
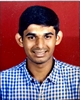
- Open Access
- Authors : Omkar Karnik, Shreyas Kotian
- Paper ID : IJERTV13IS040063
- Volume & Issue : Volume 13, Issue 04 (April 2024)
- Published (First Online): 16-04-2024
- ISSN (Online) : 2278-0181
- Publisher Name : IJERT
- License:
This work is licensed under a Creative Commons Attribution 4.0 International License
Theoretical Investigation for Performance Analysis of a Car Radiator for Effective Cooling of Internal Combustion Engine
Omkar Karnik
Department of Mechanical Engineering, KJ Somaiya College of Engineering, Mumbai- 400077,India
Shreyas Kotian
Department of Mechanical and Aerospace Engineering, University of California, San Diego, San Diego, CA, 92093, USA.
ABSTRACT
Goal of the present investigation is to analyze the thermal and hydraulic performance parameters of plate fin heat exchanger (car radiator) using a theoretical methodology at various operating conditions of hot and cold fluid. It was observed that the effectiveness of heat exchanger was above 44 % for all the working conditions and increased up to 94 % with decreasing cold fluid flow rate up to Reynolds number of 30000 and inlet temperature of
40°C. The overall heat transfer coefficient was above 55 W/m2K and increases up to 130 W/m2K with hot fluid flowrate. It is also observed from the results that with increasing hot fluid flow rate the pressure drop across tube and air sides of the heat exchanger decreases up to 4 Pa and increases up to 4300 Pa respectively which is within the appreciable limit.
Keywords: Theoretical investigation, Internal combustion engine, Performance analysis.
NOMENCLATURE
Symbol |
Terminology |
Unit/ Value |
A |
Heat transfer surface area |
m2 |
bmep |
Brake Mean Effective Pressure |
kPa |
BP |
Brake Power |
kW |
() |
Specific heat capacity of air in the cylinder at constant volume |
J/ kg.K |
() |
Specific heat capacity of fuel at constant volume |
J/ kg.K |
Specific heat capacity of cold fluid at constant volume |
J/ kg.K |
|
C* |
Heat capacity rate ratio, Cmin/Cmax |
– |
Hydraulic diameter of tube |
m |
Friction factor of the air |
– |
|
Friction factor of the tube |
– |
|
fmep |
Frictional Mean Effective Pressure |
kPa |
Fluid mass velocity of coolant |
kg/m2 s |
|
Fluid mass velocity of air |
kg/m2 s |
|
imep |
Indicated Mean Effective Pressure |
kPa |
IP |
Indicated Power |
kW |
k |
0.5 for 4-stroke engine |
– |
1 for 2-stroke engine |
– |
|
Ls |
Stroke length of cylinder |
m |
n |
Number of cylinders in the engine |
– |
N |
Engine speed |
RPM |
NTU |
Number of Transfer Units |
– |
1 |
Pressure of gas at the commencement of compression process in Otto cycle |
K |
Heat transfer from engine gas to the inner liner of the cylinder |
kW |
|
Heat transfer from inner liner to the outer liner of cylinder |
kW |
|
Heat transfer from the outer liner of the cylinder to the coolant jacket |
kW |
|
r |
Compression ratio of the cylinder |
– |
R |
Gas Constant |
kJ/ kg K |
Reynolds number of cold fluid |
– |
|
Reynolds number of hot fluid |
– |
|
Tube wall thickness |
m |
|
2 |
Temperature of gas at end of compression process in Otto cycle |
K |
3 |
Maximum temperature of gas in Otto cycle |
K |
Inner temperature of liner of cylinder |
K |
|
Outer temperature of liner of cylinder |
K |
U |
Overall heat transfer coefficient of heat exchanger |
W m-2 K -1 |
v |
Velocity of air |
m/s |
Velocity of coolant in tube |
m/s |
|
1 |
Volume of gas at end of compression process in Ottocycle |
K |
Greek Symbols |
||
Dynamic viscosity of coolant |
Pa s |
|
Density of coolant |
kg/m3 |
|
Density of petrol |
kg/m3 |
|
Efficiency of heat exchanger |
– |
|
Specific heat ratio |
– |
|
Air free flow ratio |
– |
|
Fin efficiency |
– |
|
Surface efficiency |
– |
|
Pressure drop |
Pa |
-
INTRODUCTION
Plate fin heat exchangers are a class compact heat exchangers are used to transmit heat energybetween two streams at different temperatures in an array of applications. Plate fin heat exchangersare employed as car radiators in the automobile industry because of their high surface to volume ratio, which allows for excellent cooling of internal combustion engines. This component has received little attention for a number of years, with little change in its production cost, operation, or geometry. As a result, in order to effectively cool the engine, it is required to examine the performance parameters of the automobile radiator. Many researchers have examined various aspects of the