastic (GP) composites with various orientations under tensile and impact loading was studied by Naresh [26]. The theoretical tensile characteristics are determined using the classical laminate theory (CLT). The theoretical model's predictions and the results of experimental experiments agree well on the properties. The study's key findings show that the tensile strength and modulus decrease as the off-axis loading angle increases. For orthotropic circular cylindrical shells with traditional boundary conditions, B. Liu [27] developed an analytical method and closed-form vibration solutions with analytically calculated coefficients. The closed-form natural frequencies are successfully derived in this work using the separation of variables method. They discovered in a small package. In addition, the eigenvalues' properties were looked at. By numerical comparisons with existing solutions in the literature and the semi-analytical differential quadrature finite element method (S-DQFEM) solutions, the precise solutions were validated. Equilibrium equations and the corresponding boundary conditions for doubly curved, reasonably deep, and thick composite shells were presented by Ebrahim Asadi [28]. There were employed two First Order Shear Deformation Theories (FSDTs). For thick shells, the first one employs plate stiffness parameters, whereas in the second, the effect of curvature is taken into account when calculating the stiffness parameters. A three-dimensional (3D) study was used to test the correctness of the shell theories, and the findings are compared between the two hypotheses.
A static and dynamic analysis of graphite/epoxy composite plates was presented by Junaid Kameran Ahmed [29]. In order to determine the maximum deflection, laminated plate parametric studies were included in the static analysis. ANSYS 12.0 was used to model the plates, and the results were compared to those of the finite element approach. Evaluating the plates' inherent frequency served as the study's dynamic component. The outcomes demonstrated that for both isotropic and orthotropic plates, the deflection for a clamped boundary condition is lower than that for a simply supported boundary condition.
-
MATHEMATICAL FORMULATION
-
Laminate representation
A laminate is made of a group of single layers bonded to each other. Each layer can be identified by its location in the laminate, its material, and its angle of orientation with a reference axis as shown in Fig. 3 [30]. Each lamina is represented by the angle of ply and separated from other plies by a slash sign. The first ply is the top ply of the laminate. Special notations are used for
Fig. 3 Schematic of a laminate
-
Mathematical model
It is commonly known that laminate analysis can be accomplished using the Classical Laminate Theory (CLT). There are two most common theory to solve beam problem [2, 15].
-
Classical beam theory
-
Timoshenko beam theory (shear deformation beam theory)
In the present work, Classical beam theory is considered. Assumptions of classical beam theory are:
-
Plane section remain plane.
-
The transverse normal on mid plane remain normal to mid plane after deformation.
-
The transverse normal is unstretched.
-
A lamina and a group of laminae known as a laminate make up a fiber composite beam. Because each lamina has three symmetry planes, it exhibits orthotropic material behaviour. Hence, the stress-strain (ij – ij) relationship is expressed as given in (1) [2]
(1)
where, [Cij] is stiffness matrix.
The above equation is for the 3D state of stress, but the thickness of the lamina is less as compared to its length, so our assumption is to make it a plane stress condition
(3=31=23=0). Now the stress strain relationship expressed as [2]
(5)
where, [Q] is known as reduced stiffness matrix.
(2)
where, is the slope of the laminated middle surface in the x direction.
All fibers are not set in a principal direction, so we have to
transform the other lamina along an arbitrary direction as per the beam co-ordinate x and y direction.
(3)
where, [ and [T] are reduced transformed stiffness matrix and transformation matrix, respectively.
The transformation matrix [T] due to an inplane rotation is expressed as [2, 30-32]
(4)
Similarly, the displacement, v, in the y-direction is
(6)
Also, the vertical translation of point C in the direction of the z-axis is given by:
(x, y, z) = 0 (x, y) (7)
As per Kirchhoff hypothesis, strain – displacement
relations are expressed at any point within the laminate such as [[2, 30-32]
Strain in x direction:
The implications of the Kirchhoff hypothesis on the laminate displacements u, v, and w in the x, y, and z directions are derived by use of the laminated cross section in the x-z plane as shown in Fig. 4. The displacement in the x of point B from the undeformed middle surface to the deformed middle surface is u0.
Since, line ABCD remains straight under deformation of the laminate, the displacement, u, at point C through the laminate thickness is expressed as
(8)
Strain in y direction:
(9)
Fig. 4 Laminate geometry of deformation in the x-z plane
Shear strain in x and y plane:
(10)
The second assumption of classical lamination theory [2, 30-32] is that each point within the volume of a laminate is in a state of plane stress. Therefore, the stress-strain relations for a lamina is
(11)
where, mid-plane strains and curvatures are denoted by 0 and k, respectively.
