
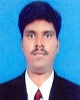
- Open Access
- Authors : J Suresh Babu , Dr. S. Chakradharagoud , Dr. V. S. S. Murthy
- Paper ID : IJERTV10IS030292
- Volume & Issue : Volume 10, Issue 03 (March 2021)
- Published (First Online): 12-04-2021
- ISSN (Online) : 2278-0181
- Publisher Name : IJERT
- License:
This work is licensed under a Creative Commons Attribution 4.0 International License
Structural Analysis of Flax Fiber Reinforced Epoxy Composites with Micro and Nano Tio2 Filler Addition
J. Sureshbabu1, Dr. S. Chakradharagoud2 Dr. V. S. S. Murthy3
1 Scholar, Department of Mechanical Engineering, Shri Jagdishprasad Jhabarmal Tibrewala University, Jhunjhunu, Rajasthan.
2 Professor, Department of Mechanical Engineering, Shri Jagdishprasad Jhabarmal Tibrewala University, Jhunjhunu, Rajasthan.
3 Professor, Department of Mechanical Engineering, K. S. R. M. College of Engineering, Kadapa, Andhra Pradesh.
Abstract:- At present the mechanical reaction to outer applied heaps of another flax fiber supported periodontics post is reenacted by nite element (FE) analysis of a bi-dimensional model. The new post has a necessary shape with a smooth end to satisfactorily t the root cavity, and to dodge edges that could go about as undesired pressure concentrates. Mechanical information got by three twisting tests on certain models manufactured in the lab are introduced and utilized in the FE model. Under different stacking conditions, the subsequent pressure component elds are consequently contrasted and those got on account of two business periodontics posts (for example a cast metal post and a carbon fiber post) and with the reaction of a characteristic material. The gold cast post-and-center creates the best pressure focus at the post-dentin interface. Then again, fiber-supported composite posts do introduce very high anxieties in the cervical locale because of their exibility and furthermore to the presence of a less hardened center material. The flax fiber composite shows the most reduced pinnacle stresses inside the root since its firmness is a lot of like dentin. Aside from the power focus at the cervical edge, the flax fiber composite post actuates a pressure eld very like that of the common material. The warm conduct of fiber composites supported with short flax filaments was concentrated by methods for thermo gravimeter and dynamic mechanical warm investigation. The warm solidness of the composites was discovered to be higher than that of flax fiber and the PS lattice. Catchphrases: Mechanical Reaction, Support, limited component examination and Warm conduct.
Key words: Mechanical Response, Reinforcement, finite element analysis & Thermal behavior
INTRODUCTION
The utilization of fiber materials in the creation of fiber arranged composites is exceptionally benecial as these materials improve the sturdiness and strength of plastics. More over these materials are extremely modest, Biodegradable and exible. Dissimilar to glass fiber, they decrease the wear of hardware. They are of low thickness, and produce no well-being risks [1-2]. Thermal analysis is a regular technique in understanding the design property Relationships and warm security of composite materials [3-4]. Warm investigation can be utilized to decide the dampness substance and unstable component present in composites. Since the dampness substance and unpredictable components have weakening impact on the properties of the composite these investigations are vital [5-6]. Characteristic fiber composites (bio composites) are principally made mix out of cellulose, hemi cellulose, and lignin, which can be gotten not just from leaf (e.g., sisal), best (e.g., flax and hemp), seed (e.g., cotton), and organic product (e.g., coir), yet in addition from different sources, for example, chicken quills and these regular fibers offers number of benefits over existing engineered fibers (e.g., carbon and agamid fibers) [7-8]. From an ecological point of view, characteristic fibers are biodegradable and are carbon positive since they assimilate more carbon dioxide than they produce. Regular fibers additionally have various benefits as far as explicit material properties as demonstrated in Table 1. The best and leaf fibers loan mechanical help to the plants stem or leaf, individually; models for these sorts of fibers incorporate flax, hemp, jute, and ramie [9-12].
The surfaces of regular fibers are lopsided and unpleasant which gives great attachment to the network in a composite material [13]. The particular mechanical properties of characteristic fibers have high importance for their use in composites. In characteristic fiber-supported composites, fiber goes about as support and shows high rigidity and firmness [14-15]. The mechanical properties of support (fibers) have direct connection with the elasticity and firmness of the composite. The determination of appropriate building up fibers follows certain measures, for example, warm security, fiber-framework grip, long time conduct, extension at disappointment, and additionally cost and handling costs. Most of bio composites by and by utilized is in the car, development, furniture, and bundling enterprises. The strategies used to produce bio composites depend generally on existing procedures for preparing plastics or composite materials. These incorporate press forming, hand lay-up, fiber winding, pultrusion, expulsion, infusion shaping, pressure shaping, pitch move embellishment, and sheet forming compound technique [16-19].
