
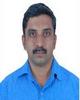
- Open Access
- Authors : S.Chandra Sekhar, Dr. Virendra K. Sharma
- Paper ID : IJERTV13IS080021
- Volume & Issue : Volume 13, Issue 08 (August 2024)
- Published (First Online): 18-08-2024
- ISSN (Online) : 2278-0181
- Publisher Name : IJERT
- License:
This work is licensed under a Creative Commons Attribution 4.0 International License
Survey Paper: A Novel Approach of Multi-Level Inverter for Industrial Drive Applications
S. Chandra Sekhar, Research Scholar, Department of Electrical and Electronics Engineering,
Bhagwant University, Ajmer, India
AbstractMulti-level inverters (MLIs) are increasingly being used in industrial drive applications due to their ability to produce high-quality voltage waveforms with reduced harmonic distortion. This paper provides a comprehensive survey of the novel approaches in the design and implementation of multi-level inverters, focusing on their application in industrial drives. Various topologies, such as Diode-Clamped, Capacitor-Clamped, and Cascaded H-Bridge inverters, are discussed, highlighting their respective advantages and disadvantages. Traditional control methods like Pulse Width Modulation (PWM) are evaluated alongside modern adaptive control strategies utilizing neural networks and fuzzy logic, which offer enhanced performance and efficiency. The integration of these advanced control techniques enables MLIs to adapt to varying operating conditions, improving the robustness and reliability of industrial drive systems. Additionally, the challenges associated with MLIs, such as complexity in control strategies and the need for precise voltage balancing, are addressed. The future directions for research are also explored, focusing on the development of more efficient algorithms, reduction of component count, and improvement in reliability and fault tolerance. This survey aims to provide a detailed understanding of the current state and future potential of MLIs in industrial drive applications, emphasizing their critical role in achieving high performance and energy efficiency.
KeywordsMulti-Level Inverter (MLI), Industrial Drive Applications, Harmonic Distortion, Diode-Clamped Inverter, Capacitor-Clamped Inverter, Cascaded H-Bridge Inverter, Pulse Width Modulation (PWM), Neural Network-Based Control, Fuzzy Logic Control, Adaptive Learning Control, Speed Control of Induction Motors, Torque Control, Voltage Balancing, High- Performance Drives, Direct Torque Control (DTC), Total Harmonic Distortion (THD), Voltage Waveforms, Switching Losses, High-Power Applications, Modern Adaptive Control
- INTRODUCTION
The demand for efficient and high-performance drive systems in industrial applications is continuously increasing due to the advancements in automation and the need for energy conservation. Traditional inverters, which convert DC to AC power, often face limitations such as significant harmonic distortion and high switching losses. These issues can lead to inefficiencies and reduced lifespan of the equipment. Multi- level inverters (MLIs) offer a promising solution by providing multiple voltage levels, which results in improved output waveforms and significantly reduced total harmonic distortion (THD).
MLIs have gained popularity in industrial drive applications due to their ability to produce high-quality voltage waveforms, which are essential for the smooth and efficient operation of
Dr. Virendra K. Sharma, Professor, Department of Electrical and Electronics Engineering,
Bhagwant University,
Ajmer, India
motors and other industrial equipment. The basic idea behind MLIs is to use multiple smaller voltage steps to approximate a sinusoidal waveform, which helps in reducing the stress on power electronic components and improves the overall system performance. This survey explores the advancements in MLI technology, focusing on novel approaches in their design and implementation. It delves into various topologies, such as Diode-Clamped (Neutral Point Clamped), Capacitor-Clamped (Flying Capacitor), and Cascaded H-Bridge inverters, discussing their working principles, benefits, and drawbacks. The performance of MLIs is heavily dependent on the control strategies employed. Traditional control methods, primarily based on Pulse Width Modulation (PWM), are examined along with modern adaptive control techniques using neural networks and fuzzy logic.
Neural networks and fuzzy logic controllers have emerged as powerful tools for managing the complexities of MLIs. Neural networks, with their adaptive learning capabilities, can optimize the inverter performance in real-time, adapting to changing operating conditions and load variations. Fuzzy logic controllers, on the other hand, offer robustness and simplicity in handling non-linear systems, making them suitable for industrial applications. The integration of these advanced control techniques not only enhances the performance and efficiency of MLIs but also addresses some of the inherent challenges such as voltage balancing and control complexity. This paper aims to provide a comprehensive survey of these advancements, highlighting their impact on industrial drive applications. Furthermore, the challenges associated with MLIs, including the need for precise control and the high number of components, are discussed, along with future research directions aimed at developing more efficient and reliable MLI systems.
