
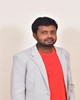
- Open Access
- [post-views]
- Authors : Mr. Kollipara Durga Prasad, Tiruveedhula Purna Naga Venkata Sai Kiran, Mynam Jagadeesh, Massimuku Naga Pavan Tejendra, Vanka Hemanth Kumar, Kanteti Sahithya, Dagani Ratna Raju
- Paper ID : IJERTV13IS040095
- Volume & Issue : Volume 13, Issue 04 (April 2024)
- Published (First Online): 24-04-2024
- ISSN (Online) : 2278-0181
- Publisher Name : IJERT
- License:
This work is licensed under a Creative Commons Attribution 4.0 International License
Study of Glass Concrete Manufacturing Techniques
Mr. Kollipara Durga Prasad M.Tech,
Associate Professor, Department of Mechanical Engineering,
VKR VNB & AGK College of Engineering, Gudivada , Krishna, Andhra Pradesh-521301
Tiruveedhula Purna Naga Venkata Sai Kiran
Mechanical Department
VKR VNB & AGK College of Engineering
Mynam Jagadeesh
Mechanical Department
VKR VNB & AGK College of Engineering
ABSTRACT
Glass is produced in many forms, including packaging of container glass (bottles, jars), flat glass (windows, windscreens), bulb glass (light globes), cathode ray tube glass (TV screens, monitors, etc), all of which have a limited life in the form they are produced and need to be reused/recycled in order to avoid environmental problems that would be created if they were to be stockpiled or sent to landfill. This paper deals with the recycling aspects of container glass, and the term glass hereafter refers to this type only.
Post-consumer glass containers have traditionally been disposed of either in domestic refuse, which ends up in landfill, collected in designated collection spots for reuse/recycling, or collected from kerbside and then transported to collection sites. The major aim of environmental authorities is to reduce, as far as possible, the disposal of post-consumer glass in landfill and diversion to economically viable glass product streams. Glass is a unique inert material that could be recycled many times without changing its chemical properties. In other words, bottles can be crushed into cullet, then melted and made into new bottles without significant changes to the glass properties. Most of the glass produced is in the form of containers, and the bulk of what is collected post-consumer is again used for making containers.
The efficiency of this process depends on the method of collecting and sorting glass of
different colours. If different color glass (clear, green, amber) could be separated, then they could be used for manufacturing similar colour glass containers. However, when the glass colors get mixed, they become unsuitable for use as
containers, and are then used for other purposes, or sent to landfill. The utilization of glass in concrete is of particular interest for the work reported here
Massimuku Naga Pavan Tejendra
Mechanical Department VKR VNB & AGK College of
Engineering
Vanka Hemanth Kumar
Mechanical Department VKR VNB & AGK College of
Engineering
Kanteti Sahithya
Mechanical Department VKR VNB & AGK College of
Engineering
Dagani Ratna Raju
Mechanical Department VKR VNB & AGK College of
Engineering
INRODUCTION
Glass Concrete is a type of fiber/glass powder/glass wool reinforced concrete. Glass fiber concretes are mainly used in exterior building façade panels and as architectural pre cast concrete. Glass is produced in many forms, including packaging of container glass (bottles, jars), flat glass (windows, windscreens), bulb glass (light globes), cathode ray tube glass (TV screens, monitors, etc), all of which have a limited life in the form they are produced and need to be reused/recycled in order to avoid environmental problems that would be created if they were to be stockpiled or sent to landfill.
This paper deals with the recycling aspects of container glass, and the term glass hereafter refers to this type only.
1.1 Recycling of glass
There are large amounts of recycled glass available for use in concrete, but there have been many notable failures in concretes containing recycled glass due to unusual chemistries that occur when glass is included in a concrete mix. This paper discusses these interactions and provides remedies to safely use recycled glass aggregates and some glass powders in concrete mix designs.
Post-consumer glass containers have traditionally been disposed of either in domestic refuse, which ends up in landfill, collected in designated collection spots for reuse/recycling, or collected from curbside and then transported to collection sites.
The major aim of environmental authorities is to reduce, as far as possible, the disposal of post-consumer glass in landfill and diversion to economically viable glass product streams.
Glass is a unique inert material that could be recycled many times without changing its chemical properties. In other words, bottles can be crushed into cullet, then melted and made into new bottles without significant changes to
the glass properties. Most of the glass produced is in the form of containers, and the bulk of what is collected post- consumer is again used for making containers
The efficiency of this process depends on the method of collecting and sorting glass of different colors. If different color glass (clear, green, amber) could be separated, then they could be used for manufacturing similar color glass containers
However, when the glass colors get mixed, they become unsuitable for use as containers, and are then used for other purposes, or sent to landfill.
Rindl (1998) reported the many non-container uses of glass cullet, which included road construction aggregate, asphalt paving, concrete aggregate, building applications (glass tiles and bricks, wall panels, etc), fiber glass insulation, glass fiber, abrasive, art glass, agricultural fertilizer, landscaping, reflective beads, tableware, hydraulic cement, among other applications. The utilization of glass in concrete is of particular interest for the work reported here. A major concern regarding the use of glass in concrete is the chemical reaction that takes place between the silica-rich glass particles and the alkali in the pore solution of concrete, i.e., alkali-silica reaction (ASR).
This reaction can be very detrimental to the stability of concrete, unless appropriate precautions are taken to minimize its effects. Such preventative actions could be achieved by incorporating a suitable pozzolonic material such as fly ash, silica fume, or ground blast furnace slag in the concrete mix at appropriate proportions.