Composite materials utilized for primary purposes frequently have low densities, bringing about high firmness to weight and high solidarity to weight proportions when contrasted with conventional designing materials. Likewise, the high exhaustion solidarity to weight proportion and weariness harm resilience of numerous composites additionally makes an appealing choice. Composite mechanical properties are unequivocally affected by the mechanical properties, dispersion of the fibers, and lattice, and well as the proficiency of stress move between these two components [20]. Polymer composites are generally utilized in many significant designing primary applications. The grid fills for chiefly two significant needs; in particular, it bonds the sinewy stage, and under an applied power, it disfigures and appropriates the pressure to the high-modulus stringy constituent. A definitive property of the composites rely upon numerous properties like constituents, size, and state of the individual supporting fibres or particles, underlying plan and dispersion, relative measure of every constituent, and the interface among framework and support.
The current work is centred around examining the after-effects of the fiber composite examples with various mechanical properties utilizing ANSYS programming by playing out a FEM examination and contrasting the outcomes and the mechanical outcomes and assessing the best outcomes..
-
Finite Element Model and Analysis
Fiber composites comprise of fiber and grid stages, and the mechanical conduct of the composites is highly dictated by the fiber and framework properties. Microstructures, for example, fiber shape, fiber cluster, and volume part of strands are additionally more significant in deciding the mechanical properties [10]. Micromechanical models have been utilized to anticipate the properties beginning from the inherent properties and their constituents [11], and these models show that the fiber strength isn't as a rule totally utilized because of helpless fiber grid interfacial attachment and fiber length.
The material is displayed utilizing certain presumptions and broke down for mechanical properties with limited component technique programming (ANSYS). The composite material is allotted as unidirectional composite by accepting a few properties that are given beneath.
A portion of the presumptions utilized for the examination work have been accumulated by the writing
-
Fibers are not permeable.
-
The material property for evey one of the constituents are credited as isotropic material for the two volumes.
-
Fibers are uniform in properties with distance across.
-
Interphone holding is kept up among strands and network.
-
Perfect connection among fiber and framework and no slippage.
-
Fibers are orchestrated in unidirectional way and entirely adjusted.
-
Composite material is liberated from voids.
The interface among fiber and framework is additionally an interface that serves to move remotely applied burdens to the support through shear worries about the interface. Controlling the strength of the interface is basic. Obviously, great holding is fundamental if stresses are to be satisfactorily moved to the support and subsequently give a genuine building up work. Another significant mechanical property is sturdiness or the capacity of a designing material to oppose the spread of breaks. This happens in composites by ethicalness of their heterogeneous design. It is significant that under particular conditions interfacial bond separates in order to permit different hardening instruments to get usable. These components incorporate break blunting as proposed by and different energy retention cycles, for example, the frictional sliding of deboned fiber pieces inside the network, fiber crack, and the production of new break surfaces.
The limited component technique (FEM) was utilized to display the conduct of a material based on micromechanical level. The model was thought to be an isotropic material with a rectangular segment of a pillar. This segment is then displayed in definite utilizing volume components to address the composite. Every component will have an isotropic property and will be situated relating to the strands, and the lattice locales are coarsely coincided (united arrangement).
The model is treated as a straight isotropic issue. The FEA model is comprised of SOLID 95 components, utilized for fiber- framework structure as appeared. The model incorporated the fiber, grid, and fiber-framework interface. Nine filaments were demonstrated to the encompassing grid. The filaments, with encompassing framework were chosen for pressure investigation in this model. These districts were displayed utilizing the coarse cross section (merged arrangement) as demonstrated in Figure and the heap applied at the top edge of the model.
