
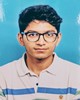
- Open Access
- Authors : Ranveer Patil , Sachin More , Pratik Nagtile
- Paper ID : IJERTV9IS110044
- Volume & Issue : Volume 09, Issue 11 (November 2020)
- Published (First Online): 19-11-2020
- ISSN (Online) : 2278-0181
- Publisher Name : IJERT
- License:
This work is licensed under a Creative Commons Attribution 4.0 International License
Terrain Sensing and Self Adjusting Air Suspension System
Mr. Ranveer Patil Mechanical Department KITs College of Engineering Kolhapur, India
Mr. Sachin More, Mr. Pratik Nagtile
Mechanical Department KITs College of Engineering Kolhapur, India
Abstract Need of autonomy is must in every field. Various sectors such as packaging, manufacturing, robotics and automotive have already implemented automation, and adopted various technological advances to achieve it. Here in this paper, there is a revolutionary technology that will make an impact on automotive industry. We have done doing various activities and research on automotive sector especially on autonomy of vehicles. Advance vehicles are emerging technology adopted by many companies in the world. In this paper we have put a light on a critical problem in vehicles which havent been solved yet. The problem is related to maneuver of a car according to the road conditions; many autonomous as well high end cars are facing this problem in past few years. We have come up with a solution which will tackle this problem and make the maneuvers much easier by using inspiring RGB-D sensor and advance air suspension system. The reason for studying and implementing this technology is to make cars safer and comfortable for driver as well as passenger.
Pot Holes: Bowl-shaped depressions in the road surface, resulting from the loss of pavement material.
I. INTRODUCTION
In the past few years the development was possible due to the automotive industry. The automobile was first invented and perfected in Germany and France in the late 1800s. From late 1800s the real era of development started. Automotive gave mankind the medium through which they can expand their businesses all over the country. Automotive made the transportation to different states possible which created a connection between two states. In any automotive, suspension system is among the most important part because it stabilizes the vehicle by keeping it in contact with the road. The suspension system not only looks after vehicle dynamics but also the comfort of the passenger. In 21st century we cant predict the road condition, it might change every 50km or 10km or even 3km so the passenger is not aware of such type of changes and due to unawareness various components of automotive might get distorted.
We have developed such a system that it will evaluate the road condition and texture with the help of low cost RGB-D sensors and micro controllers, and to react accordingly to the required condition and comfort with the help of air suspension.
II. ROAD CONDITIONS
Corrugations: An unsealed road surface having ripples or undulations along the road.
Rough: The consequence of irregularities, uneven in nature, in the longitudinal profile of a road with respect to the intended profile. Interpretation of conditions will not allow vehicles to use the road at customary speeds.
Rutting: A longitudinal deformation of a pavement surface formed by the wheels of vehicles. May be on a sealed or unsealed road.
III. KINECT V2.0 RGB-D SENSOR
In November 2010, Microsoft released the Kinect RGB-D sensor as a new Natural User Interface (NUI) for its XBOX 360 gaming platform. The Kinect, like other RGB-D sensors, provides color information as well as the estimated depth for each pixel. At $150, the Kinect is an order of magnitude cheaper than similar sensors that had existed before it. This has dramatically reinvigorated interest in RGB-D sensors and their applications in areas such as Natural User Interfaces, reconstruction and virtual reality, or 3D mapping. The Kinect v2.0 is the successor of the Xtion Pro Live RGB-D camera, called the Kinect v1.0. The version 2.0 Kinect RGB-D camera consists of a color (RGB) camera, an IR illuminator or projector and IR camera. While the RGB camera records color information in high definition (HD), the IR projector emits an infrared laser and the IR camera is the sensor for the infrared laser.:
A. Kinect v2.0 RGB-D sensor specification
B. Working of Kinect v2.0 RGB-D sensor
The Kinect v2 field in the horizontal is 70.6° and 60° in the vertical as depicted in Figure . The values in the z-direction (depth values), are calculated using the Time of Flight (ToF) principle, as shown in Eq. (1), and the x and y values are determined by using the homogeneous image coordinates u and v, and calculated as in Eqs. (2) and (3). The RGB and IR images acquired with the Kinect v2.0 partially overlap, because the RGB color camera has a wider horizontal field of view (FOV), and IR camera has a larger vertical FOV.
