
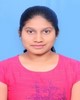
- Open Access
- Authors : Sushma U B , Rakshitha K P , Yashwanth Raj R , Shilpa B S
- Paper ID : IJERTV12IS050133
- Volume & Issue : Volume 12, Issue 05 (May 2023)
- Published (First Online): 17-05-2023
- ISSN (Online) : 2278-0181
- Publisher Name : IJERT
- License:
This work is licensed under a Creative Commons Attribution 4.0 International License
Sustainable Approach in Noise Control using Natural Fibres-A Review
Sushma U B
UG Student, Department of Civil Engineering Vidyavardhaka College Of Engineering Mysuru, India
R Yashwanth Raj
UG Student, Department of Civil Engineering Vidyavardhaka College Of Engineering Mysuru, India
Rakshitha K P
UG student, Department of Civil Engineering Vidyavardhaka College Of Engineering Mysuru, India
Shilpa B S
Associate Professor, Department of Civil Engineering Vidyavardhaka College Of Engineering
Mysuru, India
AbstractNoise generally indicates unwanted sound emerging from sources in the environment with a greatvariety of frequencies. In the last two decades, noise pollution has been emerging as a significantenvironmental concern to public health. Noise pollution impacts millions of people daily. The most common health problem it causes is Noise Induced Hearing Loss (NIHL). Exposure to loud noise can also cause high blood pressure, heart disease, and stress. One major solution for this problem is using noise or sound insulation material acting as a sound transmission medium. There are several speciality materials available for sound control. These are designed to provide strategic advantages over traditional materials. Generally, Noise barriers are made up of steel, concrete, glass, and rock wool. In the last few years, many new materials for noise control have been studied and developed as alternatives to the traditional ones, these materials are either natural or recycled for sustainable applications.
Keywords – Sustainable, Noise barrier, Natural fibers, Sound absorption
than 55% of the population has been started to live in urban cities (Kesten et al., 2020)
Noise pollution has become a major concern worldwide. Many researchers have come forward sharing views and conducting studies pertaining to the noise issue. Whilst majority agrees at some level that the current traditional sound absorption panels using synthetic materials such as glass, mineral wool, felts or polyester fibers are the solution to the noise problems, others on the other hand voice out concerns on the health and environmental impacts of such synthetic materials. Thus, new research on sustainable sound absorption panels is now trending. By looking at the current hype of green and sustainable approach, waste is now the major highlight as the possible alternative (Ismail et al., 2014).
-
CONVENTIONAL BARRIER
-
INTRODUCTION
Noise control is an important issue in modern life. A lot of factors contribute to its increase, e.g., population growth, expansion of the urban centers, densification of the housing sector, correlated to the number of vehicles, the development of automatic machines in industrial companies and devices. Noise pollution is the second most important environmental factor in Europe, North America and South-East Asia, contributing to different diseases after air pollution. People of all age groups are becoming more vulnerable to mental stress, heart diseases, sleep disturbance, tinnitus, learning disabilities etc (Tudor et al., 2020)
Despite the recognition of the importance to reduce environmental noise has had a lower priority than that the other environmental problems such as air and water pollution, noise pollution is one of the phenomena that should be addressed in many cities in the world. The adverse impacts of transportation related noise in general and road traffic noise on the society have gained recognition in the last 40 years in the world where more
Kesten et al., 2020 have worked on Acoustic and structural
design of a highway noise barrier. The aim of this study is to evaluate the noise mitigation capabilities, aesthetic features and costs of acoustic designs for the residential buildings located near the urban highway and evaluate the structural performances against wind and earthquake. Through the interviews, the designs higher than 10m are not found acceptable by the residents and also due to the aesthetic concerns the upper part of the noise barrier is set to be constructed as glass. Therefore, the noise reduction capabilities and construction cost and the alternatives that complies with the constraints are determined and the corresponding costs are calculated accordingly. Noise simulation software is used to identify the effectiveness of selected noise barriers and structural analysis and design software is used to evaluate the structural performance. The results show that designed precast lightweight concrete and glass composite noise barrier meet the required noise reduction goal along with a resilient structural performance and affordable cost.
