
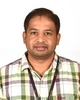
- Open Access
- Authors : Sreharri S, Raghul K.B, Akash S, Thirumurugaveerakumar S
- Paper ID : IJERTV13IS120054
- Volume & Issue : Volume 13, Issue 12 (December 2024)
- Published (First Online): 20-12-2024
- ISSN (Online) : 2278-0181
- Publisher Name : IJERT
- License:
This work is licensed under a Creative Commons Attribution 4.0 International License
Supply Chain Resilience in Industrial Manufacturing
Sreharri S, Raghul K.B, Akash S, Thirumurugaveerakumar S
Department of Mechanical Engineering, Kumaraguru College of Technology, Coimbatore- 641049, Tamil Nadu.
ABSTRACT:
Supply chain resilience has become an essential aspect of industrial production, as disruptions from global crises, natural disasters, and market volatility have highlighted vulnerabilities in traditional supply chains. This study explores strategies to enhance resilience in industrial supply chains, focusing on risk assessment, diversified sourcing, digitalization, and agile response frameworks. Key factors such as predictive analytics, supply chain visibility, and supplier collaboration are evaluated for their roles in mitigating disruptions. The research demonstrates that companies adopting a proactive, flexible approach can significantly reduce downtime, maintain production continuity, and improve adaptability in face of unforeseen challenges. This paper provides a framework for integrating resilience- building practices, encouraging industry stakeholders to invest in long-term supply chain stability, and paving the way for more sustainable, reliable industrial production systems.
Keywords: Supply Chain Resilience, Risk Management, Inventory Optimization, Technology Integration, Metrics
-
INTRODUCTION
Supply chain resilience has emerged as a key priority for industrial production due to the rising frequency and intensity of disruptions in recent years. The complex, interconnected nature of global supply chains means that even minor disruptions can ripple across industries, causing significant production delays and financial losses. As companies strive to meet increasing demands for reliability and sustainability, developing resilient supply chains is essential. This study explores the challenges faced by industrial supply chains, the objectives of enhancing resilience, and the scope of our research in this area.
-
PROBLEMS FACED
Modern supply chains are exposed to numerous risks, both internal and external, which impact industrial production. Major problems include:
-
Global Disruptions: Events such as the COVID-19 pandemic, natural disasters, and geopolitical conflicts have caused widespread supply chain interruptions, halting production and leading to severe shortages and cost spikes.
-
Dependency on Single Sources: Many companies rely heavily on a limited number of suppliers, often based in specific regions, which makes them vulnerable to localized disruptions.
-
Lack of Visibility and Data Integration: Many supply chains still operate with limited transparency, lacking real-time data on inventory levels, supplier health, and demand forecasts, which hampers effective decision-making in times of disruption.
-
Demand Volatility: Rapid changes in consumer demand and market dynamics often strain production capacity, requiring supply chains to be flexible enough to adapt quickly to shifts.
-
-
OBJECTIVES OF THE STUDY
The primary objectives of this study are as follows:
-
Identify Key Strategies for Building Resilience: Examine various approaches, including risk assessment, diversified sourcing, and the use of technology, that enhance supply chain resilience.
-
Analyze the Role of Technology: Investigate how digital tools such as predictive analytics, Internet of Things (IoT), and artificial intelligence (AI) can provide greater visibility and responsiveness.
-
Develop a Framework for Resilient Supply Chains: Propose a comprehensive framework that companies can adopt to strengthen their supply chains, minimize disruptions, and improve their adaptability to changing market conditions.
-
-
SCOPE OF THE STUDY
This study focuses on the industrial production sector, examining a range of industries where supply chain resilience is critical for maintaining operational continuity. By reviewing both theoretical frameworks and practical case studies, we assess how resilience strategies can be integrated at different stages of the supply chain, from raw material sourcing to final distribution. This research also covers emerging technologies and their impact on supply chain management, providing actionable insights for industry stakeholders to build more reliable, sustainable supply chains in the face of future challenges.
