
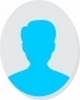
- Open Access
- [post-views]
- Authors : Tirumalrao Mutalikdesai , Kushal Kapali
- Paper ID : IJERTV11IS090039
- Volume & Issue : Volume 11, Issue 09 (September 2022)
- Published (First Online): 11-10-2022
- ISSN (Online) : 2278-0181
- Publisher Name : IJERT
- License:
This work is licensed under a Creative Commons Attribution 4.0 International License
Study and Comparison of Conventional Analysis with Construction Sequence Analysis using ETABS
Tirumalrao Mutalikdesai
Student
Dept. of Civil Engineering, SDMCET, Dharwad, India
Kushal Kapali
Asst. Professor
Dept. of Civil Engineering, SDMCET, Dharwad, India
Abstract Some of the columns in multistorey buildings are designed to be floating columns with transfer girder support. These columns are being analysed in a single step under the presumption that the frame will be subjected to design loads. This is necessary because architectural requirements dictate that certain columns be designed as floating columns. In point of fact, loads are applied at various points during the construction process as the frames of the building are built storey by storey. Within the scope of this study, we have looked at two different instances. Whereas in Case 1 the multistoreyed building with floating columns and transfer girder with 16 stories will be analysed as a whole for the subjected loading, in Case 2 the multistoreyed building with floating columns and transfer girder with 16 stories will be analysed with reference to the construction sequence or staged construction. Both cases involve a multistorey building with floating columns and transfer girders. For the purpose of illustrating the floating column on girders, a comprehensive analysis and comparison of the change in deformations, bending moment, shear force, and axial force will be shown for the transfer girders. The ETABS software is used for both the analysis of the building
KeywordsFloating columns; Construction sequence analysis; Conventional analysis; Staged construction; ETABS
-
INTRODUCTION
The multistorey building frames have been studied for a very long time under the presumption that the entire load is applied to the finished frame structure with all loads acting on the buildingself-weight, superimposed load, live load, and lateral loadsapplied on the finished frame at a specific instant as a single step analysis. But in reality, when the building structure is built storey by storey in a sequential manner, the dead load owing to each structural component and finishing item is imposed separately. When different loads are imposed all at once, a building structure performs quite differently than when the stresses are applied gradually. Construction sequence analysis refers to the process of analysing a structure in accordance with real construction methods (CSA). Construction sequence analysis, commonly referred to as staged construction analysis, is a static non-linear method of analysis that takes the idea of incremental loading into consideration.
One of the topics that has drawn a lot of engineering research efforts and designers' attention is the structural
analysis of multistorey structures. However, there is one area that has received little attention from earlier researchers: the implications of building sequence analysis in a multistorey frame. The structural components are added gradually while a building is constructed, and as a result, their dead load is supported by the portion of the structure that is complete at the time of their installation. As a result, the qualities of the members that have not yet been built have no impact on how displacement and stresses are distributed within a given story. By adding together, the outcomes of the study of each step of the building frame structure, it is possible to determine the right distribution of the displacement and stresses of every part.
Construction sequence analysis is becoming a crucial component of analysis since so many well-known analysis software packages now incorporate this feature. However, due to a lack of understanding of its value and use, nonlinear static analysis is not as well known. Construction sequence analysis, like many other analyses, had a role throughout the structure's design phase. As was already noted, it deals with nonlinear behaviour under static loads in the form of sequential load increase and how it affects structures when structural elements begin to respond to loads before the entire system is complete. ETABS (Extended 3D analysis of building systems), one of the top analysis programmes, is used for finite element analysis. All displacement outcomes are recorded in meters, whereas moments and axial loads are quantified in KN-m and KN, respectively
-
OBJECTIVES
-
To use construction sequence analysis to get an analytical understanding of the behaviour of the high- rise building during the construction process at its various stages.
-
To study of the similarities and differences between the conventional method and the Construction Sequence analysis.