-
-
NOISE BARRIER FROM WASTE MATERIAL
Ismail et al., 2014 have carried out the work on producing sustainable absorption panels from agricultural wastes. The study shows the fabrication of particle board using coconut coir powder (CCP) mixed with shredded wastepaper (SWP) using gypsum as binder. The panel was fabricated in different mix ratio 25% of CCP with 75% of SWP for sample 1, 50% both material for sample 2, 75% CCP mixed with 25% of SWP for sample 3, and lastly 100% of CCP for sample 4. The absorption coefficient was tested in a reverberation chamber. Based on the results, sample 1 gave the highest absorption coefficient compared to sample 2, 3 and 4. It can be concluded that the acoustic panel made from a mixture of 25% coconut coir powder with 75% shredded wastepaper provided higher absorption coefficient compared to the performance of the other samples. This might be due to the size of the coir powder, which is very small, creating less void space in between the panel and thus causing it to absorb less sound, since it is very much affected by the availability of void space of the panel.
Shahrzad Mehrzad et al., 2022 Carried out research on using sugarcane bagasse waste (SBW) fibers as thermal insulation and sound-absorbing materials for application in sustainable buildings. SBW is an eco-friendly material used to fabricate fibrous samples of different densities and thicknesses. The SBW fibers were obtained from the sugar processing plants and washed with distilled water to remove any particles and contaminants and then dried at 60C until reaching a constant weight. Afterward, the SBW was fed to a grinder to obtain fine fibers then sieved to remove fiber clumps. Polyvinyl alcohol as a non-toxic, biodegradable, and water-soluble polymer was used as the binder to fabricate the specimens, by using guarded hot plate and impedance tube techniques The thermal insulation and sound absorption performance of the specimens were investigated. The thermal conductivity values of the specimens were found to range between 0.034 and 0.042 W/mK. The sound absorption average (SAA) and noise reduction coefficient (NRC) of the prepared samples were between 0.26-0.64 and 0.270.62 it shows that SBW fibers shows good performance in the low- and mid-frequency ranges.
Beom yeol yun et al., 2020, have carried out research work on circular reutilization of coffee waste for sound absorbing panels. In this paper, coffee waste sound absorption materials was manufactured using coffee waste and urea resin as an adhesive. The manufacturing process is divided into a dry process and composite process. The drying process of the coffee waste was calculated according to ISO12570 and dried for 24h at 105°C. After the drying process it is sieved by 300mm, medium size 300mm to 600mm. the coffee volume used was 25 g, 30 g and 35 g. For the binder role of urea resin, it was mixed with 25% solution of ammonium chloride in a ratio of 100:3 and themixed urea resin used 50% compared to weight of the coffee paste and it is heated at 140°C for 15 minutes as the manufacturing of coffee waste sound
absorption was completed. The size of the manufactured coffee waste sound absorption panel is of width 45mm and height 50mm. Each density is 0.4 g/cm3, 0.5 g/cm3 and 0.6 g/cm3 in order of decreasing density. The performing SEM analysis, BET analysis, sound absorption coefficient measurement with impendence tube method and compressive strength assessment. The highest sound absorption coefficient was observed at 0.4 g/cm3 density, which is the lowest density of the three different density type samples. In addition, D50 of up to 0.8 was shown above 500 Hz after the application of the manufactured sound absorbing material in the cafe. The reverberation time was also reduced from 1.2 s without sound absorbing material to 0.7 s with CWSA. The sound pressure level was reduced by 7 dB
Azma Putra et al., 2022, have studied Performance and Acoustic Characterization of Waste Durian Husk Fibers as Natural Sound Absorber. The paper presents the sound absorption coefficient of acoustic absorbers fabricated from natural durian husk fibers. Samples fabricated with different fiber densities and thicknesses and the sound absorption performance was measured using the impedance tube method. The results reveal that the durian husk fibers can have absorption coefficient of more than 0.5 above 1 kHz for a minimum thick sample of 20 mm and with minimum density of 160 kg/m3. The optimised macroscopic parameters for various densities were calculated using the inverse method employing the well- known Johnson Champoux-Allard (JCA) model for porous material and has been shown to give good agreement between the predicted and measured absorption coefficient. Durian husk fibers can therefore be the alternative natural sound absorber.
