
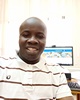
- Open Access
- Authors : Buari T. A , Olutoge F. A , Dada S. A , Ademola S. A, Ayankunle R.A
- Paper ID : IJERTV9IS040462
- Volume & Issue : Volume 09, Issue 04 (April 2020)
- Published (First Online): 27-04-2020
- ISSN (Online) : 2278-0181
- Publisher Name : IJERT
- License:
This work is licensed under a Creative Commons Attribution 4.0 International License
Sustainability of Palm Kernel Shell Ash (PKSA) as SCM in Self-Consolidating Concrete (SCC) Design
Buari T.A1, 2, 3*Olutoge F.A2, 3 Dada S.A3 Ademola S.A4, Ayankunle R.A1
1Department of Building Technology, the Federal Polytechnic Ede, Nigeria
2Faculty of Engineering, the University of the West Indies, Trinidad and Tobago
3Department of Civil Engineering, University of Ibadan, Nigeria
4Department of Building Technology, Osun State Polytechnic Iree, Nigeria
Abstract This research work investigates the rheological (fresh) and hardened properties of self-consolidating concrete (SSC) with Palm Kernel Shell Ash (PKSA) as supplementary cementitious material (SCM). The experimental tests adopted for fresh properties of SCC in this research work, was mainly the Slump Flow test, L-box test, V-funnel test and T50 cm as per
-
standards. The mix design was iterative mix design method of five different proportioned mixes of 0%, 5%, 7.5%, 10% and 12.5% replacement of cement with PKSA as SCM. The mixes were prepared in conformity with [1] specifications. A total of 45 cube samples (150mm x 150mm) and 15 cylindrical samples (150mm x 300mm) were used to examine the hardened properties of SCC experimentally. The cube samples were tested for Compressive strength at curing ages of 7, 28 and 56 days while the splitting tensile strength test was performed on the cylinder samples after a curing age of 28 days. The results of investigation revealed that all the fresh properties of PKSA blended SCC were within the obtainable standard in [1] and the compressive test results showed that 0% 0f PKSA produced 41.33N/mm2 at 56 days, 5% produced 38.40N/mm2, 7.5% produced 36.71N/mm2, 10% produced 33.78N/mm2and 12.5% replacement of cement with PKSA produced 29.50N/mm2 at 56days.The splitting tensile strength test gave strengths of 3.36, 3.18, 3.16, 3.01, and 2.68 N/mm2 for 0%, 5%,7.5%, 10%, and the 12.5% levels of replacement of cement with PKSA respectively at 28days. From the results, it could be that SCC can be produced by substituting cement with PKSA up to12.5% without compromising the workability and the strength of the SSC produced.
Keywords SCC, PKSA, pozzolana, additives, strengths
-
INTRODUCTION
-
Material usage in concrete production would indeed be an interesting area to be studied and investigated. The readily available natural materials can be applied in concrete production as alternative for aggregates, cement, binders or filler to ensure industrial and ecological balance as defined by [2], industrial ecology is a practice which tends to substitute the naturally occurring materials with waste (bi- products) of an industry. Palm kernel shell ash (PKSA), a pozzolanic material gotten from the calcination of palm kernel shell readily available as a waste product from the oil mill industry can be used as partial substitute for cement in self-consolidating concrete. Its applicable in a number of ways, among which are buildings, roads, bridges, dams, retaining structures, stadiums, airports, etc. and due these wide range of its application, the natural law of demand sets
in and this lead to an increase in its price. According to [3], its usage is around 10 billion tons per year, which is tantamount to 1 ton per man. With the world population increasing at a geometric rate, the need for shelter, infrastructure, and work places also increases as these are the essential needs of man. Self-compacting concrete (SCC), a new kind of high performance concrete (HPC) with excellent deformability and segregation resistance, was first developed in Japan in 1986. It is a special kind concrete that can flow through and fill the gaps of reinforcement and corner of molds without any need for vibration and compacting during the placing process. Additives or admixtures are used to alter and improve hardened properties of concrete; they may enhance the durability, workability or strength characteristics of a given concrete mixture. A lot researches had been done on the use of mineral additives other than PKSA such as: High volume natural pozzolana and lime stone [4], Coconut shell aggregate [5], Palm oil fuel ash [3],rice husk ash, sawdust and palm kernel shell,[6]; Groundnut Shell Ash (GSA),[7] and Periwinkle Shell Ash(PSA), [8].