By exploring the state-of-the-art in MLI technology and its applications in industrial drives, this survey provides valuable insights into the current trends and future possibilities in this field, emphasizing the critical role of MLIs in achieving high performance and energy efficiency in industrial applications. The demand for efficient and high- performance drive systems in industrial applications continues to grow due to advancements in automation and energy conservation requirements. Multi-level inverters (MLIs) have emerged as a promising solution to address limitations such as significant harmonic distortion and high switching losses in traditional inverters.
Recent studies have focused on various topologies
and control strategies to further enhance the performance and efficiency of MLIs.
- MULTI-LEVEL INVERTER TOPOLOGIES
Multi-level inverters (MLIs) have evolved significantly to meet the growing demands for higher power quality and efficiency in industrial applications. Here, we discuss the three primary MLI topologies: Diode-Clamped, Capacitor- Clamped, and Cascaded H-Bridge inverters, along with references to highlight their development and application.
- Diode-Clamped Multi-Level Inverters
Diode-Clamped Multi-Level Inverters, also known as Neutral Point Clamped (NPC) inverters, use diodes to clamp the voltage levels, which helps in reducing the voltage stress on power electronic devices. The basic principle involves dividing the DC bus voltage into multiple levels through capacitors and diodes. Each switch in the inverter can block only a fraction of the total DC voltage, allowing for higher voltage applications. Recent innovations in diode-clamped MLIs aim to reduce component count and improve reliability. For instance, V. D. Juyal, et al. [1] proposed a new configuration that minimizes the number of clamping diodes required, enhancing the inverter’s overall efficiency and performance. Additionally, improvements in voltage balancing techniques have been introduced, addressing one of the primary challenges of this topology [2].
- Capacitor-Clamped Multi-Level Inverters
Capacitor-Clamped Multi-Level Inverters, also known as Flying Capacitor inverters, use capacitors to achieve multiple voltage levels. This topology is characterized by its capability to generate a higher number of voltage levels, which helps in improving the quality of the output waveform.
Capacitor-clamped inverters have seen advancements in balncing capacitor voltages, which are crucial for maintaining output quality. V. Singh et al. [3] presented an improved balancing algorithm that significantly enhances the performance and reliability of capacitor-clamped inverters. Moreover, new control strategies have been developed to handle the complexities associated with this topology [4].
- Cascaded H-Bridge Inverters
Cascaded H-Bridge Inverters consist of multiple H-bridge inverters connected in series. Each H-bridge generates a three- level output, and the overall inverter output is the sum of the outputs of the individual H-bridges. This topology is particularly advantageous for medium to high-power applications due to its scalability and modularity.
Cascaded H-Bridge inverters are now more scalable and modular, making them suitable for high-power applications. N. Sujitha. et al. [5] explored new configurations that allow for easier expansion and improved fault tolerance. Recent studies have also focused on reducing the overall component count while maintaining high performance [6].
- Diode-Clamped Multi-Level Inverters
- CONTROL STRATEGIES FOR MULTI-LEVEL INVERTERS
The performance of MLIs significantly depends on the control strategies employed. Traditional control methods are being enhanced by modern techniques such as adaptive control, neural networks, and fuzzy logic controllers.
- Pulse Width Modulation (PWM)
PWM is the most commonly used control strategy for MLIs. Various PWM techniques such as Sinusoidal PWM, Space Vector PWM, and Selective Harmonic Elimination PWM are employed to control the switching of the inverters to achieve desired voltage levels.
Hybrid PWM techniques have been developed to enhance the performance of MLIs. R. Kumar et al. [7] introduced a hybrid PWM method that combines sinusoidal and space vector PWM to achieve better harmonic performance and efficiency. Studies have also explored selective harmonic elimination techniques to further reduce harmonic distortion [8].
- Neural Network-Based Control
Neural networks are used to design controllers that can adapt to varying operating conditions. The adaptive learning capability of neural networks allows them to optimize the inverter performance in real-time. For example, Zerikat and Chekroun (2008) proposed an adaptive learning algorithm based on artificial neural networks for the speed control of induction motors in high-performance drives.
Neural networks offer adaptive learning capabilities that optimize inverter performance in real-time. A. Bakeer, et al. [9] conducted case studies demonstrating significant improvements in speed control and efficiency using neural network-based controllers. Recent advancements include integrating neural networks with other control strategies for enhanced performance [10].