-
-
LITERATURE REVIEW
Numerous academic journals have published extensive research addressing the importance of supply chain resilience. Notable journals include the Journal of Supply Chain Management, which focuses on strategies for resilience; Supply Chain Management: An International Journal, highlighting case studies and methodologies; and the International Journal of Production Economics, which explores operational strategies. Additional journals include the Transportation Research Part E, which addresses logistical challenges, and the Journal of Business Logistics, which examines practices that enhance resilience.
Further contributions come from the Supply Chain and Operations Management, the Journal of Operations Management, and the International Journal of Logistics Management, which investigate logistics strategies and their impact on resilience. The Journal of Purchasing and Supply Management discusses procurement strategies, while the Journal of Retailing and Consumer Services emphasizes consumer-centric supply chain strategies. The International Journal of Operations & Production Management offers insights into operational efficiency, and the Journal of Business Research* provides a broader perspective on how supply chain practices affect overall business outcomes. Other relevant journals include the European Journal of Operational Research, which analyses quantitative methods in supply chain management, and the International Journal of Physical Distribution & Logistics Management, focusing on the logistics aspects of supply chain resilience.
Several pivotal articles provide deeper insights into resilience strategies. For instance, "Supply Chain Resilience: A Review and Research Agenda" offers a comprehensive overview of resilience concepts, while "Building Resilience in Supply Chains: Strategies and Methods" discusses approaches like diversification and technology adoption. Articles such as "The Role of Information Technology in Supply Chain Resilience" explore how technological advancements bolster resilience, and "Agility and Resilience in Supply Chains: A Dual Perspective" analyses the interplay between agility and resilience. Furthermore, "Risk Management Strategies in Supply Chains: A Resilience Perspective" emphasises the necessity of integrating risk management into resilience frameworks. Collectively, this body of literature emphasises the multifaceted nature of supply chain resilience, incorporating elements of risk management, technology integration, and strategic planning.
-
STRATEGIES FOR BUILDING RESILIENCE
Building supply chain resilience involves several key strategies. First, risk assessment frameworks are essential for understanding and mitigating vulnerabilities within the supply chain. Organisations must develop comprehensive frameworks to identify potential disruptions and prepre accordingly. The integration of advanced analytics and machine learning in risk assessment enables organisations to predict potential disruptions more accurately, enhancing preparedness.
Supplier diversification is crucial; reducing reliance on a single supplier allows organisations to better navigate disruptions. Establishing a network of diverse suppliers across different geographic locations can mitigate risks associated with regional disruptions. Furthermore, creating strategic alliances with key suppliers fosters collaboration and enhances supply chain visibility.
Inventory optimization techniques play a significant role in building resilience. Implementing Just-In-Time (JIT) practices alongside safety stock calculations helps organisations balance supply and demand effectively. Additionally, utilising demanddriven inventory models can improve responsiveness and minimise excess stock. Advanced analytics can be employed to determine optimal inventory levels based on historical data and market trends.
Collaborative planning and forecasting are vital components of a resilient supply chain. Strengthening communication with suppliers and customers enhances responsiveness and accuracy in meeting demand. Collaborative Demand Planning (CDP) allows organisations to synchronise their forecasts with those of their suppliers, creating a unified approach to managing supply chain fluctuations.
Demand Driven
Models
Strategic
Alliances
Scenario Planning
Collaborative Planning & Forecasting
Inventry optimisation
Supplier Diversification
Risk Assessment Framework
Scenario planning, which prepares organisations for various potential disruptions through strategic foresight, is another vital strategy that ensures operational continuity. By simulating different disruption scenarios, organisations can develop contingency plans that enhance their ability to respond swiftly and effectively.
-
KEY METRICS FOR PERFORMANCE MONITORING
To effectively manage supply chains, organisations must track critical metrics. Lead time, which measures the total duration from order placement to delivery, is essential for production planning and customer satisfaction. Order cycle time, the time between consecutive replenishment orders, ensures timely restocking to prevent stockouts. The Reorder Point (ROP) formula triggers new orders before inventory runs out, while safety stock protects against variability in demand.
