
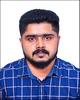
- Open Access
- Authors : Nikesh K, Ms. Shamya Sukumaran M
- Paper ID : IJERTV12IS050162
- Volume & Issue : Volume 12, Issue 05 (May 2023)
- Published (First Online): 06-05-2023
- ISSN (Online) : 2278-0181
- Publisher Name : IJERT
- License:
This work is licensed under a Creative Commons Attribution 4.0 International License
Structural Performance of Steel Encased Composite Multilayered Concrete Beam
Nikesh K
Department Of Civil Engineering
Sree Narayana Guru College Of Engineering And Technology, Kannur, Kerala, India
Ms. Shamya Sukumaran M
Department Of Civil Engineering
Sree Narayana Guru College Of Engineering And Technology, Kannur, Kerala, India
Abstract- In this paper, a composite multilayered concrete beam is analyzed by using ANSYS workbench software. An I section which is partially encased with Ultra-High Performance Concrete [UHPC] and Ultra-Light weight Cement Concrete [ULCC]. These composite materials had been arranged horizontally and vertically along the I Section. Compressive strength of various multilayered composite beams has been compared. Instead of using conventional steel or reinforced concrete members, this form of beams offers greater strength and stiffness.
Keywords:- Ultra-High Performance Concrete [UHPC], Ultra-Light weight Cement Concrete[ULCC]
-
INTRODUCTION
Structural steel which is partially enclosed or fully enclosed with concrete are frequently used in building construction. Instead of using conventional steel or reinforced concrete members, this form of beam offers greater strength and stiffness. The steel section is protected from fire, the compression flange is kept from buckling locally, and the resistance of the beam to lateral-torsional buckling is increased by the concrete encasement. Where standard beams are insufficiently serviceable, composite beams are used. We can somewhat minimize the cross-sectional area of the beams by using composite ones made of greater stiffness materials. They are utilized to make the construction stronger. Large areas can be covered by composite beams without the need for an intermediary structure.
UHPC is a cementitious composite material made up of a high proportion of discontinuous internal fiber reinforcement, a water-to-cementitious materials ratio less than 0.25, and an optimized gradation of granular elements. A brand-new category of concrete called UHPC has recently been created due to its extraordinary strength and endurance. The first UHPC bridge in North America was built in Canada in 1997 as a pedestrian bridge. Compressive strength of UHPC is ten
times greater than that of conventional concrete. Portland cement, fine sand, pulverised quartz, accelerating admixtures, steel fibres, and water are the main ingredients in UHPC. With low densities of less than 1400 kg/m3 and compressive strengths of up to 60 MPa, ultra-lightweight cement composites (ULCC) are the perfect choice for usage in buildings where material weight is important. In structural applications with low weight and permeability requirements, lightweight aggregate concrete (voids are primarily in aggregates) is often used in place of conventional aggregate. Lightweight concrete is especially beneficial for long-span constructions, high-rise structures, and sandwich structures that must have minimal self-weight.
-
OBJECTIVES
-
To study the partially encased composite beams.
-
The effect of different composite materials.
-
The effect of number of layers.
-
The effect of arrangement [Horizontal/ Vertical]
-
-
SCOPE OF THE WORK
The scope of this study is to develop a high strength multi- layered composite beam instead of using steel or conventional reinforced concrete beams.
-
PARAMETRIC STUDY
Multiple aspects were taken into consideration when conducting the investigation on the partially encased multi- layered concrete beam. The beams measure 2000mm in length, 250mm in depth, and 200mm in breadth overall. All examples are constructed using WB 225 hot-rolled wide- flange beams. Vertical and horizontal arrangements had been made with the composite cementitious materials. A single beam included three layers of cementitious material, each with an identical layer thickness.
Code of references: Indian Standard codes IS 808(1989)
-
SUMMARY OF LITERATURE REVIEW
The base journal "Flexural Behaviour of Steel Composite Beams Encased by Engineered Cementitious Composites" was among the literatures studied. Analyses are done on how different composite constructions behave in different environments. Utilising cementitious material will increase the steel member's residual strength. Traditional concrete beams might be considerably heavier than composite beams. In comparison to conventional beams, it can also support higher weight. Large areas can be covered by composite beams without the requirement for any intermediary columns. Many seismic-resistant structures now opt to use concrete- encased steel composite columns. The steel block shear connectors used to join the high-strength steel and precast concrete together create a composite beam with a high bending capacity and stiffness. The flexural strength and ductility of bare steel beams could be greatly improved by the use of ECC and LWC encasements.
-
MODELLING
The modelling is done in the ANSYS Software.
In the case of horizontal arrangement there are almost 8 specimens in which cementitious material layers are arranged. ULU, LUL, UUL, LLU, UUU, ULL, LLL and
LUU. Here U stands for ultra- high performance concrete layer and L stands for ultra-light weight cement concrete layer.
