
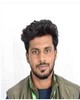
- Open Access
- Authors : Mohammed Mujtaba Ul Haq , Uma Shankar Yaligar
- Paper ID : IJERTV11IS120036
- Volume & Issue : Volume 11, Issue 12 (December 2022)
- Published (First Online): 12-12-2022
- ISSN (Online) : 2278-0181
- Publisher Name : IJERT
- License:
This work is licensed under a Creative Commons Attribution 4.0 International License
Study On Flexural Behaviour of Deck Slab using GFRP Bars
Mohammed Mujtaba Ajaz Ul Haq [1]
Guided by: Professor Uma Shankar Yaligar [2]
Department of Civil Engineering, Guru Nanak Dev Engineering College, Bidar,585401, INDIA
Abstract To meet the needs of modern infrastructure, new innovative materials and technologies have started their way in the construction industry. Any technology or material has its limitations with structures became older and with increasing bar corrosion, older buildings began to demand extra retrofits to increase their durability and life. Recent studies suggest that glass fibers may help replace cement in the concrete industry. Glass fiber has very good Cementous properties, so they can be used as an alternative to cement. Cement production with large amounts of carbon dioxide gas is not good for the environment, so replacing cement with glass fibers has a positive effect on the environment. Now the glass industry is facing a problem related to glass waste. This study is beneficial to both industries. Traditional steel bars used in RCC jobs are slowly being replaced with glass fiber reinforced polymer (GFRP) bar. This large change in construction training is due to the high strength, corrosion resistance, durability and good visibility of conventional steel rods in proportion to the weight of the GRRP. However, due to the linear stress strain behavior of GFRP, they are prone tosudden and brittle failures, thereby strengthening the fiber to provide structural protection. In the present study, a review was conducted to discuss aspects of the GFRP bars in RC members.
Keywords Glass fiber, Cementous, Reinforced Polymer
1.INTRODUCTION
Bridges are adversely have been adversely affected as they are continuously subjected to significant harsh environmental and loading conditions. The environmental conditions include excessive de-icing slat, freeze-thaw cycles, wet-dry cycles, and fluctuation oftemperature. In addition being exposed to weather, bridge structures in India are also generally located in aggressive environments such as marine locations and inland water crossings. The Cracks formed in concrete build routes for the agents of the aggressive environments to reach the reinforcing and/or pre-stressing steel and begin the corrosive oxidation process. The loading conditions effects rise mainly from the ever-increasing traffic loads and volumes. Due to the dual effects of the reinforcement corrosion and the traffic loads, many concrete bridge structures reduced the capacity of a Reinforced concrete (RC) elements through several mechanisms such as loss of the area of steel reinforcement section, the loss of concrete section as a result of longitudinal cracking and spalling of concrete, and a reduction in the bond between the steel reinforcement and concrete.Repair of these bridges constitutes a major challenge when measured in terms of rehabilitation cost and traffic disruption. It was reported that India loses 5-7% of GDP due to corrosion problems.Since
Glass FRP isless expensive than other kinds of FRP (Carbon Aramidand Basalt), Glass FRP composite reinforcement (GFRP, commonly, consists of glass fibers impregnated in a resin)is more attractive to the infrastructure application sand the construction industry. From numerous studies from literature on GFRP reinforced RC elements, it was reported that GFRP reinforced RC elements fail due to de-bonding of GFRP bar and Punching shear failure in deck slabs. Hence, there is a necessity to improve the bond strength and prevent punching shear failure in deck slab. Therefore, this research is intended to study the performance of concrete bridge deck slabs reinforced with GFRP bars under fatigue loads by improving strength.
II.GFRP PROPERTIES
The basic components used to make the GFRP bar are glass-fiber filament and resin matrix, usually polyester resin. These glass- fiber filaments are similar to those obtained by mixing. GFRC sheets and members directly into the concrete mix. Glass-fibers intended for GFRC purposes have a special alkali-resistant coating on their surface. These strands have exceptional tensile strength and they are the load-bearing parts of the bar. Matrix or polyester resin has been introduced as a binding agent to initiate dimensional stability and hold fibers together.
-
Tensile strength:
GFRP bars are anisotropic due to the origin of the fibers, which are fixed on the longitudinal axis. It has high tensile strength (500-1200 MPa) compared to steel rods (250-550 MPa). Their strength is controlled by their diameter and is inversely related to it. This is due to the phenomenon of "cut- log".