ROP = (Demand during lead time) + (Safety stock)
Economic Order Quantity (EOQ) helps balance ordering and holding costs, determining the optimal quantity of inventory to order. Demand forecasting, which predicts future demand, informs production and inventory control strategies. Additionally, fill rate measures customer service performance, calculated as,
Fill Rate = (Orders Filled on Time / Total Orders) × 100
While the inventory turnover ratio assesses inventory efficiency using the formula, Inventory Turnover = COGS / Average Inventory
On-time delivery rate reflects logistics efficiency and is calculated as the percentage of orders delivered on time.Other important metrics include the Cost to Serve (CTS), which assesses the total cost incurred to serve a customer, and the Customer
Satisfaction Index (CSI), measuring how well a company's products and services meet customer expectations. Tracking these metrics enables organisations to identify areas for improvement and ensure a resilient supply chain.
Lead Time
Quantity (EOQ)
Economic Order
Stockout Rate
Holding Cost
Inventory Turnover Ratio
Safety Stock
Reorder Point (ROP)
Order Cycle Time
Qualitative
Quantitative
Forecasting
Consumer Surveys
Sales Force Estimates
Trend Projection
Exponential Smoothing
Delphi Method
Naive Approach
Executive Opinion
Moving Averages
Key Metrics
-
FORECASTING METHODS
-
TYPES OF FORECASTING METHODS
-
Quantitative forecasting
-
Naïve Approach
-
Moving Averages
-
Exponential Smoothing
-
Trend Projection
-
-
Qualitative forecasting
-
Executive Opinion
-
Delphi Method
-
Sales Force Estimates
-
Consumer Surveys
-
-
QUANTITATIVE FORECASTING
-
Naïve Approach
A naive approach is a basic, straightforward way of solving a problem. It typically:
-
Focuses on simplicity: The naive approach uses the most obvious steps to reach a solution, without worrying about efficiency.
-
Ignores complex optimizations: It doesnt involve any advanced techniques to reduce computation time or memory usage.
-
Can be less efficient: Due to its simplicity, a naive approach may be slow or impractical for large problems or datasets.
Example: Suppose you have an unsorted list of numbers and want to find a specific number. A naive approach would be to check each number one by one until you find the target. This is straightforward but inefficient for long lists, as it could involve a lot of unnecessary checks. A more optimized solution might use sorting or data structures like hash tables to improve speed.
Naive approaches are often used as a first step. They provide a functional solution that can later be refined or optimized if needed.
-
MOVING AVERAGES
A moving average is a calculation used to analyze data points by creating a series of averages of different subsets from a complete dataset. It involves taking the average of a fixed number of consecutive data points, moving this window along the data series, and recalculating the average each time.
Moving averages are commonly used in time series data to smooth out short-term fluctuations and highlight longer-term trends or cycles. There are several types, including:
-
Simple Moving Average (SMA): Averages a specific number of recent data points equally.
-
Weighted Moving Average (WMA): Averages data points with more weight given to recent observations.
-
Exponential Moving Average (EMA): Averages data points with exponentially increasing weights, prioritizing more recent values.
Moving averages are widely used in fields like finance, economics, and data analysis to help interpret trends and forecast future data points.
-
-
EXPONENTIAL SMOOTHING
Exponential smoothing is a forecasting technique that applies exponentially decreasing weights to past observations, giving more importance to recent data. Unlike a simple moving average, where each data point in the window has equal weight, exponential smoothing assigns progressively less weight to older data. This makes it highly responsive to recent changes while still incorporating information from the past.
The technique relies on a smoothing factor (often denoted as alpha, ), which controls the rate of decline for the weights. When is close to 1, the model is very responsive to recent changes; when its closer to 0, the model becomes less responsive.
