
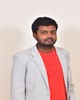
- Open Access
- Authors : Mr. Kollipara Durga Prasad, K. Rahul, N. Mallikarjuna Rao, A. Yaswanth Krishna Sree, Ch. Venkata Naga Mohith, G. Ganesh
- Paper ID : IJERTV13IS040094
- Volume & Issue : Volume 13, Issue 04 (April 2024)
- Published (First Online): 24-04-2024
- ISSN (Online) : 2278-0181
- Publisher Name : IJERT
- License:
This work is licensed under a Creative Commons Attribution 4.0 International License
Study of Advanced Shock Absorbers
Mr. Kollipara Durga Prasad M.Tech
Associate Professor, Department of Mechanical Engineering,
VKR VNB & AGK College of Engineering, Gudivada
K. Rahul
Mechanical Department VKR VNB & AGK College of
Engineering
N. Mallikarjuna Rao
Mechanical Department
VKR VNB & AGK College of Engineering
ABSTRACT
Shock absorbers or shocks were built to help absorb the up-and-down shock created by the springs whenever a vehicle hits a bump. Aside from absorbing the impact, they also keep the car or truck easily maneuverable even after a bumpy ride. The absence of shock absorbers would definitely result to a bouncing ride as energy is stored in the spring and then released to the vehicle, oftentimes exceeding the permitted range of suspension movement.
Most spring-based shock absorbers employ coil springs or leaf springs, though torsion bars can be used in torsion shocks as well. Springs alone are not shock absorbers as they only store and do not distribute or absorb energy. Modern vehicles typically use both springs and torsion bars along with hydraulic shock absorbers. With this setup, the shock absorber is reserved specifically for the hydraulic piston that takes in the vibration.
Today's technologically-advanced shock absorbers are fitted with velocity hydraulic damping devices which provide increased speed in the movement of the suspension to attain greater resistance. The result is a versatile shock absorber that can easily adapt to various road conditions. The effects of constant bounce, sway, brake dive and acceleration squat are thus significantly reduced.
Current designs of shock absorbers are either in twin tube designs and mono tube designs. A twin tube shock absorber is made up of an inner and outer tube that work seamlessly together to achieve its intended purpose while a mono tube is made up of one tube mounted in an upside down position to help reduce the load.
A shock absorber is just that…an absorber. In mathematics it is modeled as a dashpot which is a viscous dampener. The absorber works the same in both directions. It is a hole that a viscous fluid can pass through only so quickly.
-
Yaswanth Krishna Sree
Mechanical Department
VKR VNB & AGK College of Engineering
Ch. Venkata Naga Mohith
Mechanical Department
VKR VNB & AGK College of Engineering
G. Ganesh
Mechanical Department
VKR VNB & AGK College of Engineering
INTRODUCTION
The hydraulic shock absorber is one of the least understood fluid power components, both in functional and design considerations. The basic function of the shock absorber is to absorb and dissipate the impact kinetic energy to the extent that accelerations imposed upon the airframe are reduced to a tolerable level. Existing shock absorbers can be divided into two classes based on the type of the spring being used: those using a solid spring made of steel or rubber and those using a fluid spring with gas or oil, or a mixture of the two that is generally referred to as oleo-pneumatic. The high gear and weight efficiencies associated with the oleo-pneumatic shock absorber make it the preferred design for commercial transports.
Based on the analysis procedure as outlined in this chapter, algorithms were developed to determine the required stroke and piston length to meet the given design conditions, as well as the energy absorption capacity of the shock absorber.
The basic weight support functions of the oleo- pneumatic shock struts, which have a high efficiency under dynamic conditions both in terms of energy absorption and dissipation, is provided by a compressed cylinder of air and oil. A single- acting shock absorber, which is the most commonly used design for commercial transports, is shown. This type of shock strut absorbs energy by first forcing a chamber of oil against a chamber of dry air or nitrogen and then compressing the gas and oil. During the compression process, the oil and gas either remain separated or are mixed depending on the type of design. After the initial impact, energy is dissipated as the air pressure forces the oil back into its chamber through recoil orifices. Although the compression orifice could be merely a hole in the orifice plate, most designs have a metering pin extending through it, and by varying the pin diameter the orifice area is varied. This variation is adjusted so that the strut load is fairly constant
under dynamic loading. If this can be made constant, the gear efficiency would be 100 percent. In practice, this is never obtained and efficiencies of 80 to 90 percent are more usual. Since only the efficiency factor is of interest in the conceptual design phase, no additional discussion on the design of the metering pin will be provided.