HISTORY
GLASS is a transparent material produced by melting a mixture of materials such as silica, soda ash, and CaCO3 at high temperature followed by cooling during which solidification occurs without crystallization. Glass is widely used in our lives through manufactured products such as sheet glass, bottles, glassware, and vacuum tubing. Glass is an ideal material for recycling. The use of recycled glass in new container helps save of energy. It helps in brick and ceramic manufacture, and it conserves raw materials, reduces energy consumption, and the volume of waste sent to landfill. In many countries the container industry cannot consume all of the recycled
container glass that will become available in the coming years, mainly due to the color imbalance between that which is manufactured and that which is consumed. The resulting surplus of green glass from imported bottles containing red wine may be exported to producer countries, or used locally in the growing diversity of secondary end uses for recycled glass.
Jin, Meyer and Baxter (2000) found that glass particles of around 1.2 mm caused the largest mortar bar expansion in the particle size range of 0.15 4.75 mm. They found that the largest expansion resulted when glass particles formed 100%
of the aggregate, and that green glass containing more than 1.0% chromium oxide had a beneficial suppressive effect on ASR. Carpenter and Cramer (1999) also reported that powdered glass was effective in educing ASR expansion in accelerated mortar bar tests, similar to the effects of fly ash, silica fume and slag.
This is in agreement with the present authors unpublished results Shayan and Xu, (1998), where it was shown that glass powder could suppress the ASR expansion caused by natural reactive aggregates and coarse glass particles.
GLASS POWDER CONCRETE
-
Glass fiber reinforced concrete
Glass fiber is a recent introduction in making fiber concrete. It has very high tensile strength 1020 to 4080
2
N/mm . The alkali resistant glass fiber reinforcement in
concrete shows considerable improvement in durability also.Glass-fiber-reinforced concrete (GFRC) has been used worldwide since the early 1970s. Over the last few years there has been a growing recognition of the material as a durable and lightweight alternative to the traditional natural and cast stone architectural dressings used in house building. GFRC uses glass fibers for reinforcement instead of steel. It is typically cast in a thin section of around 1/2 to 3/4. Since the fibers cannot rust like steel, there is no need for a protective concrete cover thickness to prevent rusting. With the thin, hollow construction of GFRC products, they can weigh a fraction of the weight of traditional precast concrete.
COMPONENTS OF GFRC
GFRC is a composite of cement, glass fibers, aggregates and polymers. The main components of GFRC are: Cement: – The cement used in the GFRC should be ordinary Portland cement
Aggregates: – Usually in GFRC only fine aggregates are only used fine aggregates are of silica sand. If used, coarse aggregates may be of crushed stones.
Glass fibers: – glass fiber shall be an alkali resistant, continuous filament fiber developed and to have high strength retention in ordinary Portland cement environments.
Polymers: Polymers are used in the GFRC mix to give toughness to the mix and give a curing effect to the mix
after hardening due to its high water content. Acrylic polymers having low solid content is used usually
Admixtures: Addition of glass fibers reduces the workability of the concrete mix to a great extent, for making the concrete workable plasticizers can be used in required dosage.
Structural Properties of GFRC
STRESS STRAIN DIAGRAM FOR FIBER REINFORCED CONCRETE
Concrete, reinforced with fiberglass, has been found to perform very well. On the stress/strain chart (Figure 3, left side "A") shows each component (cement matrix and glass fibers) by themselves. (Figure 3, left side "B") shows the composite system.
In Region 1, the matrix and fibers act together (as stated previously) behaving essentially elastically. At this stage, there are no visible cracks in the matrix. At the end of Region 1, the matrix cracks and the load at the cracked surface is transferred to the glass fibers. This is called the "First Crack" point. The process
APPLICATIONS
Applications in various fields, ranging from construction to artistic creations. Architectural elements such as facades, cladding, and countertops benefit from the material's lightweight nature and adaptability.
ADVANTAGES
-
A high tensile strength than steel.
-
Non-combustible so it will not burn.
-
It is thinner and stronger than plain concrete.
-
Lightweight and tough materials also reduce the transportation expense.
-
Allow for flexibility in design and reduce the impact on the environment
DISADVATAGES
Cost: The main disadvantage of GRC is that it is more expensive when compared to concrete at face value.
Lack of Ductility: GRC lacks ductility, which is a solid material's ability to deform under stress.
Difficult to Self-Mix
GRC is difficult to self-mixX.
CONCLUSION
The main study considered is to investigate the effect of using glass powder filler on hot asphalt concrete, glass wool in concrete, glass fibre on concrete, glass powder on concrete mixture.
Using glass powder filler in hot asphalt concrete mixtures led to produce lighter mixtures almost with higher percentage of voids as compared with corresponding mixtures containing ordinary Portland cement or limestone powder.
Studies are required on durability of mixtures with glass powder fiber by testing resistance to many cycles of freezing and thawing.
Recycled glass aggregates can be safely used in concrete mix designs as long as the ASR potential is mitigated with a proper chemistry.
Both fine and coarse aggregate could also be replaced in concrete of 32 MPa strength grade with acceptable strength development properties.
REFERENCES
-
PHILLIPS, J.C. and CAHN, D.S. Refuse Glass Aggregate in Portland Cement.
-
NYSERDA. Use of Recycled Glass for Concrete Masonry blocks RINDL, J. Report by Recycling Manager, Dane County, Dept of Public Works, Madison,USA,
-
E. A Byars, B. Morales-Hernandez, and Z.H. Ying, Waste glass as concrete aggregate and pozzolan – laboratory and industrial projects, Concrete, vol. 38
-
Recommendations for measurement of pulse velocity through concrete.BSI Standard.
-
Paving blocks-Requirements and test methods. TSE Standard 2824 EN 1338, 2005.