
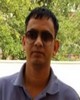
- Open Access
- Authors : Dr. Abdullah Ahmed Laskar , Anupam Sarkar , Sagar Mondal
- Paper ID : IJERTV9IS110141
- Volume & Issue : Volume 09, Issue 11 (November 2020)
- Published (First Online): 24-11-2020
- ISSN (Online) : 2278-0181
- Publisher Name : IJERT
- License:
This work is licensed under a Creative Commons Attribution 4.0 International License
Technique for Prevention of Surface Problem in
Construction of RCC Chimney Shell by using of
Galvanised Cold Rolled Color Coated Plain Sheet
Dr. Abdullah Ahmed Laskar
Sr Manager,
Bharat Heavy Electricals Ltd, Power Sector Eastern Region,
Kolkata-91, WB, India.
Anupam Sarkar
Dy Engineer,
Bharat Heavy Electricals Ltd,
Power Sector Eastern Region,
Kolkata-91, WB, India.
Abstract— RCC chimney is one of the essential and important structure in Thermal power plant & the RCC shell of chimney is usually constructed by using slip form technique. But during construction of chimney shell by using slip form technique, surface damage of RCC chimney shell is one of most common problem in every chimney during construction. Such surface problem issue indicate doubt on concrete quality & workmanship, which leads to investigation of in situ concrete quality and repairing of the damage concrete. In addition to that because of such surface problem with slip form concrete finally durability of concrete get compromised of such important chimney structure. Thus such surface issues leads to uncertain period of time for investigation with subsequent repairing at site, and in some cases it was also experienced that part of the chimney shell required to dismantle due to bad remarks in investigation report. Hence the surface issue of RCC chimney shell will impact on many issues related to construction of chimney like unexpected delay on overall completion of chimney, unexpected cost for investigation and repairing & finally compromising with the quality of concrete and integrity of the chimney structure. So considering the negative impact of such surface issue an experiment was conducted with 0.47 mm thick plain color coated cold rolled steel plate as an intermediate protective membrane between concrete & slip form steel shutter plate. Based on the outcome of the experiment it has been observed that concrete surface of shell with 0.47 mm thick plain color coated sheet found smooth & no damage occurred while slipping of forms, however the surface of concrete get damaged partially or completely in the locations where there was no sheet was used along with slip form shutter plate. Hence by adopting the technique of using
0.47 mm thick color coated cold rolled sheet along with slip form steel shutter plate it is possible to eliminate such surface damage problem of chimney shell concrete & subsequently it is possible to construct a defect free RCC chimney within a specified time schedule and also it helps to eliminate unexpected cost of investigation & repairing works.
Keywords—Chimney; RCC-shell; Lifting crack; Delamination; Concrete collapse, Lump formation.
I. INTRODUCTION
The construction of RCC chimney shell by using slip form technique is one of the most critical construction activity in the field of civil Engineering, due to usual surface
Sagar Mondal
Dy Engineer,
Bharat Heavy Electricals Ltd,
Power Sector Eastern Region,
Kolkata-91, WB, India.
problem in RCC shell during construction stage. The surface problem is a very common phenomenon in construction of RCC chimney shell by using slip form technique due to many reasons like improper construction management, poor quality of concrete, defective geometry of slip form system installed and the quality of the slip form plate. However maintaining all the parameter in line with requirement of slip form system during execution stage may not be possible, which in turn surface problem is a very common phenomenon & the extent of such damage is varying from minor to major damage like loss of entire cover concrete. Considering the severity of the surface issue in one of the twin flue RCC chimney shell of 275 m high, an experimental study was conducted with application of 0.47 mm thick galvanized cold rolled color coated sheet along with normal mild steel plate and the results of the application was found commendable. Based on the available literature about the guidelines for construction of RCC chimney shell by using Slip form technique, there is a lack of suitable guide lines for preventive measures of surface problem in RCC chimney shell during construction stage. But there are very few available guide lines, which are mostly for improving the slip form system correction, like fast pouring of concrete, even layer of concrete pouring and controlled setting time of concrete by many expert of the same field. But the suggested guidelines has some limitation during execution stage, like fast pouring of concrete are linked with many factors like labor component, machinery performance & number of lifting equipment like winch etc. Similarly controlling of setting time of concrete uniformly at all the time is again difficult, as the setting of concrete are again depending on many factors like ambient temperature, Relative humidity, w/c ratio, type of cement, type of water reducing admixture. Because of such limitation of available guidelines by many expert, an experimental study was conducted by using of 0.47 mm thick plain color coated cold rolled steel plate as an intermediate protective layer between slip form steel shutter plate & concrete surface & the results shows an extensive improvement towards elimination of surface problem in RCC-chimney shell construction by using slip form technique.