Fig 1: Composite material with fibre and matrix Fig 2: Fibre and Matrix region
-
-
FINITE ELEMENT METHOD(FEM) ANALYSIS
In this FEM investigation in two kinds underlying and warm examination. In underlying examination we discovered mechanical properties like elasticity, yield strength, absolute distortion, and so on In warm examination we have performed and discover the temperature variety, heat transition, convection and so on Limited Element Analysis or FEA is the re-enactment of an actual marvel utilizing a mathematical mathematic procedure alluded to as the Finite Element Method, or FEM. This interaction is at the centre of mechanical designing, just as an assortment of different controls. It likewise is one of the key standards utilized in the improvement of reproduction programming. Specialists can utilize these FEM to lessen the quantity of actual models and run virtual examinations to streamline their plans. Complex math is needed to comprehend the actual marvels that happen surrounding us. These incorporate things like liquid elements, wave spread, and warm examination.
Investigating the vast majority of these wonders should be possible utilizing fractional differential conditions, yet in complex circumstances where numerous exceptionally factor conditions are required; Finite Element Analysis is the main numerical procedure.
3.1 Structural analysis
A static structural analysis determines the displacements, stresses, strains, and forces in structures or elements caused by loads that do not induce significant inertia and damping effects. Steady loading and response conditions are assumed; that is, the loads and the structures response are assumed to vary slowly with respect to time. A static structural load can be performed using the ANSYS, Same, or ABAQUS solver. The types of loading that can be applied in a static analysis include:
-
Externally applied forces and pressures
-
Steady-state inertial forces (such as gravity or rotational velocity)
-
Imposed (nonzero) displacements
-
Temperatures (for thermal strain)
Here we are going to find out the tensile stress, equivalent stress, total deformation, etc.
I. Tensile stress
Tensile stress () is the resistance of an object to a force that could tear it apart. It is calculated with the highest tension endured by the object in question without tearing, and is measured in Newtons/mm2, but was originally denoted in tons/incp. Tensile stress can be defined as the magnitude of force applied along an elastic rod, which is divided by the cross-sectional area of the rod in a direction perpendicular to the applied force. Tensile means the material is under tension and that there are forces acting on it trying to stretch the material. Tensile stress measures the strength of a material; therefore, it refers to a force that attempts to pull apart or stretch a material. Many mechanical properties of a material can be determined by a tensile test.
Fig 3:Tensile Test Specimen with Flax ad epoxy matrix reinforcement
Fig 4:Tensile Test Specimen with Flax+TiO2(micro) and epoxy matrix reinforcement
Fig 5:Tensile Test Specimen with Flax+TiO2(nano) ad epoxy matrix reinforcement
Fig 6:Tensile Test Specimen results for Flax+TiO2(nano)+TiO2(micro) ad epoxy matrix reinforcement
Table 1:Tensile Test Specimen results for Flax ad epoxy matrix reinforcement
S.no
Reinforcement
Matrix
Load (KN)
Ultimate Tensile strength (MPa)
1.
Flax (20%)
Epoxy (80%)
11
89.7
2.
Flax (30%)
Epoxy(70%)
11
90.2
3.
Flax (40%)
Epoxy(60%)
11
91.3
4.
Flax (50%)
Epoxy(50%)
11
91.8
5.
Flax (60%)
Epoxy(40%)
11
92.01
Table 2:Tensile Test Specimen results for Flax+TiO2(micro) ad epoxy matrix reinforcement
S.no
Reinforcement
Matrix
Load (KN)
Ultimate Tensile strength (MPa)
1.
Flax +TiO2(micro)(20%)
Epoxy (80%)
11
88.4
2.
Flax +TiO2 (micro)(30%)
Epoxy(70%)
11
89.1
3.
Flax +TiO2 (micro)(40%)
Epoxy(60%)
11
89.97
4.
Flax +TiO2 (micro)(50%)
Epoxy(50%)
11
90.9
<>5. Flax +TiO2 (micro)(60%)
Epoxy(40%)
11
91.67
Table 3:Tensile Test Specimen results for Flax+TiO2(nano) ad epoxy matrix reinforcement
S.no
Reinforcement
Matrix
Load (KN)
Ultimate Tensile strength (MPa)
1.
Flax +TiO2(Nano)(20%)
Epoxy (80%)
11
92.4
2.
Flax +TiO2 (Nano)(30%)
Epoxy(70%)
11
93.5
3.
Flax +TiO2 (Nano)(40%)
Epoxy(60%)
11
94.2
4.
Flax +TiO2 (Nano)(50%)
Epoxy(50%)
11
95.6
5.
Flax +TiO2 (Nano)(60%)
Epoxy(40%)
11
96.1
Table 4:Tensile Test Specimen results for Flax+TiO2(nano)+TiO2(micro) ad epoxy matrix reinforcement
S.no
Reinforcement
Matrix
Load (KN)
Ultimate Tensile strength (MPa)
1.
