
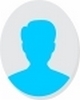
- Open Access
- Authors : Shobhit Gupta , Ajay Srivastava , Rajiv Singh
- Paper ID : IJERTV11IS100064
- Volume & Issue : Volume 11, Issue 10 (October 2022)
- Published (First Online): 02-11-2022
- ISSN (Online) : 2278-0181
- Publisher Name : IJERT
- License:
This work is licensed under a Creative Commons Attribution 4.0 International License
Study of the Performance of Induction Motor Under Various Voltage Sags Subjected to Different Loading Conditions
Shobhit Gupta, Ajay Srivastava, Rajiv Singh
1,,3 2Department of Electrical Engineering, College of Technology,
G.B. Pant University of Agriculture and Technology Pantnagar, Udham Singh Nagar, Uttarakhand, 263145, India
Abstract: For the efficient performance of the induction machine, it is important to maintain the high quality of power supply. There are several power quality issues and voltage sag is one of the most important disturbances among them. One sag event may cause a great monetary loss to the affected industry. There are multiple effects of the voltage sag on the performance of induction machines which are cumulative in nature. And the end result may reduce its efficiency, shortens its life and in the worse case causes premature failure. In this paper a comparative study has been done on the performance of a 10 hp induction motor under various voltage sag conditions in the MATLAB-SIMULINK enviornment. The motor has been operated under full load condition as well as under half load condition. The current and torque peaks and the speed loss have been chosen as the variables for study the sensitivity of induction motor towards the voltage sags.
Keywords: Induction motor, voltage sag.
-
INTRODUCTION
The term power quality was used first time by H.H. Kajihara in 1968. The definition of power quality given in the IEEE dictionary originates in IEEE standard 1100 is: Power quality is the concept of powering and grounding electronic equipment in a manner that is suitable to the operation of that equipment and compatible with premise wiring system and other connected equipments [2]. There are many power quality disturbances which may affect the performance of an induction motor in different ways. Voltage sag is most common event among various power quality disturbances. In a survey conducted by Bell Telephone Laboratories 87.2% of events were reported as voltage sag [9].
Sags may results in low efficiency, decreased life, malfunctioning and complete shutdown of induction motor [5].
may cause the current and torque peaks and speed loss in the induction motor. Different sag initiation angles affect the performance of induction motor in different ways [6]. All these changes can be observed just after the time of sag initiation and recovery instant.
The torque of the induction motor is directly proportional to the square of the voltage. So if any change in the magnitude of the voltage occurs it affects the value of torque drastically. In this paper the performance of 10 hp, 400 V, 50 Hz induction motor has been simulated and effects have been studied in terms of current peaks, torque peaks and speed loss under various voltages. Section II describes the characterisation of various voltage sags. Effects of various voltage sags on the performance of induction motor under different loading conditions have been studied in section III. Conclusion has been given in section IV.
-
VOLTAGE SAG CHARACTERIZATION Voltage sags experienced by three phase loads can be classified in to seven different types, namely A,B,C,D,E,F and G. Type A sag is a symmetrical sag whereas other sags are of unsymmetrical type. Phasor diagrams of various voltage sags and their equation has been shown in Figure 1 and Table 1 respectively. hV is the magnitude of remaining voltage having a value between 0 and 1.
According to IEEE standard 1159-1995, a voltage sag is defined as a decrease in RMS voltage down to 90% to 10% of nominal voltage for a time greater than 0.5 cycles of the power frequency but less than or equal to one minute. [4, 7]. Voltage sag may be symmetrical or asymmetrical, depending upon the type of fault. In symmetrical voltage sag the magnitude of the individual phase voltages are equal and their phasor are displaced at 1200 from each other. The main reason of a symmetrical voltage sags are three phase fault or starting of a large induction motor. The single line to ground faults, line to line fault or two lines to ground fault results in unsymmetrical voltage sags in the system. The voltage sag
Figure 1: Voltage sag classification for h=0.5
Table 1: Different Voltage Sag Equations
h = 0.1
h = 0.5
h = 0.8
14
12
Current Peak (pu)
10
8
6
4
2
0 20 40 60 80 100 120 140 160 180
Angle of Sag Initiation (Degree)
Figure 2: Current peak for sag A under half load condition
h = 0.1
h = 0.5
h = 0.8
10
9
Current Peak (pu)
8
7
6
Transients are observed in the voltage just after the start of voltage sag and just after the clearance of fault [3, 8]. There is always a chance that there may be a phase shift in the voltage or type of the voltage sag may change [1]. For keeping the things to be simple the shape of the voltage sag is assumed to be rectangular in this paper and no change in the sag type has been considered.