HISTORY HISTORICAL DEVELOPMENT OF SHOCK ABSORBERS
The first primitive shock absorber was used as early as 1900 in the larger and faster racing cars. Even though, several designs were available, its use was very limited as most of early automobile designers categorised shock absorbers as unnecessary. 1920's saw gradual adoption of shock absorbers. Although early dampers were mostly friction devices, it was soon realised, that they were not suitable primarily due to their high initial stiction and damping force being independent of velocity. In comparison, the damping force in viscose damping is independent of velocity, and it also has a minimal stiction.
In the post- World War II years, the trend to coil springs arid softer rides favored shock absorbers of telescopic form. This form of dampers is now used in a wide range of damping applications everything from automobiles to tanks, locomotives and even bridges. Most commonly used configuration is still non pressurized twin tube hydraulic type. However, recently pressurized type is making rapid in roads especially in the passenger car market.
TYPES OF SHOCK ABSORBERS NON-PRESSURISED TWIN TUBE
TELESCOPIC HYDRAULIC DAMPERS
A twin tube telescopic non-pressurized hydraulic damper consists of a cylinder with a piston moving inside it. The piston has various designed orifices to allow fluid to flow between the compression and rebound chambers. To store the displaced oil by the
piston rod movement, a storage tube is provided. The mechanical energy absorbed by the damper is converted into heat. Heat so produced is dissipated to the atmosphere through the storage tube. A bottom valve which fits into the bottom end of the cylinder is provided to allow the oil to flow back to the cylinder tube from storage tube during rebound.
To avoid mechanical damage to the piston rod due to stones and dust that are thrown up during the travel of the vehicle at a high velocity, a protection tube is provided on the shock absorbers.
A number of types of non-pressurised twin tube hydraulic shock absorbers with minor refinements are available. Basic refinements offered can be classified into
Adjustable damping co-efficient, and
Variable damping co-efficient type.
GAS CHARGED SHOCK ABSORBERS
Gas charged shock absorbers are essentially hydraulic dampers with the addition of gas under pressure to improve the working efficiency. They are sometime also called 'gas shock absorber'. Only gas cannot be used as damping medium. Oil is a must. Pressurising the shock absorber oil allows elimination of cavitation (foaming of oil) a problem inherent in hydraulic dampers. Elimination of cavitation allows better control at all piston speeds and mvements. This leads to better vehicle control, improved ride quality and quicker operation. Gas charged dampers are two types, namely: Mono-Tube, and Double Tube types.
-
Mono-tube Shock Absorbers:
The original gas pressurised shock absorbers were of the single or mono-tube construction. In the mono-tube shock absorber, the usual arrangement is to close the bottom end of the working space by
a floating piston held in contact with the fluid by gas (usually nitrogen) under pressure below. The movement of the floating piston is confined to that necessary to absorb the rod volume. All of the valving function is handled by only the working piston as mono-tube unit has no bottom valve, so it must run at very high gas pressure in order to maintain proper control during the operation.
-
Twin Tube Pressurised Shock Absorbers :
A much later development, its construction is similar to twin tube non-pressurized shock absorber. It uses lower gas pressure than a mono- tube unit. This is possible, because control of the oil flow is provided by the bottom valve. Low pressure of the twin tube unit also allows the use of a larger diameter piston rod. In twin tube nitrogen gas is sealed in the reservoir can be maintained at
0.5 to 1.5 MPa, compared to 2.0 to 3.00 MPa in a monotube type. Length required in pressurised twin tube is smaller than mono-tube type. This ensures the best fitment and performance characteristics. These can be fitted without any problem in the same manner as fitting of conventional non- pressurised hydraulic shock absorber.
SPRING ASSISTED DAMPERS
Primary purpose of a damper to its dampen the oscillations. They cannot carry any load. Dampers with spring across it are available for the front and rear suspensions to carry load. They resemble a conventional shock absorber with a coil spring fitted on to it.
Spring assisted dampers are normally of two basic types, namely MacPherson strut and spring damper. MacPherson is used normally on a 4-wheel passenger car and spring dampers on two- wheelers.
