
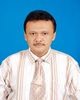
- Open Access
- Authors : Joko Susetyo , Imam Sodikin , Abdussalam
- Paper ID : IJERTV10IS100150
- Volume & Issue : Volume 10, Issue 10 (October 2021)
- Published (First Online): 02-11-2021
- ISSN (Online) : 2278-0181
- Publisher Name : IJERT
- License:
This work is licensed under a Creative Commons Attribution 4.0 International License
Supplier Performance Evaluation based on Vendor Performance Indicator and Taguchi Loss Function Method At Pt. Mandiri International Jogja
Joko Susetyo1, Imam Sodikin2, Abdussalam2
1, 2, 3Jurusan Teknik Industri, Fakultas Teknologi Industri, Institut Sains & Teknologi AKPRIND Yogyakarta
Jl. Kalisahak 28, Balapan Yogyakarta 55222
Abstract:- Mandiri Jogja Internasional company has 3 suppliers in the fulfillment of leather raw materials, each supplier has different characteristics, ranging from price, delivery accuracy and the accuracy of the number of goods and quality. Frequent occurrence of stock outs is due to the supplier being less responsive in fulfilling requests for procurement of leather raw materials. This causes excess quantity or quantity in production (overproduction), excessive inventory (excess inventory) and also waste in waiting time for the production process (waiting). Therefore, the selection of the right supplier can provide benefits for the company so that the price, delivery accuracy and quantity of goods, as well as quality can be maintained properly. This study aims to determine the best supplier by selecting relatively based on predetermined criteria. The method used is VPI to determine the target value and reality of each supplier based on sub-criteria. The next approach uses the AHP method, which is used to calculate the quality value. Then to determine the value of the loss, the Taguchi Loss Function method is used. The final approach with the Traffic Light System aims to evaluate each supplier. The results of processing with VPI obtained supplier scores from Magetan Widi Leather, and UD. Ardho amounted to 85.4%, 87%, and 83.3% with a loss value of Rp 217,670,455, Rp 137,035,411, and Rp. 264,109,266. The selection of the best supplier of leather raw materials gets the highest value and the lowest loss value is the Widi Leather supplier with a performance achieved of 82%, while for other suppliers it is 73%. So the company must increase the capacity for ordering raw materials and extend cooperation with suppliers of Widi Leather and reduce the capacity for ordering with suppliers of Magetan and UD. Ardho so that the value of losses from both suppliers can be reduced optimally.
Key Words: VPI, AHP, Loss Function, Traffic Light System, Scoring System
Abstrak
Perusahaan Mandiri Jogja Internasional mempunyai 3 supplier dalam pemenuhan bahan baku kulit, masing-masing supplier mempunyai karakteristik yang berbeda-beda, mulai dari segi harga, ketepatan pengiriman dan ketepatan jumlah barang serta kualitas. Sering terjadinya stock out disebabkan karena pihak supplier kurang responsif dalam pemenuhan permintaan pengadaan bahan baku kulit. Hal tersebut menyebabkan terjadinya kelebihan kuantitas atau jumlah dalam produksi (overproduction), persediaan yang berlebihan (excess Inventory) dan juga pemborosan dalam waktu menunggu jalannya proses produksi (waiting). Oleh karena itu pemilihan supplier yang tepat dapat memberikan keuntungan bagi perusahaan agar harga, ketepatan pengiriman dan jumlah barang, serta kualitas dapat terjaga dengan baik. Kajian ini bertujuan untuk menentukan supplier terbaik dengan menyeleksi secara relatif berdasarkan kriteria yang sudah ditentukan. Metode yang digunakan yaitu VPI untuk menentukan nilai target dan realita dari setiap supplier berdasarkan subkriteria. Pendekatan berikutnya menggunakan metode AHP, digunakan untuk menghitung nilai bobot. Kemudian untuk menentukan nilai kerugian digunakan metode Taguchi Loss Function. Pendekatan terakhir dengan Traffic Light System bertujuan untuk mengevaluasi masing-masing supplier. Hasil pengolahan dengan VPI diperoleh nilai score supplier dari Magetan Widi Leather, dan UD. Ardho sebesar 85,4%, 87%, dan 83,3% dengan nilai kerugian sebesar Rp 217.670.455, Rp 137.035.411, dan Rp. 264.109.266. Pemilihan supplier terbaik bahan baku kulit mendapatkan nilai tertinggi dan nilai kerugian terendah adalah supplier Widi Leather dengan kinerja tercapai sebesar 82%, sedangkan untuk supplier lainnya sebesar 73%. Jadi perusahaan harus meningkatkan kapasitas pemesanan bahan baku dan memperpanjang kerja sama pada supplier Widi Leather dan menurunkan kapasitas pemesanan pada supplier Magetan dan UD. Ardho agar nilai kerugian dari kedua supplier bisa diturunkan secara optimal.