MATETRIALS AND METHOD
Materials used
Materials used for this study were; cement, Palm kernel shell ash (PKSA), Fine Aggregate (FA), Coarse aggregate(CA), Water, Super Plasticizer (COMPLAST SP430). The cement utilized in this study was Grade 32.5 cement which satisfies [9]. The shells were collected from a local oil mill located at Ikoyi-Ile in Ikoyi, Osun State. Thereafter, they were washed, filtered thoroughly to remove sand and other particles and sun dried. The shells were weighed and burnt into ashes at the foundry laboratory, university of Ibadan in the furnace at a temperature of 800-10000C as obtained from the Chapelles test conducted on the ash. The chemical and physical analysis of the PKSA and aggregates used are presented in table1- table3 below. The aggregates complied with the requirement of [10]. Super-plasticizer (SP430) conforming to [11] was also used to improve the rheological properties of the concrete.
Experimental work
Chapelle test, one of the tests used in determining the reactivity of pozzolanic materials as well as their optimum calcine temperature. The test followed [12] as stated by [13].
Based on the result obtained from the test, the PKSA used for this study was obtained from palm kernel shell calcined at a temperature of 8500C.Sieve analysis of fine aggregates was carried out as specified in [14] using sieve size of 6.3mm,4.75mm,2.36mm,1.18mm, 600um, 300um, 150um, and 75um as shown in the table 2 and figure 1 below and the coefficient of uniformity (Cu) and coefficient of curvature (Cc) being 1.45 and 0.96 respectively with the percentage passing the 600um sieve being 47% which is less than 51% as stated by [12] in his book, Self- Consolidating concrete; applying what we know that sand to be used for SCC production, the percentage passing the 600um sieve shouldnt be >51%.
Table 1.0 OPC vs PKSA(chemical composition)
Chemical Composition |
OPC |
PKSA |
SiO2 |
17.26 |
42.62 |
Al2O3 |
4.19 |
2.41 |
Fe2O3 |
2.36 |
5.80 |
CaO |
61.72 |
4.20 |
MgO |
1.04 |
2.22 |
Na2O |
0.04 |
1.31 |
K2O |
0.41 |
0.60 |
SO2 |
1.63 |
0.03 |
MnO |
– |
0.006 |
P2O2 |
– |
0.004 |
Moisture Content |
– |
0.008 |
LOI |
0.04 |
0.76 |
Sieve size (mm) |
Table 2: Mass retained (g) |
Particle Siz %retained |
e Distribution Cumulative %retained |
%passing |
|
6.3 |
10.0 |
2.5 |
2.5 |
97.5 |
|
4.75 |
14.0 |
3.5 |
6 |
94 |
|
2.36 |
38 |
9.5 |
15.5 |
84.5 |
|
1.18 |
44 |
11 |
26 |
73.5 |
|
0.60 |
106 |
26.5 |
53 |
47 |
|
0.30 |
144 |
3.6 |
89 |
11 |
|
0.15 |
14 |
3.75 |
92.75 |
7.25 |
|
0.75 |
16 |
4 |
96.75 |
3.25 |
|
PAN |
6 |
1.5 |
98.25 |
– |
Figure 1: Particle Size Distribution
Table 3: Physical properties of materials
Properties |
Fine Aggregate |
Coarse Aggregate |
PKSA |
Aggregate size (mm) |
10 |
4.5 |
– |
Water absorption (%) |
0.42 |
1.23 |
– |
Specific gravity |
2.62 |
2.73 |
1.21 |
Fineness modulus (FM) |
2.38 |
– |
– |
%passing the 600micron sieve |
41 |
– |
100 |
Coefficient of uniformity (Cu) |
1.45 |
– |
– |
Coefficient of curvature (Cc) |
0.96 |
– |
– |
Proportion of Samples
After series of trial mixes all aiming at designing a mix that will conform to the [1] specification and based on the specification, a mix design was adopted and the mix design combination is shown in table 4 below.
