
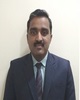
- Open Access
- Authors : Niket Malvade, Dr. Raju Pawade
- Paper ID : IJERTV13IS070048
- Volume & Issue : Volume 13, Issue 07 (July 2024)
- Published (First Online): 22-07-2024
- ISSN (Online) : 2278-0181
- Publisher Name : IJERT
- License:
This work is licensed under a Creative Commons Attribution 4.0 International License
Surface Roughness and Cutting Forces Optimization in Machining of Biodegradable Magnesium Calcium Alloy
Published by : http://www.ijert.org
International Journal of Engineering Research & Technology (IJERT)
ISSN: 2278-0181
Vol. 13 Issue 07, July-2024
Niket Malvade Dr. Raju Pawade
Research Scholar Associate Professor
Department of Mechanical Engineering, Department of Mechanical Engineering, Dr. Babasaheb Ambedkar Technological University Dr. Babasaheb Ambedkar Technological University
Lonere ,India Lonere ,India
Assistant Professor
K.B.P. College of Engineering, Satara
Abstract
Mg-Ca1.0 is newly developed biodegradable material which do not produce any toxic elements in the body. It is widely used in bone implants supporting plate and fixation screw. The implant surface is in direct contact with body solution so surface integrity is the most important factor affecting the degradation rate of biodegradable implants. Very few studies are reported on machining of biodegradable magnesium calcium alloy till date. Besides, investigation using CVD diamond like carbon coated carbide insert has not been used for face milling of MgCa1.0 alloy. In view of the above, the study reports the effects of machining parameters, process and cutting tool on performance of biodegradable magnesium calcium alloy implant in terms of surface roughness and cutting force in face milling operation using CVD diamond like carbon coated carbide inserts. The effect of cutting speed, feed rate and depth of cut on surface roughness was investigated in face milling of MgCa1 magnesium alloy. The experimental result shows that the feed rate is the most significant factor influencing the average surface roughness value which is closer to 0.142 µm.
Keywords Surface integrity, Cutting force, Magnesium- calcium alloy, Face milling
-
INTRODUCTION
Biodegradable implants will be an ideal solution to the challenges of stress shielding and surgical interventions caused by metallic implants which dissolve in the human organism [1]. Today, Mg-based alloys have lot of scope due to their properties nearly equal to that of human bone. Magnesium and magnesium alloys are nonferrous metals with low density, good ductility, moderate strength and good corrosion resistance. It has been found from the vivo studies that the magnesium- calcium alloys are suitable as degradable biomaterial for use in medicalimplant[2][6].
The problems associated with non-degradable implants have led to a growing interest in biodegradable materials. The idea is that the implant remains in the body i.e., serving its purpose during the healing process, and then naturally degrades in the body fluid and excretes without any complication. Biocompatible and biodegradable polymers e.g. polylactide, polyglycolide and their copolymers are commercially available, but the mechanical strength of these polymers is too low to be used in orthopedic load-bearingapplications.[7]
Koleini et al. [7] studied the influence of hot rolling parameters on microstructure and biodegradability of MgCa1.0 alloy. They expressed that more thickness reduction caused less corrosion and high preheated temperature of the MgCa implant increases the corrosion. Harandi et al.[8] observed that after forging, mechanical strength and corrosion resistance of MgCa1 alloy was improved. Denkena et al. [9] observed that the lower cutting speed gives lower corrosion rate in turned Mg-Ca3.0 alloy. It is noted that increase in surface roughness led to a faster degradation rate. Salahshoor [10] studied dry high-speed face milling of MgCa0.8 alloy using PCD tipped tool and found that the cutting parameters lead to changes in the microstructure in near surface due to thermal effects. The compressive residual stresses induced in the implant slows down the corrosion rate of the implant in human body fluid. It is found that an increase in cutting speed and feed rates, causes the increase in microhardness. Friemuth et al. [11] carried out turning and subsequent rolling of AZ91 magnesium alloy and noted that increase in surface hardness and induced compressive stresses
IJERTV13IS070048
(This work is licensed under a Creative Commons Attribution 4.0 International License.)
in the subsurface further increase the corrosion resistance. Birol [12] found that the higher cutting speed causes inhomogeneous shear strain and the chip changes from continuous chip to saw-tooth chip.
Based on the extensive literature survey, it is noted that few studies reported on the machining performance of MgCa0.8 alloy. However, no work has been reported on machining of Mg-Ca1.0 forged component using CVD-DLC coated carbide inserts which is more improved. Thus the focus of the present study is to determine the effect of machining parameters on performance in terms of surface roughness.
-
MATERIALS AND EXPERIMENTAL DETAILS
Experimental setup to conduct milling experiments is shown in Fig 1. Work material, Mg-Ca 1.0 alloy in the form of plates 80 mm x 60 mm x 10 mm is used in dry face milling. CNC milling center Hardinge VMC 600 II) with a max spindle speed of 3800 rpm has been used to carry out experiments. DLC coated carbide cutting inserts (Make- HITACHI) were used and the cutting diameter is 50 mm.