Erni Setyowati et al., 2018, have carried out research on the Sound Absorption Improvement of Water Hyacinth and Coconut Husk based Fiber Reinforced Polymer Panel. This paper emphasizes the sound absorption improvement of the water hyacinth and coconut husk-based fiber reinforced polymer (FRP) panel. The dry water hyacinth and coconut husk were milled and sieved then mixed with polyester and methyl ethyl ketone peroxide as the catalyst. The composition is 200 ml, 25 grams, and 20 ml for the polyester, fiber, and catalyst respectively and casted using a square tray to form a flat FRP panel through open air drying without any compaction. Three different approaches
i.e. multiple quarter wavelength resonators, air cavity, and front fibrous layer inclusion are implemented to the FRP to improve its sound absorption performance. The entire measurements conducted by using transfer function-based impedance tube technique refer to ASTM E-1050-98 standard. B&K 4206. It is found that the proposed approaches increase sound absorption coefficient of the bulk FRP significantly. The best performance occurred on the coconut husk based FRP when the 8 quarter wavelength resonators combined with the fibrous layer. Sound absorption increased accordingly to above 0.7 starting from
1.5 kHz. On the other side, the air cavity shows similar influence on the entire test sample due to Helmholtz
resonance mechanism. The cavity backed natural fiber reinforced polymer panel (NFRP) composite made of water hyacinth, and coconut husk has the valuable possibility for replacing the synthetic fiber composite mainly for building noise control applications.
C.F. Da Silva et al., 2017, have carried out the work on Improvement of indoor air quality by MDF (Medium Density Fibreboard) panels containing walnut shell. The study shows the porous microstructure of the MDF, and walnut shell and their chemical composition were analysed using SEM, XRD and FTIR. Compared to a control panel, walnut shell additions showed an improved ability to remove VOCs and formaldehyde from the indoor air and buffer humidity. MDF panels were made to a density of 760 kg/m3, with area dimensions of 0.4 * 0.4 m2 and a thickness of 12 mm. A commercial mix of spruce, pine and fir chips was refined at 8 bars at the Bio Composites Centre. The fibre, scavenger and resin were individually weighed and combined in a drum blender. The resonated fibre was weighed out again and formed into a mat which was subsequently pre-pressed by hand before finally being pressed between two heated platens at 200°C for 5 min following the Bio Composites Centre's standard press profile (controlled by the Pressman control program). The scavenger loading for the panels was 5, 10 and 15% fibre weight, The incorporation of walnut within the MDF panels showed excellent promise for the future of MDF as a building material. This is particularly important as MDF could be identified as a problematic material due to its high formaldehyde emissions and negative impacts on the health and wellbeing of humans exposed. Adoption of walnut shell as an additive in fibre-based building materials will not only improve indoor air quality, but also provide an alternative to landfill or incineration of the shell, with an associated reduction in embodied CO2.
Azma Putra et al., 2022, have carried out research on Utilizing Sugarcane Wasted Fibers as a sustainable Acoustic absorber. Sugarcane consists of tiny and soft fibers which can potentially be a good sound absorber it is coupled with another strong material to increase strength. The diameter of fibers ranges from 11-23 m. In the pre- treatment stage, raw material was cut into 1 to 3 mm length then sundried for 1 week and heated in the oven at 800°C for 5 minutes to let the excess water evaporate. Later, raw material was cut into 5 to 10 mm lengths. In the preparation stage, the raw material was mixed with different composition of binder. the binders used are polyurethane and polyester mixture was then hot-pressed in a mould to obtain a round shape. The measurement of sound absorption coefficient was performed in an impedance tube by applying two microphone transfer function methods according to ISO 10534-2:2001. The effect of binder composition and fiber density are discussed with the former affects only for the 3 grams fibers and the latter to give better absorption coefficient. It is found that acoustical performance of the sugarcane absorber with thickness of ½ inch is comparable with that of commercial sound insulator
with average absorption coefficient of 0.65 at frequency 1.2
– 4.5 kHz.