Table4: SCC Combination
MIX |
CEMENT (kg) |
PKSA (kg) |
FINE AGGREGATE (kg) |
COARSE AGGREGATE (kg) |
WATER (kg) |
WATER CEMENT RATIO |
SUPER PLASTICISER (kg) |
0% |
22.13 |
– |
48.68 |
45.81 |
9.07 |
0.41 |
0.443 |
5% |
21.03 |
1.11 |
48.68 |
45.81 |
8.62 |
0.41 |
0.421 |
7.5% |
20.47 |
1.66 |
48.68 |
45.81 |
8.39 |
0.41 |
0.409 |
10% |
19.92 |
2.21 |
48.68 |
45.81 |
8.17 |
0.41 |
0.398 |
12.5% |
19.36 |
2.78 |
48.68 |
45.81 |
7.94 |
0.41 |
0.387 |
TOTAL |
102.91 |
7.76 |
243.42 |
229.05 |
42.19 |
2.058 |
III RESULTS AND DISCUSSION
The tests to be carried on Self compacting concrete are in the dimensions which includes the;
-
The fresh state property tests and
-
The hardened state property tests
The fresh state property tests
For a self-compacting concrete mix to be workable, the mix must be subjected to the three important tests (Filling ability, passing ability, and Segregation resistance test) to be carried out on the mix in its fresh state. In this research, the Slump- flow by Abram cone and the V-funnel was adopted for Filling, ability test, the V-funnel at T5mins for the Segregation resistance and the L-Box test for passing ability as shown in table 4 and figures 3-7. The tests were carried in order to ensure that the SCC produced passes the required tests as specified in [13] guidelines for SCC production. The apparatus for the tests is shown in figure2 below.
Figure 2: Test Apparatus for the fresh properties test
For the hardened state property test, compressive strength test was carried out on the cubes at all levels of replacement including the control at curing ages 7, 28 and 56days. Also, splitting tensile strength was as well carried out on the cylinders at all levels of replacement with the control inclusive at a curing age of 28days.
Slump flow test method
The slump flow is the test used in the assessment of the filling ability of self-consolidating concrete (SCC) i.e. its ability to flow under its own weight in the without blockage. The test was carried on the fresh concrete mix by the filling the freshly prepared SCC into the cone without vibration, compaction or any form of consolidation, the cone is lifted and the SCC is allowed to flow. The suggest three classes for the slump flow according to the final spread which are SF1, SF2 and SF3 with flow diameters 550-650, 660-750 and 760- 850 respectively.
L box test method
The L-Box test is a test used to access the ability of the SCC flow through when obstructed by reinforcements. For a good SCC mix design, the blocking ratio (H2/H1) must fall within the range 0.8-1.0 [15]. It is an indication to the slope of the concrete when at rest, (i.e. an indication of passing ability) or a reveal of the degree to which the passage of concrete through the bars is restricted. The [15] suggest two classes according to H2/H1 ratio, PA1 and PA2 with passing ability
0.80 with 2 bars and 0.80 with 3 bars.
V-Funnel test
The V-funnel test was conducted according to [15]guidelines to evaluate the filling ability and the V-funnel at T5mins for the Segregation test of SCC by measuring the time the concrete needs to flow through the V-funnel under its own weight. The
-
guidelines suggest two classes according to the V-funnel time, VS1/VF1 with T50 spread time 2 and v-funnel time 8; VS2/VF2 with T50 spread time>2 and v-funnel time 9- 25seconds.
