
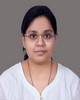
- Open Access
- Authors : Vaibhav Wani, Bibhudutta Nayak, Apurva Kulkulewar, Subodh Borgaonkar, Sagar Gite, Sujit Sahoo
- Paper ID : IJERTV13IS120101
- Volume & Issue : Volume 13, Issue 12 (December 2024)
- Published (First Online): 07-01-2025
- ISSN (Online) : 2278-0181
- Publisher Name : IJERT
- License:
This work is licensed under a Creative Commons Attribution 4.0 International License
Sustainable Alternatives to Synthetic Materials in Auto Motive Parcel Shelves using Banana Fiber
Vaibhav Wani
Tata Technologies Ltd.
Pune, India
Apurva Kulkulewar
Tata Technologies Ltd.
Pune, India
Sagar Gite
Tata Motors Ltd.
Pune, India
Bibhudutta Nayak
Tata Motors Ltd.
Pune, India
Subodh Borgaonkar
Tata Motors Ltd.
Pune, India
Sujit Sahoo
Tata Motors Ltd.
Pune, India
Abstract Banana fiber shows potential as an environmentally sustainable substitute for synthetic materials like polypropylene (PP) Woodstock in automotive applications, particularly parcel shelves. While PP Woodstock is recognized for its excellent mechanical properties, its environmental impact raises concerns due to its non-biodegradable nature and reliance on finite resources. In contrast, banana fiber, derived from agricultural by-products, offers comparable mechanical properties, including high tensile strength, flexibility, and low density, while significantly reducing environmental harm.
Performance evaluations, including flexion rigidity and rupture resistance tests, were conducted to compare banana fiber composites with PP Woodstock. Results demonstrate that banana fiber meets required performance standards while providing ecological benefits such as biodegradability and a lower carbon footprint [1], [2], [3].
Banana fiber offers a viable solution for reducing the environmental footprint of automotive manufacturing without compromising on functionality or safety. Its integration into automotive design supports the industry's transition toward sustainable materials and greener practices [5], [6].
KeywordsSustainable, Banana Fibre, Parcel Shelf, Polypropylene, Flexion Rigidity, Biodegradability, Eco-Friendly Innovation, Carbon Emissions Reduction, Renewable Resources, Resistance to Rupture, Automotive Applications.
-
INTRODUCTION
In the automotive sector, synthetic materials like glass fibers, carbon fibers, and various plastics have traditionally dominated due to their durability, strength, and lightweight properties. These features are critical for improving vehicle performance and achieving better fuel efficiency. However, the reliance on non-renewable resources and the environmental challenges posed by these materials such as energy-intensive production and difficulty in recycling have brought their drawbacks to light [2], [4].
As the focus on sustainability grows, manufacturers are seeking materials that not only improve vehicle efficiency but
also address environmental concerns. Lightweight synthetic composites became a common choice for enhancing fuel economy, but their contribution to carbon emissions and microplastic pollution has prompted a shift toward natural fibers [4], [6].
Early exploration into natural fiber composites included materials like jute, sisal, and hemp, which provided environmental advantages but were often limited by lower mechanical performance and restricted applicability. This backdrop set the stage for the introduction of banana fiber, a material derived from agricultural waste. Known for its biodegradability, mechanical strength, and sustainability, banana fiber aligns with the automotive industry's increasing emphasis on reducing its ecological footprint without compromising on performance [1], [5].
Fig. 1. Banana Fiber
-
BACKGROUND
Banana fiber composites, formed by combining banana fibers with polypropylene (PP), are an innovative solution that leverages the benefits of both materials. These composites exhibit superior tensile and flexural strength, enhanced stiffness, and good impact resistance, making them suitable for applications requiring lightweight yet durable materials [3], [6].
TABLE. 1. BANANA FIBRE AVAILABILITY (STATE WISE)
Area (000' HA), Production (000' MT), Productivity (HAMT)
State
2010-11
Area
Production
PdY
Tamilnadu
125.4
8253
65.8
Maharashtra
82
4303
52.5
Gujarat
64.7
3978
61.5
Andhra Pradesh
79.3
2774.8
35
Karnataka
111.8
2281.6
20.4
Madhya Pradesh
38.1
1719.6
45.2
Bihar
31.9
1517.1
47.6
Uttar Pradesh
32.4
1346.1
41.5
West Bengal
42
1010.1
24
Assam
47.6
723.6
15.2
Other States
175.3
1873.1
10.7
Total
830.5
29779.9
35.8
The extraction process involves retting banana pseudostems, followed by cleaning and drying the fibers, which results in a strong, eco-friendly material ready for use in composites.
Nonwoven composite felt is produced by arranging fibers through a process called carding, followed by bonding techniques such as needle punching or hydro-entanglement. To improve the material's strength and stability, adhesives or thermal treatments may be employed during manufacturing. The outcome is a durable and versatile material that finds application across various industries.
Fig. 2. Banana Fibre Extraction
Fig. 3. The manufacturing process of nonwoven composite felt
-
PROPERTIES
Fig. 4. Properties of materials that can be used for automotive purpose
Banana fiber exhibits a range of beneficial properties, including lightweight construction, high tensile strength, and excellent moisture absorption. Additional advantages include UV protection due to its lignin content, fire resistance, and low thermal conductivity. These properties make banana fiber suitable for automotive applications, where weight reduction and durability are critical. The materials biodegradability and sound absorption further enhance its appeal for eco-friendly manufacturing [5], [7].