car radiator. The influence of geometric characteristics (fin spacing, louvre angle) and the importance of flow of cooling fluid on the efficacy of the radiator was investigated by (Oliet et al., 2007). The impact of changing the flow rates of different streams on performance characteristics (coolant load, pressure drop) was also investigated. (Chen et al., 2001) studied the thermal characteristics of the radiator in the laboratory and established regression models for different thermal and hydraulic performance parameters of the heat exchanger. (Perez-Segarra et al., 2008, Oliet et al., 2008) developed a simulation model for two radiator models and compared the performance parameters whose results were compared to that of the experimental observations.
(Gollin et al., 1996) studied how the thermo-hydraulic performance varied under different models of the heat exchanger using various ethylene glycol combinations as a coolant. Using the finite dfference method and the concept of thermal resistance, (Yadav et al., 2011) examined the thermal and hydraulic parameters of an automotive radiator. A bench scale system was also created, with various performance characteristics being evaluated using different concentrations of water and propylene glycol as coolants. (Lin et al., 2000) studied the effect of temperature variations in the ambient and coolant radiator inlet on the specific dissipation rate. With ambient temperatures as well as coolant temperatures varying to a great extent, the findings were computed using a analytical heat transfer model of the heat exchanger. (Charyulu et al., 1999) performed computer simulations on a finned tube heat exchanger of a diesel engine using the NTU technique, concentrating on the effect of materialistic properties of the fin and tube on the efficacy of the heatexchanger. The effect of flow rates and temperatures of the fluid streams on the performance parameters of the heat exchanger were also studied. (Elias et al., 2014) investigated if nano fluidscould be utilised as coolants in automotive radiators to improve heat transfer performance. New discoveries on the thermal characteristics of Al2O3 nanoparticles distributed in water are also presented in this work. (Leong et al., 2010) used ethylene glycol-based copper nano fluids to study the thermal characteristics of a heat exchanger which is used in transport vehicles. The thermal performance of a nano fluid-operated automobile car radiator was compared to that of a radiator using standard coolants such as ethylene glycol mixes. (Nieh et al., 2014) studied the use of nano-coolants to improve the heat recovery of an automobile radiator in an experimental setting. With various nanoparticle concentrations and sample temperatures, the thermal properties of the nano coolants were measured, and the nano coolants were then used in an air-cooled radiator to assess various thermal and hydraulic characteristics at different flow rates of the hot and cold stream and various inlet temperature of the hot fluid.
(Jamnani et al., 2011) evaluated the use of forced convection heat transfer in a vehicle radiator to cool fluids of different chemical compositions. The heat transmission properties of pure water and pure ethylene glycol, as well as their combinations, were also examined. With different amounts of different nanoparticles added to the water, (Peyghambarzadeh et al., 2013) evaluated the thermal and hydraulic performance of the heat exchanger using the – NTU approach. In order to calculate the thermal as well as hydraulic characteristics for a nano fluid flowing in a radiator with specific heat load, (Bozorgan et al., 2012) examined the heat transfer correlations between airflow and nano fluid coolant. (Hussein et al., 2014) examined the hydraulic and thermal performance parameters of SiO2 nano particles distributed in water as a base fluid in a finned heat exchanger for a variety of industrial applications by validating it experimentally and numerically in a car radiator. (Sheikhzadeh et al., 2014) investigated the influence of increasing nanoparticle concentrations in the coolant on the heat exchanger's thermal performance metrics. The performance parameters of the heat exchanger are dependent on the geometry as well as the flow conditions, according to a comprehensive review of the literature. We investigated the impact of cold and hot fluid flow rates on the heat exchanger's performance parameters in this study.