Figure 3: L-Box and V-Funnel Tests
Results obtained from the fresh state property test are summarized in table 4 below.
MIX (% PKSA)
Table 4: fres
SLUMP FLOW DIAMETER(mm)
hstate property t
T50 FLOW
TIME(seconds)
est results
V-FUNNEL TEST FLOW
TIME(seconds)
L- BOX TEST H1/H2
0
680
3.09
10.00
0.93
5
676
3.22
9.6
0.91
7.5
663
3.43
9.1
0.89
10
658
3.82
8.5
0.83
12.5
652
4.92
8.1
0.81
MIX (% PKSA)
Table 4: fres
SLUMP FLOW DIAMETER(mm)
hstate property t
T50 FLOW
TIME(seconds)
est results
V-FUNNEL TEST FLOW
TIME(seconds)
L- BOX TEST H1/H2
0
680
3.09
10.00
0.93
5
676
3.22
9.6
0.91
7.5
663
3.43
9.1
0.89
10
658
3.82
8.5
0.83
12.5
652
4.92
8.1
0.81
Hardened Properties of SCC
The hardened stte property tests are the test which include the compressive test and the splitting tensile strength test were conducted on the SCC in its hardened state.
Compressive strength test of SCC
The cubes were tested after curing age of 7, 28 and 56days at all levels of replacement including the control mix. The compressive strength was computed by dividing the ultimate
load by the cross sectional area of the cube. Three specimens
were tested for each of the curing days and the average of three values is then taken to determine the compressive strength of concrete. The test was carried out as described in [14]. As presented in Table 5 and figure 8, the compressive strength of SCC ranged from 12.36 -18.67N/mm2, 27.47 32.66N/mm2and 29.56 – 41.33N/mm2at 7, 81 and 56days respectively. Generally, the strength increases with the curing age for all the prepared mixes. The compressive strength of SCC at 7 days, 21 days, and 28 days were 18.67N/mm2, 32.66N/mm2, and 41.33N/mm2for 0% PKSA; 16.44N/mm2,
30.44N/mm2and 38.40N/mm2for 5%PKSA; 15.78N/mm2,
29.99N/mm2and 36.71N/mm2for 7.5%PKSA; 14.22N/mm2, 28.36N/mm2 and 33.78N/mm2for 10%PKSA and 12.36N/mm2, 27.47N/mm2and 29.56N/mm2for 12.5%PKSA; respectively. The percentage variation in compressive strength of SCC dosed with 5%, 7.5%, 10% and 12.5%
Figure 5: T50cm flow time
Figure 6: Slump flow Test
Figure 7: L-Box test
PKSA as expressed in terms of their control sample (0% PKSA) were -11.9%, -15.5%, -23.8% and -33.8%
respectively at 7 days; -6.8%, -8.3%, -13.2% and -15.9%
28days; -7.1%, -11.2%, -18.3%, and -28.5% at 56days
respectively.
From the results obtained as shown in the charts and tables, it could be observed that the compressive strength of all the samples under study regardless of their levels of replacements (0, 5, 7.5, 10, and 12.5% PKSA) increased with time but though lower than that of the mix without PKSA irrespective of curing age. This work contravenes the works of some researchers [17, 18], with the research findings of [17], it could be observed that, in all sample mixes of the self- consolidating concrete incorporated with PKSA under study, there was reduction in their strength when compared with the mix without PKSA as the strength decreases with increasing percentage of PKSA content and this agrees with conclusions drawn from the research and findings of [18].However, the obtained results in this research is in line with the findings of
-
as this same trend was followed when he replaced cement with PKSA in term of compressive strength properties.