By substitution of the strain variation through the thickness in the stress-strain relations (11), the stresses in the kth layer is given in terms of the laminate middle- surface strains and curvatures (k) as [2, 30-32]
(12)
In addition, the force and moment resultants acting on a laminate are computed by integration of the stresses in each layer through the laminate thickness (H) as follows [2, 30- 32]
and,
(13)
where, Nx, Ny, and Nz = Force per unit width of cross section in x, y, and z directions and, Mx, My, and Mz = Moment per unit width of cross section in x, y, and z directions, respectively.
Furthermore, force and moment components on a laminate are shown in Fig. 5 and Fig. 6, respectively.
Laminate analysis by means of the Classical Laminate Theory combines Kirchhoffs hypothesis for bending of thin plates with integration over separate layers leading to the well-known ABD-matrix, relating forces and moments per unit width, N and M, respectively, to the mid-plane strains and curvatures, denoted as 0 and k, as [2, 15, 31].
Fig. 5 Force components on a laminate
Fig. 6 Moment components on a laminate
The forces and moments in the lamina are expressed also as
(14)
(15)
where, zk is the directed distance to the bottom of the kth layer and zk-1 is the directed distance to the top of the kth layer.
are obtained using:
(16)
Each component of [ABD] matrix is formulated as below
where, A11, B11, and D11 are the stiffness coefficients.
The equations of motion are
,
(18)
and, (19)
(17)
where, Aij (extensional stiffnesses) are the sum of the product of the individual laminae [and the laminae thicknesses, Bij represents the bending-extension coupling stiffnesses, and, Dij represents the bending stiffnesses.
-
-
FINITE ELEMENT ANALYSIS
-
Static Analysis of a composite beam
Using assumptions for thin beams, force and moment resultants
where, px and pz are external forces per unit length in x and z directions, respectively.
Two simultaneous displacement differential equations of u and w were obtained after solving (19). The displacement differential equations expressed as
and,
(20)
Boundary conditions considered to solve the above equations are such as:
vibration) is obtained by substitution of the displacement in u and w directions as given in equation 1.25. The equation is expressed as [31]
(26)
where,
For simply supported beam are:
and,
For fixed supported beam are:
and,
(21)
and,
where, I = moment of inertia, b = width of the beam and (k) is the lamina density per unit volume.
The nontrivial solution for natural frequencies of the above dynamic equation can be found by setting the determinant of the characteristic equation matrix to zero. After equating the determinant of the above equation to zero, the natural frequencies of the beam. Non-dimensional frequency is expressed as
(22)
Stress in the axial direction in any lamina can be found by the following equation
(27)
where, E1= Stiffness in longitudinal direction, = Density of the material, h = Thickness of the beam, and, a = Length of the beam.
(23)
The shear stress in any lamina can be found by using the following equation
(24)
-
Dynamic Analysis of a composite beam
The dynamic characteristic equation has calculated by considering simply supported boundary condition and the following displacement [31]
-
-
RESULTS AND DISCUSSION
Static and free vibration analysis is carried out by MATLAB for a composite beam. The results presented in this section are based on simply supported and fixed supported boundary conditions of a beam. The ([302 /602] and [452 /452]) angle plies laminates are considered for the analysis based on General Theory, Vinson and Sierakowski, and Rios and Chan theories of approximation [3,23,31,33].
Material properties and dimensions of the beam are given as E1 = 138 GPa, E2 = 8.96 GPa, 12 = 0.3, G12 = 7.1 GPa,
= 1580 kg/m3, and, a=1m, b=0.025m, h=0.05m.
where, E = Youngs modulus, = Poissons ratio, G= Shear modulus, = material density,
and a, b, and h are the length, width, and thickness of the
where, ,
and, and m represent natural frequency and mode number, respectively.
(25)
beam.
-
Static Analysis
A uniformly distributed load of 250000 N/m was applied in the transverse direction to the beam and the resulting deflection, stresses, and frequencies of angle-plies laminates ([302/602] and [452/452]) were assessed by MATLAB and finite element analysis (FEA). Moreover, MATLAB R2015a results considered different approaches (General Theory,
The dynamic characteristics equation of motion (free
Vinson and Sierakowski, Rios and Chan) [3, 23, 31, 33]. In
addition, FEA used MSC. PATRAN/NASTRAN tools for the present work. Two types of boundary conditions (simply supported and fixed supported) were considered for the analysis.