-
GEOMETRY OF HEAT EXCHANGER
For the present study, a plate fin type heat exchanger has been used. Table 1 and Table 2 illustratethe geometrical parameters of the heat exchanger on the air side and tube side respectively.
Table 1
Geometrical parameters of the radiator on the air side.
Geometric Parameters
Magnitude
Radiator length
0.1 m
Radiator width
0.04 m
Radiator height
0.1 m
Length of tube
0.1 m
Width of tube
0.019 m
Height of tube
0.003 m
Thickness of tube
0.0005 m
Number of tubes
14
Distance between tubes
0.01 m
Tube hydraulic diameter
0.00351 m
Air free flow ratio
0.33
Table 2
Geometrical parameters of the radiator on the tube side.
Description
Magnitude
Fin width
0.04 m
Fin height
0.01 m
Fin thickness
0.0005 m
Number of fins per row
251
Area of cross section
0.000045 m
-
METHODOLOGY
-
Development of Theoretical Model:
Although there has been a good amount of research work done before, the development of current model was done by incorporating the heat transfer from engine cylinder to the coolantjacket which is a novel methodology not seen in most literature survey.
Conditions under which the model was developed: –
-
All tubes, plates and fins are taken to be of uniform size and shape each
-
Convective heat transfer coefficient varies axially but is again constant for a particularsection throughout
-
Parameters such as Prandtl Number, density, viscosity, specific heat do not changethroughout the heat exchanger but for a particular given inlet temperature.
-
Material properties do not change.
The designing of a car radiator begins with the determination of cooling load which is to be dissipated by the radiator, determination of outlet temperature of the coolant from the coolant jacket and sizing of the car radiator as a compact crossflow heat exchanger.
-
Determination of cooling load requirements for internal combustion engine
From a sample space of 30 Indian hatchback car engines (brake power rated from 30 HP to 108 HP), the following engine parameters were obtained: brake power, bore length, stroke length, number of cylinders, compression ratio, cylinder capacity (in cc), mileage and RPM at maximum brake power. From these parameters the following engine performance parameters were calculated.
The brake power of the engine is calculated as:
6 ×
= (1)
× 10
Heywood [19], stated that the frictional mean effective pressure(fmep) is related to the engine speed according to the following relation. Here, the maximum engine speed is considered for extreme operating conditions.
= 0.97 + 0.15 (
1000
) + 0.05 (
)
1000
2 (2)
Subsequently, the indicated mean effective pressure is given as:
= + (3)
Hence, the indicated power is calculated as:
× × 106 (4)
=
By calculating the indicated power for all the car engines, the highest calculated value for indicatedpower is 103.63 kW. According to Stone [17], for petrol engines, the heat energy to the coolant isnearly 28% of the indicated power. Hence for the calculations of the car radiator, the coolant loadis taken as 30 kW.
-
Determination of coolant outlet temperature from engine
The determination of coolant outlet temperature from the coolant jacket begins with the calculationof maximum temperature attained during the combustion process in the engine cylinder at varyingengine speeds and engine load. During this process maximum heat tansfer takes place from the engine cylinder to the coolant jacket. Subsequently, applying appropriate heat transfer equations, the heat transferred from the engine cylinder to the coolant jacket is calculated and the coolant outlet temperature from the engine is obtained.
-
Calculation of maximum temperature in engine cylinder Thus, the maximum temperature in engine cylinder is obtained as:
. () = . (). (3 2) (5)
Mass of fuel consumed per second at various car speeds () is given as:
= ×
(6)3600
Mass of air consumed for combustion process in the engine cylinder () is given as:
1. 1 (7)
= .
