
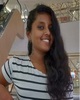
- Open Access
- Authors : G. Pratyusha , R. Sabari Vihar , Dr. D. Govardan
- Paper ID : IJERTV10IS050491
- Volume & Issue : Volume 10, Issue 05 (May 2021)
- Published (First Online): 07-06-2021
- ISSN (Online) : 2278-0181
- Publisher Name : IJERT
- License:
This work is licensed under a Creative Commons Attribution 4.0 International License
Thermal Analysis of Heat Treatment for AMS-4078/7075-T75 Aluminium Alloy
G. Pratyusha1, R. Sabari Vihar2, D. Govardhan5
Research student1, Assistant professor2, Head of the department3,
Department ofAeronautical Engineering, Institute of Aeronautical Engineering, Telangana, India.
Abstract: Aluminium alloys are lightweight materials and have high strength ratio. AMS 4078/7075-T75 is an aluminium alloy in which zinc is the main alloying agent including small quantities of copper, magnesium and chromium is using. This combination will make wrought aluminium alloy an extremely strong material. The heat treatment for this alloy will make the material to increase the strength and mechanical properties. Thermal analysis of this considered material is carried out at different temperatures during heat treatment process. The result values are noted down and Comparison of the results between analysis in Ansys 19.2 and the results from the performed heat treatment process will be noted.
Keywords: Aluminum alloy, Heat treatment, Analysis, wrought aluminum alloy
-
INTRODUCTION
While comparing to other metals aluminium has less density, its about one-third that of steel. When a aluminium is exposed to air, it forms a protective layer of oxide on the surface due to its high affinity for oxygen. A process for extraction aluminium is developed by Paul Heroult and Charles Martin Hall named Hall-Heroult process, which made aluminium much more accessible to the public, and mass production of aluminium led to its widespread use in industry and everyday life. Aluminium was a critical strategic resource for aviation during World Wars I and II.
The aluminium alloys have the improvised characteristics compared to aluminium metal. They are mainly classified to two categories:
-
Casting Alloys
-
Wrought Alloys
-
-
LITERATURE SURVEY
-
Wrought Aluminium
Wrought aluminium is the most using alloy of aluminium. They are pressure-processed alloys such as rolling, extrusion (pressing), forging, punching.
All wrought aluminium alloys are divided into eight series (groups) based on their alloying system, among them AMS 4078/7075-T75 is a wrought aluminium of 7xxx series. Wrought aluminium has great structural integrity. The properties of wrought aluminium 7xxx series are thermally solidifying and have strengths going from medium to high. Different components, like copper and chromium, are typically included follow sums. Modest quantities of scandium are added to improve their properties. High strength 7xxx series composites have a lower protection from breaking because of erosion under pressure and are often utilized in prosternum to give the best mix of solidarity, consumption
opposition, and crack sturdiness. The wrought aluminium has the high strength to low weight ratio, because of that property it is the most using material in many industries like aerospace, defence, automobile etc.,
-
Heat Treatment
Heat treatment is a process which enriches the characteristics of the material and improvise the microstructure lattice of the alloy. The Heat-treated material can withstand high structural loads such as compressive loads, tensile loads, bending loads, torsional loads etc.,
The progress will proceed through solution treatment, Quenching, Ageing.
Solution treatment process can be done at a certain temperature by dissolving in CuAl2 which is known as solution treatment of aluminium-copper systems.
An aluminium alloy part which is heated in molten salt bath to achieve fast solution heat treatment. Mostly for solution treatment we use alkaline solutions which are maintained at required temperatures.
Quenching is defined as The restricted extraction of heat. Any medium that concentrates heat from the part is alluded to as a quenchant. The quenchant can appear as a fluid, solid or gas. The complete Cycle of Quenching will progress through three stages which follows as Vapour stage, Boiling stage, Convection stage.
Ageing is the cycle by which a supersaturated strong arrangement which leads to improve the strength properties. Ageing can be done in two types based on our requirements named as Natural ageing and Artificial ageing.