Kata Kunci: VPI, AHP, Loss Function, Traffic Light System, Scoring System
-
INTRODUCTION
Suppliers play an important role in improving the company's performance in building supply chains. If the supplier is less responsive in meeting the demand for raw material procurement, the result will be a stock out and if the lead time from the supplier is long, it will disrupt the production process, causing a decrease in the company's products (Chen, 2011).
PT. Mandiri Jogja Internasional is one of leather craft companies in Yogyakarta, which manufactures various kinds of leather bags, leather shoes, leather wallets, and other leather accessories with the main raw material being leather. Product marketing has spread into European countries such as Amsterdam, the Netherlands and Asian regions such as Japan. Companies are always required to maintain product quality so that products are always accepted in national and international markets. In the last 3 months the company experienced a decline in production. In January 2019 the number of products was 2370 products, in February 2019 the number of products was 2150 products and in March 2019 the number of products was 2050 products. The decline in this product was due to a decrease in demand from consumers and a decrease in delivery delays from suppliers in providing leather raw materials. According to Saunder in the research journal Prabowo, R (2013) evaluating suppliers should be based on the supplier's ability to cooperate with the company, a long term relationship is needed because it will foster mutual trust and reliability, things like that will certainly benefit both sides. According to Dobler (1990), supplier selection aims to obtain material sources with the desired quality, quantity, time, price and service as well as the required technical assistance. Supplier selection is an important factor in the supply chain because it is one of the company's strategies to be able to compete with other companies in terms of customer satisfaction and also to improve or maintain the company's service level in meeting consumer demand.
-
MATERIALS AND METHODS
Vendor Performance Indicator
Vendor Performance Indicator (VPI) is a management system for measuring supplier performance that is carried out comprehensively and according to company requirements and can show the performance of suppliers. To ensure the stability of production from shortage of raw materials, the company has more than one supplier for each item of goods, therefore the Vendor Performance Indicator is used to evaluate the performance of each supplier.
Determination of supplier selection, the thing that is considered is the determination of the criteria needed to assess the capabilities and performance of the supplier in producing the desired unit. The term supplier selection criteria in the industrial world is currently better known as Vendor Performance Indicators (VPI). The following is the QCDFR framework from Vendor Performance Indicators (VPI) according to the research journal Rochmoeljati (2012), including Quality, Cost, Delivery, Flexibility, and Responsiveness.
Analytical Hierarchy Process (AHP)
The Analytical Hierarchy Process is a decision support model developed by Thomas L. Saaty. This decision support model will describe complex multi-factor or multi-criteria problems into a hierarchy, according to Saaty in Supriadi et al (2016)'s book. Hierarchy is defined as a representation of a complex problem in a multi-level structure where the first level is the goal, followed by the level of factors, criteria, sub-criteria, and so on down to the last level of alternatives. With a hierarchy, a complex problem can be broken down into groups which are then arranged into a hierarchical form so that the problem will appear more structured and systematic. According to Dweiri (2016) AHP as an MCDM (Multi Criteria Decision Making) method provides a comprehensive framework for solving decision-making problems by quantifying subjective judgments and aims to integrate different steps into one overall assessment to determine supplier selection and evaluation decisions.
Tahapan AHP
The steps in the Analytical Hierarchy Process Method are as follows:
-
Determine the types of criteria used.
-
Develop a hierarchical structure.
-
Arrange these criteria in the form of a paired matrix.
Description:
= , i, j = 1,2,n …………………………………………………………………………………………… (1)
= The value of the quality comparison of the i and j criteria.
= The quality for the i-th criterion (row).
= Quality for the j-th criterion (column).
= Number of criteria compared.
-
Geometric Mean
= (
1
………………………………………………………………………………… (2)
Description:
1
2
)
= Geometric Mean (Nilai rata-rata).
= The value of the quality comparison of the i and j criteria.
= Total scores of respondents
-
Normalization
= ……………………………………………………………………………………………………………….(3)
Description:
= The value of the quality comparison of the i and j criteria.