1). Laminate [302/602]
The results of static analysis (MATLAB and FEA) using simply supported boundary conditions for a composite beam are given in Table 1 and Fig. 7 to Fig. 8, respectively.
Table 1: Static analysis results for laminate [302/602] using simply supported boundary condition
Results
General Theory
Vinson and Sierakowski
Rios and Chan
FEA
(Deflection in z) max (m)
0.3333
0.7452
0.6785
0.7120
(Shear stress) max (Pa)
0.9309×109
1.8705×109
1.7645×109
1.7941×109
Fig. 7: Deflection in transverse direction
Fig. 8: Shear stress for lamina
The results show that the FEA of the [302/602] laminate using simply supported boundary conditions beam has closer results with the Vinson and Sierakowski and the Rios and Chan approaches [3,23,31,33] rather than the General Theory approach.
The results of static analysis (MATLAB and FEA) using fixed supported boundary conditions for a composite beam are given in Table 2 and Fig. 9 to Fig. 10, respectively.
Table 2: Static parameters for laminate [302/602] using fixed supported boundary condition
Results
General Theory
Vinson and Sierakowski
Rios and Chan
FEA
(Deflection in z) max (m)
0.0667
0.1490
0.1357
0.1645
(Shear stress) max (Pa)
0.9019×109
1.8276×109
1.7503×109
1.7141×109
Fig. 9: Deflection in transverse direction
Fig. 10: Shear stress for lamina
The results show that the FEA of the [302/602] laminate using fixed supported boundary conditions beam has closer results with the Vinson and Sierakowski and the Rios and Chan approaches rather than the General Theory approach.
2). Laminate [452/452]
The results of static analysis (MATLAB and FEA) using simply supported boundary conditions for a composite beam are given in Table 3 and Fig. 11 to Fig. 12, respectively.
Table 3: Static parameters for laminate [452/452] under simply supported boundary condition
Results
General Theory
Vinson and Sierakowski
Rios and Chan
FEA
(Deflection in z) max(m)
0.2753
0.7980
0.7980
0.7358
(Shear stress) max (Pa)
0.4585×109
1.3292×109
1.3292×109
1.3314×109
Fig. 11: Deflection in transverse direction
Fig. 12: Shear stress for lamina
The results show that the FEA of the [452/452] laminate using simply supported boundary conditions beam has closer results with the Vinson and Sierakowski and the Rios and Chan approaches [3,23,31,33] rather than the General Theory approach.
The results of static analysis (MATLAB and FEA) using fixed supported boundary conditions for a composite beam are given in Table 4 and Fig. 13 to Fig. 14, respectively.
Table 4: Static parameters for laminate [452/452] using fixed supported boundary condition
Results
General Theory
Vinson and Sierakowski
Rios and Chan
FEA
(Deflection in z) max (m)
0.0551
0.1596
0.1596
0.1725
(Shear stress) max (Pa)
0.4585×109
1.3292×109
1.3292×109
1.3125×109
Fig. 13: Deflection in transverse direction
Fig. 14: Shear stress for lamina
The results show that the FEA of the [452/452] laminate using fixed supported boundary conditions beam has closer results with the Vinson and Sierakowski and the Rios and Chan approaches rather than the General Theory approach .
-
Dynamic Analysis
Different approaches for obtaining the natural frequencies of the first 3 modes were evaluated. Two different types of laminates were selected to cover different kinds of composite beams. These include [302/602] and [452/452] angle plies laminates.
Free vibration analysis is carried out in MATLAB for a composite beam using simply supported boundary
conditions. Furthermore, modal analysis of a simply supported boundary condition one dimensional composite beam is also performed with the help of a finite element tool (MSC. PATRAN/NASTRAN).
Results of free vibration analysis of a composite beam by MATLAB are presented in non-dimensional frequencies () for General Theory, Vinson and Sierakowski, Rios and Chan models [3, 11, 23, 33]. In addition, results of finite element
modal analysis are also presented in this section. Furthermore, the results are summarized in Table 5 and Table 6 for [302/602] and [452/452] laminates, respectively. In addition, mode shape (Mode 1) of simply supported composite beam with [302/602] and [452/452] laminates is also shown in Fig. 15 and Fig. 16, respectively.
The results show that both laminate non-dimensional frequency calculations by FEA and MATLAB (different theories) have good agreement. In addition, the results of modal analysis are closer to Vinson and Sierakowski and Rios and Chan results than General Theory results.
