
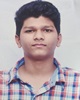
- Open Access
- Authors : Bangaru Bharath Kumar
- Paper ID : IJERTV10IS050301
- Volume & Issue : Volume 10, Issue 05 (May 2021)
- Published (First Online): 01-06-2021
- ISSN (Online) : 2278-0181
- Publisher Name : IJERT
- License:
This work is licensed under a Creative Commons Attribution 4.0 International License
Thermal Analysis of Disc Brake Rotor
Bangaru Bharath Kumar UG, Mechanical Engineering, Vasavi College of Engineering, Hyderabad ,India.
Abstract:- The purpose of this research is to analyze a slotted disc brake, which is commonly used in Motorsport and Luxury Automobiles. Even though, Braking systems in an Automobile has come a long way in the past decades. Basic concept of the braking system has been the same ever since it has been invented. The main purpose of this study is to analysis the thermal behavior of the dry contact of the brake disc during the braking phase. The design of the Disc brake is done in SOLIDWORKS and analysis part of the research is done in ANSYS 2021 R1. This research shows comparison between Brake disc materials namely, Stainless Steel and Cast Iron.
Keywords: Disc brake, Solidworks , ANSYS, Thermal analysis
-
INTRODUCTION:
When a vehicle is in motion, braking system is as important as any other part on the automobile. The Braking in an automobile has undergone huge evolution in the past few decades. From using mechanical scuff brakes to drum brakes, to advanced disc brakes. Braking also plays a major part in Motorsports. It can be a margin between safety of the driver and a mishap. Since, everything is dealt in tenth of a second, braking and cooling of the system must be efficient according to the conditions. This research provides the temperature distribution on a brake disc on different materials.
Nowadays, in the competitive automobile industry, demand for efficient braking system has increased exponentially. The deceleration of the wheel is obtained by the friction between the brake calipers and the disc itself. As the whole system runs on the principles of friction and heat dissipation, the thermal behavior of the disc and the material is important parameter to improve efficiency. When the brake is applied, the pressure is applied on the brake calipers, which in turn apply pressure on the disc itself. This contact between calipers and the disc leads to the buildup of frictional forces, which lead to the retardation of the vehicle. During this process, the kinetic energy of the automobile is converted into heat generated between brake calipers and the brake disc.
-
MATERIALS OF BRAKE ROTOR:
Brake rotor is the most significant part of the automobile of the system in terms of safety and stability of vehicle point of view. Brake rotor material is selected on the basis of various conditions like consistency , friction and wear properties under various loads under velocity, load , environment, temperature and durability. Parameters to be taken into consideration are friction , wear and density. Also, to be taken in thought is the cost of material. The materials considered in this research are
Martensitic Stainless Steel: This type of steel forms a crystalline structure on heat treatment and high corrosion resistance. It contains 11.5% of chromium in its composition. Grade 410 steels are a general purpose Martensitic steels which are used. Taking into account its cost, ease for manufacture, thermal stability it is mostly used in two wheelers.
Cast Iron: This type of metallic carbon usually contains 2 – 4.5% of carbon in its matrix. This also called as Gray Cast Iron. It has good characteristics like vibration damping, wear resistance and cracking. These characteristics make this material a good choice for brake rotors in 4 wheelers. The properties of the materials are given in the tabular column below.
MATERIAL PROPERTIES
GRAY CAST IRON
STAINLESS STEEL
DENSITY (kg/m3)
7200
7750
POISSONS RATIO
0.25
0.31
YOUNGS MODULUS(GPa)
125
193
THERMAL CONDUCTIVITY(W/m-K)
54.5
23
SPECIFIC HEAT(J/kg-K)
586
753
COEFFICIENT OF FRICTION
0.25
0.4
-
CALCULATIONS OF INPUT PARAMETERS:
In order to prevent a collision between vehicles, braking performance is given utmost importance. The rotor model heat flux is calculated for the car moving with a velocity 55.55m/s (200kmph) and the following is the calculation procedure.