In the case of vertical arrangement there are almost 6 specimens in which cementitious materials are arranged. UU- UU, UL-UL, LU-LU, UL-LU, LU-UL and LL-LL.
Fig 1: Horizontal Arrangement
Fig 2: Vertical Arrangement
A. Material Properties
Two different cementitious material are selected and arranged in different layers in vertical and horizontal manner along the hot rolled wide flange beams WB225.
TABLE 1: MATERIAL PROPERTIES
UHPC
ULCC
STEEL
Density(kg/m3)
2350
1250
7850
Youngs Modulus[MPa]
44500
10620
200000
Poisson Ratio
0.12
0.12
0.3
-
TEST RESULT AND DISCUSSION
Among the 8 specimens of horizontally arranged cementitious material, two models are uniformly layered [UUU, LLL]. The weight and the maximum load carrying capacity of these various specimens are studied.
WEIGHTS[kg]
ULU
266.66
LUL
233.77
LUU
266.66
UUL
266.66
LLU
233.77
UUU
299.55
ULL
233.77
LLL
200.89
TABLE 2: WIGHT OF HORIZONTALLY LAYERED SPECIMENS
When comparing ultra-high performance concrete composite beams with ultra-light weight cement composite beams, the weight increases by 49.11% that of LLL.
TABLE 3: LOAD CARRYING CAPACITY OF HORIZONTALLY LAYERED SPECIMENS
LOAD[kN]
ULU
723.32
LUL
669.12
LUU
720.63
UUL
689.24
LLU
758.01
UUU
696.43
669.92
LLL
704.11
The model with uniform layered ultra-high performance concrete has higher load carrying capacity than model with uniform layered ultra-light weight cement concrete composite beam.
The percentage of increase in load is 13.149
When compared with composite sections, ULL performs effectively with least weight. ULU performs effectively with most weight.
Fig 3: Geometry of ULU
Fig 4: Deformation of ULU
Fig 5: Cross section of ULU model
Among the 6 specimens of vertical layered cementitious material, two models are uniformly layered [UU-UU, LL- LL]. The weight and the maximum load carrying capacity of various specimens are studied.
TABLE 4: WEIGHT OF VERTICALLY LAYERED SPECIEMEN
WEIGHT[kg]
UU-UU
299.55
UL-UL
250.22
LU-LU
250.22
UL-LU
250.22
LU-UL
250.22
LL-LL
200.89
The model UU-UU has most weight compared to other models. The model LL-LL has the least weight compared to other models. The increase in weight of UU-UU is about 49.11% compared to the model LL-LL.
TABLE 5: LOAD CARRYING CAPACITY OF VAERTICALLY LAYERED SPECIMEN
TABLE 7: COMPARISON OF ULU WITH I- SECTION [WB225]
LOAD
(kN)
% INCREASE
IN LOAD
I-SECTION
618.06
0
ULU
723.32
17.03
LOAD [kN]
UU-UU
760.2
UL-UL
717.54
LU-LU
718.03
UL-LU
716.55
LU-UL
717.87
LL-LL
670.69
When ULU is compared with normal I-Section its load carrying capacity increases by 17.03%.
When multi layered composite models are compared with uniform layered composite model UU-UU, the composite model with layer LU-LU has the least amount of percentage decrease in load.
When multi layered composite models are compared with uniform layered composite model LL-LL, the composite model with LU-LU layered has the most % increase in load.
When multi layered composite models compared with each other, LU-LU has the maximum load carrying capacity. UL- LU has the minimum load carrying capacity.
Fig 6: Cross section of LU-LU model
TABLE 6: LOAD CARRYING CAPACITY OF I SECTION
LOAD[kN]
HOT ROLLED I SECTION [WB225]
6.18.06
The hot rolled wide flange beams [WB225] has a load carrying capacity of 618.06KN.
TABLE 8: COMPARISON OF LU-LU WITH I SECTION [WB225]
LOAD (kN)
% INCREASE IN LOAD
I SECTION
618.06
0
LU-LU
718.03
16.17
When vertically layered LU-LU model is compared with I- SECTION its load carrying capacity increases by 16.17%.
TABLE 9: Comparison of ULU & LU-LU
LOAD(kN)
ULU
723.32
LU-LU
718.03
From this table we can find that cementitious material horizontally arranged composite model ULU has higher load carrying capacity than cementitious material vertically arranged composite model LU-LU.
-
CONCLUSION
In the case of multi-layered composite models with horizontal arrangement following conclusions are made,
The model with uniform layered ultra-high performance concrete has higher load carrying capacity than model with uniform layered ultra-light weight cement concrete composite beam. The percentage of increase in load is 13.149. When compared with ultra-light weight cement composite beams with ultra -high performance concrete composite beams, the increase in weight is 49.11% that of LLL. When multilayer models are compared with uniform layered model UUU, ULU has the least percentage decrease in load. When multilayer models are compared with uniform layered model
LLL, ULU has the maximum percentage increase in load. When ULU is compared with normal I-Section its load carrying capacity increases by 17.03%. Hence in the case of multi-layered composite models with horizontal arrangement ULU is the most efficient model in the case load carrying ability.