-
To Determine the percentage of change in deflection, bending moments, shear force, and axial force, of the structural elements using the Conventional analysis and the construction sequence analysis
-
-
METHODOLOGY
In conventional design, all of the design assessments, including those for strength, stability, and deflection, are carried out by taking into consideration the application of loads in a single step. But in practice, the behaviour of the structure is not the same since the deflection of the components is not the same because of the self-weight, which operates in a sequential manner. The structural self-weight, external loads, boundary conditions, and materials are all dependent on phases of the building process; yet, their fluctuations are neglected in conventional design, which is nothing more than a restriction of the traditional design approach. It is necessary to develop a non-linear static load case in order to carry out an analysis of the structure in a sequential fashion, which depicts said load scenario. During the analysis process, grouping of each narrative is taken into consideration so that the program may determine the total number of steps necessary to finish the task. An analysis that is carried out step by step, taking into account the nonlinear behaviour of the materials analyzed in the prior stage, guarantees that the building sequence effects are accurately reflected in the research.
-
Procedure
-
Creating models:
Two models of G+15 storied RC frame are created in ETABS v.16. One model for conventional lumped analysis and another for Construction Sequence Analysis. Steps for creating a model are as follows:
-
Creating grid lines taking reference from an architectural drawing
-
Defining material properties
-
Defining frame section properties
-
Defining slab section properties
-
Assigning properties
-
-
Assignment of loads:
-
Defining load cases
-
For Conventional Analysis:
-
Defining load combinations
-
Assigning of loads and supports
-
-
For Construction sequence Analysis:
-
Setting Auto construction sequence load case to be active
-
Defining Auto construction sequence load case with combination of defined loads
-
Defining stages and duration for each stage
-
Assigning of loads and supports
4. Comparison of results:
The results obtained for parameters such as bending moment, shear force, deformation and axial force from both conventional analysis and construction sequence analysis are tabulated and compared with each other and the changes in results are observed. Percentage increase in the parameters is calculated and the conclusion is drawn.
-
-
-
li>
Flow chart for construction sequence analysis
Creating grid lines based on architectural drawing
Defining material properties Defining frame section properties Defining slab section properties Assigning properties
Defining load cases
Setting active auto construction sequence case
Defining Autoseq case with load combinations
Defining stages and duration for each stage
Assigning loads
Assigning supports
Run the model for Autoseq case
-
-
PROBLEM STATEMENT
In this study we have considered a G+15 storey building with floating column. The effects of staged construction have been simulated by setting the auto construction sequence case active in ETABS software. This enables us to define stages of construction and give time duration for all the stages. Here in this study, the building is analyzed for both conventional load combinations mentioned further in this section and auto construction sequence case and for this, each storey is defined as a stage and time duration is not considered and defined as zero. The details of the building are discussed further.
-
Analysis:
-
Run the model for set load cases for conventional lumped analysis
-
Run the model for Auto construction sequence case for construction sequence analysis
-
-
Structural details
The details such as loads considered, details of the building and load combinations are discussed in this section.
-
Loads considered
Material/Load
Load/Density
Density of Concrete
25 KN/m2
Floor Finish
1 KN/m2
Partition wall load
8.39 KN/m
External wall load
16 KN/m
Live load on floor
2.5 KN/m2
Earthquake load
1.25 KN/m2
Wind pressure
0.8 windward
Table 1: Loads considered
-
Details of the structure
Table 2: Structural details
-
-
Plan and elevation
Sl.
No.
Contents
Values
1
Number of Stories
16
2
Plan Dimensions
16 m × 20 m
3
Total Height of Building
53 m
4
Height of Each Storey
Base to Storey1 2.7 m
Storey 1-16 3.35 m
5
Grade of Concrete
M 40
6
Grade of Steel
Fe 500
7
Beam 1
230 mm × 610 mm
8
Beam 2
230 mm × 305 mm
9
Column 1 and Floating Column
230 mm × 610 mm
10
Transfer Column
600 mm × 900 mm
11
Transfer Beam
600 mm × 900 mm
12
Slab 1 Thickness
152 mm
13
Partition wall
120 mm
14
External wall
230 mm
15
Seismic Zone
II
16
Importance Factor
1
17
Seismic Zone Factor
0.36
Fig 1: Plan of the building
3) Load combinations
Comb 1
1.5(DL+LL)
Comb 2
1.2(DL+LL+EX)
Comb 3
1.2(DL+LL+EY)
Comb 4
1.2(DL+LL+WX)
Comb 5
1.2(DL+LL+WY)
The load combinations defined and used are as follows Table 3: Load combinations
Note 1: DL= Dead load, LL= live load, EX and EY= Seismic force in X and Y direction respectively, WX and WY= Wind Pressure along X and Y direction in windward direction.