-
Determine priority weight
= ……………………………………………………………………………………………………………….. (4)
Description:
= Priority quality.
= Number of rows in each i-th criterion.
= Number of criteria compared.
-
Calculating vector values
Description:
= Geometric Mean.
= Priority quality.
-
Vector value consistency
Description:
= Result vector.
= Priority quality.
= ( ) …………………………………………………………………………………. (5)
= [ ] …………………………………………………………………………………………………………….. (6)
-
Calculating of lamda value max (eigen value)
= …………………………………………………………………………………………………………………. (7)
Description:
= Lamda value max (eigen value).
= value of D.
= Number of criteria compared.
-
Calculating concistency index (CI)
CI = ……………………………………………………………………………………………………………… (8)
1
Description:
CI = Consistency index.
= Lamda value max (eigen value).
= Number of criteria compared.
-
Calculating concintency ratio
Description:
CR = Consistency ratio. CI = Consistency index. RI = Random index.
CR = ………………………………………………………………………………………………………………… (9)
The comparison matrix is acceptable if the value of the consistency ratio (CR) 0,1.
Taguchi Loss Function
According to Taguchi, in the research of the journal Sari, D. P and Kusumo, S. A, (2011), there are 2 general aspects of quality, namely the quality of design and the quality of fit. Design quality is an intentional variation in the quality level of a product, while fit quality is how well the product conforms to the specifications and allowances required by the design.
Quality Loss Function
The calculation of the amount of loss for the Taguchi company uses the concept of Quality Loss Function (QLF). QLF is a mathematical model that relates quality loss in value for money because quality deviates from the desired target specification. Loss in question is maintenance costs, failure costs, adverse effects on the environment such as pollution or costs that are too large in producing products. The quality approach according to Taguchi is a new innovation in the field of quality. According to Phillip J. R (1995) in general there are three quality loss functions specifically for the sample, namely:
-
Smaller the Better
Fig. 1 Smaller the Better
Figure 1 has continuous and non-negative quality characteristics that have a value from 0 to where the desired defect value is 0. So the signal to noise ratio can be calculated as follows:
Loss for an individual part
= (2) ………………………………………………………………………………………………………………… (10)
Average loss part in a distribution ( )
= [2 + (2)] ………………………………………………………………………………………………………. (11)
Description: L = Loss
= Cost consequences y = Measured value
2= Distribution variance
= Average measured value
-
Larger the better
Fig. 2 Larger the Better
Figure 2 has a continuous and non-negative quality characteristic that has a value of 0 until the expected target value is other than 0 or in other words has the largest possible value. So the signal to noise ratio can be calculated by the formula:
Loss for an individual part
= ( 1 )………………………………………………………………………………………………………………….. (12)
2
2
2
Average loss part in a distribution ( )
= [ 1 ] [1 + (3 )] ………………………………………………………………………………………………… (13)
Description: L = Loss
= Cost consequences y = Measured value
2= Distribution variance
= Average measured value
-
Nominal the Best
2
2
Fig. 3 Nominal the Best
Figure 3 has continuous and non-negative quality characteristics that have values from 0 to ~ where the expected target value is other than 0 and is a finite number. So the signal to noise ratio can be calculated by the formula:
Loss for an individual part
= ( )2 ………………………………………………………………………………………………………….. (14)
Average loss part in a distribution ( )
= [2 + ( )2] ……………………………………………………………………………………………….. (15)
Description: L = Loss
= Cost consequences y = Measured value
2= Distribution variance
= Average measured value m = target value
Loss Function
=1
=1
Calculating the loss function value of each supplier evaluation criteria, in the first calculation process stage, namely choosing the formula in equation (10) to (15). The formula used is according to the characteristics and deviation data from each criterion. This is done to reduce miscalculation of the losses incurred by each supplier. The next stage is to determine the value of k or the value of the cost consequences of each criterion. Th last stage is to do the calculation so that the loss value of each supplier can be known by the equation formula below.
Description:
Loss 1 = Total loss value
Loss (j) =
………………………………………………………………………………………………….. (16)
J = Supplier A, Supplier B, up to Supplier n
= Quality of AHP
= Value of loss function
Scorring System
Scoring system is carried out to determine the achievement value of the targets that have been set for each performance indicator, as for several measurements of the score, namely:
-
VPI Scoring
VPI scoring is carried out in accordance with the supplier evaluation system hierarchy. The calculation of the VPI score uses several types of provisions, as for the types of provisions, namely:
-
Smaller is better because the smaller the value of the provisions, the better. The score calculation for smaller is better is:
Description:
Score of VPI =
………………………………………………………………………… (17)
Score of VPI = score of vendor performance indicator. Realization data = factual data that was got by the company. Target data = Limits of companys decision.
