
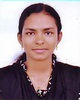
- Open Access
- Authors : Sibi Mathew , Narayanan N I
- Paper ID : IJERTV10IS070246
- Volume & Issue : Volume 10, Issue 07 (July 2021)
- Published (First Online): 30-07-2021
- ISSN (Online) : 2278-0181
- Publisher Name : IJERT
- License:
This work is licensed under a Creative Commons Attribution 4.0 International License
Steel Fiber Reinforced Concrete Encased Steel Composite Columns Subjected to Combined Axial and Lateral Cyclic Loading
Sibi Mathew
Dept. of Civil Engineering Govt. College of Engineering, Kannur
Kannur, India
Prof. Narayanan N I
Dept. of Civil Engineering Govt. College of Engineering, Kannur
Kannur, India
AbstractConcrete Encased Steel (CES) composite columns are those columns in which structural steel is encased inside reinforced concrete. By combining both materials, columns can handle a large amount of load with a lesser cross sectional area. Moreover they improves the overall rigidity of the building and provide significant resistance to lateral loads. These columns are widely used in high rise building construction. Main disadvantage of these columns are the construction difficulties. Since reinforcement bars and steel sections are encased, the concrete pouring becomes more difficult. Solution for these problems are the use of welding couplers or providing holes in steel flanges and steel web. Both the methods will increase the cost of construction and also it can affect the total bearing capacity and authenticity of the structure. An innovative method proposed to overcome these difficulties is the use of steel fibers and replacing the reinforcement bars. This paper studies the behavior of steel fiber reinforced concrete encased steel sections under combined axial and lateral cyclic loading. This paper also investigates the influence of axial compression ratio on the behavior under combined axial and lateral cyclic loading.
KeywordsConcrete encased steel, steel fiber, composite column, combined axial and cyclic lateral loading
-
INTRODUCTION
Concrete Encased Steel (CES) is an ordinary type of composite construction in which a structural steel section is placed inside reinforced concrete. Main advantages of using this type of construction is that by combining all the materials we can utilize the benefits of all the materials. These type of constructions are becoming more popular in top down constructions and construction of high rise buildings [9]. Moreover, they can take a large amount of load using a smaller cross sectional area. Thus it brings economic benefits also. Other benefits include they improves the overall rigidity of the buildings and performs better seismic behaviour. They also shows better protection against fire. In spite of these advantages, the main disadvantage with these columns is their construction difficulty. Since the structural steel is placed inside the reinforced concrete, they lacks concrete pouring quality. Lateral reinforcement provides confinement to concrete core. Other factors includes its distribution, loading type and cross section configuration [2]. Also the steel section causes difficulties for the formation of reinforcement cage. They also sometimes leads to unclosed and discontinuous stirrups. The common methods used to overcome these difficulties includes the use of welding couplers or to provide slots in the steel
flanges and webs for the stirrups to get closed. The openings can affect the load bearing capability of the column. The use of welding couplers also increases expenses and also needs additional labour. Another method proposed to overcome these difficulties is the addition of steel fiber (SF) and removal of the reinforcement cage. Steel fibers can effectively improves the structural performance of the concrete and also it delays the formation and propagation of cracks [5]. By removing the reinforcement cage and adding steel fiber, the process of making of rebar cage can be avoided and also a better steel section can be used. It causes an increase in moment of inertia and height of the steel section. Thus the shear capacity and bending capacity of the member also increases.
-
VALIDATION
A. Geometry Modelling
Nonlinear finite element analysis (FEA) is conducted using ABAQUS software. Cross section dimensions of the section used in the study are 230 mm x 230 mm and length 1000 mm. Reinforcement of two different diameters were used. Bars of 12 mm diameter were used at the four corners. Minimum clear cover is provided. Stirrups of 8 mm diameter were used throughout the length of column at a spacing of 120 mm centre- to-centre. Structural steel of ISMB 100 section is used. Total depth of 100 mm, flange width of 75 mm, flange thickness of
-
mm and web thickness of 4 mm. Concrete is modelled as 3D deformable solid extrusion type element with square cross section 230mm x 230 mm and length 1000mm. Main reinforcement and tie bars are modelled as 3D wire planar element. Structural steel is also modelled as 3D deformable solid extrusion type homogeneous element with a depth of 1000mm. Fig.1 shows the cross sectional details of the specimen.
out using static general step. Analysis is conducted as load controlled. At the top face of column load is specified as uniform pressure. After the analysis is completed reaction force and displacement values were obtained. The obtained results from numerical analysis were compared with experimental results. Table 3 shows the comparison of experimental and numerical results.