Note 2: Only Comb1 is used for comparison of parameters.
Fig 2: Elevation of building
Fig 3: 3D Model
-
-
RESULTS
The structure has been analyzed and studied for parameters axial force, bending moment, shear force and deflection for conventional method and compared with Construction Sequence Analysis. The comparisons are represented graphically as follows.
-
Comparison of parameters in TB
In construction sequence analysis the parameters vary in each and every stage and goes on increasing as the stages are added and gives a higher value in TB when all the stages are added. On the contrary, in conventional analysis as all the loads are added in single step there is no variation in parameters in TB and the value is also low.
Comparison of deformation of TB
60
40
20
0
DEFORMATIONS (mm)
-
Deformation
20
Construction Sequence Analysis
Conventional Analysis
0 5
10
STOREYS
15
Fig 4: Comparison of deformation in TB
Comparison of Bending Moment
in TB
10000
5000
0
BENDING MOMENT (KN-M)
-
Bending moment
20
Construction Sequence Analysis
Conventional Analysis
0 5
10
STOREYS
15
Fig 5: Comparison of bending moment in TB
Comparison of Shear Force in TB
2500
2000
1500
1000
500
0
SHEAR FORCE (KN)
-
Shear force
20
Construction Sequence Analysis
Conventional Analysis
0 5
10
STOREYS
15
Fig 6: Comparison of shear force in TB
Comparison of Axial Force on TB
5000
4000
3000
2000
1000
0
AXIAL FORCE (KN)
-
Axial force
20
Construction Sequence Analysis
Conventional Analysis
0 5
10
STOREYS
15
Fig 5: Comparison of Axial force on TB
-
-
Storey-wise comparison of parameters
In this section we are comparing the change in parameters, storey-wise at section 1, where the transfer beam and floating column are present and clearly visible.
Here we can see that the parameters in construction sequence analysis are generally higher in TB level and get lower in the stories above TB. On the contrary, in conventional analysis the values are lower in TB level and go up for the stories above.
-
Deformation
Storeywise comparison of deformation
-
Shear force
Storeywise comparison of shear force
2500
SHEAR FORCE (KN)
2000
1500
1000
500
0
AXIAL DEFORMATION (MM)
70 -500
60
50
40
30
0 5 10 15 20
STOREY
Construction Sequence Analysis Conventional Analysis
20
10
0
0 5 10 15 20
STOREY
Construction Sequence Analysis Conventional Analysis
Fig 8: Storey-wise comparison of shear force
-
Axial force
Fig 9: Storey-wise comparison of axial force
Storeywise comparison of Axial force
Fig 6: Storey-wise comparison of deformation
2) Bending moment
Storeywise comparison of bending moment
BENDING MOMENT (KN-M)
8000
5000
AXIAL FORCE (KN)
4000
3000
2000
1000
0
-1000
0 5 10 15 20
STOREY
6000
4000
2000
Construction Sequence Analysis Conventional Analysis
0
-2000
0 5 10 15 20
STOREY
Construction Sequence Analysis Conventional Analysis
Fig 7: Storey-wise comparison of bending moment
-
-
-
Percentage variations in parameters
The parameters vary for certain percentage in construction sequence analysis than in conventional analysis. Here, the variations of the parameters for TB are shown in graphical manner.
