
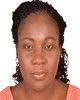
- Open Access
- Authors : Eneasato C. F , Egwuagu O. M , Onah T. O
- Paper ID : IJERTV11IS060222
- Volume & Issue : Volume 11, Issue 06 (June 2022)
- Published (First Online): 27-06-2022
- ISSN (Online) : 2278-0181
- Publisher Name : IJERT
- License:
This work is licensed under a Creative Commons Attribution 4.0 International License
Techno-Economic Investment Analysis of Biodiesel Production using Waste Vegetable Oil
1Eneasato C. F., 2Egwuagu O. M., *3Onah T. O.
1 Department of Mechanical Engineering Federal Polytechnic Oko, Oko Anambra State
2* 3 Department of Mechanical and production Engineering, Enugu State University of Science and Technology, Agbani, Enugu State
Abstract:- The techno-economic analysis of biodiesel production using waste vegetable oil, was studied. From which these processes were carried out; processing of waste vegetable oils into biodiesel through transesterification. Thereafter, determination of the characteristics of the biodiesel processed was compared to biodiesel standards. This was followed by its ecological effects and comparative analysis as well as performance evaluation of diesel engine properties on the test-bed when compared to the biodiesel. In addition, it was compared with conventional diesel. The brake power stretched the maximum value for speed ranging from 1800rpm to 2400rpm, which displayed that the engine operates more efficiently within the above speed range. Besides, the brake power declined with produced biodiesel for the same load. Consequently, the brake thermal efficiency terminated but invariably the specific fuel consumption (SFC) increased. It was revealed that biodiesel proved to be more efficient than conventional diesel fuel in this range. For conventional diesel fuel, the efficiency under wired to drop when the speed decreased below 2000 rpm. Subsequent upon this, gives better combustion of biodiesel because of its higher cetane number. This efficiency can then be said to be relative to combustion efficiency. The fuel consumption of biodiesel was also relatively higher than that of conventional diesel fuel. This is a suggestive that biodiesel has higher specific gravity and viscosity and thus lower volume flow rate than Petro-diesel. Last of all, the techno economic cost investment analysis gives 21.7% financial savings compared to petrol-diesel.
Keywords: Economics, biodiesel, investment, production, waste vegetable
INTRODUCTION
The American Society for Testing and Materials (ASTM) defined biodiesel as mono alkyl ester of long chain fatty acids derived from a renewable lipid feedstock, such as vegetable oil or animal fat. It is renewable, biodegradable and oxygenated. Though, it is monoalkylesters of long chain fatty acids derived from vegetable oils or animal fats for use in compression ignition engines. Thus, it is produced by reacting vegetable oils or animal fats with an alcohol in the presence of a catalyst to form the corresponding ester in a process known as transesterification [1]. This process produces a fuel with properties close to those of conventional diesel.
Commercial production of biodiesel began in the late 1990s when the US National Biodiesel Board (NBB) reported production of 500,000 gallons (32.6 barrels per day) in 2000. This US biodiesel industry reached a milestone by producing 1 billion gallons of this fuel in 2011 alone; supporting 39,027 jobs across the country and more than $2.1 billion in household income. According to the latest Environmental Protection Agency (EPA) statistics type of asphalt concrete plant 2012. More importantly, some recent estimates (92011) off world-wide proven petroleum reserves of
1.35 trillion barrels with 80 million barrel as daily production rate predict them to last for the next 40 years (heat transfer analysis of bitumen 2010.