Table 3 : Comparison of experimental and FEA results
Column ID
Deformation (mm)
% error
Experimental
FEA
FEC/ISMB 1
4
4.07
1.75
FEC/ISMB 2
5
5.3
6
-
-
PARAMETRIC STUDY
-
Specimens
Fig.1 Cross section details of the specimen
-
Material modelling
In finite element modelling, defining property is an important step. Defining the property of material and section is included in this module. Defining properties of the section involves assigning thickness. CES composite column is made up of concrete and structural steel. Structural steel section of yield strength 250MPa and reinforcement bars are of high yield strength deformed bars with yield strength 500MPa was used. While modelling concrete, concrete damage plasticity model which is capable of predicting compressive and tensile failure was incorporated in property module. Different properties of the materials used in modelling are as given in Table 1. Tensile properties of steel are shown in Table 2. The reinforcement- concrete interface is provided as embedded region.
Sl No.
Material
Density (N/mm3)
Youngs Modulus (MPa)
Poissons Ratio
1
Concrete (26 MPa)
2.4379
25495
0.15
Concrete (42 MPa)
32403
2
Bar 12 mm dia
7.6982
200000
0.3
Bar 8 mm dia
3
ISMB 100
Sl No.
Material
Density (N/mm3)
Youngs Modulus (MPa)
Poissons Ratio
1
Concrete (26 MPa)
2.4379
25495
0.15
Concrete (42 MPa)
32403
2
/td>
Bar 12 mm dia
7.6982
200000
0.3
Bar 8 mm dia
3
ISMB 100
Table 1: Input Material Properties [1]
For conducting the study under combined axial and lateral cyclic loading, 8 specimens are modelled with different design parameters. Analysis is conducted to study the influence of steel fibers and axial load on the seismic performance of CES column. All the specimens have same stirrup ratio of 0.65. For studying the effectiveness of steel fibers 0.5%, 1% and 1.5% volume fraction of steel fibers are added and the results are compared with the specimen without steel fibers. Aspect ratio of steel fibers used is 50. Table 4 shows the details of specimens.
Column ID
Concrete Compressive Strength
Percentage of steel fibers
CES1-1-0
26 MPa
0
CES1-1-0.5
0.5
CES1-1-1
1
CES1-1-1.5
1.5
CES2-1-0
42 MPa
0
CES2-1-0.5
0.5
CES2-1-1
1
CES2-1-1.5
1.5
Column ID
Concrete Compressive Strength
Percentage of steel fibers
CES1-1-0
26 MPa
0
CES1-1-0.5
0.5
CES1-1-1
1
CES1-1-1.5
1.5
CES2-1-0
42 MPa
0
CES2-1-0.5
0.5
CES2-1-1
1
CES2-1-1.5
1.5
Table 4: Design Parameters of the specimen
-
Analysis
Material
Yield Stress (MPa)
Ultimate Stress (MPa)
Yield Strain
Ultimate Strain
Bar 8 mm
500
635
0.00317
0.14559
Bar 12 mm
500
633
0.003210
0.13554
ISMB 100
250
361
0.003792
0.1288
Material
Yield Stress (MPa)
Ultimate Stress (MPa)
Yield Strain
Ultimate Strain
Bar 8 mm
500
635
0.00317
0.14559
Bar 12 mm
500
633
0.003210
0.13554
ISMB 100
250
361
0.003792
0.1288
Table 2: Tensile Properties of Steel [1]
-
Lateral Cyclic Loading
Several protocols are proposed for structural components and systems for their cyclic testing. Several cyclic testing of reinforced concrete subassemblies have been conducted by many researchers using different loading protocols. For testing reinforced concrete structures a formal cyclic loading protocol has been developed by the researchers in New Zealand. This protocol is based on the yield displacement. The yield displacement is taken as the displacement corresponding to 75% of the theoretical strength. Fig 2 shows the loading history of New Zealand Protocol [11]. As per the protocol the first three cycles are load controlled. Lateral force equals to 50% of the theoretical force are imposed during the first two cycles of loading. First yield displacement is determined in the third cycle. After that the subsequent cycles are displacement
Load module is used for assigning boundary conditions. At the bottom of column a reference point is defined and all the degrees of freedom are arrested. At the top freedom of rotation is released and also axial translation is set free. All components are meshed properly. Approximate size of global seeds are chosen in such a way that the model gives accurate results with reasonable time. Concrete is assigned as C3D8R element. Rebars are assigned as T3D2 element and structural steel section as S4R element. Nonlinear analysis have been carried
controlled.