Flax + TiO2 (micro)+TiO2(Nano)(20%)
Epoxy (80%)
11
96.2
2.
Flax + TiO2 (micro)+TiO2 (Nano)(30%)
Epoxy(70%)
11
96.9
3.
Flax + TiO2 (micro)+TiO2 (Nano)(40%)
Epoxy(60%)
11
97.6
4.
Flax + TiO2 (micro)+TiO2 (Nano)(50%)
Epoxy(50%)
11
98.75
5.
Flax + TiO2 (micro)+TiO2 (Nano)(60%)
Epoxy(40%)
11
99.51
Ultimate Tensile strength (MPa) Flax
Ultimate Tensile strength (MPa) Flax +
92.6
TiO2(Micro)
92.4
94.5
92.2
94
92
93.5
91.8
93
91.6
91.4
92.5
91.2
92
91
91.5
11.1 11.2 11.3 11.4 11.5
11.6
11.55 11.6 11.65 11.7 11.75 11.8
Load(N)
Load(N)
Ultimate tensile strength
Ultimate tensile strength
Ultimate tensile strength
Ultimate tensile strength
Ultimate tensile strength
Ultimate tensile strength
Ultimate tensile strength
Ultimate tensile strength
Graph 1. Tensile strength variation w.r.t matrix reinforcement Graph 2. Tensile strength variation w.r.t matrix (Flax + Epoxy) reinforcement(Flax +TiO2(micro) + Epoxy)
Ultimate Tensile strength (MPa) Flax + TiO2(Nano)
Ultimate Tensile strength (MPa) Flax + TiO2(Nano)+ TiO2(Micro)
94.5
94.5
94
94
93.5
93.5
93
93
92.5
92.5
92
92
91.5
91.5
11.55 11.6 11.65 11.7 11.75
11.8
11.55 11.6 11.65 11.7 11.75 11.8
Load(N)
Load(N)
Graph 3. Tensile strength variation w.r.t matrix reinforcement Graph 4. Tensile strength variation w.r.t matrix
(Flax +TiO2(Nano) + Epoxy) reinforcement(Flax + TiO2(micro) +TiO2(Nano) + Epoxy)
From the above graph results we can see that the maximum tensile strength is obtained for Flax + TiO2 (micro) + TiO2(Nano) Epoxy Resin (LY-556) along with Hardener (HY-951) matrix composite. Tensile stress may also be known as normal stress or tension. When an applied stress is less than the materials tensile strength, the material returns completely or partially to its original shape and size. As the stress approaches the value of the tensile strength, the material has already begun to flow plastically and rapidly forms a constricted region called a neck, which is the point at which it fractures.
-
Equivalent stress
Equivalent stress is used when there is a multiracial stress state with multiple stress elements acting at the same time in the structure. In such case we can use selected criterion to transform the whole stress tensor into a single equivalent element that can be treated as a tensile stress and thus compared with materials strength easily. Various criteria may be utilized but among them there is one with incomparably larger popularity than the others – von Misses yield criterion or otherwise maximum distortion energy criterion. Its commonly used in engineering as for example Finite Element Analysis programs use it as a default stress measure. On Misses stress is a value used to determine if a given material will yield or fracture. It is mostly used for ductile materials, such as metals. The von Misses yield criterion states that if the von misses stress of a material under load is equal or greater than the yield limit of the same material under simple tension then the material will yield.
Fig 7:Equvalent Tensile Test Specimen with Flax ad epoxy matrix reinforcement
Fig 8:Equvalent Tensile Test Specimen with Flax+TiO2(micro) and epoxy matrix reinforcement
Fig 9:Equivalent Tensile Test Specimen with Flax+TiO2(nano) ad epoxy matrix reinforcement
Fig 10:Tensile Test Specimen results for Flax+TiO2(nano)+TiO2(micro) ad epoxy matrix reinforcement Table 5:Equivalent Tensile Test Specimen results for Flax ad epoxy matrix reinforcement
S.no
Reinforcement
Matrix
Load (KN)
Equivalent Tensile strength (MPa)
1.
Flax (20%)
Epoxy (80%)
11
143
2.
Flax (30%)
Epoxy(70%)
11
116
3.
Flax (40%)
Epoxy(60%)
11
95.2
4.
Flax (50%)
Epoxy(50%)
11
91.8
5.