-
EFFECT OF VOLTAGE SAG ON INDUCTION MOTOR UNDER FULL LOAD AND HALF LOAD
CONDITION.
In this paper the performance of induction motor has been simulated under half load and full load condition subjected to various sag conditions. The analysis has been done in terms of current peaks, torque peaks and magnitude of speed loss. Three different sag magnitudes have been considered for the analysis which are h=0.1, 0.5, 0.8. Seven different sag initiation angles ( =00, 300, 600, 900, 1200, 1500, 1800) have been considered for the study.
5
4
3
0 20 40 60 80 100 120 140 160 180
Angle of Sag Initiation (Degree)
Figure 3: Current peak for sag B under half load condition
h = 0.1
h = 0.5
h = 0.8
12
11
10
Current Peak (pu)
9
8
7
6
5
4
3
10 hp motor under half load condition:
Results for the current peaks under half load conditions for different voltage sag conditions are given from Figure 2 to Figure 8.
0 20 40 60 80 100 120 140 160 180
Angle of Sag Initiation (Degree)
Figure 4: Current peak for sag C under halfload condition
h = 0.1
h = 0.5
h = 0.8
13
12
11
Current Peak (pu)
10
9
8
7
6
5
4
0 20 40 60 80 100 120 140 160 180
Angle of Sag Initiation (Degree)
and F where as maximum current peaks are obtained at sag initiation angle of 00 for sag C, E and G. It can also be noticed that the magnitude of current peaks also increases with the increase in the magnitude of sag.
h = 0.1
h = 0.5
h = 0.8
11
10
9
Current Peak (pu)
8
7
6
5
Figure 5: Current peak for sag D under half load condition
h = 0.1
h = 0.5
h = 0.8
11
10
4
3
2
0 20 40 60 80 100 120 140 160 180
Angle of Sag Initiation (Degree)
Figure 8: Current peak for sag G under half load condition
Current Peak (pu)
9
8
Effects of various voltage sag conditions
7 on the performance of induction motor in terms of torque peaks have been shown in Figure 9 to Figure 15.
6
h = 0.1
h = 0.5
h = 0.8
10.5
5
10
4
9.5
3
0 20 40 60 80 100 120 140 160 180
Angle of Sag Initiation (Degree)
Torque Peak (pu)
9
8.5
Figure 6: Current peak for sag E under half load condition 8
7.5
h = 0.1
h = 0.5
h = 0.8
11 7
10 6.5
9
Current Peak (pu)
8
7
6
5
4
3
2
0 20 40 60 80 100 120 140 160 180
Angle of Sag Initiation (Degree)
6
5.5
0 20 40 60 80 100 120 140 160 180
Angle of Sag Initiation (Degree)
Figure 9: Torque peaks for sag A under half load condition
h = 0.1
h = 0.5
h = 0.8
7
6.5
Torque Peak (pu)
6
5.5
5
Figure 7: Current peak for sag F under half load condition
It can be seen from Figure 8-15 that the maximum current peaks are obtained for sag A. The maximum current peaks are almost independent of the sag magnitude for sag A. it can also be observed from the Figure 2- 8 that maximum current peaks are obtained at sag initiation angle of 90o for sag B,D
4.5
4
3.5
0 20 40 60 80 100 120 140 160 180
Angle of Sag Initiation (Degree)
Figure 10: Torque peaks for sag B under half load condition
h = 0.1
h = 0.5
h = 0.8
10
9
Torque Peak (pu)
8
7
6
5
4
0 20 40 60 80 100 120 140 160 180
Angle of Sag Initiation (Degree)
indicate that for a particular sag magnitude torque peaks are almost constant for all sag initiation angles in case of sag A.
Maximum torque peaks are obtained at sag initiation angle of 90o for sag B, sag D and sag F, and minimum peaks are observed at an angle of 00 for above mentioned sags. Opposite results are obtained for sag C, sag E, and sag G.
Figures 11-12 indicate that sag C and sag D have similar values of maximum and minimum torque peaks but at different initial angles.