Ebrahim Taban et al., 2021 This paper aimed to evaluate the sound-absorbing characteristics of date palm fibers using normal- and random-incidence methods. Samples were produced at four thicknesses (25, 35, 45, and 55 mm) and two bulk densities (125 and 175 kg/m3). This work describes the fabricate absorbing panels from date palm waste fibers and assess their performance for sound absorbing applications. The normal-incidence sound absorption coefficient was measured using the impedance tube. The findings show that the samples with a thickness of 55 mm and a density of 175 kg/m3 have the highest sound absorbing performance. The acoustic behavior of this new material was investigated in a reverberation room method. It was found that the sample enjoys high absorption at middle- and high-frequency ranges. It was also found that by the installation of the acoustic panels, RT significantly decreases, especially at low- and mid- frequency bands. Afterward, the performance of the acoustic panels was investigated using Odeon software. To this end, the acoustic characteristics of an empty rectangular conference hall were investigated. Afterward, 20, 30, and 50% of the hall walls were virtually covered with the acoustic panels in the software, and the acoustic parameters of the hall, including RT, EDT, STI, D50, and C80, were calculated. The results show that the acoustic performance of the hall considerably enhanced after installing the acoustic panels. It was found that with the addition of acoustic panels on the hall walls, the values of RT and EDT decrease, and the vales of D50 and C80 increase.
Seyed Ehsan Samaei et al., 2021, have carried out the work on Natural fibro-granular composite as a novel sustainable sound-absorbing material this study shows An innovative natural fibro-granular composite made of kenaf fibers and waste rice husk granules is developed. A quadratic model was established to identify the effects of independent variables, including the thickness (2060 mm), density (100300 kg/m3), binder content (1030 %w/w), and fiber to granule ratio (0.333) on the sound absorption average. The RSM-CCD model provided the combination for the optimized composite, i.e. thickness of 50 mm,density of 200 kg/m3, binder content of 15 %w/w, and fiber to granule ratio of 2.33. Results show that at all frequencies, the optimized fibro-granular sample provides higher sound absorption compared with samples made of 100% kenaf or 100% rice husk. From the environmental and economic perspectives, this work focused on studying the acoustic behavior of sustainable engineered fibro-granular composites made from natural kenaf fibers and waste rice husk, sourced locally.
Eyub Canli et al., 2022 carried out work on Determination of Sound Absorption Coefficient and Transmission Loss Properties of Almond Shell Particle Boards. The study shows the particle boards from almond shell particles are investigated in terms of sound absorption and transmission
properties. For board construction Almond shells were processed, and they became particles with diameters having different values between 0.4mm and 3.4 mm. Sieves were used to obtain an almond shell particle size distribution. Dark pine chip size changed between 0.2-0.6 mm. In order to conduct acoustic tests, two test tubes were used. One tube with 100 mm test diameter, acoustic tests with frequency interval of 50 to 1500 Hz were conducted. Another test tube has 30 mm diameter, and it has a frequency interval of 500 to 6000 Hz. In the paperwork, feasibility and properness of almond shell particle boards having almond shell particles and dark pine chips as the main constituents for sound insulation purposes. they have an effect of sound insulation and this effect can be considered in structural purposes.
Dario Alfonso Paez Soto et al., 2020, carried out a work on Evaluation of an acoustic conditioning panel made from typical Colombian fibres the study shows a perforated panel from guadua fibres is implemented after acoustic characterization of the fibres. for the obtention of the guadua fiber they used alkaline method the solution is prepared with a 10%concentration which corresponds to 100 grams of sodium hydroxide (NaOH) per liter of water A perforated panel was designed with an objective frequency of 500 Hz, thus energy attenuation is at low frequencies. The guadua sheet that was used for the construction of the acoustic panel has a thickness 0.5cm, and a surface of 1m x 1.2m. For the construction of the perforated panel, 10 tables of guadua were used, which were pressed to obtain a final laminate of 1.2 m length by 1 m width, with a thickness oscillating between 0.3 cm and
0.6 cm, obtaining an average thickness of 0.5 cm. from this panels the results show that the guadua panel is a potential product for the acoustic conditioning market. Its massive implementation would contribute to the principles of Sustainable Development.