where z is the depth measure in meters, is the phase shift, c is the speed of light and f is the modulation frequency; x is the horizontal position, u is the vertical image coordinate, Cx is optical center in the X-direction and fx is the focal length in the X-direction, and y is the vertical position, v is the horizontal image coordinate, Cy is optical center in the Y-direction and fy is the focal length in the Y- direction. In Figure 1(b), P is the measured point on object surface, E is the IR emitter C is the IR sensor, and h or z is the unknown distance of measured point from sensor origin.
C. Potholes Measurement
RGB-D sensor will measure the unevenness on road surface, potholes and speed breakers. The unevenness in the surface and speed breakers will be measured with the help of working phenomenon given in 1.2.
D. Potholes Metrology
Figure 4 illustrates the conceptual approximation of a pothole with dimensional parameters that define the pothole metrology as: width, depth, surface area and volume. Assuming the potholes have the shape of a circular paraboloid, then in 2D they can be represented by the function f(x,y)=x2+y2.
E. Pothole depth determination using depth image
The depth-image plane (Figure 4) is one of the noise factors, whereby the plane is not necessarily parallel to the pavement surface. The noise points, which are the non-defect points between the pavement-pothole plane and the camera, have to be filtered out for the accurate depth detection and the subsequent 2D-pothole detection from the depth image. The general principle of removing the outlier points (noise), is by determining the local minimum of each column and then subtracting from the column itself in order to extract the pothole from the rest of data. The minimum of each column defines the depth below which the pothole starts on the road pavement surface, and is referred to as the depth-image plane. Using this approach, the depths di including the maximum depth dimax can be quantified, and the mean depth di for a given pothole is also computed.
z=h=c/4f E1
x=(uCx)/fx E2
y=(vCx)/fy E3
F. Pothole width measurement
The width of a pothole can be defined by the semi- major aa and semi-minor b axes, on the assumption that an ellipse, based on the major path elliptic regression, is used pothole shape extraction. To determine the lateral width of the pothole, it can be estimated using a circular paraboloid, which is an elliptical paraboloid. And, an elliptical paraboloid is a surface with parabolic cross-sections in 2-orthogonal directions and 1-elliptical cross-section in the other orthogonal direction. Using an edge detection algorithm, the near-true shape of the pothole is first derived using the proposed SFCM, and then an elliptical fit is used to approximate the shape, from which the axes are defined for the calculation of the surface area and volume of the pothole.
G. Pothole surface area determination
In order to determine the surface area o the pothole, the optimally detected edge is used to fit the shape of the pothole as either elliptic paraboloid or circular paraboloid. While the former is defined by the dimensions of semi-major axis aa and semi-minor axis b, the latter is defined by the estimated radius rr . The surface area is then computed by using the surface integrals of either of the paraboloids, as respectively shown in Eqs. (17) and (18) for the elliptic and circular paraboloids.
If pixels counts are used, then Eq. (19) can be implemented. Whereby in Eq. (19), l is the pixel size and Ip is the binary value of pixel at coordinate position (x,y). The area Ap is estimated on the basis of the average of a 2 × 2 window.
H. Pothole volume estimation
If T is a closed region bounded by a surface S, and F is a vector field defined at each point of T and on its boundary surface, then TFdv is the volume integral of F through the bounded region T. As in case for the surface area of a pothole, the area is either estimated by an elliptic paraboloid or a circular paraboloid. The volume of the elliptic paraboloid V can be estimated according to Eq. (20), and the volume Vr of the pothole is estimated using a circular paraboloid as in Eq. (21).
Since the depth for each pixel didi is obtainable from the depth image, the integration of all small volumes represented by each pixel leads to the total volume of area within the frame. Therefore the estimated volume VdVd in terms of the pixel depth is given by Eq. (22).
Where Vd is the total pothole volume, and Id(x,y) is depth of pixel p at location (x,y).