Similarly, it can be observed from Figure 13 – 15 that torque peaks vs angle of sag initiation curves have the same pattern for sag E and sag G, i.e. the values of torque peaks are same for sag E and sag G at each value of initial angle. The maximum and minimum values of torque peaks for sag E, sag D, and sag F are also equal in above mentioned figures.
Figure 11: Torque peaks for sag C under half load condition
h = 0.1
h = 0.5
h = 0.8
10
9
Torque Peak (pu)
8
7
6
h = 0.1
h = 0.5
h = 0.8
7.5
7
6.5
Torque Peak (pu)
6
5.5
5
4.5
4
3.5
5
4
0 20 40 60 80 100 120 140 160 180
3
0 20 40 60 80 100 120 140 160 180
Angle of Sag Initiation (Degree)
Angle of Sag Initiation (Degree)
Figure 12: Torque peaks for sag D under half load condition
h = 0.1
h = 0.5
h = 0.8
7.5
7
6.5
Torque Peak (pu)
6
5.5
5
4.5
4
Figure 14: Torque peaks for sag F under half load condition
h = 0.1
h = 0.5
h = 0.8
7.5
7
6.5
Torque Peak (pu)
6
5.5
5
4.5
4
3.5
3
0 20 40 60 80 100 120 140 160 180
Angle of Sag Initiation (Degree)
3.5
3
0 20 40 60 80 100 120 140 160 180
Angle of Sag Initiation (Degree)
Figure 13: Torque peaks for sag E under half load condition
Figure 9-15 depict that among all sags, sag A has the maximum torque peaks for all the three sag magnitudes. Values of maximum torque peaks are 10.8, 6.8, and 5.8 p.u. for sag magnitudes h=0.1, 0.5, and 0.8 respectively. Figure 9
Figure 15: Torque peaks for sag G under half load condition
Speed loss curves for motor under half load condition have been represented in Figures 16-22.
From the Figure 16 it is clear that during sag A, when the sag magnitude is h=0.1 motor completely stops irrespective of sag initiation angle. For h =0.5 and h=0.8 the
speed loss is almost constant i.e. 9.38 and 3.82 p.u. at all sag 25
initiation angles.
In Figure 16-22, maximum speed loss is observed
for sag A in comparison to all other sags. The maximum 20
Speed Loss (pu)
speed loss is observed at 900 for sag B, sag D, and sag F whereas sag C, sag E and sag G have maximum speed loss at
00 angle. Figure 20-22 depicts that sags E and G have the 15
similar speed loss for same values of sag initiation angles and that maximum and minimum values of speed loss are
10
equal for sag E, sag F, and sag G.
h = 0.1
h = 0.5
h = 0.8
h = 0.1
h = 0.5
h = 0.8
5
25
20 0
0 20 40 60 80 100 120 140 160 180
Angle of Sag Initiation (Degree)
Speed Loss (pu)
15 Figure 18: Peak of speed loss for sag C under half load condition
10 25
5 20
h = 0.1
h = 0.5
h = 0.8
Speed Loss (pu)
20 40 60 80 100 120 140 160 180
Angle of Sag Initiation (Degree) 15
Figure 16: Peak of speed loss for sag A under half load condition
h = 0.1
h = 0.5
h = 0.8
7 10
6
5
Speed Loss (pu)
5
0
0 20 40 60 80 100 120 140 160 180
Angle of Sag Initiation (Degree)
4
Figure 19: Peak of speed loss for sag D under half load condition
h = 0.1
h = 0.5
h = 0.8
18
3
16
2 14
Speed Loss (pu)
12
1
0 20 40 60 80 100 120 140 160 180 10
Angle of Sag Initiation (Degree)
Figure 17: Peak of speed loss for sag B under half load condition 8
6
4
2
0
0 20 40 60 80 100 120 140 160 180
Angle of Sag Initiation (Degree)
Figure 20: Peak of speed loss for sag E under half load condition
h = 0.1
h = 0.5
h = 0.8
8
h = 0.1
h = 0.5
h = 0.8
18
16 7
14
Current Peak (pu)
6
Speed Loss (pu)
12
10 5
8
4
6
3
4
2 2
0
0 20 40 60 80 100 120 140 160 180
Angle of Sag Initiation (Degree)
1
0 20 40 60 80 100 120 140 160 180
Figure 21: Peak of speed loss for sag F under half load condition
Angle of Sag Initiation (Degree)
Figure 23: Current peak for sag A under full load condition
h = 0.1
h = 0.5
h = 0.8
18
h = 0.1
h = 0.5
h = 0.8
6
16
5.5
14
5
Speed Loss (pu)
Current Peak (pu)
12
4.5
10
4
8
3.5
6
3
4
2.5
2
2
0
0 20 40 60 80 100 120 140 160 180
Angle of Sag Initiation (Degree)
1.5
0 20 40 60 80 100 120 140 160 180
Angle of Sag Initiation (Degree)
Figure 22: Peak of speed loss for sag G under half load condition
10 hp motor under full load condition:
The simulation has been performed on the motor under full load condition for three different sag magnitudes. Results for current peaks, torque peaks, and speed loss have been investigated. The simulation results for 10 hp motor under full load condition have been shown in Figure 23-29 in terms of current peaks.