-
Compressive strength:
GFRP rebars are very fragile due to the origin of the fibers and are not suitable for use in compression members. However, for most applications GFRP bars are considered morefundamental than compressive strength. The compressive strength of GFRP bars was found to be 40-60% of its tensile strength.
-
Creep and Fatigue:
It has been observed and reported that the final stress caused by creep is approximately 3% of the initial elastic stress(Ehsani, 1993). Fatigue of GFRP bars is generally lower compared to steel rods.
-
Weight:
Specifications |
|
Specific weight (kg/m3) |
910 |
Yarn length (m) |
0.018 |
Electrical conductivity |
Low |
Acid and salt resistance |
High |
Melting point |
162°C |
gnition point |
593 °C |
Heat conductivity |
Low |
Alkali resistance |
Alkali proof |
Tensile strength (MPa) |
300-400 |
Modulus of elasticity (MPa) |
4000 |
Due to the fibrous origin, GFRP bars are found to be lighter than steel rods, allowing them to be easily maintained, stored and transported.
III.OBJECTIVES
-
Investigating the behavior of bridge deck slabs reinforced with GFRP bars with addition of polypropylene fibers under cyclic loading.
-
Optimizing the design of deck slabs through investigating the different reinforcement ratios and configurations.
-
To develop guidelines for design and construction of Deck slab reinforced with FRP bars.
-
Comparison of different national code provisions for the design of GFRP RC bridge deck slabs.
-
Developing an analytical model to predict the fatigue life of GFRP RC bridge deck slabs.
6.Reinforcement
Table 1
IV.EXPERIMENTAL DETAILS
-
Materials used in Construction:
-
Cement
Ordinary Portland Cement (OPC) of 53 grade will be used in the preparation of concrete mix. OPC 53 Grade cement is conform to BIS specification IS: 12269-1987 with a designed strength for 28 days being a minimum of 53 MPa or 530 kg/cm2 . 53 Grade OPC provides high strength and durability to structures because of its optimum particle size distribution and superior crystallized structure.
-
Sand
Local River Sand will be used to fill in the spaces left between the large coarse aggregate and to lock the larger pieces together. Sand helps in reducing the quantity of cement paste required and decreases the amount of shrinkage that could occur.
-
Coarse Aggregate
Locally available coarse aggregate ill be used in mix, whichforms the major body of concrete. The aggregates contribute to the overall strength of the concrete by increasing density.
4.Water
Water for mixing and curing concrete shall be clean, fresh water taken from the public supply.
5.Propylene fibers
Technical properties of the polypropylene fiber used are presented in Table 1
Two types of reinforcing bars will be used in this study; sand coated GFRP rods with warping of Mild steel wires and HYSD grade Fe 550 bars. The GFRP bars are manufactured by combining the pultrusion process with an inline coating process for the outside sand surface. The mechanical properties of the GFRP and steel were obtained from slandered tests, which were carried according to IS and ACI codes.Table 2 summarizes the mechanical properties of the reinforcing materials used in this research.Table 3 summarizes the reinforcement detailsof the five test deck slab prototypes.
Bar type
Bar diameter (mm)
Bar area (mm2)
Modulas of Elasticity(Gpa)
Ultimate Strength(Mpa)
GFRP
10
78.54
53
1028
13
132.74
56
738
Steel
10
78.54
200
585
Table 2
Slab
Bar type
Transverse direction
Longitudinal direction
Bottom
Top
Bottom
Top
S0
Steel bar
10 mm
@ 300
c/c
10 mm
@ 300
c/c
10 mm
@ 300
c/c
10 mm
@ 300
c/c
S1
GFRP(0.10%)
10 mm
@300
c/c
10 mm
@ 300
c/c
10 mm
@ 300
c/c
10 mm
@ 300
c/c
S2
GFRP(0.15%)
10 mm
@ 205
c/c
10 mm
@ 300
c/c
10 mm
@ 205
c/c
10 mm
@ 205
c/c
S3
GFRP(0.20%)
10 mm
@ 155
c/c
10 mm
@ 300
c/c
10 mm
@ 155
c/c
10 mm
@ 155
c/c
S4
GFRP(0.25%)
10 mm
@ 120
c/c
10 mm
@ 300
c/c
10 mm
@ 120
c/c
10 mm
@ 120
c/c
Table 3
-
-
Tests Undergone
-
Pull out Test
After the specimens curing for 28 days, the pullout tests,referring to the ASTM D7913/D7913M-14 criterion, will be conductedon a loading device. The relative slipvalue between the FRP bars and concrete will be recorded by a displacementmeter having a precision of ± 0.01 mm that was placed at the free-end of the FRP bars. The pull-out force was collected by a force sensor that was set at the loaded end of the FPR bars. The pull-out force was applied to the FRP bars through a displacement control program with a speed of
1.2 mm/min. When the slippage value of the FRP bars at the free-end reached 3 mm orthe FRP bars was fractured, the applied load was terminated.The applied pull-out load and the bar slippage were recorded automatically throughout the test. The test was stopped when no more load could be carried by the bar.