Fig. 1 Experimental Setup
In this study, cutting experiments have been planned using Response surface methodology design using MINITAB 18. This design is created considering three milling parameters namely milling speed, feed and depth of cut. 20 experiments have been carried out with the parameters given in Table 1. After machining surface roughness is measured using Mitutoyo surface roughness tester (model- SJ-201, make- Mitutoyo). A sampling length of 2.5 mm has been considered, while measuring the surface roughness parameter Ra.
TABLE I: Face milling parameter
Cutting speed Vc
(m/min)
Feed
f
(mm/rev)
Depth of cut ap
(mm)
350
0.15
0.15
450
0.20
0.20
550
0.30
0.25
-
RESPONSE SURFACE METHODOLOGY
In the current study, the experiments were organised following a central composite matrix, according to the response surface methodology (RSM). Statistical analysis (ANOVA) was used to assess the effects of the input parameters upon the outcomes of the process. The responses taken into consideration for analysis in this paper are surface roughness (Ra) and Cutting forces. In a central composite design (CCD), the design points consist of three groups: two level factorial points, which are all the combinations of the +1 and -1 levels of the factors; the central points corresponding to the average value of the factors, which are repeated four times for a better estimation of the error; the axial (star) points resulted by multiplying the factorial levels with +/- (alpha), which is calculated in order to assure the rotatability of the design.[13] The levels of each experimental factor are presented in Table II.
TABLE II Experimental factors and levels.
-
RESULTS AND DISCUSSION
Expt No.
Speed (m/min)
Feed (mm/rev)
Depth of cut (mm)
Roughness in
(µm)
Cutting force (N)
1
0.225
0.200
0.208
10.822
2
550.00
0.300
0.250
0.224
10.308
3
450.00
0.225
0.115
0.202
10.213
4
350.00
0.300
0.250
0.274
12.936
5
550.00
0.150
0.150
0.142
8.441
6
450.00
0.225
0.200
0.202
10.478
7
450.00
0.225
0.200
0.210
10.601
8
450.00
0.098
0.200
0.143
8.491
9
618.17
0.225
0.200
0.166
8.479
10
550.00
0.300
0.150
0.218
9.813
11
450.00
0.225
0.200
0.206
10.470
12
350.00
0.150
0.250
0.198
11.564
13
350.00
0.150
0.150
0.192
11.069
14
281.82
0.225
0.200
0.250
12.898
15
450.00
0.225
0.200
0.207
10.678
16
450.00
0.225
0.284
0.213
10.976
17
450.00
0.351
0.200
0.272
12.007
18
450.00
0.225
0.200
0.208
10.608
19
550.00
0.150
0.250
0.148
8.940
20
350.00
0.300
0.150
0.268
12.441
Analysis of variance (ANOVA) is a statistical tool used in DOE to establish the significance of the factors or their interactions. As a general rule, total variance of a model is attributed to the factors and to the random error, respectively. The significance of a factor is assessed by performing statistical (F-tests) under a null hypothesis: large values of F-ratios imply a high influence of the factor on the response. Significance is determined according to a confidence interval, which is established for a certain p-value. The p-value represents the probability that the results of the tests could have occurred by random chance. This study uses (corresponding to a 95% confidence interval), which means that a factor is considered significant only if p value is less than 0.05[13].
-
Surface Roughness Analysis
The goal of the research is to reduce the surface roughness parameters Ra while taking into account the input parameters cutting speed, feed, and cut depth. The analyses' findings are presented in Table III. Feed rate is the most important component (with 69.63 percent contribution). Speed was also shown to be considerable (with a contribution of 29.88 percent)/Depth of cut had a lesser impact on Surface roughness. When the feed values rise, the surface roughness rises with them. As demonstrated in Figure 2, the roughness values increase from 0.143 m to 0.272 m.
-
Cutting force Analysis
Table IV displays the results of an ANOVA on the principal cutting force. The model is quite important. In this the most important component is Speed, which contributes 69.21 percent, followed by Feed, which contributes 27.92 percent. Although there are additional important aspects, their influence is minor. Figure 3 shows that as the cutting force reduces from
12.90 N to 8.47 N as the speed increases from 281 m/min to 618 m/min. This is because when the speed of the machine increases, the material softens, reducing the amount of cutting force required for machining.
TABLE III Analysis of Variance for Roughness
Source
DF
Adj SS
Adj MS
F-Value
P-Value
% of Contribution
Speed
1
0.008528
0.008528
2259.45
0
29.88
Feed
1
0.019872
0.019872
5265.02
0
69.63
Depth of cut
1
0.000132
0.000132
35.04
0
0.46
Speed*Speed
1
0.000003
0.000003
0.85
0.378
0.01
Feed*Feed
1
0.000001
0.000001
0.33
0.577
0.00
Depth of cut*Depth of cut
1
0.000001
0.000001
0.33
0.577
0.00
Speed*Feed
1
0
0
0
1
0.00
Speed*Depth of cut
1
0
0
0
1
0.00
Feed*Depth of cut
1
0
0
0
1
0.00
Error
10
0.000038
0.000004
Total
19
0.028575
Fig. 2 Main Effects plot for Roughness
Fig. 3 Main Effects plot for Cutting force
-
-
CONCLUSION
In this study, the RSM method was used to investigate the high-speed milling process of a magnesium calcium alloy (MgCa1.0). The work was organised to establish how surface quality and the main cutting force are affected by the choice of the machining conditions: cutting speed, feed, depth of cut. The most relevant conclusions of this study are as follows:
Surface roughness is mostly influenced by the feed (expressed in this study as the feed mm/rev). The most favorable conditions for a good surface quality, under the studied circumstances, are a combination of high cutting speed, small feed and depth of cut.