Figure 23 depicts that maximum current peak of 7.88, 4.67 and 2.15 p.u. have been obtained for sag A at h=0.1, 0.5 and 0.8 respectively. The magnitudes of current peaks for sag A has almost constant current peak for every sag initiation angle. Similar to half load condition, at sag initiation angle 900, sag B, sag D, and sag F have their maximum current peaks and sag C, sag E, and sag G have their maximum current peaks at 00 sag initiation angle.
Figure 24: Current peak for sag B under full load condition
h = 0.1
h = 0.5
h = 0.8
8
7
Current Peak (pu)
6
5
4
3
2
1
0 20 40 60 80 100 120 140 160 180
Angle of Sag Initiation (Degree)
Figure 25: Current peak for sag C under full load condition
h = 0.1
h = 0.5
h = 0.8
h = 0.1
h = 0.5
h = 0.8
8 8
7
7
Current Peak (pu)
6
Current Peak (pu)
6
5
5
4
4 3
3 2
2
1
0 20 40 60 80 100 120 140 160 180
Angle of Sag Initiation (Degree)
Figure 26: Current peak for sag D under full load condition
h = 0.1
h = 0.5
h = 0.8
8
7
Current Peak (pu)
6
5
4
3
2
1
0 20 40 60 80 100 120 140 160 180
Angle of Sag Initiation (Degree)
Figure 27: Current peak for sag E under full load condition
1
0 20 40 60 80 100 120 140 160 180
Angle of Sag Initiation (Degree)
Figure 29: Current peak for sag G under full load condition
Figure 30 – 36 represents the result of simulation of 10 hp motor under full load condition for torque peaks under various sags. It has been observed from Figure 30-36 that maximum torque peaks are obtained for sag A. Values of maximum torque peaks are 6.6, 3.4 and 2.6 p.u. for sag magnitudes h=0.1, 0.5, and 0.8 respectively. Figure 4.36 depicts that torque peaks have almost constant value irrespective of sag initiation angles for sag A.
As similar to half load condition maximum torque peaks for sag B, sag D, and sag F have been obtained at sag initiation angle of 90o (from Figure 31, 33 and 35) and for sag C, sag E, and sag G. maximum torque peaks are obtained at 00 sag initiation angle.
Figure 34 and Figure 36 display the same pattern of torque peak vs sag initiation angle curves for sag E and sag
G. It can also be observed from Figures 34-36 that the maximum and minimum values of torque peaks are obtained for sag E, sag D, and sag F are same but at different values of sag initiation angles. Similarly Figure 32 and Figure 33 indicate that sag C and sag D have similar values of maximum and minimum torque peaks.