The use of substitute fuel started since the first oil crisis in 1970s, various alternative fuels have been investigated as potential supplements to conventional petroleum based supplies. The interest then was fuel supply and security. Currently, attention has shifted to the use of renewable fuels in order to reduce environmental effects of fossil fuels combustion [2]. One type of fuel that is well suited for diesel engines is that based on vegetable oils. Tests with vegetable oil based fuels in diesel engines indicate that their performance is comparable to that of diesel fuel, and they are presently rated among the energy fuels considered as the most promising substitute for the highly priced and diminishing fossil fuels [3]. Modern diesel engines have direct injection fuel systems that are more sensitive to fuel spray quality than indirect injection engines [4]. Since the diesel engine is optimized for diesel fuel, a fuel with properties closer to those of diesel is desired to avoid engine modifications. Besides, usage of bio-fuel as a substitute fuel in diesel engines was invented from the protest of the first diesel engine by the inventor of diesel engine Rudolf Diesel at the World Exhibition in Paris in 1900 by using peanut oil as a fuel for the engine. Then in the current years, thoughtful energies have been made by several investigators to use different sources of energy as fuel in present diesel engines especially with constant surge in petroleum prices and worries regarding petroleum accessibility. This paves way for yearning on thesis suggesting that its extensive thesis and demonstrations have shown that this alternative fuel can be used as pure or blends with conventional diesel fuel in untouched diesel engines machine by analyzing its techno economic implications on Engine Test bed. It is established that, the world-wide fossil fuel is predicated to last for the next four decades. The above fossil fuel reserves in Nigeria (22-25 billion barrels) will be exhausted in the next 29 years. Viable alternatives to this conventional energy source must be sort before it becomes too late.
The production and consumption of fossil fuel release tremendous amounts of greenhouse gases such as carbon monoxide (CO), carbon dioxide (CO2), oxides of Nitrogen (NOx), particulate matters (PM), Hydrocarbons (HC) and sulfur dioxide (SO2) into the atmosphere which cause disastrous global warming because of the seemingly irreparable depletion of the ozone layer.
Consequently, the polar ice blocks melt and sea levels rise world-wide causing flooding and unprecedented inundation of entire cities. For instance, nitrous oxide, N2O, a gas emission
associated with the exhaust of petro-engines has an alarming Global Warming Potential (GWP) value of 310 with atmospheric lifetime of 120 years. According to the Manufacturers Association of Nigeria, the cost of conventional diesel production in Nigeria per week is N1.8b and the daily national consumption is (Chemical and Process Engineering Research). [5], million liters. Biodiesel is much more affordable, environmental friendly and highly oxygenated. However, high viscosity and poor volatility are the major limitations of waste vegetable oil for utilization as a fuel in diesel engines. But these limitations are overcome in the oil is transesterified in the presence of a catalyst to form methylesters. [6], They all reported that, biodiesel resulted in fewer CO2 emissions than mineral diesel during complete combustion due to the lower carbon to hydrogen ratio. This is attributed to the fact that biodiesel is a low carbon fuel.
The Payback period and Accounting Rates of returns used for petrol-diesel according to [7] showed 12 to 15.5% financial savings value with pollution adverse effect on ecological system This however calls for higher diesel production percentage with lesser pollution. Besides, [8] suggested using waste organic edible oil to account for better financial saving that could be above the registered value of [7]. Hence this created a room using waste vegetable oil for a better techno economic in financial savings.
According to [9]. transesterification can be defined as a raction between a triglyceride (oil) and an alcohol (e.g., methanol or ethanol) in the presence of a catalyst, such as sodium hydroxide or potassium hydroxide, to chemically break the molecule of the oil into methyl or ethyl esters (biodiesel). Glycerin also known as glycerol, is the by-
Product of this reaction. The process is similar to hydrolysis except that alcohol is used instead of water. This reaction is given below.
catalyst
Triglyceride + 3MeOH 3 Biodiesel + Glycerin (1)
Transesterification reaction can occur at ambient/70 degrees F, but it needs 4-8 hours for completion. The reaction is shortened to 2-4 hours at 105 degrees F. Even shorter time of 1-2 hours at 140 degrees F is possible.
The higher the temperature, the faster the rate of reaction but at temperatures above 65 degrees C (148 degrees F), the boiling point of methanol, the methanol evaporates.