Exponential smoothing is commonly used in time series forecasting, especially in finance, inventory management, and demand forecasting, because it provides a simple yet effective way to make short-term predictions by emphasizing recent trends.
-
TREND PROJECTION
-
-
Trend projection is a forecasting method used to predict future values in a time series by extending a trend from historical data. It assumes that past patterns in the data (like growth or decline trends) will continue into the future. This method is often applied to data that exhibits a consistent direction over time, whether its increasing, decreasing, or following a linear or exponential trend.
Steps in Trend Projection:
-
Analyze the Historical Data: Identify patterns and trends in past data, such as a linear increase or seasonal variations.
-
Fit a Trend Line: Use a statistical method (often linear regression) to create a trend line that best fits the data. This trend line represents the general direction of the data over time.
-
Extend the Trend Line: Project the line into the future to estimate upcoming data points.
Types of Trends:
-
Linear Trend: Increases or decreases at a constant rate (e.g., straight-line growth).
-
Exponential Trend: Grows or decays at an increasing rate (e.g., compounding growth).
-
Seasonal or Cyclical Trends: Fluctuations based on recurring patterns, often over weeks, months, or years.
Uses of Trend Projection:
Trend projection is widely used in business, economics, and inventory management to forecast sales, revenue, and demand. Its helpful for short- to medium-term predictions where past trends are expected to continue under similar conditions. However, if conditions are expected to change significantly, other forecasting methods may be more reliable.
-
-
-
-
QUALITATIVE FORECASTING
-
-
-
EXECUTIVE OPINION
Executive opinion is a forecasting method where a group of experts or senior managers within an organization provide their judgments and insights to predict future outcomes. This technique relies on the knowledge, experience, and intuition of the decision-makers rather than statistical models or historical data. It is often used when reliable data is scarce, or when trying to forecast uncertain or complex situations where expert judgment is valuable.
-
DELPHI METHOD
The Delphi method is a structured forecasting and decision-making technique that gathers insights and opinions from a panel of experts over multiple rounds. The goal is to reach a consensus on a specific issue or forecast. The process is iterative, and feedback from each round is shared with the participants to refine their answers. This method is often used for complex or uncertain problems where expert judgment is crucial.
Key Features of the Delphi Method:
-
Expert Panel: A group of knowledgeable individuals or experts is selected to provide their opinions or insights on a particular topic.
-
Multiple Rounds: The process involves several rounds of questions. After each round, the responses are aggregated, summarized, and shared with the group.
-
Anonymity: Participants answer questions independently, which helps to reduce the influence of dominant voices and groupthink.
-
Feedback and Refinement: In each subsequent round, experts can revise their earlier responses based on the groups feedback and reasoning.
-
Consensus: The method aims to arrive at a convergent opinion or forecast by the final round, based on collective expert input.
Uses of the Delphi Method:
-
Forecasting future trends, such as technological developments or market changes.
-
Making decisions in areas of high uncertainty.
-
Identifying risks, opportunities, or innovations in complex fields.
The Delphi method is particularly useful when objective data is unavailable or when the problem requires diverse viewpoints and expert knowledge to form a well-rounded forecast or decision.
-
-
-
SALES FORCE ESTIMATION
Sales force estimation is a forecasting method that relies on the insights and judgments of a companys salespeople to predict future sales. Since salespeople are often in direct contact with customers and have a deep understanding of market conditions, customer behavior, and sales opportunities, their estimates are valuable in providing realistic sales projections.
Key Features of Sales Force Estimation:
-
Expert Insight: Salespeople use their knowledge of customer trends, upcoming deals, and the general market to estimate future sales.
-
Direct Customer Interaction: Sales teams are well-positioned to gather intelligence about customer preferences, product demand, and potential sales, which can help inform their forecasts.
-
Subjective Judgment: The accuracy of the estimates depends on the experience and intuition of the salespeople, as well as their understanding of market conditions.