Flax (60%)
Epoxy(40%)
11
92.01
Table 6:Equivalent Tensile Test Specimen results for Flax+TiO2(micro) ad epoxy matrix reinforcement
S.no
Reinforcement
Matrix
Load (KN)
Equivalent Tensile strength (MPa)
1.
Flax +TiO2(micro)(20%)
Epoxy (80%)
11
141
2.
Flax +TiO2 (micro)(30%)
Epoxy(70%)
11
120
3.
Flax +TiO2 (micro)(40%)
Epoxy(60%)
11
99.6
4.
Flax +TiO2 (micro)(50%)
Epoxy(50%)
11
93.2
5.
Flax +TiO2 (micro)(60%)
Epoxy(40%)
11
92.1
Table 7:Equivalent Tensile Test Specimen results for Flax+TiO2(nano) ad epoxy matrix reinforcement
S.no
Reinforcement
Matrix
Load (KN)
Equivalent Tensile strength (MPa)
1.
Flax +TiO2(Nano)(20%)
Epoxy (80%)
11
146
2.
Flax +TiO2 (Nano)(30%)
Epoxy(70%)
11
121.1
3.
Flax +TiO2 (Nano)(40%)
Epoxy(60%)
11
96.2
4.
Flax +TiO2 (Nano)(50%)
Epoxy(50%)
11
92.3
5.
Flax +TiO2 (Nano)(60%)
Epoxy(40%)
11
93.6
Table 8:Equivalent Tensile Test Specimen results for Flax+TiO2(nano)+TiO2(micro) ad epoxy matrix reinforcement
S.no
Reinforcement
Matrix
Load (KN)
Equivalent Tensile strength (MPa)
1.
Flax + TiO2 (micro)+TiO2(Nano)(20%)
Epoxy (80%)
11
147
2.
Flax + TiO2 (micro)+TiO2 (Nano)(30%)
Epoxy(70%)
11
126
3.
Flax + TiO2 (micro)+TiO2 (Nano)(40%)
Epoxy(60%)
11
112
4.
Flax + TiO2 (micro)+TiO2 (Nano)(50%)
Epoxy(50%)
11
103.5
5.
Flax + TiO2 (micro)+TiO2 (Nano)(60%)
Epoxy(40%)
11
99.5
92.6
equivalent tensile strength
equivalent tensile strength
92.4
92.2
92
91.8
91.6
91.4
91.2
91
Equivalent Tensile strength (MPa) Flax
11.1 11.2 11.3 11.4 11.5 11.6
Load(N)
Equivalent Tensile strength (MPa) Flax
+ TiO2(Micro)
94.5
equivalent tensile strength
equivalent tensile strength
94
93.5
93
92.5
92
91.5
11.55 11.6 11.65 11.7 11.75 11.8
Load(N)
equivalent tensile strength
equivalent tensile strength
equivalent tensile strength
equivalent tensile strength
Graph 1. Equivalent strength variation w.r.t matrix reinforcement Graph 2. Equivalent Tensile strength variation w.r.t (Flax + Epoxy) matrix reinforcement (Flax +TiO2 (micro) + Epoxy)
Equivalent Tensile strength (MPa) Flax + TiO2(Nano)
Equivalent Tensile strength (MPa) Flax
+ TiO2(Nano)+ TiO2(Micro)
94.5
94.5
94
94
93.5
93.5
93
93
92.5
92.5
92
92
91.5
91.5
11.55
11.6
11.65
11.7
11.75
11.8
11.55
11.6
11.65
11.7
11.75
11.8
Load(N)
Load(N)
Graph 3. Equivalent strength variation w.r.t matrix reinforcement Graph 4. Equivalent Tensile strength variation w.r.t matrix (Flax +TiO2 (Nano) + Epoxy) reinforcement (Flax + TiO2 (micro) +TiO2(Nano) + Epoxy)
As far as possible talked about before depend on basic pressure or uniaxial stress tests. The most extreme bending energy hypothesis, nonetheless, began when it was seen that materials, particularly pliable ones, acted contrastingly when a non- basic pressure or non-uniaxial stress was applied, showing opposition esteems that are a lot bigger than the ones saw during basic strain tests. A hypothesis including the full pressure tensor was thusly evolved. From the above outcomes we can see that the same rigidity is acquired at Flax + TiO2 (micro)+TiO2 (Nano)(20%) and Epoxy (80%) organization.