Table 1: Chemical Formula of Biodiesel [9].
Class of Alcohol |
Value of n |
Name of Biodiesel |
Molecular Formula |
Chemical Formula |
Methanol |
16 |
Methyl Linoleate |
CH3(CH2)16COOH |
C19H38O2 |
Ethanol |
17 |
Ethyl stearate |
CH3(CH2)17COOCH3 |
C20H40O2 |
Methanol is preferred to ethanol because methanol gives higher yield of biodiesel due to the simultaneous transesterification of triglycerides and methyl esterification of fatty acids. Secondly, ethanol forms an azeotrope with water. So it is expensive to purify ethanol during recovery. Methanol recycles easier since it does not form an azeotrope.
Compression-Ignition (CI) engines are a class of reciprocationg internal combustion (IC) engines in which combustion is initiated spontaneously by virtue of the rise in temperature during the compression process, [10].
Investment analysis involves computation of return on investment of individual or group of machines/plant using the contract rates of all work the machine does in order to ascertain their level of capitalization [11]. Although, investment decision pointers such as Benefit Cost Ratio (BCR), Net Present Value (NPV), Payback period and Accounting Rates of returns are used individually to ascertain the economic efficiency of systems, their integrated methodology called benefit-cost analysis are often used in new machinery assessment because of its high prediction accuracy [7]and [8]. Cost-benefit analysis is a tool for evaluating all the potential costs and revenues that may be generated prior to actual implementation of investment decisions in order to avoid the risk of going into an unprofitable venture and wasting valuable time and money [12] This involves identification, categorization, projection, monetization, computing and comparison of present values of costs and benefits over the lifespan of an investment [7]. Integrated approach of benefit-cost analysis indicates that an investment is worthy when its projected potential benefits outweigh its costs; its rate of return exceeds the required minimum rate; its pay- back period is less than its salvage period and its net present value exceeds zero [12] Application of this economic evaluation tools in successful machinery investment decisions is evident in report of [13]. Which revealed profitability of garri processing machines in Ondo State of Nigeria was with NPV, BCR and internal rate of return. Integrated BCR and IRR approach was also used in the feasibility study of small-scale palm oil processing in Nigeria by [14].
It is therefore pertinent to embark on the thesis and production of this alternative diesel early enough to be able to cope with the expected cost of biodiesel and huge daily demands when fossil diesel has become extinct.
MATERIALS AND METHOD
About 30 liters of used waste cooking oil were collected from big restaurants of which one liter was first used for demonstrations. Thereafter, more 28 liters of biodiesel were produced which were used both for the fuel property determination and the engine performance analysis.
1 liter of used waste cooking oil, 200 ml of methyl alcohol also known as methanol, 3.5 grams of 0.1% pure potassium hydroxide (KOH), 200 ml capacity graduated cylinder, Large maxon jar (big enough to hold at least 2 liters) were used. Also used are Small
mason jar (big enough to hold at least 1 liters), 1 liter of distilled water with 1 liter capacity measuring cup, pH indicator (10 ml of phenolphthalein solution), Heating element such as a stove, Thermometer and Digital Scale, Chemical gloves and 200 ml capacity glass jar with tight-fitting lid for mixing of chemicals and 1500 ml and 20 ml capacity beakers and a funnel.