Table 5: Non-dimensional frequencies for [302/602] laminate
Mode Number |
General Theory |
Vinson and Sierakowski |
Rios and Chan |
FEA |
1 |
5.1439 |
3.4507 |
4.8197 |
4.259 |
2 |
20.5648 |
13.7655 |
19.1842 |
15.858 |
3 |
46.1895 |
30.9458 |
43.0678 |
35.194 |
Table 6: Non-dimensional frequencies for [452/452] laminate
Mode Number |
General Theory |
Vinson and Sierakowski |
Rios and Chan |
FEA |
1 |
5.6614 |
3.3248 |
4.5414 |
3.865 |
2 |
22.6457 |
18.1615 |
18.1626 |
14.649 |
3 |
50.9528 |
40.8629 |
40.8754 |
32.682 |
Fig. 15: Mode 1-Natural frequency for [302/602] laminate
Fig. 16: Mode 1-Natural frequency for [452/452] laminate
VI CONCLUSION AND FUTURE SCOPE
Different approaches (General Theory, Vinson and Sierakowski, Rios and Chan) by MATLAB for static and dynamic analysis of a composite beam with different angle plies ([302/602], [452/452]) were studied. The approaches were compared with finite element analysis (MSC. PATRAN/NASTRAN) of a composite beam with different angle plies ([302/602], [452/452]).
Furthermore, the results (deflection, shear stress, and non-dimensional frequencies) showed good accuracy of the Vinson and Sierakowski and Rios and Chan models for the composite beam with different angle plies ([302/602], [452/452]) in static and dynamic analysis with respect to General Theory model.
In addition, the results of static and dynamic analysis of a composite beam withdifferent angle plies ([302/602], [452/452]) also showed that ([302/602] has more stiffness than [452/452].
In future studies, the analysis could be extended to consider different types of aerodynamic loads, fatigue life estimation, and layup delamination effect etc.
ACKNOWLEDGEMENT
I am thankful to my friends for their kind support.
REFERENCES
[1] A. S. Sayyad, Y. M. Ghugal, On the free vibration of angle-ply laminated composite and soft core sandwich plates, Journal of Sandwich Structures and Materials, 19 (6), 2016, https://doi.org/10.1177/1099636216639000. [2] R. M. Jones, Mechanics of Composite Materials, 2nd edition, CRC Press, ISBN 9781315272986, 1999. [3] J. R. Vinson, R. L. Sierakowski, The behavior of structures composed of composite materials, Solid Mechanics and its Applications, 105:1445, doi: 10.1115/1.3172985, 2002. [4] Michael C. Y. Niu, Airframe stress analysis and sizing, Hong Kong Conmmilit press LTD, 2nd edition, 1999. [5] S. Kumar, A. K. Jha, G R Kesheorey, Design and Fatigue Analysis of a Typical Aircraft Wing fuselage Lug attachment structure, International Research Jounral of Engineering and Technology 10 (1):e ISSN:23950056, p-ISSN:23950072, 2023. [6] Prashanth S., Subbaya K. M., Nithin K., Sachhidananda S., Fiber Reinforced Composites – A Review, Journal of Material Science& Engineering, 06(03), 2017.
[7] Ashok Rajpurohit, Fiber Reinforced Composites Advances in Manufacturing Techniques, FRP Today Samanthi Publications Pvt. Ltd., 04:1-22, 2014. [8] A. Vinod, M. R. Sanjay, Siengchin Suchart, P. Jyotishkumar, Renewable and sustainable biobased materials: An assessment on biofibers, biofilms, biopolymers and biocomposites, Journal of Cleaner Production, 258, 2020. [9] Muhsin J. Jweeg, Ali S. Hammood, Muhannad Al-Waily, Experimental and theoretical studies of mechanical properties for reinforcement fiber types of composite materials, International Journal of Mechanical and Mechatronics Engineering, 12(4), pages 6275, 2012. [10] Mehdi Hajianmaleki, Mohamad S. Qatu, Vibrations of straight and curved composite beams: A review, Composite Structures, 100, pages 218232, 2013. [11] M. S. Qatu, In-plane vibration of slightly curved laminated composite beams, Journal of Sound and Vibration, 159(2), pages 327338, 1992. [12] Haidar F. AL-Qrimli, Fadhil A. Mahdi, and Firas B. Ismail, Carbon/Epoxy Woven Composite Experimental and Numerical Simulation to Predict Tensile Performance,Advances in Materials Science and Applications, 4(2), pages 3341, 2015. [13] Sudhir S. Mathapati, Tushar T. Hawal, Prashant P. Kakamari, and Nikhil R, Original Article Analysis and characterization of Tensile and Compressive Properties of the Chopped Strand Mat E-Glass Fiber Reinforced Epoxy Composites, AdvancedEngineering and Applied Sciences: An International Journal, 4(3), pages 2933, 2014.