-
-
Concluding remarks
-
The elasticity of the multitude of six examples was assessed and test consequences of all examples are appeared in table. It was discovered that example 1 is having most minimal extreme rigidity when contrasted with outstanding examples, at that point after there was a tremendous expansion in extreme elasticity for examples 2 and 3. At that point for example 3 and 4the extreme rigidity is somewhat expanded when contrasted with example 1 to 2 .It has been seen that out of every one of the four examples, for examples 1,2 and 3 which is having syntheses have shown unusual outcomes which is having less elasticity, which are pertinent for little family and staple things. Further, it is seen that example 4 is having higher youthful modulus when contrasted with residual examples.
-
In the current work, the measurements for the four examples are taken according to the ASTM principles. The hardness test for the example examples are completed on Rockwell hardness arrangement. In this investigation we have considered ball 1/16 as the indenter. From table example 1 is having most reduced hardness when contrasted with residual examples. There is a slow increment from example 1 to 4. Higher the hardness number lower is an ideal opportunity to extinguish it. Here in this test it is seen that example 4 is having higher hardness and example 1 is having lower hardness in C-scale separately.
-
The flexural strength of the multitude of four examples was assessed and test consequences of all examples are appeared in table. It was discovered that example 1 is having least flexural strength when contrasted with outstanding examples, at that point after there was a gigantic expansion in flexural strength for examples 2 and 3. At that point for example 3 and 4the flexural strength is somewhat expanded when contrasted with example 1 to 2 .It has been seen that out of each of the four examples, for examples 1,2 and 3 which is having pieces have shown unusual outcomes which is having less flexural strength, which are relevant for little family and staple things.
-
In the current work, Fabrication of another class epoxy based composites supported with short flax normal filaments. Evaluated the mechanical properties, for example, flexural strength, sway strength, elasticity and miniature hardness of the got examples.
-
According to the malleable test explores the example 1 have most extreme pressure strain bend and example 4 has least pressure strain bend. The pressure test is most extreme for the example 1 and least for the example. The hardness number is greatest for the jute symmetrical fiber. When we contrasted with the two outcomes, it is plainly seen that the logical outcomes are greatly improved due to limited lattice of example.
-
As of the plain estimations of Tensile strength, Hardness, Flexural strength are expanded up to 750 after that we can see from that the qualities are diminished step by step. So that the better mechanical properties at 750 direction from investigation. From over every one of the outcomes we can see that the fiber organization have better elasticity hardness when contrasted with flexural strength
REFERENCES
-
Kokta BV, Kamdem PD, Bushy AD, Daneult C, In: Sediacate B, editor. Polymer composites. Berlin: de Gruyter, 1986.p.251.
-
AkitaK, KaseMJ.PolymSciA-11967; 5:833.
-
Basha, LewinM.JPolymSciPolymChemEd1973; 11:3071.
-
Bash A, Lewin M.J PolymSciPolymEd1973; 11:3097.
-
Bash A, Lewis M. J Polym Sci, Polym Ed1974; 12:2053.
-
Rodrigo H, Bash A, Lewin M. J Polym Sci Polym Chem Ed 1975; 13:1921.
-
Kessira L, Richard A. J Appl Polym Sci1993; 49:1603.
-
Dong S, Gauvin R. Polym Compos1993; 14:414.
-
GuoW, AshidaM.JApplPolymSci1993; 50:1435.
-
Hwang SJ, Gibson RF. Journal of Composite Materials 1992; 26:2585.
-
Joseph K, Thomas S, Pavithran C. J Reinf Plast Compo 1993; 12:139.
-
George J, Bhagavan SS, Thomas S. J Therm Analysis 1996; 47:1121.
-
Manikandan NairKC, Diwan SM, Thomas S.JAppl PolymSci 1996; 60:1483.
-
Nair KCM, Kumar RP, Schit SC, Ramamurthy K, Thomas S. Composites Part A2000;31:1231.
-
Chand N, Verma S, Khazanchi AC. J Mater Sci Lett 1989; 8:1307.
-
Naugen T, Zavarin E, Barall EM. J Macromol Sci, Rev Macromol Chem1981;20.
-
Tang MM, Bacon R. Carbon 1964; 2:211.
-
Chu NJ. J Appl Poly Sci1970; 14:3129.
-
Akay M. Comp Sci Technol1993; 47:419.
-
Finegan IC, Gibson RF. Composite Structure1999; 44:89.