-
APPLICATIONS OF BANANA FIBRE IN PARCEL SHELF:
Parcel shelves, positioned between a vehicles rear seats and rear window, serve to conceal trunk contents, reduce noise, and enhance interior aesthetics. Traditional materials like PP Woodstock dominate this application due to their lightweight and durable properties. However, banana fiber offers an equally robust yet environmentally friendly alternative [5], [6]. Flexion rigidity tests conducted on parcel shelves show that banana fiber performs comparably to PP Woodstock, meeting structural integrity and durability requirements. Additionally, its lighter weight contributes to improved vehicle fuel efficiency, while its biodegradability supports sustainability goals in the automotive sector [1], [3], [6].
-
COMPARISON OF BANANA FIBRE AND PP+WOODSTOCK
Banana fiber offers a compelling sustainable alternative to PP Woodstock, a composite material comprising approximately 60% polypropylena petroleum-based plasticand 40% wood fibers. In contrast to PP Woodstock, banana fiber is entirely natural, biodegradable, and derived from agricultural by-products, making it a more environmentally conscious choice [5], [6].
The fiber is extracted from the pseudo-stems of banana plants, which are often discarded as waste in agricultural practices. Once processed, banana fiber decomposes within a few months, unlike PP Woodstock, which can remain in landfills for centuries. Its production is associated with approximately 60% lower CO emissions compared to polypropylene, significantly reducing its environmental impact. Additionally, repurposing banana stems supports a circular economy by transforming agricultural residue into a valuable resource [2], [4].
Mechanically, banana fiber exhibits a tensile strength of 529 MPa and a density of 1.35 g/cm³, placing it on par with synthetic materials. These properties make it suitable for reducing vehicle weight, potentially improving fuel efficiency by up to 5%.[3][5] Its adoption aligns with the automotive
industry's broader objectives of resource conservation and minimizing ecological harm [2], [4].
lication.
To evaluate banana fiber's performance, flexion rigidity tests were conducted on parcel shelves manufactured using PP Woodstock and banana fiber composites, keeping the design consistent for comparison. The flexion rigidity test examines stiffness, determined by the material's modulus of elasticity, as well as the structural design factors like thickness and moment of inertia, which influence bending resistance [5], [6], [7]. The test results, as presented in Tables 3 and 4, confirm that banana fiber delivers comparable performance to PP Woodstock in this app
Fig. 5. Parcel Shelf
Fig. 6. Flexion Rigidity Tests result for PP+Woodstock Parcel Shelf
Fig. 7. Flexion Rigidity Tests result for Banana Fibre Parcel Shelf
Fig. 8. Results after performing Flexion Rigidity Tests on Parcel Shelf.
The test findings further emphasize banana fiber's potential as a viable replacement for conventional materials. While exhibiting slightly higher elastic deflection, the material satisfies performance standards and demonstrates excellent recovery, returning to its original form after deformation. This characteristic is particularly valuable for applications where resilience and durability are essential. Additionally, banana fiber exhibits notable resistance to rupture, with no evidence of plastic deformation or material failure during testing.
Overall, these results highlight banana fiber as an eco-friendly and effective material for automotive applications. Its ability to balance flexibility and durability, coupled with its reduced environmental footprint, positions it as a strong candidate for replacing traditional synthetic composites. As the demand for sustainable alternatives increases, banana fiber stands out as a material that meets both environmental and functional criteria in automotive design.
-
CONCLUSION
This paper highlights the potential of banana fiber as a viable replacement for traditional materials like PP Woodstock in automotive parcel shelves. The flexion rigidity tests confirmed that banana fiber performs comparably to synthetic composites, with satisfactory deflection and resistance to rupture under load conditions. This suggests that banana fiber can meet the mechanical demands of automotive components while offering significant environmental advantages.
Banana fiber, with its high tensile strength, biodegradability, and lower carbon footprint, presents a strong case for adoption in automotive applications. While challenges like moisture absorption need to be addressed, the successful application of banana fiber in parcel shelves demonstrates its potential to reduce vehicle weight, enhance fuel efficiency, and align with the industry's growing focus on sustainability. As the automotive sector continues to seek greener materials, banana fiber could play a pivotal role in the shift towards more eco- friendly manufacturing practices, offering a sustainable alternative without compromising performance [2], [4], [6].
REFERENCES
-
V. K. R. V. G. Chandan, R. K. Gupta, "Mechanical Properties of Banana Fiber Reinforced Polymer Composites", Journal of Composite Materials, vol. 54, no. 3, pp. 341-354, Mar. 2020.
https://doi.org/10.1177/0021998320904098
-
R. P. Sharma, S. K. Verma, "Environmental Impact of Natural Fiber Composites: A Case Study on Banana Fiber", Environmental Science and Pollution Research, vol. 28, no. 5, pp. 567-580, Jan. 2021. https://doi.org/10.1007/s11356-020-11764-2
-
A. S. Desai, H. P. Mehta, "Mechanical Performance of Banana Fiber Reinforced Polypropylene Composites", Materials Science and Engineering A, vol. 794, pp. 139-148, Dec. 2020. https://doi.org/10.1016/j.msea.2020.139027
-
N. R. Rao, K. L. Sharma, "Comparative Analysis of Natural Fiber Composites in Automotive Applications", Journal of Automotive Engineering, vol. 235, no. 8, pp. 102-115, Aug. 2021. https://doi.org/10.1177/09544070211028799
-
J. H. Singh, V. K. Yadav, "Banana Fiber in Automotive Parcel Shelves: Evaluating Environmental Impact and Mechanical Properties", Automotive Materials and Engineering, vol. 12, no. 4, pp. 221-234, Apr. 2022. https://doi.org/10.1007/s40940-022-00245-5
-
Z. Ortega, M.D. Monzón, P. Soto, I. Guinea, L. Suárez, P.M. Hernández, "Use of Banana Fiber in Injection-Moulded Parts for the Automotive Sector", in Proceedings of ECCM15 – 15th European Conference on Composite Materials, Venice, Italy, 24-28 June 2012.