Eugenia Mariana Tudor et al., 2020 have carried out the work on sound-Absorption Coefficient of bark-based Insulation Panels. In this paper The spruce and larch bark were collected. The bark planks were ground by means of a 4-shaft shredder with a mesh of 30 mm. Subsequently, the bark particles were dried at 60 °C and 200 to 250 mbar in a vacuum kiln dryer Brunner-Hildebrand High VAC-S, HV- S1 from 65% to 9.0% moisture content. The material was repeatedly screened according to EN 15149-1:2011 with a sieve shaker, to obtain particles in a size spectrum of 8-13 mm and 10-30 mm. Four types of bark-based insulation boards were manufactured. The spruce bark was bonded with 10% urea formaldehyde type Prefer 10F102. The larck bark from Graggaber sawmill, was glued with 10% tannin- based adhesive. The formulation included Mimosa tannin extract powder from Phenotan, Tanac, Brasil, hexamethylenetetramine and sodium hydroxide solution. A total of 50% tannin extract powder and 50% water were stirred with a mechanical mixer at 700 and 1500 rpm. A total of 10% of hexamine was added and sodium hydroxide was used to adjust the pH value to 9. The boards were pressed at 180 C for five minutes with a press factor of 24
s/mm. 100 mm diameter samples were cut from bark-based insulation boards manufactured in the laboratories. The thermal conductivity, mechanical properties, microstructures, and volatile organic compounds emissions of these panels were analyzed in publications by Kain et al. The average moisture content of the samples was 89%, according to EN 322:2005 Acoustical Measurements in Impedance Tube. The acoustical properties of bark-based insulation panels were measured with an impedance tube system. This covers a frequency range from 50 to 5000 H.
-
NOISE BARRIERS USING CEMENT AND EPS BEADS
Lutfullah Gunduz et al.,2018 have carried out research on cement bonded particle board. In this paper, sound transmission loss performance of Cement Bonded Particle Board panels for noise barrier applications will be discusses in different construction models. In this research, the general form of the composite sound barrier panel is a sandwich panel type, there is one board at the front and one at the back and in between there is an insulation layer. Thickness of the cement bonded particle boards and insulation layer were chosen according to model design. According to the findings, NRC value of flat surface Cement-Bonded Particle Boards is defines as 0.025 with 10 mm board thickness. For 12 mm board thickness, NRC values was determined as 0.030 and 0.035 for 18 mm board thickness. On the other hand, NRC value of surface textured Cement-Bonded Particle Boards is defines as
0.035 with 10 mm board thickness. For 12 mm board thickness, NRC values was determined as 0.040 and 0.045 for 14 mm board thickness. Due to the wood chip within the structure of the boards, it was observed that the NRC value of the material was slightly higher than the other fiber cement boards. In the model 1, the weighted sound reduction index Rw value for the cement-bonded particle board composite sound barrier panel designed with a thickness of 50 mm is 48 dB, while in the Model 2 version the Rw value with the equivalent insulation layer thickness is obtained as 51 dB with 3 dB increment. According to the research results, cement-bonded particle boards with a composite form is an effective application in terms of acoustic outdoor noise barriers.