1 2
Temperature at beginning of compression process in the engine (2) is given by:
2 = 1. ()1 (8)
-
Calculation of heat transfer from engine cylinder to coolant jacket
The heat transfer from engine chamber to the coolant jacket is given by the equation:
= =
(9)
With substituting with the corresponding heat transfer equation, we get the following relation andthe coolant outlet temperature from the coolant jacket (Tc) is calculated as:
2. . . ( )
. . ( ) =
ln ( )
= . . ( )
(10)
-
-
Design and analysis of compact heat exchanger for engine cooling system
There are two critical factors to consider while designing a heat exchanger. One is the heat exchanger's thermal performance, and the other is the heat exchanger's hydraulic performance. Theflow rate of the hot and cold fluid streams, as well as their inlet temperatures, are the primary determinants of these performance metrics.
Tube side calculations
The heat transfer coefficient of the coolant is given as:
. [( ) ] (11)
= . . 0.66
.
() . ()
= (12)
-
Air side calculations
For practical conditions the car speeds are assumed to vary from 4 m/s to 42 m/s wherein the carradiator operates. Therefore, the Reynolds number of air side is given as:
. .
=
.
(13)
Since the range of the Reynolds number is less than 5 × 105, the flow of air is laminar in nature.Hence according to Sadik [18], the equation for Nusselt number for laminar flow is given as:
= 0.037 × ()0.5 × ()0.33 (14)
Subsequently the coefficient of heat transfer coefficient of air is calculated as:
.
=
(15)
Also, the thermal resistance offered by aluminium as the tube wall is given as:
=
. (16)
According to Peyghambarzadeh [7], the overall heat transfer coefficient is expressed as:
1 1 1
= + +
(17)
. . . . .
The surface efficiency related to the fin efficiency is as follows:
= 1 (1 ) (18)
Where, is the surface area of the fin.
= + (19)
Where, is the surface area of the bare tube without fins.The fin efficiency () can be calculated as:
tanh ()
=
where,
(20)
2
= (21)
.
Subsequently, the number of heat transfer units is expressed as:
.
= (22)
The specific heat capacities of the two fluids
= . (23)
= . (24)
The heat capacity ratio is defined as:
=
(25)
The relationship between effectiveness of heat exchanger, heat capacity ratio is given as:
= 1 (1 [(1)]) (26)
Consequently, taking into account the effectiveness (), heat to be dissipated by the radiator (Q), coolant inlet temperature(Thi), air inlet temperature (Tci), the outlet temperature(Tho) is calculatedas:
= . . ( ) (27)
= . . ( ) (28)
-
-
Calculation of pressure drop across air side and tube side:
The pressure drop across the radiator core (air side) and the pressure drop across the radiator tubes(tube side) are given as: For Air side:
The total air side pressure drop across the heat exchanger is given by the following equation.
= ([ 2) ( 2)
2
+ 1 + 2 ( 1) + 1 ] (29)
2
=
2
2
[(1 + )2(1) +
. ]
(30)
For Tube side:
The pressure drop across the tube side is given as:
= (
1 2) . [4. ] (31)
2
Where, f is the friction factor of the tube which varies according to the Reynolds number of hotfluid.
-
-
-
RESULTS AND DISCUSSION
The effect of inlet parameters of the heat exchanger on the performance parameters werestudied for theoretically and appropriate graphs were plotted.
-
Effect of Hot fluid flow rate on performance parameters of heat exchanger
Fig. 1. Variation of overall heat transfer coefficient with Reynolds number of hot fluid at various temperatures
of hot fluid and different Reynolds number of the cold fluid.
Figure [1] depicts the variation in overall heat transfer coefficient with variation in mass flow rate of the hot streams and different discharges of the cold stream. For the lowest and highest cold fluid flow rates (Re = 30000 to 300000), U increases with hot fluid flow for maximum operating temperatures of hot fluid. It's because the thermal characteristic of a hot fluid stream augments asthe discharge of the stream increases. It is also reported that as the cold fluid flow rate increases, the overall heat transfer coefficient increases. It's because the heat transfer coefficient of cold fluidincreases as the flow rate of cold fluid increases.