Speed is an important factor of influence for the main cutting force. However, Feed has important effect on Cutting force with a contribution of 27.92 %. To a much lesser extent, the cutting force is influenced by their interaction.
IJERTV13IS070048
(This work is licensed under a Creative Commons Attribution 4.0 International License.)
TABLE IV Analysis of Variance for Cutting Force
Source
DF
Adj SS
Adj MS
F-Value
P-Value
% of Contribution
Speed
1
23.571
23.571
376.86
0
69.21
Feed
1
9.5089
9.5089
152.03
0
27.92
Depth of cut
1
0.7814
0.7814
12.49
0.005
2.29
Speed*Speed
1
0.0644
0.0644
1.03
0.334
0.19
Feed*Feed
1
0.1129
0.1129
1.81
0.209
0.33
Depth of cut*Depth of cut
1
0.0162
0.0162
0.26
0.622
0.05
Speed*Feed
1
0
0
0
0.996
0.00
Speed*Depth of cut
1
0
0
0
0.996
0.00
Feed*Depth of cut
1
0
0
0
0.996
0.00
Error
10
0.6255
0.0625
Total
19
34.7015
-
REFERENCES
-
M. Salahshoor and Y. Guo, Biodegradable orthopedic magnesium-calcium (MgCa) alloys, processing, and corrosion performance, Materials (Basel)., vol. 5, no. 1, pp. 135155, 2012
-
M. P. Staiger, A. M. Pietak, J. Huadmai, and G. Dias, Magnesium and its alloys as orthopedic biomaterials: A review, Biomaterials, vol. 27, no. 9,
pp. 17281734, 2006.
-
G. Eddy Jai Poinern, S. Brundavanam, and D. Fawcett, Biomedical Magnesium Alloys: A Review of Material Properties, Surface Modifications and Potential as a Biodegradable Orthopaedic Implant, Am. J. Biomed. Eng., vol. 2, no. 6, pp. 218240, 2013,
-
M. Thomann, C. Krause, D. Bormann, N. Von Der Höh, H. Windhagen, and A. Meyer-Lindenberg, Comparison of the resorbable magnesium alloys LAE442 und MgCa0.8 concerning their mechanical properties, their progress of degradation and the bone-implant-contact after 12 months implantation duration in a rabbit model, Materwiss. Werksttech., vol. 40, no. 12, pp. 8287, 2009.
-
M. B. Kannan and R. K. S. Raman, In vitro degradation and mechanical integrity of calcium- containing magnesium alloys in modified-simulated body fluid, Biomaterials, vol. 29, no. 15, pp. 2306
2314, 2008.
-
N. T. Kirkland, J. Lespagnol, N. Birbilis, and M. P. Staiger, A survey of bio-corrosion rates of magnesium alloys, Corros. Sci., vol. 52, no. 2, pp.
287291, 2010.
IJERTV13IS070048
-
S. Koleini, M. H. Idris, and H. Jafari, Influence of hot rolling parameters on microstructure and biodegradability of Mg-1Ca alloy in simulated body fluid, Mater. Des., vol. 33, no. 1, pp. 2025, 2012.
-
S. E. Harandi, M. Hasbullah Idris, and H. Jafari, Effect of forging process on microstructure, mechanical and corrosion properties of biodegradable Mg-1Ca alloy, Mater. Des., vol. 32, no. 5, pp. 2596 2603, 201.
-
B. Denkena, A. Lucas, F. Thorey, H. Waizy, N. Angrisani, and A. Meyer-Lindenberg, Biocompatible Magnesium Alloys as Degradable Implant Materials – Machining Induced Surface and Subsurface Properties and Implant Performance,
Spec. Issues Magnes. Alloy., 2011
-
M. Salahshoor and Y. B. Guo, Surface integrity of biodegradable orthopedic magnesium- calcium alloy by high-speed dry face milling, Prod. Eng., 2011.
-
T. Friemuth and J. Winkler, Machining of magnesium workpieces, Adv. Eng. Mater., vol. 1, no. 34, pp. 183186, 1999.
-
B. Akyuz, Machinability of magnesium and its alloys, Online J. Sci. Technol., vol. 1, no. 3, pp. 3138, 2011.
-
B. Chirita, C. Grigoras, C. Tampu, and E. Herghelegiu, Analysis of cutting forces and surface quality during face milling of a magnesium alloy, IOP Conf. Ser. Mater. Sci. Eng., vol. 591, no. 1, 2019.
(This work is licensed under a Creative Commons Attribution 4.0 International License.)