- Fuzzy Logic Control
Fuzzy logic controllers (FLC) are capable of handling non- linear systems and can be easily implemented for MLIs. FLCs use a set of fuzzy rules to manage the inverter switching, providing robustness against parameter variations and disturbances [11-12].
- Pulse Width Modulation (PWM)
- APPLICATION IN INDUSTRIAL DRIVES
MLIs are widely used in industrial drives for applications requiring high power and performance. The ability to produce high-quality voltage waveforms with low harmonic distortion makes MLIs suitable for driving induction motors and other industrial machinery.
-
- Speed Control of Induction Motors: Adaptive learning control schemes using neural networks have shown significant improvements in the speed control of induction motors. These controllers can accurately track reference commands and adapt to load changes, providing robust performance under various operating conditions. Advanced adaptive learning control schemes have shown significant improvements in speed regulation of induction motors. Mencou, Siham & Majid et al. [13] demonstrated that neural network-based adaptive control could accurately track reference commands and adapt to load changes, providing robust performance [14].
- Torque Control: The use of MLIs in direct torque control (DTC) schemes for induction motors has demonstrated enhanced performance. The multi-level output voltage of MLIs allows for finer control of the motor torque and flux, resulting in reduced torque ripple and improved dynamic response. Direct Torque Control (DTC) schemes using MLIs have been enhanced to provide finer control over motor torque and flux. Ahmad Tarusan et al. [15] presented a new DTC approach that reduces torque ripple and improves dynamic response, making it suitable for high-performance industrial applications [16].
-
- COMPARISON OF MULTI-LEVEL INVERTER TOPOLOGIES
Each multi-level inverter topology offers unique advantages and disadvantages, making them suitable for different industrial drive applications. Here, we compare the key features of Diode-Clamped, Capacitor-Clamped, and Cascaded H-Bridge inverters. Recent studies have provided new insights into the efficiency, harmonic distortion, and complexity of different MLI topologies.
Topology | Diode-
Clamped Inverters |
Capacitor- Clamped Inverters | Cascaded
-Bridge Inverters |
Efficiency | High,
due to reduced switching losses. |
Moderate to high,dependig on the
control strategy. |
High, due to modular
structure and scalability. |
Harmonic Distortion | Low,
with good quality output voltage. |
Very low, with excellent voltage waveform quality. | Very low,
with high number of output voltage levels. |
Complexity | High,
due to the large number of clamping diodes required. |
High, due
to the need for complex control strategies to manage capacitor voltages. |
Moderate to high, requiring
separate DC sources for each H- bridge. |
Applications | Suitable
for high- voltage applications where efficiency and harmonic performance are critical. |
Ideal for applications requiring high-quality voltage waveforms and modularity. | Suitable
for medium to high- power applications where modularity and fault tolerance are important. |
Diode-Clamped Inverters is having High efficiency due to reduced switching losses has been a key advantage. Upadhyay, Nitin et al. [17] compared various diode-clamped configurations and highlighted the improvements in harmonic performance with advanced control techniques [18].
Harmonic study of described configurations has been done using powergui block of simpowersystem lybrary of MATLAB and analysed results are shown in figures given below.
Fig.1- FFT analysis of phase voltage of three phase 5- level diode clamped inverter
Fig 1 and fig 2 show the FFT analysis of phase and line voltage of five level diode clamped MLI. It can be noted that phase voltage has total harmonic distortion of 22.58% and line voltage has THD of 18.94%. Five level inverter has lowered down the harmonic level but still exceeds the standard limit set by IEEE.
Fig.2- FFT analysis of line voltage of three phase 5- level diode clamped inverter
Harmonic pollution in any power system can be reduced by employing any type of passive or active filter but MLI shows the property of reducing distortion as we increase the levels in any type of MLI. Hence fifteen-level DCMLI has been simulated and analyzed using powergui tool.
Fig.3- FFT analysis of phase voltage of three phase 15- level diode clamped inverter Fig 3 and fig 4 shows the FFT analysis of the output waveform of phase voltage and line voltage of fifteen-level diode clamped multilevel inverter. In the analytic study of the inverter this can be seen that the percentage THD in phase voltage is found 2.53% and line voltage has THD of 2%.
Fig.4 – FFT analysis of line voltage of three phase 15-level diode clamped inverter Capacitor-clamped inverters offer very low harmonic distortion with excellent voltage waveform quality.
Table 1
New balancing algorithms have further improved their performance [19].
Table2: Summary of methods.