Fig. 1: Flowchart of the Transesterification Process
The overall transesterification reaction is given by Equ. (1). There are many reaction kinetics developed. However, in general, three consecutive and reversible reactions are believed to occur. Accordingly, these reactions are given below:
CH2-OOR1
CH2-OH
CH-OOR2 + CH3-
CH2-OOR2
K1
CH-OOR2 + CH3-OOR1 (2)
K1
CH2-OOR3
Triglyceride (TG) Methanol Diglyceride Methyl Ester (Biodiesel)
CH2-OH
CH2-OH
K3
CH-OOR2 + CH3-OH
K4
CH2-OOR3
CH-OOR2 + CH3-OOR3 (3)
CH2-OH
Diglyceride (DG) Methanol Monoglyceride Biodiesel
CH2-OH
CH2-OH
CH-OOR2 + CH3-
CH2-OH
K5
CH-OH + CH3-OOR2 (4)
K6
CH2-OH
Monoglyceride (MG) Methanol Glycerol Biodiesels The overall reaction is below shown
CH2-OOR1
CH2-OH
CH-OOR2 + 3CH3-
catalyst
CH-OH + 3CH3-OOR . (5)
CH2-OOR3
CH2-OH
Triglyceride (TG) Methanol Glycerol Biodiesel
At each of these three stages, a molecule of fatty acid methyl ester is produced so that in all, three molecules of methanol are needed to produce three molecules of ester and one molecule of glycerol or glycerin.
The results of the evaluated biodiesel properties is shown in Table 2. It gives the values of the corresponding properties for petroleum based diesel
Carbon (C) 79.6; Hydrogen (H) 10.5
Oxygen (O) 8.6; Nitrogen (N) 1.3
Table 2: Summarizes the results of the evaluated biodiesel properties. It also gives the values of the corresponding properties for petroleum based diesel
S/n |
Property |
Determined Value |
ASTM Recommended Value |
Corresponding Value for Petro-diesel |
Unit |
1 |
Density @ 15oC |
0.886 |
0.86 0.90 |
0.835 |
Kg/m3 |
2 |
Specific Gravity |
0.86 |
0.85 0.88 |
0.85 |
– |
3 |
Flash Point (Closed Cup) |
130 |
93 minimum |
65 |
oC |
4 |
Cloud Point |
10 |
-3 12 |
5 |
oC |
5 |
Kinematic Viscosity @ 40oC |
4.1 |
1.9 6.0 |
3.4 |
mm2/s |
6 |
Pour Point |
4 |
-15 10 |
-35 15 |
oC |
7 |
Heat of Combustion (Calorific Value) |
40.01 |
37 45 |
45.345 |
MJ/kg |
8 |
Acid Value/Acid Number |
0.27 |
0.5 maximum |
0.12 |
mgKOH/g |
9 |
Water Content |
330 |
500 maximum |
500 maximum |
Mg/kg |
10 |
Methano Content or The 3/27 Test |
0.15 |
0.2 maximum |
– |
% mass |
11 |
Cetane Number |
52 |
45 65 |
46 |
– |
12 |
Boiling Point |
330 |
315 350 |
180 340 |
oC |
The experimentations and test setting up were carried out in these sections. The (112KW/150hp) diesel engine test-bed in the Peace Oil Engineering Laboratory Emene. Test-bed is shown in Fig.2. A is the Fuel tank, B is the Cooling water tank, C is the Fuel flow pipette, D is the Engine and E is Dynamometer
Fig. 2: The 112kW/150hp Diesel Engine Test-Bed Peace Oil Engineering Laboratory Emene
Table 3: Estimated cost of producing 1 liter of biodiesel
S/n |
MATERIAL |
COST (Naira) |
1 |
30 Liters of used cooking oil |
– |
2 |
100 grams of 0.1% pure KOH |
5,000 |
3 |
5 liters of anhydrous methanol |
1500 |
4 |
Laboratory Reagents/Charges |
7,000 |
Total |
13500 |
Total Production = 45 liters of biodiesel plus 5 liters of glycerin used for making soap.
, = 13500/30 =
300.00
It should be noted that the laboratory works was only to determine the amount of KOH required to neutralize the fatty acid in 1
liter of the cooking oil. This will not be done repeatedly. So eliminating the laboratory charges, the cost per liter of biodiesel becomes:
6500/45 = 144.44
Also, the methanol had to be used in excess of the stoichiometric amount but since it does not form an azeotrope with water as
against ethanol; it recycles easily and so the methanol was being recovered and reused. Petroleum-based diesel is sold at N220.00
– N230.00 per liter. Biodiesel can be sold at N180.00 per liter.