h = 0.1
h = 0.5
h = 0.8
8
h = 0.1
h = 0.5
h = 0.8
7
7
6.5
Current Peak (pu)
6 6
Torque Peak (pu)
5 5.5
5
4
4.5
3
4
2
3.5
1
0 20 40 60 80 100 120 140 160 180
Angle of Sag Initiation (Degree)
Figure 28: Current peak for sag F under full load condition
3
2.5
0 20 40 60 80 100 120 140 160 180
Angle of Sag Initiation (Degree)
Figure 30: Torque peaks for sag A under full load condition
3.2
3
Torque Peak (pu)
2.8
2.6
2.4
2.2
2
1.8
1.6
h = 0.1
h = 0.5
h = 0.8
20 40 60 80 100 120 140 160 180
Angle of Sag Initiation (Degree)
h = 0.1
h = 0.5
h = 0.8
6.5
6
5.5
Torque Peak (pu)
5
4.5
4
3.5
3
2.5
Figure 31: Torque peaks for sag B under full load condition
h = 0.1
h = 0.5
h = 0.8
5
4.5
2
1.5
0 20 40 60 80 100 120 140 160 180
Angle of Sag Initiation (Degree)
Torque Peak (pu)
4
3.5
3
2.5
Figure 34: Torque peaks for sag E under full load condition
h = 0.1
h = 0.5
h = 0.8
6.5
6
5.5
Torque Peak (pu)
5
4.5
2
0 20 40 60 80 100 120 140 160 180
Angle of Sag Initiation (Degree)
4
3.5
Figure 32: Torque peaks for sag C under full load condition
3
2.5
2
1.5
0 20 40 60 80 100 120 140 160 180
Angle of Sag Initiation (Degree)
Figure 35: Torque peaks for sag F under full load condition
h = 0.1
h = 0.5
h = 0.8
6.5
6
5.5
Torque Peak (pu)
5
4.5
4
3.5
Figure 33: Torque peaks for sag D under full load condition
3
2.5
2
1.5
0 20 40 60 80 100 120 140 160 180
Angle of Sag Initiation (Degree)
Figure 36: Torque peaks for sag G under full load condition
The curves between speed loss vs. sag initiation 25
angle have been represented in Figure 37-43. Figure 37 shows that for a very low value of remaining voltage motor
completely halts for sag A irrespective of sag initiation 20
angle.
h = 0.1
h = 0.5
h = 0.8
Speed Loss(pu)
h = 0.1
h = 0.5
h = 0.8
25 15
20 10
Speed Loss (pu)
15 5
10
0
0 20 40 60 80 100 120 140 160 180
Angle of Sag Initiation (Degree)
5
20 40 60 80 100 120 140 160
Angle of Sag Initiation (Degree)
Figure 37: Peak of speed loss for sag A under full load condition
Figure 40: Peak of speed loss for sag D under full load condition
h = 0.1
h = 0.5
h = 0.8
25
20
Speed Loss (pu)
h = 0.1
h = 0.5
h = 0.8
7
15
6
10
Speed Loss (pu)
5
5
4
3 20 40 60 80 100 120 140 160
Angle of Sag Initiation (Degree)
Figure 41: Peak of speed loss for sag E under full load condition
2
25
1
0 20 40 60 80 100 120 140 160 180
Angle of Sag Initiation (Degree) 20
h = 0.1
h = 0.5
h = 0.8
Figure 38: Peak of speed loss for sag B under full load condition
Speed Loss (pu)
25 15
h = 0.1
h = 0.5
h = 0.8
20 10
Speed Loss (pu)
15 5
10 20 40 60 80 100 120 140 160 180
Angle of Sag Initiation (Degree)
Figure 42: Peak of speed loss for sag F under full load condition
5
0
0 20 40 60 80 100 120 140 160 180
Angle of Sag Initiation (Degree)
Figure 39: Peak of speed loss for sag C under full load condition
Table 2: Comparison of current peaks under different loading
h = 0.1
h = 0.5
h = 0.8
Sag Type
Sag Magnitude
Half Load Condition
Full load condition
Sag A
0.1
13
7.88
0.5
8.2
4.67
0.8
4.8
2.15
Sag B
0.1
9.58
5.8
0.5
5.73
3.47
0.8
3.93
1.87
Sag C
0.1
11.83
7.45
0.5
7.41
3.23
0.8
4.63
2.35
Sag D
0.1
11.82
7.47
0.5
7.45
3.25
0.8
4. 6
2.37
Sag E
0.1
10.48
7.75
0.5
6.94
4.28
0.8
2.56
1.99
Sag F
0.1
10.60
7.74
0.5
6.75
4.47
0.8
2.89
2.09
Sag G
0.1
10.48
7.91
0.5
6.63
4.2
0.8
2.52
1.99
25 conditions
20
Speed Loss (pu)
15
10
5
20 40 60 80 100 120 140 160
Angle of Sag Initiation (Degree)
Figure 43: Peak of speed loss for sag G under full load condition
Figure 37-43 indicate maximum speed loss for motor is in case of sag A. At 50% remaining voltage the maximum speed loss is 9.38 p.u. whereas, when remaining voltage is 80% the maximum speed loss observed is 3.82 p.u. for sag A.
The maximum speed loss is observed at 900 for sag B, sag D, and sag F whereas sag C, sag E, and sag G have maximum speed loss at 00 sag initiation angle.