Joel John et al., 2018 have carried out research on Acoustic insulation with cement mortar by adding natural coir-fibre. In this paper Natural fibres as reinforcing agent in cement matrix are nowadays being considered as effective to steel and other inorganic synthetic fibre. Here natural fibre such as sisal, coconut, sugar-cane bagasse, hemp, jute is reported to improve sound insulation properties in composites. This paper investigates the feasibility of cement mortar in plastering as sound insulation material by adding natural fibre. The materials used in this research work are ordinary Portland cement of 53 grade conforming to IS : 8112- 1982,grading zone-II was used as fine aggregate. Specimen of size 7.05×7.05×7.05cm were casted as per IS code 12269 (OPC 53). But while adding fibre the cement, fine aggregate and fibre are mixed for one minute to attain homogenous mixture. After the mix, water is added and simultaneously mixing is done for 2 min. Mechanical
vibration is done for 1min and demould after 24hrs. By performing impendence tube method, compressive strength test, porosity determination it results in Increase in fibre volume leads to increase in sound absorption coefficient. Porosity also increases as fibre volume increase in specien. The 3% fibre added in specimen had higher value of sound absorption coefficient. More fibre added higher will be the porosity the 3% fibre added form more interconnected fibre network
Michal Boltryk et al., 2020, have carried out research on cement composites with wood waste-Design, Features and proposal of application. In this research a method for determining an approximate composition of cement composites with an organic wood waste is proposed. For the tests, the following were used-portland cement: 32.5 MPa ; organic wood waste with the following content of three fractions: 0 to 2 mSm conifer sawdust of 45%, 2 to 10
mm shavings of 45%, and 10 to 20 mm shavings of 10%; water; and aluminum sulfate and hydrated lime as mineralizing agents, wood waste was mixed with Al2(SO4)3 for 3 minutes to a homogeneous saturation. After waiting 15 minutes, Ca(OH)2 was added to neutralize the solution of the aluminum sulfate and mixed for the next 3 minutes. After waiting another 15 minutes, cement was added and all components were mixed again for 3 minutes to obtain a homogeneous mass. The use of chemicals in relation to the weight of wood waste reduces the absorption by 30%, increases compressive strength of the composite by approximately 70%, and protects the wood waste against rotting processes. Next, the cement composite mixture was cast into 10 x 10 x 10 cm molds and compacted manually and were demolded after 1 day, then cured in air-dry conditions and at a temperature of 20 ± 2°C for 28 days. This process allowed for regular drying. By various tests and calculation, it is found that the production of blocks based on shavings and sawdust will ensure the use of waste, especially from the local wood industry, and will develop the building materials market with a new, commercially viable and environmentally friendly construction product for low-rise buildings.
Abdulkadir Kan et al., 2007, have carried out the work on effect of cement and EPS beads ratios on compressive strength and density of lightweight concrete. EPS concrete is a kind of lightweight concrete.Portland cement (PC) was Type II according to the ASTM C 150 and Turkish standards CEM II-B/32.5R,commercially available spherical EPS beads of size between 3.0-8.0 mm. The bulk density was 10-20 kg/m3. A poly-carboxilate based super plasticizer was used.The chemical composition and physical properties of the materials used PC/EPS ratios, 1/0, 1:4, 1:2, 3:4 and 1:1 mix proportion by volume were prepared. EPS beads content for the mixtures were kept constant at 0.05 m3. The interfacial zone between cement paste and aggregate plays a critical role in determining mechanical properties of concrete. For this reason, EPS beads were wetted initially.The pre-wetting of lightweight aggregate will critically affect the strength and slump of its concrete. The concrete mixes were prepared in a laboratory
counter current mixer for a total of 5 min. The fresh concrete densities and slump values were measured immediately then it is poured into moulds and compacted by hand. For each mixture, three samples of 50×50×50 mm3 prisms were prepared and the specimens were cured and were oven dried at the age of 28 days at 60±5°C and weighed at 24 h intervals until the loss in weight did not exceed 1% in a 24 h according to ASTM C 33212. Saturated surface dry cubes were kept in a hot air oven at 60°C until a constant weight was attained, because at the temperature of 110±10°C, the EPS beads initially shrank and finally evaporated. At 28 days, samples were tested for compressive strength in a testing machine of 2000 kN capacity at a loading rate of 2.5 kN/s. Each test was repeated three times and the test results were averaged Density of EPS concrete has significantly influenced by the PC/EPS ratio. The 28-day compressive strength and the dry concrete density varied from 0.11 to 38.50 MPa and from 464 to 1940 kg/m3 respectively.