RESULTS
Experiments were carried out, values were plotted against the petrol diesel known values. Volumetric Efficiency (%) versus Speed Fig. 3, was plotted from Tables 4 of varying speed at constant load. This depicts the plot of volumetric efficiency against speed for a constant load (varying speed) test. The decreasing movement in efficiency with increase in engine speed was due to the consequence of the engine speed on the air flow rate. As the speed increased under constant load, more air was being strapped to the combustion chamber by the turbo charger. Subsequently, the air volume flow rate increased resultant in lower volumetric efficiency.
Table 4: Volumetric Efficiency versus Speed for Varying Speed Test
Petro-Diesel |
Biodiesel |
||
Varying Speed (rpm) |
Volumetric Efficiency (%) |
Varying Speed (rpm) |
Volumetric Efficiency(%) |
1000 |
43.39 |
1000 |
49.66 |
1200 |
46.68 |
1200 |
49.91 |
1400 |
41.42 |
1400 |
44.61 |
1600 |
37.43 |
1600 |
39.7 |
1800 |
34.3 |
1800 |
36.7 |
2000 |
31.94 |
2000 |
34.3 |
2200 |
29.97 |
2200 |
32.21 |
2400 |
28.18 |
2400 |
30.04 |
2600 |
26.39 |
2600 |
28.51 |
2800 |
25.08 |
2800 |
27.16 |
Petrol-Diesel
Biodiesel
0
500 1000 1500 2000 2500 3000
Speed (rpm)
60
50
40
30
20
10
0
Volume Efficiency
(%)
Fig. 3: Volumetric Efficiency versus Speed for Varying Speed Test
Plotted also was brake thermal efficiency (BTE or BT) one of the main performance parameters which direct the percentage of energy present in the fuel that is transformed into useful work. However, comparison of BTE of biodiesel and conventional diesel
is shown in Fig.4 of Table 5 The graph demonstrates that the efficiency varies and varies between the speeds of 1800 to 2400 rpm. It is proven that biodiesel proved to be more efficient than conventional diesel fuel in this range. For conventional diesel fuel, the efficiency underway to drop when the speed decreased below 2000 rpm. This was due to better combustion of biodiesel because of its higher cetane number. The engine efficiency can then be said to be relative to combustion efficiency.
Table 5: |
Brake Thermal Ef |
ficiency, BT ve |
rsus Speed |
Petrol-Diesel |
Biodiesel |
||
varying Speed(rpm) |
Brake Thermal Efficiency(%) |
varying Speed(rpm) |
Brake Thermal Efficiency(%) |
1000 |
26.97 |
1000 |
40.68 |
1200 |
27.88 |
1200 |
42.82 |
1400 |
27.51 |
1400 |
43.58 |
1600 |
26.15 |
1600 |
43.11 |
1800 |
24.94 |
1800 |
42.51 |
2000 |
23.15 |
2000 |
41.65 |
2200 |
21.17 |
2200 |
39.68 |
2400 |
18.83 |
2400 |
35.8 |
2600 |
16.54 |
2600 |
31.78 |
2800 |
14.06 |
2800 |
29.94 |
Petrol-Diesel
Biodiesel
0 500 1000 1500 2000 2500 3000
Speed (rpm)
50
45
40
35
30
25
20
15
10
5
0
Break Thermal
Efficiency(%)
Fig.4: Brake Thermal Efficiency versus Speed for Varying Speed Test
In addition, the brake specific fuel consumption for biodiesel compared to conventional diesel fuel is shown in Fig. 5 of Table 6. The fuel consumption of biodiesel is relatively higher than that of conventional diesel fuel. This is because the biodiesel has higher specific gravity and viscosity and
thus lower volume flow rate than Petro-diesel. This result is comparable with the result given by [15] and [16]. Where the rate of fuel delivery to engine speed was greatly affected by the density, specific gravity and viscosity of the fuel.