I. Prototype implementation strategy for pothole detection using low-cost sensor
Figure 5 illustrates the processing steps in implementing the detection, and visualization potholes and related metrological parameters from the Kinect v2.0 RGB-D, based on the experimental iMMSS data capture system. In summary the processing system should comprise of data acquisition and geometric transformation; preprocessing for noise minimization; cascaded pothole detection approach from fused RGB-D data using dual-clustering approach comprising of k-means and spatial fuzzy c-means, and a parallel processing system for pothole area and volume detection from RGB and depth imagery.
IV. AIR SUSPENSION
Basically Air suspension is a type of suspension in which compressed air is used as a working medium. The suspension is powered by either electrical means or by engine driven compressor.
The suspension unit consist cylindrical shaped rubber bellows into which compressed air is allowed to enter resulting into lifting of the chassis. The reason why rubber bellows are used is the pressure of the compressed air can be varied according to the requirement resulting into inflation of the bellow and lifting the chassis from the axle.
The most interesting part why we are using Air suspension is Air suspension units have the capability of lifting the vehicle as well as holding the vehicle in the lifted condition for a particular period of time. The holding action is very important as it can reduce the shock caused due to unevenness on the roads by a huge amount.
A. Why Air suspension?
Due to changing technology and varying requirements and also taking into consideration the comfort and luxury Air suspension is widely used by the renowned car brands such as Maybach, Rolls Royce, Jeep, Lexus, Porsche, land rover, tesla and ford.
Sports and comfort modes
Air suspension provides the ability to lift the vehicle at higher speed and continues to maintain height when engine is not running.
Adjustable suspension
Adjustable suspension in the sense they allow to sit extremely low and can rise at any height to maneuver over the obstacles on paved surfaces.
Off road pleasure
Air suspension Systems using reservoir are fully adjustable and can vary the wheel pressure allowing the vehicle to tilt sideways ,front to back or even Hop the entire vehicle into air.
Increased load carrying Capacity
Air suspension is a common suspension upgrade for those who tow heavy loads as air suspension is the most reliable and efficient suspension.
Automatic Air suspension system based on fuzzy control
This is the most important application or you can say the use of ASS. Most of the vehicles are turning towards using the Automatic Air suspension for controlling the vehicle over a large range of Variations in the road surfaces.
Nowadays SUVs are inclined towards Automatic air suspension to ensure its effectiveness over the terrain.
B. Principle of working of air suspension system
Basically air suspension system uses the properties of air to obtain necessary movement of vehicle or any other lifting of lowering of load. Air suspension system consists of a cylindrical part you can consider it as a piston with a rod and the rod is connected with the chassis of the vehicle which in result lifts the whole vehicle.
C. Various parts in an air suspension unit
1. Air spring (Rubber bellow):
A typical air spring is shown in the figure. The air springs are simply tough rubber and plastic bags connected by a
series of devices such as Air compressor, sensors and electronic controls.
Air spring is nothing but a shock absorber which used compressed air as a cushion instead of metal spring.
2. On board Compressor
All the air suspension systems come with a compressed mounted either near to each bag (Air spring) or a central compressor supplying air through pumps.The compressois generally mounted on thevehicles frame.
The compressor works by drawing the air from environment and provides the pressurized air to each bag according to requirement.The compressors can be operated manually or automatically depending upon the complexity of the system where it is been used.
Nowadays many car brands are opting for automatic air suspension system to carry out the suspension work as it is reliable and it gives best results for uneven roads and sandy paths.
D. Height control valves
Height control valves are often the most important units in an air suspension system . The control of the height is besides the driver where he can adjust the height as much as required. The height control valve also maintains a constant ride height by automatically adding air to or exhausting air from the air suspension system.
Air spring and the compressor are the main components in the air suspension system.
Other components include the
a) Sensors
b) Desiccant (air dryer)
c) Tanks
d) Lines
E. Working of air suspension
The first and the most important point to consider while working of the air suspension system is then ride height of the vehicle. Generally the height of the vehicle is determined by the manufacturer itself.
Ride height : Ride height is simply the distance between Frame of the vehicle axles that the vehicles ride at.
