
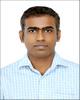
- Open Access
- Authors : Niran I R
- Paper ID : IJERTV11IS080035
- Volume & Issue : Volume 11, Issue 08 (August 2022)
- Published (First Online): 13-08-2022
- ISSN (Online) : 2278-0181
- Publisher Name : IJERT
- License:
This work is licensed under a Creative Commons Attribution 4.0 International License
Thermal Analysis of A Single Point Cutting Tool using Finite Element Method
Niran I R
Thermal Engineering (Mechanical Engineering) Toc H Institute of Science and Technology Ernakulam, India
Abstract Machining is one of the most significant and most normal assembling processes in the metal handling industry. In machining activities, mechanical work is changed over completely to warm through the plastic misshaping associated with chip arrangement and through contact between the apparatus and work piece. A portion of this intensity conducts into cutting device, bringing about high instrument temperatures close to front line. The temperature of the device assumes a significant part in the warm mutilation and the machined part's layered precision, as well as in the apparatus life in machining. Assurance of the most extreme temperature and temperature dissemination along the rake face of the cutting device is a central significance since it effects on apparatus life as well as the nature of the machined parts. The present work likewise includes the investigation of disfigurement and warm examination of single point cutting apparatus in turning utilizing Finite Element Method (FEM).
KeywordsTenperature sensor, Ansys, Thermocouple
I INTRODUCTION
Over the historical backdrop of machining, rules and shows have emerged in light of observational data of compromises between cutting pace and device substitution time. Machining is a term covering a huge assortment of assembling processes intended to eliminate material from a work piece. Machining is one of the most significant and most normal assembling processes in the metal handling industry. Metal cutting, ordinarily called machining, is the expulsion of the undesirable metal from a work piece as chips to get a completed result of wanted shape, size and finish. In machining activities, mechanical work is switched over completely to warm through the plastic disfigurement engaged with chip development and through contact between the apparatus and work
Please do not revise any of the current designations. Machining, the most boundless cycle for molding metal, has turned into an extremely huge part of current culture and industry. The significance of the machining system is apparent by the perception that essentially every gadget involved by humankind in everyday life has no less than one machined part or surface. From a materials perspective, fast machining is a relative term, since various materials ought to be machined with various slicing velocities to safeguard satisfactory instrument life. Due to this distinction and the way that cutting rate decides if a material will frame constant or sectioned chips, one method for characterizing rapid machining is to relate it to the chip development system. Machining is a typical manufacture procedure where material eliminated from a section utilizing an instrument with a little,
hard tip. Generally, the material being cut is a metal, like aluminum or steel. To create a section rapidly, a high cutting velocity wanted. These higher paces, notwithstanding, lead to a quicker debasement of the device tip, which expects that the instrument tip supplanted all the more habitually.
II LITERATURE REVIEW
. Harshit Katheriya et al [2019], Temperature at apparatus chip connection point of one reason shaper is set, produced in various speed machining activities. In particular, 3 totally unique Associate in examinations are correlation with a trial mensuration of temperature during a machining technique at slow speed, medium speed and at fast. Moreover, three examinations are finished of a High-Speed Steel and of a Carbide Tip Tool machining process at three different cutting paces, to contrast with exploratory outcomes delivered as a feature of this review. An examination of nuclear power age in shaper is performed by shifted cutting boundaries at the adequate shaper unadulterated arithmetic. The trial results uncover that the most factors to fault for expanding cutting temperature are cutting pace (v) and profundity of cut (d) severally
Amber Batwara [2018] Leftover burdens produced in device assume a vital part during machining process. The useful way of behaving of hardware can be improved or impacted by remaining burdens. To understanding the remaining pressure bestowed by machining is a significant part of the general nature of the part. The fundamental goals of this paper is foster a mathematical way to deal with foresee the close to surface lingering stresses in cutting device and work piece coming about because of turning of AISI 1006 and approve the model with ANN. The FEM Explicit elements is utilized for computing the lingering pressure progressively climate. All out L16 tests were planned by Taguchi strategy. Three information factors (profundity of cut, cutting pace and rack point) and two reactions (anxiety) chose for reenactment work. Advancements of cycle boundaries were finished utilizing plan of investigations (DOE) and examination of change (ANOVA) for some subjective result. In this study model conditions are likewise produced for additional examination utilizing straight relapse displaying strategy utilizing Minitab programming. A counterfeit brain network model is utilizing for the examination and expectation the reactions. Based on recreation work device wear is subject to rack point.