Brake Power(kw) |
Specific Fuel Consumption (kg/k Wh) |
Brake Power |
Specific Fuel Consumption (kg/k Wh) |
15.71 |
0.144 |
17.8 |
0.147 |
14.66 |
0.158 |
16.76 |
0.162 |
13.61 |
0.177 |
15.71 |
0.183 |
12.57 |
0.204 |
14.66 |
0.208 |
11.52 |
0.246 |
13.61 |
0.237 |
10.47 |
0.299 |
12.57 |
0.305 |
9.42 |
0.375 |
1.52 |
0.371 |
8.38 |
0.491 |
10.47 |
0.459 |
7.33 |
0.683 |
9.43 |
0.596 |
6.28 |
0.903 |
8.38 |
0.846 |
Tab le 6: Specific Fuel Consumption versus Brake Power for a Constant Speed Test
Petrol-Diesel
Biodesel
0 5
Break po10wer(kw)
15
20
0.9
0.8
0.7
0.6
0.5
0.4
0.3
0.2
0.1
0
Specific Fuel Consumption
(kg/k Wh)
Fig. 5. Specific Fuel Consumption versus Brake Power for a Constant Speed Test
Having analyzed the experimental data of the biodesel and conventional petro diesel, it becomes inperative to analyze the cost effectiveness for investment. Therefore the result of Investment Analysis of Biodiesel Production Using Waste Vegetable is as shown on the table below. The unit cost of processing and powering the Engine Test bed was determined as shown in Table 7
S/n |
MATERIAL |
COST (Naira) |
1 |
30 Liters of used cooking oil |
– |
2 |
100 grams of 0.1% pure KOH |
5,000 |
3 |
5 liters of anhydrous methanol |
1500 |
4 |
Laboratory Reagents/Charges |
7,000 |
Total |
13500 |
Table 7: Investment Analysis of Biodiesel Production Using Waste Vegetable
Total Production = 45 liters of biodiesel plus 5 liters of glycerin used for making soap.
, = 13500/30 =
300.00
It should be noted that the laboratory works was only to determine the amount of KOH required to neutralize the fatty acid in 1
liter of the cooking oil. This will not be done repeatedly. So eliminating the laboratory charges, the cost per liter of biodiesel becomes:
6500/45 = 144.44
Also, the methanol had to be used in excess of the stoichiometric amount but since it does not form an azeotrope with water as
against ethanol; it recycles easily and so the methanol was being recovered and reused. Petroleum-based diesel is sold at N220.00 – N230.00 per liter.
Biodiesel can be sold at N180.00 per liter.
This gives about 21.7% financial savings compared to petro-diesel.
However, for commercial production of biodiesel, the variable costs include the feedstock, reagents and labor used in the process. The following fixed assets in addition to a factory are essentially needed.