Table 5: Compressive Strength Test
Compressive Strength (MPa)
Mix
Age (Days)
7
28
56
0%PKSA
18.67
32.66
41.33
5%PKSA
16.44
30.44
38.44
7.5%PKSA
15.78
29.96
36.71
10%PKSA
14.22
28.36
33.78
12.5%PKSA
12.36
27.47
29.56
Figure 8: Compressive Strength Test
Splitting Tensile Strength Test
In an attempt to determine of the split tensile strength of Self- Compacting Concrete samples, three cylindrical shaped specimens of diameter 150mm and height 300mm casted earlier at all levels of replacement including the control were crushed with the cylinders lying on their sides. The tests were conducted on cylinders at a curing age 28 days. The results obtained from the tests are tabulated below. The results of split tensile test obtained at 28days are displayed in Table 6 while the graphical illustrations of result are presented in Figure 9. The split tensile strength dosed with 0%PKSA; 5%PKSA; 7.5%PKSA; 10%PKSA and 12.5%PKSA were
3.36N/mm2, 3.18N/mm2, 3.16N/mm2, 3.01N/mm2 and 2.68N/mm2 at 28 days respectively. From the results, it can be deduced that the splitting tensile strength of the samples decreased as the PKSA dosage is increased as they were less than the control at all levels of replacement. From these results, the reduction in strength of SCC incorporating 5%PKSA was -5.4; 7.5%PKSA, -6.0%; 10%PKSA, -10.4%
and 12.5%PKSA, -20.2%. However, the split tensile result of SCC obtained from this present study corroborates with the deduction made by [19]as the same trend was followed in their research.
Table 6: Splitting Tensile Strength Results
S/N
MIX OF PKSA (%)
SPLITTING TENSILE STRENGTH (N/mm2)
I
0
3.36
II
5
3.18
III
7.5
3.16
IV
10
3.01
V
12.5
2.68
Figure 9: Splitting Tensile Strength Results at 28 days
IV CONCLUSION
The rheological properties of self-compacting concrete for five mixes of SCC with being substituted with PKSA at various levels (0%, 5%, 7.5%, 10%, and 12.5%) with the 0% acting as control were determined. The Hardened state property tests carried out on the SCC with the same levels of substitution of cement with Palm Kernel Shell Ash were the compressive and the splitting tensile strength tests. This chapter presents the conclusion and recommendations drawn based on the research work conducted in this study. From the results obtained from the tests carried on a mix of SCC with 0, 5, 7.5, 10, and 12.5% levels of replacement of cement with PKSA, the following conclusion and recommendations were made:
-
Palm kernel shell ash (PKSA) was found to contain virtually, all the main chemical elements of cement though in varying proportions compared to that of cement, which means it can replace cement in a quantity.
-
The results obtained from the study encourage the use of PKSA as a pozzolanic material for partial cement replacement in production of SCC, and this will to a great extent reduce the cost of production, ecological problems and the landfill area required for the discarding of palm kernel shell.
-
The workability of the mixes of SCC incorporated with PKSA as partial substitute for cement at (0, 5, 7.5, 10 & 12.5%) conforms to the [13] specifications for self-consolidating concrete as the results obtained were within the upper and lower limits.
-
From the results obtained as shown in the charts and table, it was observed that all the sample mixes under study (0, 5, 7.5, 10, and 12.5% PKSA) all recorded a reduced compressive strength values as the percentage of the PKSA content increases regardless of the curing age.
-
The use of feasible super plasticizer agents in self- consolidating concrete production is a key to achieving a mix with satisfactory properties.
-
V ACKNOWLEDGEMENT
We acknowledge the contribution of Department of Civil Engineering of The University of Ibadan, Nigeria towards the conduct of this research. We also acknowledge the guidance and support of Engr. Wole Labiran (PhD) for granting the access to his laboratory for research practical work.
VI REFERENCES
-
European Federation of National Associations for Representing Concrete (EFNARC), (2005).
-
Mehta, P. K. (2001). Reducing the Environmental Impact of Concrete. Concrete International, V. 23, No. 10.