Sahu et aI (2018) have explained the field of production specifically in machining process cutting tool plays a very significant role. It not facilitates cutting task but also helps in
acquiring perfect surface finish along with certain acceptable range of accuracy. To accomplish these, the tool has to be strong enough so that it can bear various continuous as well as repeatable load and it should have to wear resistant. In this paper a single point cutting tool has been examined with the help of finite element tool.
Exp No |
Speed(V) RPM |
Depth of cut (d) mm |
Experimental Temperature |
1 |
540 |
0.5 |
128.65 |
2 |
540 |
1 |
145 |
3 |
540 |
1.5 |
152.2 |
4 |
540 |
2 |
163 |
5 |
750 |
0.5 |
144.52 |
6 |
750 |
1 |
156.72 |
7 |
750 |
1.5 |
164.2 |
8 |
750 |
2 |
176 |
9 |
940 |
0.5 |
151.26 |
10 |
940 |
1 |
163.68 |
11 |
940 |
1.5 |
177.36 [1 |
12 |
940 |
2 |
193.48 |
EXPERIMENTAL RESULT
] [1]
IV RESULT AND DISCUSSIONS
Geometry
Meshing
Exp no |
Speed |
Depth |
Temperature |
FEA Temperature |
Percentage difference |
1 |
540 |
0.5 |
128.65 |
131.72 |
2.33 |
2 |
540 |
1 |
145 |
148.05 |
2.06 |
3 |
540 |
1.5 |
152.2 |
155.21 |
1.93 |
4 |
540 |
2 |
163 |
165.94 |
1.77 |
5 |
750 |
0.5 |
144.52 |
147.58 |
2.07 |
6 |
750 |
1 |
156.72 |
159.7 |
1.87 |
7 |
750 |
1.5 |
164.2 |
167.13 |
1.75 |
8 |
750 |
2 |
176 |
178.84 |
1.59 |
9 |
940 |
0.5 |
151.26 |
154.28 |
1.95 |
10 |
940 |
1 |
163.68 |
166.61 |
1.76 |
11 |
940 |
1.5 |
177.36 |
180.19 |
1.57 |
12 |
940 |
2 |
193.48 |
196.2 |
1.38 |
CONCLUSION
Thought about the outcomes acquired from explore and limited component investigation, the outcomes were approved. The distinction in the temperature got for hss device.
HSS TOOL – 1.83
In both examination and limited component investigation, the temperature shaped during machining is more in C20 Tungsten carbide device than hss apparatus. So the opportunities for device wear or apparatus disappointment is more in carbide apparatus than in hss apparatus at same cutting circumstances.
REFERENCE
[1] Tugrul ozel, Computational modelling of 3D turning : influence of edge micro-geometry on forces, stresses, friction and tool wear in PcBN tooling, Journal of materials processing Technology 209 (2009) 5167-5177. [2] P.S. Shivakumar Gouda, Srikanth K S, Rajesh Anwal, Rakeshshanthkumar N k, G B Veeresh Kumar, R Pramod, Thermal and Vibrational characteristics of Single Point Cutting Tool on Aluminium and Wrought Carbon Grade B (WCB) Samples, Materials Today: Proceedings 5 (2018) 11423-11429. [3] L.B.Abhang and M.Hameedullah, Chip- Tool interface Temperature Prediction Model for Turning Process, L.B.Abhang et al./International Journal of Engineering Science and Technology Vol.2(4),2010, 382-393. [4] Poonam D. Kurekar , S.D.Khamankar, Finite Element Analysis of Single Point Cutting Tool, International Research Journal Of Engineering And Technology (IJRT).