-
Flexure Test
In this test set-up, the deck slabs are supported over their longitudinal edges on two built up steel main girders. The built-up section consists of top and bottom flanges. The size of the girders will be adequate for resisting maximum applied load without exceeding the permissible stress and deflection. The main girders will be spaced at 2.0 m centre to centre. Another two steel beams spaced at 3.0m in longitudinal direction will be used to support the main Girders. The load will transferred to the laboratory strong floor through four steel columns at the corners.In real bridges, the deck slab acts compositely with supporting girders and are restrained against rotations and displacement through shear connectors and continuity effects. To simulate this action, the deck slab prototypes will be tied to the two main steel girders through high strength bolts.All the deck slabs will be tested up to failure under either monotonic or cyclic loading using one concentrated load at the centre of the clear supported span, 2000mm. This load will be applied through a 75 mm thick steel plate that measures 230 x 510 mm. These dimensions simulate the footprint of the standard Class 70R Wheeled, as specified by clause 204.1.1 in the IRC: 6-2017. A 500 kN capacity actuator will be used to apply the cyclic loading. It is monitored by a computer to apply the programmed fatigue loads in a load control mode.For each slab, several electrical strain gauges will be used to measure the strains in reinforcing bars and at the top surface of the deck slab around the loaded area. Also many linear variable displacement
transducers (LVDTs) will be installed to measure the deflections at the different locations of the deck slabs as well as crack widths..
A data acquisition system will be used record the readings of the strain gauges, LVDTs, and the load cell.
Code |
Ultimate load (kN) |
Avg. load (kN) |
Ultimate Displacement (m) |
Avg. displacement (m) |
Energy consumption (kN.m) |
Avg. Energy consu- mption capacity (kN.m) |
GFRPS-1 |
75.4 |
80.97 |
0.058 |
0.0605 |
4.03295 |
4.07471 |
GFRPS-2 |
86.55 |
0.061 |
4.11647 |
|||
GFRPS- F |
81.5 |
81.5 |
0.074 |
0.074 |
5.60647 |
5.60647 |
SS-1 |
55.5 |
0.086 |
4.43293 |
|||
SS-2 |
50.65 |
53.07 |
0.083 |
0.0845 |
3.91 |
4.17146 |
V.RESULT
Table 4
VI.REFERENCES
[1] Ali F.Al-Khafaji,john j.Myers;hayder H. Alghazali. evaluation of bond performance of glass fiber rebars embedded in sustainable concrete journal of cleaner production,28,2020. [2] EL-salakawy,E.F.,B.benmokrane,and F.Biere.glass frp composite bars for concrete bridge barriers.sci.Eng.compos.mater.12(3):167- 192.2005. [3] Mohamed , H., and B.Benmokrane. Design and performance of reinforced concrete water chlorination tank totally reinforced with GFRP bars:Case study . J.compos.constr.18(1)2014:05013001 [4] EL- Ragaby A . Fatigue behaviour of concrete bridge deck slabs reinforced with Glass FRP reinforcing bars. Ph.D. Thesis department of civil engineering, University de Sherbrooke,Quebec; 2007.171p. [5] EL-Gamal S . Finite Element Analysis of concrete bridge Decks Reinforced with Fiber reinforced polymer bars. Journal of engineering research 2014 ;11(1):49-62. [6] Alsayed,S.H.,Al- Salloum ,Y.A., Almusallam, T. H ., 2000.performance of glass fiber reinforced plastic bars as a reinforcing material for concrete structures . Compos .B Eng. 31(6-7),555-567. [7] Zemou r ,N., Asadian , A., Ahmed , E.A ., benmokrane ,B.,khayat,K.H., 2019. Experimental study on splice strength of glass fiber reinforced polymer reinforcing bars innormal and selfconsolidating concrete .ACI Mater .j.116(3).