IJERTV9IS110141 www.ijert.org
Published by : International Journal of Engineering Research & Technology (IJERT)
http://www.ijert.org ISSN: 2278-0181
Vol. 9 Issue 11, November-2020
II.
LITERATURE REVIEW There are reasons which can cause surface problem in RCC chimney shell during construction by slip form technique. Some of the common surface defect in slip form concrete & its causes are as explained here. The construction of RCC chimney is usually done by slip form technique & occurrence of such surface issue in RCC shell is a very common phenomenon during construction of shell. The impact such surface problem in RCC shell is simply create doubt on quality and integrity of the structure. In addition to that because of such doubtful quality of in-situ concrete, it required thorough investigation of in-situ concrete quality & subsequent repairing or dismantling of defective part of chimney shell require sufficient time. Some of the common defect or problem in slip form concrete & the probable causes for the same are explained here.
A.
Lifting cracks
The lifting crack is usually occurred in chimney shell during slipping because of following reasons.
a)
Long interval between two successive layers of concrete.
b)
Restart of concrete over an old concrete surface after long gap of more than 3 days.
c)
Delay in lifting of slip form or long gap between two successive lift usually schedule lifting is in every 1520 minute. So in any case if it exceed more than 30 minutes & concrete get set then such problem is very common.
d) Pouring layer thickness is less than 200 mm over an old concrete surface.
Fig-1: Lifting crack in RCC chimney shell construction by Slip form
technique.
B. Delamination
The delamination is nothing but damage of cover concrete during slipping of slip form. The following are the reasons for occurrence of delamination during slipping of form.
a)
Geometrical changes like negative radius in any particular location.
b)
The level of slip form is not in a level plan mostly LVL in yoke legs get disturbed.
c)
Due to non-cleaning of slip form steel shutter plate continuously cement slurry is getting hydrated with already stick cement mortar splat & thus increasing its volume. So during lifting of slip form this stick mass
with shutter plate will damage the upper soft semi
Fig-2: Delamination problem in RCC chimney shell construction by Slip form technique.
C.Concrete collapse
The concrete collapse is usually occurred during slipping of form because of the following reasons.
a)
Lifting of slip form when concrete is not getting set.
b)
Rate of lifting is very high as comparison to the setting time of concrete i.e. lifting over non set concrete.
c)
Un-even layer pouring i.e. in some location height of of pouring is 300-400 mm while in some locations layer thickness is 150-200 mm.
Fig-3: Concrete collapse problem in RCC chimney shell construction by Slip form technique.
D. Lump formation
The lump formation is usually occurred in slip form concrete because of the following reasons
a)
High ambient temperature.
b)
Low w/c ratio in the mix i.e. less than 0.40.
c)
Using of OPC 53-grade cement as per IS-12269 or CEM-I 52.5 class cement as per BSEN-197-1more than 400 kg/cum in the mix having fineness of cement is more than 370 m2/kg.
d)
The Relative humidity of ambient air less than 60% with high ambient temperature.
e)
Very high wind speed with very high rate of evaporation loss of surface water.
f)
Low setting time of concrete i.e. less than 5 hrs
IJERTV9IS110141 www.ijert.org
Published by : International Journal of Engineering Research & Technology (IJERT)
http://www.ijert.org ISSN: 2278-0181
Vol. 9 Issue 11, November-2020
Fig-4: Lump formation problem in RCC chimney shell construction by Slip form technique.
Considering all the above cause of surface damage during slipping of form, the primary cause is very high static friction between semi solid concrete surface & slip form shutter plate because of roughness of shutter plate. Hence it is felt that if we placed a smooth surfaced material will placed between concrete & steel plate then such high static friction can be minimized & subsequently we can eliminate most of the causes which can cause surface damage during slipping of form.
III. EXPERIMENTAL METHOD
The experiment was conducted with 0.47 mm thick galvanized cold rolled color coated plain sheet application along normal MS plate used as a slip form shutter plate. The fixing arrangement of the sheet shall be done in such a way so that the sheet can be slide along with steel shutter plate during diameter adjustment of shell. The fixing arrangement of sheet is shown in Fig-8, Fig-9, and Fig-10.