How It Works:
-
Individual Sales Estimates: Each salesperson submits their own forecast based on their interactions and insights from their sales pipeline (e.g., expected deals, customer interest, etc.).
-
Aggregation: The individual estimates are collected and aggregated to form a company-wide sales forecast. This can be done at various levelsindividual, regional, or national.
-
Adjustments: The forecasts may be adjusted by management based on broader company goals, historical data, or other external factors.
Advantages:
-
Provides a forecast based on real-time, ground-level information from those closest to the customer.
-
Flexible and can adapt quickly to changing market conditions.
-
Can be used in combination with other forecasting methods to refine accuracy.
Disadvantages:
-
Can be biased by individual salespeoples optimism or pessimism.
-
Relies heavily on subjective judgment, which may lack consistency or objectivity.
-
May not account for macroeconomic factors or broader trends outside the salespersons purview.
-
Overall, sales force estimation is a practical tool for businesses that have a well-connected sales team and is often used in conjunction with other forecasting methods to improve accuracy.
-
CONSUMER SURVEYS
Consumer surveys are a forecasting method that involves collecting data from consumers through questionnaires or interviews to understand their preferences, purchasing behavior, and future intentions. The information gathered is then analyzed to predict future demand, sales trends, or market conditions. This method is particularly useful for businesses that want to understand customer expectations, product demand, or opinions about potential products or services.
Key Features of Consumer Surveys:
-
Direct Consumer Input: Surveys gather feedback directly from consumers, providing insights into their needs, preferences, and buying intentions.
-
Quantitative and Qualitative Data: Surveys can collect both numerical (quantitative) data (e.g., how many units a customer plans to buy) and descriptive (qualitative) data (e.g., reasons behind their preferences).
-
Variety of Methods: Surveys can be conducted in various formats, including online, in-person, phone interviws, or mailed questionnaires.
-
Sampling: A sample of consumers is typically surveyed, with the assumption that their responses represent the larger populations behavior or preferences.
How It Works:
-
Survey Design: A set of questions is designed to gather relevant information about consumer preferences, buying habits, and future intentions. Questions can range from simple yes/no answers to more complex multiple-choice or open-ended responses.
-
Data Collection: The survey is distributed to a sample of consumers. The sample size and selection method are critical to ensuring that the survey results are representative of the broader population.
-
Data Analysis: The responses are analyzed to identify trends, patterns, or specific insights that can be used to forecast future demand or market behavior.
-
Forecasting: Based on the responses, companies can estimate future sales, product demand, or customer behavior.
Advantages:
-
Provides direct insights into consumer preferences, which can improve product development, marketing strategies, and demand forecasting.
-
Can be used to test market reactions before launching a new product or service.
-
Allows businesses to anticipate consumer trends and adjust strategies accordingly.
Disadvantages:
-
Survey responses may be biased or not fully representative of the entire population, especially if the sample is too small or not diverse.
-
The accuracy of the forecast depends on the quality of the questions and the reliability of the data collected.
-
Consumers may not always accurately predict their future behaviors, leading to potential inaccuracies.
Uses of Consumer Surveys:
-
Demand Forecasting: Estimating future sales based on consumer intentions.
-
Market Research: Understanding consumer preferences, attitudes, and behaviors.
-
Product Development: Testing consumer reactions to potential products or services before launch.
-
Customer Satisfaction: Measuring customer satisfaction levels and identifying areas for improvement.
-
Consumer surveys are a powerful tool for gaining insights into market trends and consumer behavior, especially when combined with other forecasting methods.
In practice, executives or experts discuss the factors influencing future events and come to a consensus on a forecast, which is then used for planning and decision-making.
-
JUST-IN-TIME (JIT) PRODUCTION
Just-In-Time (JIT) is a production strategy aimed at reducing waste and improving efficiency by synchronising production with customer demand. This approach emphasises demand-driven production, inventory management, and a culture of continuous improvement. JIT promotes producing goods based on actual customer demand rather than forecasts, minimising the risk of overproduction and excess inventory.