-
Effect of hot fluid Reynolds number vs Overall Effectiveness ()
Figure [2] depicts the relationship between total efficiency and hot fluid Reynolds number at various temperatures and cold fluid Reynolds numbers. For severe operating temperatures of hot fluid at the lowest cold fluid flow rate (Re=30000), the effectiveness rises (from 76% to 94%) withhot fluid flow rate (from 76% to 94%). Also, owing of the lower Re of cold fluid, the effectivenessof higher cold
fluid flow rates is lower than lower cold fluid flow rates due to more residence time.For severe operating temperatures of hot fluid (Re. from 100 to 900), the efficacy lowers and increases with hot fluid flow rate (Re. from 100 to 900). For the maximum cold fluid flow rate (Re=300000), the effectiveness falls and increases with hot fluid flow rate (Re varying from 100 to 900).
Fig. 2. Variation of overall effectiveness () with Reynolds number of hot fluid at various temperatures of hot fluid and different Reynolds number of the cold fluid.
-
Effect of hot fluid Reynolds number vs Pressure drop across air and tube side
Fig. 3. Variation of pressure drop with Reynolds number of hot fluid at various temperatures of hot fluid and different Reynolds number of the cold fluid.
Figure [3] depicts the drop in pressure on the tube side and air side as a function of the hot fluid'sRe at various temperatures and the cold fluid's Re. At extreme hot fluid temperatures and highest Re of cold fluid, the tube side pressure drop increases with Reynolds number of hot fluid (300000).The tube side pressure drop is relatd to the hot fluid velocity and the tube friction factor, which increases with the hot fluid flow rate, as shown by equation [31]. For varied cold fluid flow rates,it is also noted that the air side pressure drop does not alter significantly with rise in hot fluid flowrate. Due to the variable nature of the heat exchanger's efficacy, the pressure drop reaches a minimal value at extreme cold fluid flow rate (Re(c) = 300000).
-
Effect of Cold fluid flow rate on performance parameters of heat exchanger
Fig. 4. Variation of overall heat transfer rate with Reynolds number of cold fluid at varioustemperatures of hot fluid and different Reynolds number of hot fluid.
Figure [4] demonstrates how the overall heat transfer rate varies with the Re of the cold fluid at different temperatures and different Re of the hot fluid. For extreme operating temperatures of hot fluid, U increases with cold fluid flow rate (Re. from 30000 to 300000) for the lowest and maximum hot fluid flow rate (Re =100 to 900). It's because the heat transfer coefficient of cold fluid increases as the flow rate of cold fluid increases. It's also been discovered that as the rate of hot fluid flow increases, the overall heat transfer coefficient increases (Re. from 100 to 900). It's because the heat transfer coefficient of a hot fluid increases as the flow rate of the hot fluid increases.
-
Effect of cold fluid flow rate vs Overall effectiveness ()
Fig. 5. Variation of overall effectiveness () with
Reynolds number of cold fluid at various temperatures
of hot fluid and different Reynolds number of the hot fluid.
Figure [5] depicts the variance in overall efficacy as a function of the Reynolds number of the cold strean at various temperatures and Reynolds numbers of the hot fluid. For the highest Reynolds number of hot fluid, the efficiency falls with increasing Re of cold fluid (900). It's because the cold fluid has a longer residence period at a lower Reynolds number. Also, for the lowest Re of hot fluid (100) at 100°C of hot fluid temperature, the efficiency improves with the Re of cold fluid. For 40°C of hot fluid temperature and lowest hot fluid flow rate (Re=100), the effectiveness drops and increases with cold fluid flow rate (Re. from 30000 to 300000). It's because the specific heat capacities of hot and cold fluids reach their lowest points at various hot fluid flow rates.
-
Effect of cold fluid flow rate vs Pressure Drop (Air side)
Figure [6] shows the drop in pressure as a function of the Re of the cold fluid at various temperatures and Reynolds numbers of the hot fluid. It's also been discovered that as the cold fluidflow rate (Re(c)) rises from 30000 to 300000, the air side pressure drop
increases. The air side pressure drop is proportional to the mass velocity of the cold fluid, as shown by equation [30], andso the pressure drop at the air side increases as the cold fluid flow rate increases.
Fig. 6. Variation of pressure drop with Reynolds number of cold fluid at various temperatures of hot fluid and different Reynolds number of hot fluid.