D. Bouvard et al.,2007, have carried out research on Characterization and simulation of microstructure and properties of EPS lightweight concrete. In this paper characterize thermal and mechanical properties of EPS concrete and to investigate the possibility of predicting these properties through modeling approaches. The materials investigated in this paper are EPS concretes. The spheres are mixed directly with the matrix during the fabrication process. Different materials have been fabricated by changing the mass fraction and the size distribution of the spheres. Two size distributions of spheres have been used. A close distribution with spheres with a diameter between 0.75 and 1.1 mm and a two-size distribution with 30 vol.% of spheres with a diameter between 0.75 and 1.1 mm and 70 vol.% with a diameter between 1.5 and 2.6 mm. This second structure is supposed to result in denser sphere packing density and thus in lower concrete density. By introducing porosity in the blend, eight concretes with various mass densities between 432 and 961 kg/m3 have been obtained, which correspond to cement volume fractions between 0.204 and 0.415. Specimens of dimension 4 × 4 × 16 cm3 have been fabricated for thermal characterization and cubes of 4 cm edge have been fabricated for mechanical testing and microstructural observation following EN 12390-2 European Norm standard. Their microstructure has been analysed in 3D by X-ray tomography and their thermal and mechanical properties have been measured. The thermal behaviour has next been modelled with a classical scheme of homogenization for two phase materials, which appeared to be sufficient. Finally, from the comparison between experimental data and model prediction, the interest of modelling for optimising EPS concrete composition is discussed.
Haghi A.k et al., 2006, have carried out research on Application of expanded polystyrene (eps) beads and polyamide-66 in civil engineering, part one: lightweight polymeric concrete. The present work is a general attempt to study the effect of polyamide-66 and EPS sizes on the
adhesion of beads with concrete. The EPS beads were wetted initially with 25% of the mixing water and super plasticizer before adding the remaining materials. A naphthalene-based super plasticized cement paste was prepared. The addition of EPS in place of normal aggregate reduces the weight of the concrete. In order to simplify the mixing process, the estimated component additions were measured by volume. Non-absorbent, hydrophobic and closed cellular aggregates like EPS beads were mixed in a planetary mixer. Mixing continued until a uniform and flowing mixture was obtained. The fresh polymer concrete was then poured into molds and compacted by hand firmly. A number of test specimens of different sizes were chosen.In this experimental study, the mixture compacted in moulds of 100 mm x 100 mm x 100 mm and cubes of
100 mm for studying the compressive strength. The samples remained in the moulds for 3 days; they were then taken out and immersed in water and allowed to harden for 3, 7 and 28 days in the laboratory environment. As a final result, it was shown that the fine EPS beads allow for the highest composite compressive strength, which on average is some 45% higher than with the largest beads used. Meanwhile, the application of polyamide-66 yarns had a significant influence on crack reduction.
-
GAP IDENTIFICATION
As per the literature of above papers, most of the literature that are referred are carried out with fibres, husk, shells, wooden bark, cement and EPS beads. Material from Delonix Regia which is non edible in nature, may be helpful in controlling the noise. In this scenario, an attempt may be made to use the Delonix Regia in noise control material with cement/ other adhesive material.
-
CONCLUSION
Use of conventional materials as noise barrier has significant effect on the environment, while the use of waste materials in fabricating the panels have found to be a good way of managing the waste and also it can be cost effective compared to the conventional noise barriers and also using the natural materals in the panel is a sustainable way. Composite panels of cement have benefits of conventional one and natural one as it has been added with some natural materials it can also be sustainable approach by reducing the carbon emission.