[14] Murat Balci, Mustafa Ouz Nalbant, Ercan Kara, Ömer Gündodu, Free vibration analysis of a laminated composite beam with various boundary conditions, International Journal of Automotive and Mechanical Engineering, 9(1), pages 1734 1746, 2014. [15] R. Akkerman, On the properties of quasi-isotropic laminates, Composites Part B: Engineering, 33(2), Pages 133140, 2002. [16] D. Scida, Z. Aboura, M. L. Benzeggagh, and E. Bocherens, A micromechanics model for 3D elasticity and failure of woven- fibre composite materials, Composites Science and Technology, 59(4), pages 505517, 1999. [17] Cesim Atas, Onur Sayman, An overall view on impact response of woven fabric composite plates, Composite Structures, 82(3), pages 336345, 2008. [18] N. Blanco, D. Trias, S. T. Pinho, and P. Robinson, Intralaminar fracture toughness characterization of woven composite laminates, Engineering Fracture Mechanics, 131, pages 361 370, 2014. [19] A. Dasgupta, R. K. Agarwal, and S. M. Bhandarkar, Three- dimensional modeling of woven-fabric composites for effective thermo-mechanical and thermal properties, Composites Science and Technology, 56(3), pages 209223, 1996. [20] V. K. Ganesh, N. K. Naik, Failure behaviour of plain weave fabric laminates under in-plane shear loading: effect of fabric geometry, Composite Structures, 30(2), pages 179192, 1995 [21] Haidar F. AL-Qrimli, Mustafa J. Al-Dulaimi, Kayser A. Ameen, Composite Failure Modes at High Cyclic Fatigue Life Evaluation, International Journal of Automotive and Mechanical Engineering, 17(3), Pages 80968103, 2020. [22] Sushree Sasmita Sahoo, Experimental and Numerical Investigation of Static and Dynamic Analysis of Delaminated Composite Plate, National Institute of Technology Rourkela, 2016. [23] Mehdi Hajianmaleki and Mohamad S. Qatu, Static and vibration analyses of thick, generally laminated deep curved beams withdifferent boundary conditions, Composites Part B: Engineering, 43(4), pages 17671775, 2012.
[24] Karnoub A. Makhlouf S, Comparison Mechanical Properties for Fabric (Woven and Knitted) Supported by Composite Material, Journal of Textile Science & Engineering, 05(04), 2015. [25] Himanshu Mevada and Dipal Patel, Experimental Determination of Structural Damping of Different Materials, Procedia Engineering, 144, pages 110115, 2016. [26] K. Naresh, K. Shankar, R. Velmurugan, Experimental and theoretical investigation of a unidirectional glass/epoxy composites under tensile and impact loading, Materials Today: Proceedings, 5(11), pages 2517425184, 2018. [27] B. Liu, Y. F. Xing, M. S. Qatu, A. J. M. Ferreira, Exact characteristic equations for free vibrations of thin orthotropic circular cylindrical shells, Composite Structures, 94(2), pages 484493, 2012. [28] Ebrahim Asadi and Mohamad S. Qatu, Static analysis of thick laminated shells with different boundary conditions using GDQ, Thin-Walled Structures, 51, pages 7681, 2012. [29] Mohamed A. M. Shehata, Ahmed S. A. Abou-Taleb, Ahmed Nassef, Investigation and Simulation of Mechanics of Solid Beam versus Sandwich Beams with Different Core Material, Research Journal of Applied Sciences, Engineering and Technology, 16(3), pages 88103, 2019. [30] A. K. KAW, Mechanics of Composite Materials. Taylor and Francis Group, USA, Second Edition, CRC Press, ISBN: 0-8493- 1343-0, 2006. [31] M. S. Qatu, Theories and analyses of thin and moderately thick laminated composite curved beams, Int. J. Solids Structures 30 (20):2743-2756, 1993. [32] Stephen W. Tsai, H. Thomas Hahn, Introduction to Composite Materials. Technomic Publishing Company, Inc., Pennsylvania, USA, ISBN 0-87762-288-4.1980. [33] Rios G., Chan W. S., A Unified Analysis of stiffened Reinforced Composite beams. In: Proceedings of 25th ASC conference. Dayton, USA, 2010.