IJERTV9IS110141 www.ijert.org
Published by : International Journal of Engineering Research & Technology (IJERT)
http://www.ijert.org ISSN: 2278-0181
Vol. 9 Issue 11, November-2020
Fig-10: Fixing of sheet along with both inner & outer shutter plate considering the provision for making horizontal sliding.
III. RESULTS AND DISCUSSIONS
There is always a possibilities of adhesion of cement mortar slurry along with normal mild steel plate of slip form shutter during concreting of RCC shell & it results smoothness of plate will lost. As the smoothness of the got reduced subsequently the friction between concrete surface & steel plate get increased & such increased friction resulting damage of surface or cover concrete while slipping. In addition to that surface attached cement mortar will gradually increasing its size by volume due to continuous hydration with newly poured concrete & thus formed lump of concrete along with shutter plate. When shutter plate will start slipping vertically it will break the upper layer of soft concrete & resulting delamination of cover concrete. On the pretext of using 0.47 mm thick cold rolled color coated galvanized sheet, it act as a smooth protective surface between steel plate & concrete surface which helps to reduce frictional force between steel plate & concrete surface and also it prevent adhesion of cement mortar to steel plate & thus helps to prevent lump formation & delamination problem.
Fig-11: Concrete surface with (Left) or without (Left) using of 0.47 mm thick galvanized cold rolled color coated sheet in inner surface of shell concrete.
Fig-12: Concrete surface with (Left) or without (Left) using of 0.47 mm thick galvanized cold rolled color coated sheet in outer surface of shell concrete.
Fig-13: Concrete surface of RCC Chimney shell by using of 0.47 mm thick color coated galvanized sheet along with steel shutter plate for Upper part of chimney shell or without using of sheet Bottom part of shell.
IV. CONCLUSION
The following are conclusion of the experimental results for application of 0.47 mm thick galvanized color coated cold rolled plain sheet.
1.
It prevent the common surface problem of slip form technique used for construction of RCC chimney shell like lifting crack, delamination of cover concrete, concrete lump formation & concrete collapse phenomenon.
2.
It helps to reduce the initial static friction during start of slipping & resulting prevention of lifting crack.
3.
It helps to eliminate the extra surface finishing requirement of shell and thus reduce the cost of finishing materials & manpower required for finishing.
4.
It helps to produce sound cover concrete & thus it improves the durability of the structure, as weaken cover concrete is always vulnerable for initiation of corrosion of embedded reinforcing steel.
5.
It helps to minimize the unexpected investigation and repairing of cost of in-situ concrete in case of any defect observed in RCC-shell concrete surface during construction stage.
6.
It helps to prevent any delay in construction time cycle due to unexpected surface problem during construction stage.
7.
It helps to produce good surface appearance as compared to concrete surface without using such sheet as per Fig-13.
IJERTV9IS110141 www.ijert.org
Published by : International Journal of Engineering Research & Technology (IJERT)
http://www.ijert.org ISSN: 2278-0181
Vol. 9 Issue 11, November-2020
REFERENCES
[1] ACI-307-08, Code Requirements for Reinforced concrete Chimneys and Commentary.[2] Dr.ing Slip forming of Vertical Concrete Structures‖ Department of Structural Engineering The Norwegian University of Science and Technology N-7491 Trondheim,Norway, 200.
[3] Bob Riser, 1995, Advances in vertical Slip form construction‖ Concrete Construction, October..
[4] Thomas W. Taylor PE Slip formed core construction Datum Engineering , Inc. Dallas /Austin.
[5] Sanjay Chandra (1997) Slip form technique A production study P G Dissertation, Madhav Institue of Technology and Science, Gawlior, India.
[6] Fossa K T , Aker Kvaerner Oslo Slip forming of advanced concrete structures by Norway‖ A. Kremer Gleitbau Salzburg Austria Jan Moksnes Consulting ,Stavanger Norway.
[7] Tarek Zayed, M Reza Sharifi, Sandel Baciu, Mohammed Amer, Slip form Application to concrete Structure‖ Moksnes, J.&Jakobsen,B.1985. High Strength Concrete Development and Potentials for Platform Design. OTC Houston. Paper OTC 5073.
IJERTV9IS110141 www.ijert.org