THE FLUIDIC CONTROL-METERING SYSTEM
The Fluidic Control Metering System is the newest form of shock absorber orificing to be offered. Fluidic Control metering uses specially shaped orifice passages to yield by hydraulic flow the effect of a mechanically varied orifice. A typical fluidic control shock absorber is shown in Figure
A description of the internal parts:
-
Cylinder
-
Piston rod
-
Piston head
-
Main orifice
-
Feeder orifices
-
End cap and seal assembly (low pressure)
-
Piston rod displacement accumulator
-
Return spring
-
Reset valve
-
Guide spool
The operation of this type of shock absorber is not self-explanatory, as are most conventional metering systems. To operate with high efficiency, a compressible working fluid must be used, such as the family of silicone base oils. The molecular structure of the silicone oils allows them to be compressed up to 10% (by volume) when used in the high pressure dynamic environment of a shock absorber at impact. Oils of this type are rarely used in the rest of the field of hydraulic technology because of their compressibility. For example, if one were to use a silicone oil to replace normal hydraulic fluid (which is relatively incompressible) in a typical hydraulic system, the compressibility of the silicone would cause losses in pumping efficiency, and a response lag from every component downstream of the pumping source. If used in a conventional shock absorber of the types previously discussed, the silicone fluid will not affect the basic output curve, but the compressibility will decrease the rise time of the shock, reducing efficiency slightly. A disadvantage of using silicone oil in a hydraulic system is that most conventional commercially available seals are not compatible with this fluid. Special seal designs and materials are usually required. The Fluidic Control Metering System must use a compressible
fluid to operate or its efficiency will be about the same as a fixed orifice metering system.
Detail of the piston head in a Fluidic Control shock absorber:
-
The shock absorber cylinder (partial view)
-
The shock absorber piston rod (partial view)
-
The piston head
-
Primary orifice passage
-
Feeder orifice
-
Fluid collector groove
-
Reset check valve assembly
-
Primary fluid flow
-
Feeder orifice flow
-
Intersecting flow point
-
Combined flow
The Fluidic Control Shock Absorber (Fluidicshok)
Advantages
-
Moderate cost
-
Very high efficiency
-
Uses only a single low pressure seal
-
Can withstand drive force inputs without spiking
Disadvantages
-
Requires close production tolerances
-
Requires special seal materials to be compatible with the silicone oil required with this design.
THE ADJUSTABLE SHOCK ABSORBER
Starting about 1964, a different type of shock absorber began to appear in industrial usage. This type of device was the adjustable shock absorber, which could be adjusted in the field for energy capacity. This eliminated the requirements for re- orificing a shock every time a given size was to be used at a different velocity. The adjustable shock absorber also allowed distributor stocking, something that could not be done with custom orificed shocks. Early adjustable shocks were quite crude, using a needle valve controlled fixed orifice
shunt across a metering pin or metering tube design. If the needle valve was closed, the shock absorber would behave like any metering pin or metering tube type of shock. As the valve was opened, the shock would begin to perform like a fixed orifice design, with inherent low efficiency. The fixed orifice shunt adjustable shock absorber is shown
A description of the parts shown:
-
Needle valve adjustment
-
Valve packing
-
Shunt orifice adjusted by needle valve
-
Shunt discharge to low pressure side of piston head
The efficiency of the fixed orifice shunt style adjustable shock absorber can range from a low of about 30% with the adjustment wide open to a high of 60-80% when the adjustment is fully closed.
DESIGNING SHOCK ABSORBER STROKE CALCULATION
The first step in calculating the stroke (S) is to select the design reaction factor (N), sometimes called the landing load factor. This factor should not be confused with the aircraft load factor, which results from maneuvers or atmospheric disturbances. For a transport-type aircraft the landing load factor varies from 0.7 to 1.5, with 1.2 being the most widely used value. Sink speed (Vs) is usually legislated by the procuring authority and/or the regulations pertaining to a particular category of aircraft. The FAA requires that a transport-type aircraft be able to withstand the shock of landing at 10 ft/s at the design landing weight and 6 ft/s at maximum gross weight. In practice, sink speeds of this magnitude rarely occur due to ground effects and flare-out of the aircraft prior to touchdown. The total energy E) of the aircraft at the instant of touchdown, which consists of kinetic and potential energy, is approximated using the expression
where W is the aircraft weight, V is the sink speed, g is the gravitational acceleration, L is the wing lift, and St is the tire deflection. S is shock absorber stroke, which is the value we are trying to find. Given that the kinetic energy capacity of the shock absorber and tire must be equal to the total energy,
Where sand tare the shock absorber and tire absorber efficiency factors, respectively. The former is generally assumed to be 0.47 and the latter 0.8 for an oleo-pneumatic strut. To maintain an adequate safety margin, an extra one inch of stroke is usually added to the calculated stroke.