Working:
Now at first the Air bags i.e (air springs) are connected on the frame of the vehicle .The components such as compressor , HCVs , lines, tanks are mounted on the frame itself. The height control valves are connected to the air bags .The lines which connect the HCV valves to the axles rotates with the axle which rotates the valves up and down. Now when the vehicle experiences a shock or it passes over discontinuity, the vehicle weight is transferred to the air springs which then get compressed this moves the frame towards the axles. And this forces the HCV linkage up and this opens up the valve and air is fed into the air bags. The added pressure and volume inflates the bags and when the weight of the vehicle reduces the air is locked into the air bags, excess air is returned through the exhaust line and thus maintaining proper ride height.
V. CONTROLLER
After sensing and setting actuators it is most important to install a micro controller. A microcontroller is a computer present in a single integrated circuit which is dedicaed to perform one task and execute one specific application.
It contains memory, programmable input/output peripherals as well a processor. Microcontrollers are mostly designed for embedded applications and are heavily used in automatically controlled electronic devices such as cell phones, cameras, microwave ovens, washing machines, etc.
In our system micro controller will gain the input in the form of co-ordinates of road which consists of pothole dimensions and unevenness of road surface, the micro controller will then compute the data and as pre set program actuators will actuate. The set program consists of required amount of actuation required for that type of road conditions. The micro controller which we are going to use here is Raspberry Pi 4. Raspberry Pi 4:
Released in 2019 Raspberry Pi 4 is the fastest microcontroller board available today. With its 4GB RAM you can build powerful and advanced electronic projects. Raspberry Pi 4 can offer up to 1.2A current for USB devices. Its available in different RAM choices, ranging from 1GB up to 4GB. More features include on-board wireless LAN, Bluetooth 5.0, two USB 2.0 and USB 3.0 ports, two Micro HDMI ports and a Gigabit Ethernet port.
VI. ASSEMBLING AND WORKING OF THE SYSTEM Assembling the system is the most important thing. First part will be the RGB sensors which will sense the road condition if there are any uneven surfaces, potholes, speed breakers or gravels on the road (working explained in section 2). This data will be sent to the control unit which is Raspberry Pi 4, depending upon the ground clearance of the car response for data will be set. Response is calculated from number of tests carried out on the cars which includes lifting of car by how much mm when it faces a speed beaker or a pothole or during a curve road. After finding and feeding all this data in the controller then the controller is joined to the actuator. The actuator will work as per given command. In our system actuator is pneumatic/air suspension.
Design of the System:
Sensors are located on the top of the car hood. The purpose behind locating it there is, a wide range of view is available and a due to this predictability of the road is possible. Further important thing is to connect sensor system with the air suspension.
VI. CONCLUSION
With the Kinect v2.0 successfully senses the road condition and then with the help of Raspberry Pi 4 we can actuate the Air suspension. This technology will play an crucial role in making automotive industry more advance. The development currently going on in the automotive industry is Autonomous vehicles. The problem faced by the AVs is they cant react to the road conditions and the system which we designed will help the AVs to work with more efficiency. Apart from AVs the current vehicles which are having lower ground clearance such as luxury sedans and sport vehicles will benefit with this technology.
REFERENCES
1. https://www.techopedia.com/definition/3641/microcontroller
2. https://www.raspberrypi.org/help/what-%20is-a-raspberry-pi/
3. https://grabcad.com/library/pontiac-g8-2009-1
4. https://www.nolo.com/legal-encyclopedia/vehicle-damage-due- to-poor-road-conditions-who-is-liable.html
5. https://www.intechopen.com/online-first/on-the-use-of-low-cost- rgb-d-sensors-for-autonomous-pothole-detection-with-spatial- fuzzy-c-means-seg
6. http://alumni.cs.ucr.edu/~klitomis/files/RGBD-intro.pdf
7. https://www.semanticscholar.org/paper/Calibration-of-Kinect- type-RGB-D-sensors-for- Karan/1c77a167ce49767712e4fbed2d439dc656667a72
8. https://www.hwhcorp.com/ml57000-014.html
9. https://www.merriam-webster.com/dictionary/air%20spring