It is clear from Figure 41-43 that, sag E and sag G have the same speed loss vs. sag initiation angle curves for all sag magnitudes. Same values of maximum and minimum peaks of speed loss have also been depicted for sag E, sag F, and sag G in above mentioned figures. Similarly equal values of maximum and minimum speed loss at different angles for sag C and sag D have been shown in Figure 39 and 40..
It can be concluded from Table 2 that higher current peaks are obtained under half load condition. Table 2 also depicts that with the low remaining voltage current peaks have higher values.
Sag Type
Sag Magnitude
Half Load
Full load
Sag A
0.1
10.1
6.6
0.5
6.8
3.4
0.8
5.8
2.6
Sag B
0.1
6.6
3.2
0.5
5.84
2.92
0.8
3.38
1.96
Sag C Sag D
0.1
9.85
4.92
0.5
6.48
3.24
0.8
4.45
2.34
Sag E Sag F Sag G
0.1
7.44
6.2
0.5
4.62
2.65
0.8
3.44
2.1
Table 3: Comparison of torque peaks under different loading conditions
Table 4.3 depicted that maximum torque peaks are obtained under balanced sag conditions. It is also observed that higher torque peaks are obtained under half load condition in comparison of full load condition.
Sag Type
Sag Magnitude
Half Load Condition
Full load condition
Sag A
0.1
25
25
0.5
9.38
9.38
0.8
3.82
2.79
Sag B
0.1
6.69
6.69
0.5
3.8
3.8
0.8
2.6
2.06
Sag C Sag D
0.1
22.21
22.2
0.5
5.51
5.5
0.8
3.48
2.6
Sag E Sag F Sag G
0.1
16.47
25
0.5
4.95
5.7
0.8
2.05
2.65
Table 4: Comparison of speed loss peaks under different loading conditions
[6]. Gupta, S. and Srivastava, A. 2019. Effect of Point of Sag Initiation on Performance of Induction Machine. International Journal of Research and Scientific Innovation Volume VI, Issue XI, November 2019 [7]. Melhorn, C. J. 1998. Voltage Sags: Their Impact on the Utility and Industrial Customers. IEEE Transactions on Industry Applications. 34(3): 549-558. [8]. Pedra, J., Corcoles, F and Suelves, F. J.. Effects of balanced and unbalanced voltage sags on VSI-fed adjustable-speed drives. IEEE Transactions on Power Delivery. 20(1): 224-233, 2005. [9]. Sarmiento, H. G., Estrada, E. 1994. A Voltage Sag Study in an Industry with Adjustable Speed Drives. In: Industrial and Commercial Power Systems Technical Conference, Irvine, CA, USA, pp 85-89.Table 4 shows that loading has almost negligible effect on the speed loss of the induction motor for Sag A, Sag B sag C and sag D. But during sag E,F and G motor has higher speed loss under full load condition in comparison to half load condition.
-
CONCLUSION:
The effect of loading conditions on the performance of induction motor has been studied under various voltage sag conditions. For the study current peaks, torque peaks and speed loss have been considered as the parameters. Higher current and torque peaks were observed under half load condition in comparison to full load condition. But speed loss was higher for full load condition in comparison of half load condition in case of sag D,E and F, whereas in case of sag A,B,C and D there was no effect of loading on the performance of induction motor.
REFERENCES
[1]. Bollen, M.. Understanding power quality problems: Voltage sags and interruptions, 2nd edition, Wiley – IEEE Press, New York, 2000. [2]. Bollen,M. H. J. Voltage recovery after unbalanced and balanced voltage dips in three-phase systems, IEEE Trans. Power Delivery, vol. 18, pp. 13761381, Oct. 2003. [3]. Corcols, F and Pedra, J. Algorithm for the study of voltage sags on induction machines, IEEE Trans. Energy Conversion, vol. 14, pp. 959968, Dec. 1999. [4]. Dougherty, J.G and Stebbins, W.L. 1997. Power Quality: A Utility and Industry Perspective. In: Annual Textile, Fiber & Film Industry Technical Conference, Greenville, SC, USA, pp 5-10. [5]. Gosbell, V.J., Perera, B.S.P and Doulai, P. 1996. Power Quality Challenges and Solutions. In: Annual Conference of the Electricity Supply Engineer's Association, Sydney, pp 32-38.