Table 8: Equipment and Cost for Commercial production of Biodiesel
EQUIPMENT |
COST ($) |
Catalyst Pre-mixer |
50,000 |
Transesterification Reactor |
350,000 |
Neutralizer Reactor |
13,500 |
Distillation Column to purify Biodiesel |
60,000 |
Distillation Column to Separate the Methanol |
40,000 |
Distallation Column to Separate the Glycerol |
77,500 |
3 Decanters |
90,000 |
The result showed reduce cost per liter of biodiesel to a gain of N120.00, with 21.7% financial savings compared to petro-diesel as argued and projected by [7] in range the of 12 to 15.5%
CONCLUSION
The techno-economic implications of biodiesel production using waste vegetable oil on Engine Test Bed, the brake power stretched the maximum value for speed ranging from 1800rpm to 2400rpm. This showed that the engine operates more efficiently within the above speed range. Consequently it was waste of economy to run the engine below 1800rpm and/or above 2400rpm. In addition, the speed surged above the efficient range, the smaller time available for combustion, it produces unsuitable combustion and hence the brake power declines. As the brake power declined for the same load, the brake thermal efficiency cuts. Subsequently, the specific fuel consumption (SFC) increased. At a constant speed, an increased in load leads to a proportionate
decreased in the developed torque and an increased in the fuel volume flow rate. These resulted in a decreased in the brake power and consequently a decreased in the brake thermal efficiency. On the contrary, the lower the load, the lesser the force needed to overcome the load would be and hence the higher the brake power and the brake thermal efficiency. The fuel consumption of biodiesel relatively higher than that of conventional diesel fuel. This is because the biodiesel has higher specific gravity and viscosity and thus lower volume flow rate than Petro-diesel. This result is comparable with the result given by researchers where the rate of fuel delivery to engine speed was greatly affected by the density, specific gravity and viscosity of the fuel. The techno economic cost investment gave 21.7% financial savings compared to petro-diesel. However, for commercial production of biodiesel, the variable costs include the feedstock, reagents and labor used in the process which still gave better ROI
REFERENCES
[1] |
Gerpen et al, "Biodiesel Production Technology," National Renewable Energy Laboratory, Colorado, 2004. |
[2] |
K. W. Scholl and S. Sorenson, "Combustion of Soy Bean Oil Methyl Ester in Direct Injection Diesel Engine," in SAE Technical, 2013. |
[3] |
R. M. Munavu and D. Odihiambo, "Physio-Chemical Charaterization of Non Conventional Vegetable Oils For Fuels In Nigeria," Nigerian Journal of Science and Technology, pp. 45 – 52, 2014. |
[4] |
E. Wright and H. Purday, Diesel Engine Fuels and Lubricants, Longman , 2015. |
[5] |
S. H. Choi and Y. Oh, "The Emission Effects by the Use of Biodiesel Fuel," International Journal of Modern Physics, pp. 1 -6, 2006. |
[6] |
Ramadhas, et al, "Use of Vegetable Oils as LC Engine Fuels: A Review," in Renewable Energy, 2004. |
[7] |
S. Gerald and Marta, "An Overview of Benefit Cost Analysis," 2015. [Online]. Available: http://www.agaecom.purdue.edu/staff/shively. |
[8] |
David et al, "A Cost-Benefit Analysis of Document Management Strategies Used at a Financial Institution in Zimbabwe A case Study," SA Journal of Information and management, 2015. |
[9] |
S. Bala, "Studies on Biodiesels From Transformation of Vegetable Oils for Diesel Engines," 2005. |
[10] |
Ozsezen et al, "Compression Ignition Engine Performance and Combustion Charateristics of a Diesel Engine Fueled with Waste Palm Oil and Canola Oil Methyl Ester," ajer, pp. 29 – 36, 2009. |
[11] |
M. Will, "Machinery Investment Analysis," 2017. [Online]. Available: http://www.farmonline.com.au/story/3582186. |
[12] |
G. Jeanne, "small business," 2018. [Online]. Available: http://www.smallbusiness.chron.com/cost-benefit-analysis-important75211.html. |
[13] |
A. S. Ajila, "Investment Analysis of Garri Processing Machineries in Ondo State Nigeria," World journal of Food Science and Technology, pp. 32 – 38, 2017. |
[14] |
Ohiman et al, "Small-Scal Palm Oil Business in Nigeria; A feasibility Study," Greener Journal of Business Management Studies, pp. 70 – 82, 2014. |
|
A. Demirbas and I. Demirbas, "Importance of Rural Bioenergy for Developing Countries," Journal of Energy Conversion and Management, pp. 86 -98, 2007. |
[16] |
J. V. Gerpan, "Biodiesel Processing and Production," in Fuel processings Technical, 2006. |