-
Effect of Inlet temperature of hot fluid on performance parameters of heat exchanger
Fig. 7. Variation of overall heat transfer coefficient with hot
fluid inlet temperature at various flow rates of hot fluid and cold fluid.
Figure [7] demonstrates how the overall heat transfer coefficient varies with hot fluid inlet temperature at various hot fluid and cold fluid flow rates. With increasing the temperature of the hot fluid inlet, the overall heat transfer coefficient changes very little. As a result, a mean value can be employed with acceptable precision within a range of coolant temperature inlet conditionsfor a particular set of operational parameters, saving money and effort.
-
Effect of hot fluid inlet temperature (Tho) vs overall effectiveness
Figure [8] depicts the relationship between overall efficiency and hot fluid input temperature for various hot fluid and cold fluid flow rates. Because the maximum heat capacity of the fluid increases to a
higher extent than the minimum heat capacity of the fluid, efficiency declines with rising hot fluid temperature for given hot and cold fluid flow rates.
Fig. 8. Variation of overall effectiveness with hot fluid inlet temperature at various flow ratesof hot fluid and cold fluid
-
Effect of hot fluid inlet temperature (Tho) vs Pressure drop (Air side and Tube side)
Figure [9] depicts the pressure drop as a function of hot fluid input temperature at various hot fluidand cold fluid flow rates. With an increase in the temperature of the hot fluid inlet, there is a minimal fluctuation in pressure drop on the tube side. As a result, for a given set of operating parameters, a mean value for the tube side pressure drop can be
.
employed within the range of hot fluid inlet temperature. It can be seen from equation [30] that the air side pressure drop varies depending from the mass velocity, density of air at the exit, and friction factor. The graph depicts the interrelationship between the terms
Fig. 9. Variation of pressure drop with hot fluid
inlet temperature at various flow rates of hot fluid and cold fluid
-
-
-
CONCLUSIONS
A theoretical model was developed as shown in the section 3. Calculations were done on the basis of experimental matrix and relevant graphs were plotted to show the effect of various conditions on the heat exchanger. The present study focused on theoretical analysis of anautomotive radiator as a plate fin heat exchanger. For the design and analysis of an automobile under typical working conditions, an analytical model was created. The impact of hot, cold, and intake hot fluid temperatures on performance measures such overall heat transfer coefficient, overall efficiency, and pressure was studied theoretically. An overview of theoretical analysis based on the current study is presented here.
-
The overall heat transfer coefficient has minimal dependence on the inlet hot fluid temperaturefor a given set of other operating parameters and hence a mean value can be used within a range of coolant temperature inlet conditions for a given set of operating parameters with acceptable accuracy, saving costs and time.
-
The overall heat transfer coefficient of the automotive radiator was over 25 W/m2K for each of the operating conditions and can be increased up to 152 W/m2K with maximum hot fluid flow rate (Re(h) = 100), minimum hot fluid inlet temperature (40oC) and maximum cold fluidflow rate (Re (c)=300000).
-
The overall efficiency of the heat exchanger was over 39% for each of the conditions and canbe increased up to 94% with decreasing cold fluid flow rate up to Re of 30000 and inlet temperature of 40°C.
-
The pressure drop across the tube side is independent of the cold fluid flow rates. The pressuredrop across tube side was over 47 Pa and can be increased up to 4300 Pa with minimum hot fluid flow rate (Re(h) = 100), minimum hot fluid inlet temperature (40oC) and maximum coldfluid flow rate (Re (c)=300000).
-
The pressure drop across the air side was over 86 Pa and can be increased up to 5500 Pa withminimum hot fluid flow rate (Re(h) = 100), minimum hot fluid inlet temperature (40oC) and maximum cold fluid flow rate (Re (c)=300000).
REFERENCES
Bozorgan, N., Krishnakumar, K., and Bozorgan, N., Numerical Study on Application of CuO- Water Nanofluid in Automotive Diesel Engine Radiator, Modern Mechanical Eng., vol. 02, pp.130136, 2012.