REFERENCES
[1] Botryk, M., Anna, K. and Pawluczuk, E., 2020. Cement composites with wood wastedesign, features, and proposal of application. Aci Materials, 117. [2] Bouvard, D., Chaix, J.M., Dendievel, R., Fazekas, A., Létang, J.M., Peix, G. and Quenard, D., 2007. Characterization and simulation of microstructure and properties of EPS lightweight concrete. Cement and concrete research, 37(12), pp.1666-1673. [3] Canli, E., Sarikaya, A., Sertkaya, A.A. and Güler, C.,2022 Determination of Sound Absorption Coefficient and Transmission Loss Properties of Almond Shell Particle Boards. Internatinonal Conference on Materials Science, Mechanical and Automotive Engineerings and Technology.pp.7-12 [4] Da Silva, C.F., Stefanowski, B., Maskell, D., Ormondroyd, G.A., Ansell, M.P., Dengel, A.C. and Ball, R.J., 2017. Improvement ofindoor air quality by MDF panels containing walnut shells. Building and Environment, 123, pp.427-436.
[5] Gunduz, l., Kalkan, s.o. and Isker, a.m., 2018. Effects of using cement-bonded particle boards with a composite component in terms of acoustic performance in outdoor noise barriers. The eurasia proceedings of science technology engineering and mathematics, (4), pp.246- 255. [6] A.K., Arabani, M. and Ahmadi, H., 2006. Applications of expanded polystyrene (EPS) beads and polyamide-66 in civil engineering, Part One: Lightweight polymeric concrete. Composite Interfaces, 13(4-6), pp.441-450. [7] Ismail, F.Z., Rahmat, M.N. and Ishak, N.M., 2014. Sustainable Absorption Panels from Agricultural Wastes. In MATEC Web of Conferences (Vol. 15, 01035). EDP Sciences [8] John, J. and Antony, J., 2018, Acoustic insulation with cement mortar by adding natural coir-fibre, Proceedings of Second National Conference on Structural Engineering and Construction Management, SECON 2018, pp. 97-102. [9] Kan, A. and Demirboa, R., 2007. Effect of cement and EPS beads ratios on compressive strength and density of lightweight concrete. [10] Kesten, S., Umut, Ö. and Ayva, B., 2020, March. Acoustic and structural design of a highway noise barrier. In IOP Conference Series: Materials Science and Engineering (Vol. 800, No. 1, p. 012029). IOP Publishing. [11] Mehrzad, S., Taban, E., Soltani, P., Samaei, S.E. and Khavanin, A., 2022. Sugarcane bagasse waste fibers as novel thermal insulation and sound-absorbing materials for application in sustainable buildings. Building and Environment, 211, p.108753. [12] Páez Soto, DarÃo Alfonso, Luis Jorge Herrera Fernández, Oscar Esneider Acosta Agudelo, and Marcelo Herrera MartÃnez. "Evaluation of an acoustic conditioning panel made from typical Colombian fibres." Revista Facultad de IngenierÃa Universidad de Antioquia 94 (2020): 102-116. [13] Putra, A., Othman, M.N., Oliveira, T., Souli, M.H., Kassim, D.H. and Herawan, S., 2022. Waste Durian Husk Fibers as Natural Sound Absorber: Performance and Acoustic Characterization. Buildings, 12(8), pp.1112. [14] Setyowati, E., Yahya, I., Supriyo, E., Romadhona, I.C. and Minardi, A., 2018. On the sound absorption improvement of water hyacinth and coconut husk based fiber reinforced polymer panel. In MATEC Web of Conferences (Vol. 159, p. 01004). EDP Sciences. [15] Taban, E., Amininasab, S., Soltani, P., Berardi, U., Abdi, D.D. and Samaei, S.E., 2021. Use of date palm waste fibers as sound absorption material. Journal of Building Engineering, 41, p.102752. [16] Tudor, E.M., Dettendorfer, A., Kain, G., Barbu, M.C., Réh, R. and Kriák, ., 2020. Sound-absorption coefficient of bark-based Insulation panels. Polymers, 12(5), p.1012. [17] Yun, B.Y., Cho, H.M., Kim, Y.U., Lee, S.C., Berardi, U. and Kim, S., 2020. Circular reutilization of coffee waste for sound absorbing panels: A perspective on material research, 184, pp.109281.