Fig 2: New Zealand Protocol [11]
-
Analysis and Results
In ABAQUS, two steps are defined as static general. Maximum design plastic resistance of composite column in axial compression is calculated as per Eurocode 4 and is applied in step 1. Step 2 is defined for lateral cyclic loading. Both steps are defined for nonlinear behavior. Lateral loading is applied on the top face of column along the lateral direction. For defining the lateral cyclic loading, in load module amplitude is created as tabular type and time-amplitude data is given as input. Time period is also given in step 2 as per the time-amplitude data.
Hysteresis curve is an important basis for studying the seismic performance. All the specimens as mentioned in above Table 4 are analysed with constant axial load of 10% of the calculated capacity and lateral cyclic loading. For obtaining the hysteresis curve, reaction force is obtained from the bottom reference point and displacement is taken from the top face. Fig 3 (a-d) shows the load-deformation curve for specimens with concrete compressive strength of 26MPa and percentage of steel fiber varying from 0% to 1.5%. Fig 4 (a-d) shows load- deformation curve with concrete compressive strength of 42MPa and varying the steel fiber content. With the increase in number of cycles the lateral load also increases and reaches a peak value. With further increase with the cycles the load decreases and the lateral deformation continues to increase. With the addition of steel fiber the specimen shows increase in lateral load and deformation.
Fig 3: Load-deformation curve with concrete strength 26MPa and steel fiber content (a) 0% (b) 0.5% (c) 1% and (d) 1.5%
Fig 4: Load-deformation curve with concrete strength 42MPa and steel fiber content (a) 0% (b) 0.5% (c) 1% and (d) 1.5%
-
Effect of Steel Fibers
For studying the influence of steel fiber, the peak load of specimens with different percentages of steel fibers were compared with that without steel fibers. Peak load is taken as the average of positive and negative peak loads. The comparison is shown in fig 5.
Fig 5 : Comparison of peak load with 0%, 0.5%, 1% and 1.5% of steel fibers
With the addition of steel fibers the load and displacement are improved. Improvement at each percentage of steel fibers are shown in table 5.
Table 5: Percentage increase in peak load
Concrete Strength
0% SF
0.5% SF
1% SF
1.5% SF
26MPa
—
13.68
18.43
22.19
42MPa
—
9.02
13.45
17.14
-
Effect of Axial load
Aim of this parametric study is to investigate the changes in hysteresis response due to the variation in axial loading. For this particular study axial load in is varied from 0% of the design capacity of the specimen to 100% of the design capacity. In particular, the axial load variation is 0%, 5%, 10%, 15%, 25%, 50%, 75% and 100%. The variations are plotted as shown in figure 7. With the increase in axial loading, the stiffness and peak load of the specimen increases. After reaching the peak load strength and stiffness of the specimen gradually degrades.
Fig 7: Comparison of peak load under different axial loading
-
Ductility Factor
Ductility factor, µ is defined as the ratio of ultimate displacement to the yield displacement. It is commonly used to quantitatively describe the ductility of the specimen. Ductility is used for the determination of deformation capacity and seismic behavior of structural members [12]. Ductility factor is given by
µ=u/y (1)
u is the ultimate displacement corresponding to the peak load [13]
y is defined as the yield displacement which corresponds to 75% of the ultimate load [13]
Table 6 shows the ductility factor for different specimens. The results indicate that the ductility factor of columns with steel fibers is greater than 3. The ductility factor greater than 3 indicates that the columns have adequate ductility and seismic behavior [12]. For the specimens with concrete compressive strength of 26MPa and without any steel fiber the ductility factor value comes to be 1.73 which is less than 3. With the addition of steel fiber the ductility factor increases and reaches to 4.35 with the addition of 1.5% of steel fibers. For specimens with concrete compressive strength of 42MPa the specimen without any steel fibers shows a value of 5.2. With the addition of 0.5% steel fibers the ductility factor increases to 5.48 and
after that with further addition of steel fiber the ductility factor decreases but still the value is greater than 3.