Charyulu, D. G., Singh, G., and Sharma, J. K., Performance evaluation of a radiator in a dieselengine – case study, Appl. Therm. Eng., vol. 19, pp. 625639, 1999.
Chen, J. A., Wang, D. F., and Zheng, L. Z., Experimental study of operating performance of a tube-and-fin radiator for vehicles, Proceedings of the Institution of Mechanical Engineers, Part D: J. Automobile Eng., vol. 215, pp. 911918, 2001.
Elias, M. M., Mahbubul, I.M., Saidur, R., Sohel, M.R., Shahrul, I.M., Khaleduzzaman, S.S., andSadeghipour, S., Experimental investigation on the thermo-physical properties of Al2O3 nanoparticles suspended in car radiator coolant, Int. Comm. Heat Mass Trans., vol. 54, pp. 48 53, 2014. Gollin, M., and Bjork, D., SAE TECHNICAL: Comparative Performance of Ethylene Glycol/Water and Propylene Glycol/Water Coolants in Automobile Radiators, 2018.
Heywood, J.B., Internal Combustion Engine Fundamentals, USA: TATA McGraw Hill, pp. 668-701, 1988.
Hussein, A. M., Bakar, R. A., Kadirgama, K., and Sharma, K. V., Heat transfer enhancementusing nanofluids in an automotive cooling system, Int. Comm. Heat Mass Trans., vol. 53, pp.195202, 2014.
Kakac, S., Liu, H., Pramuanjaroenkij, A., Heat Exchangers Selection, Rating and ThermalDesign, Boca Raton: CRC Press, pp. 427-449, 2012. Leong, K. Y., Saidur, R., Kazi, S. N., and Mamun, A. H., Performance investigation of an automotive car radiator operated with nanofluid-based coolants (nanofluid as a coolant in aradiator), App. Therm. Eng., vol. 30,
pp. 26852692, 2010.
Lin, C., Saunders, J., and Watkins, S, The effect of changes in ambient and coolant radiator inlettemperatures and coolant flowrate on specific dissipation, SAE Technical Papers, 2000.
Nieh, H. M., Teng, T. P., and Yu, C. C, Enhanced heat dissipation of a radiator using oxidenano-coolant, Int. J. Therm. Sci., vol. 77, pp. 252261, 2014.
Oliet, C., Oliva, A., Castro, J., and Pérez-Segarra, C. D, Parametric studies on automotiveradiators, App. Therm. Eng., vol. 27, pp. 2033 2043, 2007.
Oliet, C., Pérez-Segarra, C. D., and Oliva, A, Thermal and fluid dynamic simulation of automotive fin-and-tube heat exchangers, part 2: Experimental comparison, Heat Trans. Eng.,vol. 29, pp. 495502, 2008.
Pérez-Segarra, C. D., Oliet, C., and Oliva, A, Thermal and fluid dynamic simulation of automotive fin-and-tube heat exchangers, part 1: Mathematical model, Heat Trans. Eng., vol. 29,pp. 484494, 2008.
Peyghambarzadeh, S. M., Hashemabadi, S. H., Hoseini, S. M., and Seifi Jamnani, M. Experimental study of heat transfer enhancement using water/ethylene glycol based nanofluidsas a new coolant for car radiators, Int. Comm. Heat Mass Trans., vol. 38, pp. 12831290, 2011. Peyghambarzadeh, S. M., Hashemabadi, S. H., Naraki, M., and 2015.
Vermahmoudi, Y. Experimental study of overall heat transfer coefficient in the application of dilute nanofluids in the car radiator,App. Therm. Eng., vol. 52, pp. 816, 2013.
Sheikhzadeh, G., Analysis of Thermal Performance of a Car Radiator Employing Nanofluid. Int.
J. Mech. Eng. App., vol. 2, 47, 2014.
Stone, R., Introduction to Internal Combustion Engines, London: The Macmillan Press, pp. 430,1992.
Yadav, J. P., and Singh, B. R, Study on Performance Evaluation of Automotive Radiator,
SAMRIDDHI: A J. Phys. Sci. Eng.Tech., vol. 2, pp. 4756,