COMPRESSION RATIOS:
Compression ratios are the ratios of the pressure under one condition divided by the pressure under another condition, e.g., fully compressed to static. Two compression ratios are normally considered: static to fully extended and fully compressed to static. For transport-type aircraft, where floor height variation is important, a ratio of 4:1 for the static to extended case and 3:1 for the compressed to static case would be satisfactory. Assuming a static pressure (P2) of 1,500 psi, which enables standard compressors to be used for servicing and provides enough margin to allow for aircraft growth, pressures at the extended (P1) and compressed (P3) positions are calculated using the compression ratios given above. Note that the piston area (A), and subsequently the displacement volume (d), are both a function of the static pressure that is
And
Where F is the maximum static load per strut.
LOAD STROKE CURVE:
The energy absorbed by the strut during its stroke is obtained by integrating the area beneath the load- stroke curve, which relates the magnitude of the applied ground loads to the stroke traversed. Standard notation for shock strut sizing uses the subscript 1 to denote the fully extended position, 2 to denote the static position, and 3 to denote the compressed position. To accommodate excess energy produced in a heavy or semi-crash landing, shock absorbers are designed such that the piston is not fully bottomed even at the compressed position, i.e., V3 0. The reserve air volume, which is assumed to be 10 percent of the displacement, allows the shock strut at a predetermined load to
move through extra travel, absorbing the excess energy by the work done. Hence, the air volume at the fully-extended position is approximated as
Pressures between the extended and static positions are defined by the isothermal compression curve, which is representative of normal ground handling activity
Given the relationships of above Eqs, the pressure at stroke X is obtained using the expression
Pressures obtained using above Eq. are then multiplied by the piston area to arrive at the design loads as shown on the load-stroke curve.
A polytropic, i.e., real-gas, compression curve should be considered for pressures between the static and compressed positions. It is representative of dynamic compression cases such as landing impact and bumps traversal and is based upon PVnbeing constant, hence
The constant n can either be 1.35 or 1.1; the former is used when the gas and oil are separated and the latter when they are mixed during compression. The distance from the static to the fully compressed position is largely a matter of choice. Statistical data indicate
that transport-type aircraft typically have further compression beyond the static position of about 16 percent of the total stroke, a figure which tends to give a hard ride while taxiing. However, with the static position being so far up the load-stroke curve, where a large amount of energy is absorbed with a relatively small stroke travel, aircraft weight variations do not result in substantial gear deflections. That is, the built-in margin minimizes the need of redesigning the baseline shock strut for uses on future growth versions of the aircraft. Again, the pressures obtained using Eq. (5.9) are multiplied by the piston area to arrive at the design loads. At this point the values of P1 and P3 should be checked to ensure that the former is greater than 60 psi to avoid sticking due to friction between the piston and the cylinder wall, while the latter is less than 6,000 psi to prevent seal leakage.
INTERNAL CYLINDER LENGTH:
As specified by MIL-L-8552, the distance between the outer ends of the bearings shall be not less than
2.75 times the internal cylinder/piston outside diameter (D). Thus the minimum piston length is given by
Where
CONCLUSION:
Plane study on Shock absorbing systems is done and slither observation is made on working principle of Damp reduced Gear type shock absorbers and its vibrating equations.
It has been shown that various types of shock absorber designs are available, each of which performs best in specific types of applications. The formulas presented should give the reader at least a rudimentary knowledge of how to select a size for a specific job. There are many aspects of selection criteria and equations that have not been treated here.
REFERENCES
-
ISO 18431-4 Mechanical vibration and shock Signal processing Part 4: Shock response spectrum analysis
-
Harris Shock and Vibration Handbook, Cyril M. Harris, editor, Allan G.Piersol, editor, 5th ed., McGraw-Hill 2002. Chapter 23: Concepts in shock data analysis.
-
Ahlin K., Magnevall M., Josefsson A. Simulation of forced response in linear and nonlinear mechanical systems using digital filters http://www.bth.se/tek/amt/nonlinear.nsf/(WebFiles)/F75E7 709B9C6F47DC2571D50033078C/$FILE/ISMA_2006_4
44.pdf.