DATA:
-
Mass of the vehicle = 1500 kg
-
Initial velocity (u) = 55.55 m/s (200 kmph)
-
Final velocity after application of braking (v) = 0 m/s
-
Brake rotor diameter = 0.288 m
-
Axle weight distribution ()=0.42
-
Percentage of kinetic energy that disc absorbs (92%) k=0.92
-
acceleration due to gravity g =9.81m/s2
-
coefficient of friction for dry pavement µ=0.7 Kinetic energy is defined by the equation.
-
Energy generated during braking , K.E=1/2*k**(( )2/2) K.E=(0.92*0.5*0.42*1500(55.55)2)/2
K.E=446328.225 joules (2)stopping distance (x)= 2/ 2 X=55.552/(2*0.7*9.81) X=224.683m
-
Deceleration Time , V= U +at T=13 secs
-
Braking Power, (pb)=K.E/t Pb=446328.225/13
Pb=34332.940 watts
-
Heat Flux generated,Q= Pb/A A= Brake Caliper area =0.0066m2
-
(note: Brake Caliper area can assumed according to the Brake rotor and caliper contact patch area) Q=34332.940/0.0066
Q=5201960.606 W/m2 Q=0.61*5201960.606
(Note: The Brake bias for the wheels is 61:39 hence braking efficiency for front wheel as 61%)
Q=3175195.93 W/m2
From the calculations done above, following boundary conditions are set transient state thermal analysis of brake disc.
BRAKING POWER(W)
34332.940
HEAT FLUX(W/m2)
3175195.93
HEAT TRANSFER COEFFICIENT FOR STAINLESS STEEL(W/m2)
28584.46
HEAT TRANSFER COEFFICIENT FOR GRAY CAST IRON(W/m2)
25015.26
AMBIENT TEMPERATURE()
22
-
-
MODELLING OF BRAKE DISC
The models of the rotors are modeled on SOLIDWORKS 2020 SP0 and is imported for transient state analysis on ANSYS 2021 R1. This analysis is done in the time duration of 13 seconds, which is the time required for the vehicle to come to rest from 200Kmph.
-
RESULTS
The end result of the analysis on Stainless Steel rotor disc.
MATERIAL
MAXIMUM TEMPERATURE
MINIMUM TEMPERATURE
STAINLESS STEEL
1723.8
23.2
GRAY CAST IRON
1023.6
10.3
The End result of analysis on Gray Cast Iron Rotor disc.
-
CONCLUSIONS
The Brake disc rotor was analysed for thermal spikes using analytical calculations and finite element analysis. The procedure for a step-by-step analysis has been developed for anybody to follow. For the same heat flux, heat generated by Gray Cast Iron is lower than that of Stainless Steel. This study provides a useful design tool for the improvement of braking performance. According to the results, Gray Cast Iron is more suitable for disc rotors. But, Gray Cast Iron easily gets corroded in wet weather or moist conditions. So, in terms of road going automobiles, Stainless Steel can be used.
-
REFERENCES
-
Sumeet Satope, Akshayumar Bote, Thermal analysis of disc brake, International Journal for Innovative Research in Science & Technology,Volume 3, Issue 12, May 2017.
-
Manjunath T V, Structural and thermal analysis of rotor disc of disc brake, International Journal of Innovative Research in Science, Engineering and Technology, Vol. 2, Issue 12, December 2013.
-
Bansal D Simaria, Himanshu P Ravaliya. , Jigar H Chaudary , Sagar P Parmar , Prawin P Parate, Structural analysis of rotor disc of disc brake, International Journal of Advance Research in Science and Engineering, Vol. 6, Special Edition no.4 , December 2017.
-
Rakesh Jaiswal, Anupam Raj Jha, Ankush Karki, Debayan Das, Pawan Jaiswal, Saurav Rajgadia, and Ankit Basnet, Structural and thermal analysis of disc brake using solidworks and ansys , International Journal Of Mechanical Engineering and Technology,Volume 7, Issue 1, Jan- Feb 2016.
-
Swapnil R. Abhang, D.P Bhaskar, Design analysis of disc brake, International journal of engineering trends and technology (IJETT), Volume 8, Number 4, Feb 2014.