These inverters are noted for their scalability and modularity, making them ideal for medium to high-power applications. Studies have shown that they can achieve very low harmonic distortion with a high number of output voltage levels [20].
V.CONCLUSION
Multi-level inverters have become a vital component in modern industrial drive applications due to their ability to produce high-quality voltage waveforms with reduced harmonic distortion. This survey has highlighted the advancements in MLI topologies, control strategies, and their applications in industrial drives. Diode-Clamped, Capacitor-Clamped, and Cascaded H-Bridge inverters each offer distinct advantages and are suited to different applications based on their specific requirements. The integration of advanced control techniques such as neural networks and fuzzy logic has further enhanced the performance and efficiency of MLIs. Future research will continue to focus on optimizing these topologies and developing more efficient and reliable control algorithms to meet the growing demands of industrial applications.
Multi-level inverters are crucial for modern industrial drive applications due to their ability to produce high-quality voltage waveforms with reduced harmonic distortion. This survey has highlighted recent advancements in MLI topologies, control strategies, and their applications in industrial drives. The integration of advanced control techniques such as neural networks and fuzzy logic has further enhanced the performance
and efficiency of MLIs. Future research will focus on optimizing these topologies and developing more efficient and reliable control algorithms to meet the growing demands of industrial applications.
REFERENCES
Conventional PWM/SVM | VV- SVM | Carrier- overlapped PWM | Hybrid modulations | Self- balancing |
switching cycle than other alternatives.
Balance in every switching cycle not possible for high values of m; the limit depends on the load power factor. For more than three levels, in the region where balancing is not possible, capacitor voltages collapse |
Balance in every switching cycle under all
operating conditions. Lower required capacitance than with alternative modulations. Higher number of commutations per switching cycle than other alternatives |
Lower number of commutations than
VVSVM. Higher required capacitance than VV SVM. Higher number of commutations than conventional PWM/SVM. |
The applied modulation is selected
depending on m. Takes advantage of the benefits of each modulation in each operating region. Increased complexity compared to other alternatives. |
It is a do- nothing method.
Balance only for the 3-level case with restricted operating conditions and small disturbances. |
- V. D. Juyal, N. Upadhyay, K. V. Singh, A. Chakravorty and A. K. Maurya, “Comparative Harmonic Analysis of Diode Clamped Multi- Level Inverter,” 2018 3rd International Conference On Internet of Things: Smart Innovation and Usages (IoT-SIU), Bhimtal, India, 2018,
pp. 1-6, doi: 10.1109/IoT-SIU.2018.8519896.
- K. S. Gayathri Devi, S. Arun and C. Sreeja, “Comparison of capacitor voltage balancing techniques in multilevel inverters,” 2014 Annual International Conference on Emerging Research Areas: Magnetics, Machines and Drives (AICERA/iCMMD), Kottayam, India, 2014, pp. 1- 6, doi: 10.1109/AICERA.2014.6908288.
- V. Singh, A. Yadav and S. Gupta, “Open Switch Fault Diagnosis of Three-Phase Battery-Fed Capacitor Clamped Inverter using Machine- Learning Algorithm,” 2023 1st International Conference on Circuits, Power and Intelligent Systems (CCPIS), Bhubaneswar, India, 2023, pp. 1-6, doi: 10.1109/CCPIS59145.2023.10291256.
- A. A. Sneineh and M. -y. Wang, “Spectral Analysis of Hybrid Capacitor-Clamp Cascade 13-Level Inverter,” 2006 IEEE International Conference on Industrial Technology, Mumbai, India, 2006, pp. 271- 276, doi: 10.1109/ICIT.2006.372309.
- N. Sujitha. and K. Ramani., “A new Hybrid Cascaded H-Bridge Multilevel inverter – Performance analysis,” IEEE-International Conference On Advances In Engineering, Science And Management (ICAESM -2012), Nagapattinam, India, 2012, pp. 46-50.
- B. Marisekar, R. Agadeeshpriyan, R. Javaprakash, T. Jayasuriya, B. Sridhar and R. Santhoshkumar, “Fault Reduction in Cascaded H-Bridge Multilevel Inverter,” 2023 2nd International Conference on Edge Computing and Applications (ICECAA), Namakkal, India, 2023, pp. 832-838, doi: 10.1109/ICECAA58104.2023.10212418.
- R. Kumar and B. Singh, “Ensuring High Quality Power for Induction Motor Drive Through Thirty-Pulse Converter and Six-level 3P-2L-C5- VSI,” 2023 IEEE International Conference on Power Electronics, Smart Grid, and Renewable Energy (PESGRE), Trivandrum, India, 2023, pp. 1-6, doi: 10.1109/PESGRE58662.2023.10404144.