-
Larger is better because the greater the value of the provisions, the better. The score calculation for larger is better is:
Score of VPI = …………………………………………………………………………………. (18)
Description:
Score of VPI = score of vendor performance indicator. Data realisasi = factual data that was got by the company. Data target = Limits of companys decision.
-
-
Scoring Criteria
Scoring criteria is carried out based on the evaluation hierarchy in the supplier evaluation system. The criterion score is obtained from the number of multiplications between the VPI qualifying value and the VPI score value in the same criteria. The calculation of the criteria score is:
Score criteria = ( VPI x Wi VPI) ……………………………………………………………………….. (19)
Description:
Score criteria = score of criteria.
Score VPI = score of vendor performance indicator.
Wi VPI = score of priority quality of vendor performance indicator.
-
Scoring of Supplier
Supplier scoring is carried out based on the evaluation hierarchy in the supplier evaluation system. The supplier score has a formulation by adding up the multiplication between the qualifying criteria and the criteria score values. The calculation of the supplier score is:
Score of Supplier = ( riteria x Score of quality criteria)…………………………………… (20)
Description:
Score of supplier = score of supplier. Score kriteria = score of criteria.
Wi VPI = Score of priority quality of criteria.
Traffic Light System
Traffic light system is closely related to the scoring system. The traffic light system serves as a sign of whether the score of a performance indicator requires an improvement or not. Indicators of this traffic light system are represented by several colors as follows:
a) A green color with a threshold of more than 90% means that the achievement of a performance indicator has been achieved. b)Yellow color with a threshold between 60% to 90% means that the achievement of a performance indicator has not been
achieved, even though the value is close to the target. So the management must be careful with the various possibilities.
-
Red color with a threshold of less than 60% means that the achievement of a performance indicator is really below the target that has been set and requires immediate improvement.
-
-
RESULT AND DISCUSSION
Analysis of AHP's Quality Value Results
Value of Criteria Quality
Value of Criteria Quality
Based on data processing using the Analytical Hierarchy Process method, the output results obtained from the quality values of 3 respondents from the criteria and Vendor Performance Indicators. The following are the output results of the qualified criteria and Vendor Performance Indicators.
0.4
0.32
0.4
0.32
0.3
0.22
0.3
0.22
0.2
0.13 0.12 0.13
0.2
0.13 0.12 0.13
0.1
0
Criteria of Supplier Evaluation
Quality Cost Delivery Flexibility Responsiveness
0.1
0
Criteria of Supplier Evaluation
Quality Cost Delivery Flexibility Responsiveness
Fig. 4 Score of Criteria Quality
The graph of the value of the criteria qualifies is shown in Figure 4 where (x) shows the criteria for each supplier and the value (y) shows the qualifying value of each criterion. The criteria that get the first position are based on 3 respondents who are authorized in determining leather raw materials, namely the Cost criterion of 0.32, the second is the Quality criterion of 0.22, the third is the Delivery criterion of 0.13, the fourth is the Responsiveness responsibility criterion of 0.13, and the fifth is the ease of Flexibility of 0.12.