Key elements of JIT include continuous improvement (Kaizen), which fosters a culture of ongoing enhancement in processes and efficiency. Waste reduction targets various forms of waste, known as "Muda," such as overproduction and unnecessary transportation. The pull system utilised in JIT means production is triggered by customer demand, helping prevent excess inventory. Takt time refers to the pace of production synchronised with customer demand, while the Kanban system serves as a visual tool for managing material flow and production processes.
Strong supplier partnerships are essential to ensure timely delivery of materials, reinforcing the principles of JIT and enabling organisations to respond quickly to changes in demand. Additionally, maintaining a flexible workforce that can adapt to shifting production needs is crucial for sustaining JIT principles. Training employees to handle multiple tasks and fostering a culture of accountability contributes to operational efficiency.
Demand-Driven Production: JIT focuses on producing goods based on actual customer demand rather than forecasts. By closely monitoring customer orders and adjusting production accordingly, JIT minimizes the risk of overproduction, excess inventory, and stockouts.
Inventory Management: JIT advocates for maintaining minimal inventory levels by only keeping what is necessary for immediate production needs. This helps reduce storage costs, minimize the risk of obsolescence, and improve cash flow. However, it requires efficient supply chain management and close coordination with suppliers to ensure timely delivery of materials.
Continuous Improvement: JIT encourages a culture of continuous improvement throughout the production process. This involves identifying and eliminating sources of waste, such as overproduction, excess inventory, waiting time, unnecessary movement, defects, and underutilized resources. Techniques such as Kaizen (continuous improvement), Poka-Yoke (error proofing), and Value Stream Mapping are commonly used to streamline processes and increase efficiency.
Flexible Workforce: JIT requires a flexible and cross-trained workforce capable of performing multiple tasks and adapting to changing production needs. This allows for better utilization of labor resources, smoother workflow, and the ability to quickly respond to fluctuations in demand or unexpected disruptions.
Supplier Partnerships: JIT relies on close relationships with suppliers to ensure timely delivery of high-quality materials/components. Just like in-house production, suppliers must adhere to JIT principles by delivering small, frequent shipments of materials, maintaining high quality standards, and continuously improving their processes.
Quality Control: Quality is a fundamental aspect of JIT production. By focusing on prevention rather than detection, JIT aims to eliminate defects at the source and ensure that every product meets customer specifications. This involves implementing rigorous quality control measures, empowering employees to identify and address quality issues, and fostering a culture of accountability and excellence.
Kanban System: The Kanban system is often used in conjunction with JIT to facilitate the smooth flow of materials and information throughout the production process. Kanban cards signal when materials are needed at each workstation, ensuring that production is synchronized with demand and preventing overproduction or stockouts.
By implementing JIT principles, organizations can achieve significant improvements in productivity, quality, lead times, and overall competitiveness. However, successful implementation requires commitment, collaboration, and a relentless focus on continuous improvement across all levels of the organization.
Kanban System
Quality Control
Supplier Partnerships
Flexible Workforce
Continuous Improvement
Inventory
Management
Demand Driven Production
Just-In Time
-
CONCLUSION
In conclusion, building supply chain resilience is a multifaceted endeavour that requires a strategic approach to risk management, technology integration, and collaborative planning. Organisations must invest in developing robust frameworks and metrics to navigate uncertainties effectively. By leveraging advanced forecasting methods and adopting JIT principles, businesses can enhance their responsiveness and adaptability, ultimately leading to improved operational performance and customer satisfaction.
-
REFERENCES
-
Lima, F. R. P. d., et al. "Resilience Enablers to Combat Countereit Medicines." Supply Chain Management: An International Journal, vol. 23, no. 4, 2018.
-
Handfield, R. B., Bechtel, E. L., and Sweeney, T. C. J. "Supply Chain Resilience in the Face of Disruption: Insights from the Literature." Journal of Supply Chain Management, vol. 56, no. 3, 2020.