- C. Qin and X. Li, “Topology and Improved Selective Harmonic Elimination Method for the Series-Connected T-Type Multi – Level Inverter,” 2023 China Automation Congress (CAC), Chongqing, China, 2023, pp. 5507-5512, doi: 10.1109/CAC59555.2023.10451464.
- A. Bakeer, I. S. Mohamed, P. B. Malidarreh, I. Hattabi and L. Liu, “An Artificial Neural Network-Based Model Predictive Control for Three- Phase Flying Capacitor Multilevel Inverter,” in IEEE Access, vol. 10,
pp. 70305-70316, 2022, doi: 10.1109/ACCESS.2022.3187996.
- ·Y. Y. Ghadi, M. S. Iqbal, M. Adnan, K. Amjad, I. Ahmad and U. Farooq, “An Improved Artificial Neural Network-Based Approach for Total Harmonic Distortion Reduction in Cascaded H-Bridge Multilevel Inverters,” in IEEE Access, vol. 11, pp. 127348-127363, 2023, doi: 10.1109/ACCESS.2023.3332245
- GarcÃa-Gutiérrez, Gabriel & Arcos-Aviles, Diego & Carrera, Enrique & Gispert, Francesc & Motoasca, Emilia & Ayala, Paul & Ibarra Jácome, Oswaldo. (2019). Fuzzy Logic Controller Parameter Optimization Using Metaheuristic Cuckoo Search Algorithm for a Magnetic Levitation System. Applied Sciences. 9. 2458. 10.3390/app9122458.
- Wang, Dali & Bai, Ying. (2007). Implementation of Fuzzy Logic Control Systems. 10.1007/978-1-84628-469-4_3.
- Mencou, Siham & Majid, Ben yakhlef, Benyakhlef & Tazi, El bachir. (2022). Advanced Torque and Speed Control Techniques for Induction Motor Drives: A Review. 1-9. 10.1109/IRASET52964.2022.9738368.
- H. Ait Abbas, B. Zegnini and M. Belkheiri, “Neural network-based adaptive control for induction motors,” 2015 IEEE 12th International Multi-Conference on Systems, Signals & Devices (SSD15), Mahdia, Tunisia, 2015, pp. 1-6, doi: 10.1109/SSD.2015.7348180.
- Ahmad Tarusan, Siti Azura & Jidin, Auzani & Mohd Jamil, Mohd Luqman & Abdulkarim, Kasrul & Sutikno, Tole (2020). A review of direct torque control development in various multilevel inverter applications. International Journal of Power Electronics and Drive Systems (IJPEDS). 11. 1675. 10.11591/ijpeds. v11.i3. pp1675-1688.
- Meesala, R.E.K., Udumula, R.R., Nizami, T.K., Hosseinpour, A.: Development of enhanced direct torque control for surface-mounted permanent magnet synchronous motor drive operation. IET Power Electron. 16, 18141827 (2023). https://doi.org/10.1049/pel2.12504.
IJERTV13IS080021
(This work is licensed under a Creative Commons Attribution 4.0 International License.)
- Upadhyay, Nitin & Singh, K. & Chakravorty, A. & Maurya, Anoop. (2018). Comparative harmonic analysis of Diode clamped multi-level inverter. 1-6. 10.1109/IoT-SIU.2018.8519887
- Hiwase, Umesh & Muley, S.P. & Keswani, R.A.. (2018). Performance Analysis of Diode Clamped Multilevel Inverter. 297-300. 10.1109/ICSEDPS.2018.8536024.
- Alepuz, Salvador, Sergio Busquets-Monge, Joan Nicolás-Apruzzese, Àlber Filbà -MartÃnez, Josep Bordonau, Xibo Yuan, and Samir Kouro. 2022. “A Survey on Capacitor Voltage Control in Neutral-Point- Clamped Multilevel Converters” Electronics 11, no. 4: 527. https://doi.org/10.3390/electronics11040527.
- T. Bertin, G. Despesse and R. Thomas, “Cascaded H-Bridge Multilevel Inverter with a distributed control system for solar applications,” 2022 Smart Systems Integration (SSI), Grenoble, France, 2022, pp. 1-4, doi: 10.1109/SSI56489.2022.9901434.
IJERTV13IS080021
(This work is licensed under a Creative Commons Attribution 4.0 International License.)