0.8
0.7
0.73
0.8
0.7
0.73
0.1
0.1
0
0.1
Vendor Performance Indicator (VPI)
0
0.1
Vendor Performance Indicator (VPI)
Warna kulit
Tebal kulit
Tekstur kulit
Warna kulit
Tebal kulit
Tekstur kulit
Harga Cara pembayaran Kuantitas
Pengiriman Perubahan kuantitas Perubahan waktu kirim Respon masalah Jaminan
Harga Cara pembayaran Kuantitas
Pengiriman Perubahan kuantitas Perubahan waktu kirim Respon masalah Jaminan
0.7
0.7
0.7
0.7
0.6
0.6
0.64
0.64
0.5
0.5
0.59
0.59
0.4
0.3
0.4
0.3
0.36
0.36
0.31
0.31
0.3 0.3
0.3 0.3
0.2
0.2
0.27
0.27
VPI Value of Quality
VPI Value of Quality
Fig. 5 Vendor Performance Indicator Quality Value
The graph of the VPI qualifying results is shown in Figure 5, where (x) shows the VPI of each criterion and (y) shows the qualified value of each VPI. The Cost criterion is the first very important criterion because the company is very concerned about the price of leather raw materials. The lower the cost of leather raw materials, the higher the profit obtained by the company. The result of the quality value VPI_5 (price) is 0.73. Meanwhile, VPI_6 (payment method) is 0.27. Quality criteria is the second important thing in determining leather raw materials. The result of the quality value of VPI_1 (skin color) is 0.59. Furthermore, VPI_3 (suitability of skin texture) takes the second important role in quality because it will attract potential company customers by 0.31. Then VPI_2 (skin thickness suitability) takes the third important role of 0.10. The
delivery criteria has the third important criterion for the company because the accuracy of delivery will make production run smoothly. The results of the weight value VPI _6 (quantity accuracy) of 0.7 and VPI _7 (timeliness) of 0.3. The
responsibility criteria (Responsiveness) indicate that the responsibility of the supplier in the matter has an important role for the company. According to research in the journal Khoiro (2015) providing guarantees for companies ordering raw materials there must be an agreement between companies and suppliers because if there is a deviation with the goods ordered, they will provide a guarantee, namely the replacement of goods. The result of the quality value of VPI_10 is 0.64 and the result of the qualified value of VPI_11 (providing goods guarantee) is 0.36. The convenience criterion is the last criterion for the company. This ca be seen in the results which show that the quality value of VPI_9 (time change request) is 0.7 and the quality value of VPI
_8 (quantity change request) is 0.3.
Loss Result Analysis
The results of data processing using the Taguchi Loss Function method, the output results obtained from the results of differences in supplier quality and supplier quality costs. The following is the output of the total loss value of the three suppliers of leather raw materials in Figure 6.
300000000
Rp 264.109.266
Suplier Total Loss (Rp)
Suplier Total Loss (Rp)
250000000 Rp 217.670.455
200000000
Supplier A "Magetan"
150000000
100000000
50000000
0
Rp 137.035.411
Supplier B "Widi Leather"
Supplier C "UD. Ardho"
Supplier of Leather Raw Material
Fig. 6 Total Value of Supplier Losses
The graph of the total loss of each supplier is shown in Figure 6, where (x) shows the name of each supplier and (y) shows the total loss of each supplier within 6 months. The results show that the supplier who has the highest total value of the first loss to the company is supplier C "UD. Ardo amounted to Rp 264,109,266, supplier A Magetan was the second highest supplier at Rp 217,670,455, and the supplier with the lowest total loss value to the company was supplier B Widi Leather amounting to Rp 137,035,411.
Supplier Score Result Analysis
84
84
85.4
85.4
Supplier A
"Magetan"
Supplier B "Widi Leather"
Supplier C "UD. Ardho"
Supplier A
"Magetan"
Supplier B "Widi Leather"
Supplier C "UD. Ardho"
Supplier score (%)
Supplier score (%)
Based on the results of data processing using the previous Vendor Performance Indicator method in graph 2, the output results obtained from the VPI score and criteria score. The following is the output result of the total score from the three suppliers of leather raw materials in Figure 7.
88
86
87
88
86
87
Supplier of Leather Raw Material
Supplier of Leather Raw Material
82
82
83.3
83.3
80
80
Fig. 7 Total Score From Each Supplier
The graph of the total score is shown in Figure 7, where (x) shows that the name of each supplier and (y) shows the percentage of the score. The value of supplier B Widi Leather gets the highest score and ranks first with a value of 87%. Then supplier A "Magetan" ranks second with a value of 85.4%. Finally supplier C UD. Ardo ranks third with a score of 83.3%.
The results of calculating the score from each supplier in Figure 7 show that there is no too significant difference between the three suppliers. This is because the assessment given by the decision maker is subjective. This can be seen from the qualifying of the criteria, where decision makers are more concerned with the cost criteria than the other four criteria, namely quality, delivery, flexibility, and responsiveness. The cost criterion is considered very important from decision makers because the company always needs raw materials in large quantities to meet the manufacture of leather products, with low costs, the company will be able to minimize expenses.