-
Ismail Mohamed A. (2009). Study on the Properties of Palm Oil Fiber. Faculty of Civil Engineering Universti Teknologi Malaysia, 93.
-
K. Celik , M.D. Jackson , M. Mancio , C. Meral , A.-H. Emwas ,
P.K. Mehta , P.J.M. Monteiro, High-volume natural volcanic pozolan and limestone powder as partial replacements for portland cement in self-compacting and sustainable concreteJournal;Cement and Concrete Composites, 45 ISSN0958- 9465.DOI10.1016/j.cemconcomp.2013.09.003.https://escholarship.o rg/uc/item/6mq3j47).
-
Idowu H. Adebakin, K. Gunasekaran and R. Annadurai, Mix design and rheological properties of self-compacting coconut shell aggregate concrete ARPN Journal of Engineering and Applied Sciences; VOL. 13, NO. 4, FEBRUARY 2018 ISSN 1819-6608; www.arpnjournals.com.
-
Olutoge, F.A. (1995). A Study of Sawdust, Palm Kernel Shell and Rice Husk Ash as Full/ Partial Replacement for Sand, Granite and Cement in Concrete: Unpublished M.Sc thesis, Department of Civil Engineering, University of Lagos Nigeria. Res.;18(6): pg.901-910
-
Buari T.A, Ademola S.A, Ayegbokiki S.T,Short term durability study of groundnut shell ash blended Self-ConsolidatingHigh Performance Concrete in sulphate and acid environments Article inAsian Journal of Civil Engineering · March 2019.DOI: 10.1007/s42107-019-00131-3
-
Festus A.Olutoge, Oriyomi M. Okeyinka & Olatunji S. OlaniyanAssessment of the suitability of Periwinkle Shell Ash (PSA) as partial replacement for Ordinary Portland Cement(OPC)inconcreteIJRRAS10(3).www.arpapress.com/Volume s/Vol10Issue3/IJRRAS_10_3_08.pdf March 2012
-
BS EN 1008:2002. Mixing water for concrete. Specification for sampling, testing and assessing the suitability of water, including water recovered from processes in the concrete industry, as mixing water for concrete.
-
BS 882: (1992). Specification for Aggregates from natural sources for concrete. British Standards Institute, London, U.K.
-
Loland, K.E. 1983. Fasthets-og deformasjonsegenskaper i herdnet tilstand herdebetingelser. Seminar Bruk av silika i betong, Norsk Sivilingeniorers Forening, Oslo (in Norwegian
-
NF P18-513:2010. Metakaolin pozollanic addition for concrete definitions, specifications and conformity criteria. Association Françoise de Normalization, La plaine saint Denis, (in French).
-
Pontes, J.; santos Silva, A.; Faria, P. – Evaluation of pozzolanic reactivity of artificial pozzolans. Trans Tech Publications, Switzerland, Materials Science Forum 730-732 (2013), 433-438 (doi:10.4028/www.scientific.net/MSF.730-732).
-
British Standards Institution12390-3:2002. Testing of hardened concrete. Compressive strength of test specimens.
-
Daczko, J. A. (2012). Self-consolidating concrete: applying what we know: CRC Press
-
Sanket R. Jagtap, Shashi Ranjan Pandey, Flexural Behaviour of Self-Compacting Concrete with Partial Replacement of cement by Rice Husk Ash. June, 2018.
-
Sylvester Okoth Odhiambo and B. I. Lukuman, Investigation of the properties of self-consolidating concrete with PKSA as SCM.JCECT, 9(2), (2018): 11-18
-
Xie Younjun, Liu Baoju, Yin Jain, Zhou Shinqiong Optimum mix parameter of high strength self-compacting concrete (HSSCC) with ultrapulverised fly ash with ultra-pulverized fly ash. Cement and Concrete Research 32 (2002):477-480. http://www.paper.edu.cn