-
Silva, M. A. A. M., et al. "The Role of Technology in Enhancing Supply Chain Resilience." International Journal of Production Economics, vol. 210, 2019.
-
Thun, C. R., and Hoenig, M. E. "The Relationship Between Operational Capabilities and Supply Chain Resilience." Journal of Business Logistics, vol. 42, no. 1, 2021.
-
Choi, G., et al. "Supply Chain Resilience: A Dual Perspective of Suppliers and Customers." Transportation Research Part E: Logistics and Transportation Review, vol. 124, 2019.
-
Silva, M. P. F. C. J., et al. "Enhancing Supply Chain Resilience Through Risk Management Strategies." Journal of Operations Management, vol. 66, 2020.
-
A. J. M. R. A. S. C. R. B. et al. "A Framework for Assessing Supply Chain Resilience." Supply Chain Management: An International Journal, vol. 24, no. 5, 2019.
-
K. P. S. M. P. S. C. et al. "The Importance of Inventory Optimization in Supply Chain Resilience." International Journal of Production Research, vol. 58, no. 10, 2020.
-
P. A. C. J. et al. "Collaborative Forecasting for Supply Chain Resilience." Journal of Business Research, vol. 124, 2021.
-
G. A. H. H. J. et al. "Leveraging Advanced Analytics for Supply Chain Resilience." Journal of Supply Chain Management, vol. 56, no. 2, 2020.
-
M. J. et al. "The Impact of JIT on Supply Chain Performance and Resilience." International Journal of Operations & Production Management, vol. 39, no. 3, 2019.
-
P. M. H. J. et al. "Risk Management in Supply Chains: A Resilience Perspective." Supply Chain Forum: An International Journal, vol. 21, no. 2, 2021.
-
R. T. J. et al. "Techniques for Improving Supply Chain Resilience Through Supplier Diversification." Journal of Business Logistics, vol. 41, no. 4, 2020.
-
A. J. P. T. H. D. H. et al. "Strategies for Managing Supply Chain Disruptions." Transportation Research Part E: Logistics and Transportation Review, vol. 143, 2021.
-
G. P. M. H. et al. "Exploring the Role of Technology in Supply Chain Resilience." Journal of Operations Management, vol. 66, 2020.
-
C. S. J. et al. "The Significance of Collaboration in Enhancing Supply Chain Resilience." International Journal of Physical Distribution & Logistics Management, vol. 49, no. 8, 2019.
-
A. F. H. A. G. et al. "Enhancing Resilience Through Inventory Management Strategies." International Journal of Production Economics, vol. 220, 2020.
-
M. R. H. et al. "Supply Chain Flexibility and Resilience: A Review of the Literature." Journal of Supply Chain Management, vol. 57, no. 1, 2021.
-
L. P. S. A. J. C. et al. "Best Practices for Achieving Supply Chain Resilience." Journal of Business Research, vol. 116, 2020.
-
G. T. A. J. M. et al. "Analyzing the Relationship Between Supply Chain Agility and Resilience." Journal of Operations Management, vol. 65, 2019.
-
D. M. H. et al. "The Role of Risk Assessment in Building Resilient Supply Chains." International Journal of Logistics Management, vol. 32, no. 1, 2021.
-
C. G. P. D. R. M. et al. "Identifying Supply Chain Risks and Resilience Strategies." Journal of Business Logistics, vol. 41, no. 3, 2020.
-
M. A. D. G. et al. "Enhancing Supply Chain Visibility for Improved Resilience." International Journal of Production Economics, vol. 221, 2019.
-
A. J. P. T. H. D. H. C. et al. "A Comprehensive Approach to Supply Chain Risk Management." Journal of Supply Chain Management, vol. 57, no. 3, 2021.
-
D. S. P. M. G. et al. "Collaborative Planning in Supply Chains: A Resilience Perspective." Journal of Operations Management, vol. 66, 2020.