Traffic Light System Evaluation
Evaluation is carried out as a follow-up to the results of supplier performance measurements based on the Traffic Light System. Supplier A "Magetan" has 8 green indicators and 3 yellow indicators. The green indicators consist of leather texture with a score of 90%, the price of leather raw materials with a score of 97%, payment methods with a score of 100%, the accuracy of the quantity sent with a score of 100%, requests for quantity changes with a score of 100%, changes in delivery time with a score of 100%, response to problems with a score of 100%, and provision of goods guarantees with a score of 100 %. The yellow indicator consists of the suitability of skin color with a score of 70%, suitability of skin thickness with a score of 70%, and delivery time with a score of 83%.
Supplier B "Widi Leather" has 9 green indicators and 2 yellow indicators. Green indicators consist of leather texture with a score of 90%, the price of leather raw materials with a score of 95%, payment methods with a score of 100% , quantity accuracy with a score of 100%, on time delivery with a score of 91%, requests for changes in quantity with a score of 100%, changes in delivery time with a score of 100%, response to problems with a score of 100%, giving guarantee of goods with a score of 100%. The yellow indicator consists of suitability of skin color with a score of 80% and suitability of skin thickness with a score of 80%.
Supplier C "UD. Ardho has 8 green indicators and 3 yellow indicators. Green indicators consist of the price of leather raw materials with a score of 92%, payment methods with a score of 100%, quantity accuracy with a score of 100%, delivery timeliness with a score of 91%, requests for quantity changes with a score of 100%, changes in delivery time with a score of 100%, response to problems with a score of 100% and the provision of goods guarantees with a score of 100%. Yellow indicators consist of suitability of skin color with a score of 80%, suitability of skin thickness with a score of 70% and suitability of skin texture with a score of 60%.
-
CONCLUSION
The results of the analysis of the research discussion can be concluded that the results of the total losses from the three suppliers are Magetan, Widi Leather, and UD. Ardho amounted to Rp 217,670,455, Rp 137,035,411, and Rp 264,109,266 with scores of 85.4%, 87%, and 83.3%. The loss value of each supplier quality difference that experienced a significant difference was found in the delay schedule due to large expenses by the company. The results of the scores from each supplier show that the Widi Leather supplier gets the highest score with the lowest loss value. So the company must increase the capacity for ordering raw materials and extend the cooperation contract with the Widi Leather supplier and reduce the ordering capacity for the Magetan and UD suppliers. Ardho so that the value of losses from both suppliers can be reduced optimally.
REFERENCES
-
Chen, Y.J, 2011, Structured Methodology for Supplier Selection and Evaluation in A Supply Chain, Information Sciences, vol. 181, pp. 1651-1670.
-
Dobler, D.W; Burt, D.N., and Lee Jr., L.,1990, Purchasing and Materials Management, McGraw-Hill.
-
Dweiri. F, Kumar. S, Khan. S, A, and Jain. V, 2016 Designing an integrated AHP based decision support system for supplier selection in automotive industry, Expert Systems with Applications, vol. 62, pp. 273-283.
-
Khoiro, W, 2015, Evaluasi Supplier Bahan Baku Plat Besi Dengan Menggunakan Metode Analytical Hierarchy Process Dan Taguchi Loss Function, jurnal Teknik Industri, vol. 16(12).
-
Phillip, J. R, 1995, Taguchi Techniques for Quality Engineering, United States: McGraw-Hill Education-Europe.
-
Prabowo, R, 2013, Analisa Pemilihan Supplier Polyurethan Dengan Vendor Performance Indicator Berbasis Quality Cost Delivery Flexibility Responsiveness Di PT Sinar Foam Jaya Surabaya, jurnal Teknik Industri, Fakultas Teknologi Industri, Institut Teknologi Adhi Tama Surabaya.
-
Rochmoeljati, R, 2012, Pengukuran Kinerja Supplier Berdasarkan Vendor Performance Indicator Dengan Metode Quality Cost Delivery Flexibility Responsivness, jurnal Teknik Industri, Fakultas Teknologi Industri, UPN Veteran Surabaya.
-
Sari, D. P, dan Kusumo, S. A, 2011, Evaluasi Pemilihan Supplier Terbaik Menggunakan Metode Taguchi Loss Function dan Analytical Hierarchy Process Di PT Indomaju Textindo Kudus, jurnal Teknik Industri, 6(3): 162-167.
-
Supriadi, A dkk, 206, Analytical Hierarchy Process (AHP) Teknik Penentuan Strategi Daya Saing Kerajinan Bordir. Yogyakarta: Deepublish (CV Budi Utama).