Table 6: Ductility factor of specimens
Column ID
Ductility Factor
CES1-1-0
1.73
CES1-1-0.5
3.88
CES1-1-1
3.98
CES1-1-1.5
4.35
CES2-1-0
5.20
CES2-1-0.5
5.48
CES2-1-1
3.09
CES2-1-1.5
3.95
-
-
CONCLUSIONS
Finite Element Analysis of CES columns are conducted using ABAQUS software. Results obtained under axial compression loading was compared with that of experimental results [1]. Numerical model shows a good agreement with the experimental results and thus the model is validated. On the validated model, analysis is conducted under combined axial and lateral cyclic loading. Parametric study is done to investigate the effects of steel fiber content and axial loading on the seismic performance of CES column. Ductility factor of specimens also calculated. From the analysis the following conclusions are obtained.
-
For improving the hysteresis performance of CES columns steel fiber of 0.5%, 1% and 1.5% were added. Specimens showed better performance with the addition of steel fiber
-
Percentage improvement in peak load for the specimen with concrete compressive strength of 26MPa and 1.5% addition of steel fiber is 22.19%.
-
Percentage improvement in peak load for the specimen with concrete compressive strength of 42MPa and 1.5% addition of steel fiber is 17.14%.
-
By increasing the axial load on the column the lateral peak load of the column is also increased.
-
All the specimens with steel fiber shows a ductility factor value greater than 3 which shows specimen have adequate ductility and seismic performance.
REFERENCES
-
Kartheek, Thunga, and T. Venkat Das. "3D modelling and analysis of encased steel-concrete composite column using ABAQUS." Materials Today: Proceedings (2020).
-
Chen, Cheng-Chih, and Nan-Jiao Lin. "Analytical model for predicting axial capacity and behavior of concrete encased steel composite stub columns." Journal of Constructional Steel Research 62.5 (2006): 424- 433.
-
Ellobody, Ehab, and Ben Young. "Investigation of concrete encased steel composite columns at elevated temperatures." Thin-Walled Structures 48.8 (2010): 597-608.
-
Mander, John B., Michael JN Priestley, and R. Park. "Theoretical stress- strain model for confined concrete." Journal of structural engineering 114.8 (1988): 1804-1826.
-
Ng, Tian Sing, and Trevor Htut. "Structural application of steel fiber reinforced concrete with and without conventional reinforcement." Australian Structural Engineering Conference: ASEC 2018. Engineers Australia, 2018.
-
Karadelis, John N., and Lei Zhang. "On the discrete numerical simulation of steel fiber reinforced concrete (STEEL FIBERRC)." Journal of Civil Engineering Research 5.6 (2015): 151-157.
-
Hamoda, Ahmed, Mohamed Emara, and Walid Mansour. "Behavior of steel I-beam embedded in normal and steel fiber reinforced concrete incorporating demountable bolted connectors." Composites Part B: Engineering 174 (2019): 106996.
-
Chao, Shih-Ho, Antoine E. Naaman, and Gustavo J. Parra-Montesinos. "Bond behavior of reinforcing bars in tensile strain-hardening fiber- reinforced cement composites." ACI Structural Journal 106.6 (2009): 897.
-
Wu, Kai, Feng Chen, Chuyang Chen, Huiming Zheng, and Jianan Xu. "Analysis of the Bearing and Damage Mechanism in SteelSteel fiber Reinforced Concrete-Composite Member." Journal of Materials in Civil Engineering 32, no. 10 (2020): 04020274.
-
Shende, A. M., A. M. Pande, and M. Gulfam Pathan. "Experimental study on steel fiber reinforced concrete for M-40 grade." International Refereed Journal of Engineering and Science 1, no. 1 (2012): 043-048.
-
Filiatrault, Andre, Assawin Wanitkorkul, and Michalakis C. Constantinou. Development and appraisal of a numerical cyclic loading protocol for quantifying building system performance. No. 13. MCEER, 2008.
-
Chen, Caihua, Cuikun Wang, and Huizhong Sun. "Experimental study on seismic behavior of full encased steel-concrete composite columns." Journal of structural engineering 140.6 (2014): 04014024.
-
Park, Robert. "Evaluation of ductility of structures and structural assemblages from laboratory testing." Bulletin of the new Zealand society for earthquake engineering 22.3 (1989): 155-166.
-
Eurocode 4, Design of Composite Steel and Concrete Structures (BS EN 1994-1-1), European Committee for Standardization, Brussels, Belgium, 2004.
-
IS:456, Plain and Reinforced Concrete – Code and Practice, Bureau of Indian Standards, New Delhi, 2000.