-
Deformation
-
-
Axial force
5000
Axial Force (KN)
3139
4000
Axial Force in TB
3998
Deformation in TB
Deformation (mm)
60
45.032
37.166
40
20
3000
2000
1000
0
Axial Force
0
Deformation
Conventional Analysis Construction Sequence Analysis
Fig 10: Variation of deformation in TB
Bending Moment in TB
10000
6761.4
5441.13
5000
0
Bending Moment
Conventional Analysis Construction Sequence Analysis
Bending Moment (KN-m)
2) Bending moment
Fig 11: Variation of bending moment in TB
Conventional Analysis Construction Sequence Analysis
Fig 13: Variation of axial force on TB
5) Percentage increase in parameters
Table 4: Percentage increase in parameters
Contents
Conventional Analysis
Construction Sequence Analysis
%
Increase
Deformation of TB (mm)
37.166
45.03
21.16%
Bending Moment of TB (KN-m)
5441.13
6761.4
24.26%
Shear Force of TB (KN)
1785.39
2182.07
22.24%
Axial Force on TB
3139
3998
27.36%
-
-
CONCLUSION
3) Shear force
Shear Force (KN)
3000
2000
1000
0
Shear Force in TB
2182.07
1785.39
Shear Force
Within the scope of this study, a finite model with variable height has been taken into consideration. Analysis has been carried out using both the traditional and construction sequences. When compared to the linear static analysis, which shows that the axial deformation is greater in the top storey and less in the bottom storey, the results of the construction sequence analysis show that the axial deformation is greater in the supporting beams. This is in contrast to the linear static analysis, which shows that the axial deformation is greater in the top and less in the bottom. When compared to linear static analysis, building sequence analysis reveals that external columns experience significantly higher axial forces. In comparison to linear static analysis, the Moment that is created
Conventional Analysis Construction Sequence Analysis
Fig 12: Variation of shear force in TB
using sequential analysis consists of more columns. When compared to linear static analysis, shear force in columns
during sequential analysis is significantly higher. Its possible that this is due to the building being done in stages.
Following all of the preceding observations, the following is the conclusion that can be drawn:
-
Construction sequence analysis in structures made of RCC is required in order to improve the analysis accuracy in terms of displacement, axial, moment, and shear force in supporting beams and columns that are close to it, as well as for the structure as a whole.
-
When doing a study of a multistoried RCC structure, using a sequential load case results in a design that is more realistic than the standard design.
-
There is a considerable increase in the values of parameters of about 23% on an average when construction sequence is considered.
-
Therefore, when we design the structure for these higher parameters obtained from construction sequence analysis, the structure gets safer.
REFERENCES
[1] R. Pranay, I. Yamini Sreevalli, Er. Thota. Suneel Kumar (2015) Study and Comparison of conventional lumped Analysis with construction sequence analysis Civil Engineering Systems and Sustainable Innovations ISBN: 978-93-83083-78-7 [2] Santosh Panigrahi, Dr. Vikram Patil, Madan S. H, Somanagouda Takkalaki (2019) Importance of construction sequence analysis in design of high rise buildings IJISET – International Journal of Innovative Science, Engineering & Technology, Vol. 6 Issue 4, April 2019. [3] Tin Yadanar Kyaw, Nyein Nyein Thant (2017) Comparative Study on Construction sequence analysis on steel structure without and with floating columns International Journal of Trend in Scientific Research and Development (IJTSRD), ISSN: 2456- 6470, Volume-3 Issue-5, August 2019 [4] Kiran Y. Naxane, Prof. Mr. Laxmikant Vairagade, Mrs. GitadeviB. Bhaskar (2017) Construction sequence analysis of multistoried RCC building International Research Journal of Engineering and Technology (IRJET) Volume: 04 Issue: 07, July -2017
[5] Mohammad Jalilzadeh Afshari, Ali Kheyroddin, Majid G holhaki (2017) Simplified sequential construction analysis of buildings with the new proposed method Structural Engineering and Mechanics, Vol. 63, No. 1 (2017) 77-88, ISSN: 1225-4568 [6] A. Vafai, Mohsen Ghabdian, Homayoon E. Estekanchi, Chandrakant S. Desai (2009) Calculation of creep and shrinkage in tall concrete buildings using nonlinear staged construction analysis Asian journal of civil engineering, 2009, Vol. 10, no. 4, Pages 409-426. [7] Hyo-Gyoung Kwak, Jin-KookKim (2006) Time-dependent analysis of RC frame structures considering construction sequences Building and Environment Volume 41, Issue 10, October 2006, Pages 1423-1434