In the case of multi-layered composite models with vertical arrangement following conclusions are made,
The model UU-UU has most weight compared to other models. The model LL-LL has the least weight compared to other models. The increase in weight of UU-UU is about 49.11% compared to the model LL-LL. When compared with uniform layered composite model UU-UU, the composite model with layer LU-LU has the least amount of percentage decrease in load. When compared with uniform layered composite model LL-LL, the composite model with LU-LU layered has the most amount of percentage increase in load. When compared with composite sections, LU-LU has the maximum load carrying capacity, UL-LU has the minimum load carrying capacity. When vertically layered LU-LU model is compared with I-SECTION its load carrying capacity increases by 16.17%. Hence we conclude that among the various multi-layered composite beam model, LU-LU is most efficient in case of load carrying ability.
Cementitious material horizontally arranged composite model ULU has higher load carrying capacity than cementitious material vertically arranged composite model LU-LU.
REFERENCES
[1] Mohammad M. Rana, C.K. Lee, Safat Al-Deen & Y.X. Zhang Flexural behavior of steel composite beams encased by engineered cementitious composites, School of Engineering and Information Technology, The University of New South Wales, Canberra, ACT 2600, Australia [2018] [2] Gang Xiong, Wei Li, Xuanding Wang, Jiepeng Liu, Yongtao Bai & Y. Frank Chen Flexural behavior of prefabricated high-strength steel-concrete composite beams with steel block connectors Journal of Constructional Steel Research 197 (2022) 107507 [3] Feng-Wei Shi, Chang-Hui Sun, Xiao-Gang Liu, Hao Wang & Liang ZongFlexural behavior of prefabricated composite beam with cast-in-situ UHPC:Experimental and numerical studies Structures 45 (2022) 670684
[4] Qiwu Yan, Zheng Zhang, Jin Yan & Simon Laflamme[2021] Analysis of flexural capacity of a novel straight-side U-shaped steel-encased concrete composite beams. [5] Zhiwen Zhang, Ebrahim M.A. Abbas, Yi Wang Weihua Yan , Xiaoning Cai, Shan Yao, Rong Tang, Dafu Cao, Weigang Lu & Wenjie GeExperimental study on flexural behavior of the BFRC-concrete composite beams. Case Studies in Construction Materials 15 (2021) e00738. [6] Cong-Luyen Nguyen & Chi-King Lee Flexural behaviours of Engineered Cementitious CompositesHigh strength steel composite beams Engineering Structures 249 (2021) 113324. [7] Md. Imran Kabir, C.K. Lee, Mohammad M. Rana & Y.X. Zhang Flexural and bond-slip behaviours of engineered cementitious composites encased steel composite beams Journal of Constructional Steel Research 157 (2019) 229244. [8] Yong Liu, Lanhui Guo, Bing Qu & Sumei Zhang Experimental investigation on the flexural behavior of steel-concrete composite beams with U-shaped steel girders and angle connectors Engineering Structures 131 (2017) 492502. [9] Xinpei Liu, Mark A. Bradford & Abdolreza Ataei Flexural performance of innovative sustainable compsite steel-concrete beams Engineering Structures 130 (2017) 282296. [10] Yang Zou, Kun Yu, Junlin Heng, Zhongya Zhang, Hongbo Peng, Chaolan Wu, Xifeng Wang Feasibility study of new GFRP grid web – concrete composite beam Composite Structures[2022] [11] Zhiyong Wan , Zhi Fang , Linong Liang, Shaohua He, Xiangdong SunStructural performance of steelconcrete composite beams with UHPC overlays under hogging moment[2022] [12] Muhammad N.S. Hadi & Jian Song Yuan Experimental investigation of composite beams reinforced with GFRP I-beam and steel barsConstruction and BuildingMaterials144(2017)462474
[13] Wen-Liang Lu, Wen-Qiang Peng, Li Zhu, Bing Ma & Feng-Lin LiStudy on mechanical behavior of steel-UHPC-NC composite beams under negative bending moment Case Studies in Construction Materials 17 (2022) e01593 [14] Xudong Zhao , Xudong Shao , Junhui Cao , Zongxuan Shao & Rongjun YingLi Experimental studies on shear behavior of steel-UHPC composite beam with hot rolled shape steel Engineering Structures 274 (2022) 115160 [15] Mingze Wu, Shenggang Fan, Hang Zhou, Yunlong Han & Dun LiangExperimental and numerical research on fire resistance of stainless steel- concrete composite beam Journal of Constructional Steel Research 194 (2022) 107342.