Basically, In industries the complete process in which an aluminium alloy can be manufactured as a part follows as each and every material has its own material number and heat number. After receiving the raw material it will be cutted as per the required dimensions and then it will be sent for part production. Passing through many operations over the work centres the part will be finished. Then the part will be inspected and the tolerance will be checked. The part will be hand overed to Deburring in which the sharp edges, modifications are be done so that the part will be finished smoothly. Later it will go through the quality department and there each and every inch will be inspected and checked thoroughly if there are any rejections then it will be send back to the relative department or else it will be send to special processes like heat treatment, Welding etc., where the part will be immersed in alkaline solution for some time and temperature. The part will be placed for quenching and then artificial ageing will be happen. The mechanical properties of the part will be tested in NDT(Non- destructive test).
The components are made out of wrought aluminium alloy of AMS-4078/7075-T75 will undergo for heat treatment. The parts will be heated on furnace of 4660C-4930C for 30-45 mins of time according to specific parts heat number. The heat-treated material will be then sent for quenching process in which the quenchant is in the liquid form. The quenchant used is the composition of Glycol which is 13% and De- mineralized water. By using the cooling fans the heat treated material will be cool down to the temperature of range 320C- 380C. Because of the heat treatment the material may undergo some deformations so it will be checked and then straightening of the part will be done. After the CHS the part will undergoes agening process. According to the parts some will be sent to natural ageing and remaining for artificial ageing. Natural ageing will be done at the room temperature for few days. Artificial ageing will be done at 1500C-1800C for 2- 3 days.
-
-
METHODOLOGY
The components are made out of wrought aluminium alloy of AMS-4078/7075-T75 will undergo for heat treatment. The parts will be heated on furnace of 4660C-4930C for 30-45 mins of time according to specific partss heat number. The heat- treated material will be then sent for quenching process in which the quenchant is in the liquid form. The quenchant used is the composition of Glycol which is 13% and De-mineralised water. By using the cooling fans the heat treated material will be cool down to the temperature of range 320C-380C.Because of the heat treatment the material may undergo some deformations so it will be checked and then straightening of the part will be done. After the CHS the part will undergoes agening process. According to the parts some will be sent to natural agening and remaining for artificial agening. Natural agening will be done at the room temperature for few days.
Artificial agening will be done at 1500C-1800C for 2- 3 days.
-
Design
The Computational analysis begins with designing of a model in fusion 360 software for further thermal analysis of heat treatment of the aluminium alloy. As the part design is confidential, considering a wing model and designing it in fusion 360 software.
Wing of chordlength 15 cm with coordinates were downloaded using airfoiltools.com website. The data file was selected and made into spline sketch using an addon in fusion 360 software.
Figure 1:Sketch is extruded for span
Figure 2:Wing Design for analysis
-
Analysis:
A computational thermal analysis has been done over the wing model at various temperature of the given temperature range. The software used to develop the computational thermal model in this thesis was ANSYS Workbench 19.2 version. In this analysis the quenching of heat treatment has been done for different temperatures of 4240C,5090C and 7500C.The fusion 360 model is converted to igs format so that it can be imported to ansys software. For the quenching process of heat treatment, the transient thermal is used. In engineering data, we should select the aluminium alloy as the part is manufactured by aluminium material. Import the igs file to geometry of the transient thermal. Select the geometry and generate the mesh. Give the initial temperature, convectional coefficient, temperature of the quenching. Solve for the results.
Figure 3:Meshing of the wing model
Figure 4:Thermal analysis at 4240C
Figure 5: Thermal analysis at 5090C
Figure 6:Thermal analysis at 7500C
-
-
OBSERVATIONS
As per the contours produced for the thermal analysis of aluminium alloy at different temperatures for heat treatment, the heat treatment should be carried out at optimal temperature range for improvising the characteristics of the material.
We can observe the contours at the different temperatures of 4240C and 5090C the maximum and minimum points are same for the both temperatures which it is optimal condition.
While the thermal analysis of the aluminium alloy at 7500C the complete body of the wing has the maximum point of heat as we can see in the thermal contours above mentioned in figure 6.
-
SUMMARY
The heat-treated material will be having the improvised characteristics such that it can handle the high structural loads such as compressive loads, bending stress, torsion stress because of micro structure of wrought aluminium alloy will be improvised.
The heat treatment will be done only in the optimal temperature range of 4130C-5940C because beyond that temperature the mechanical properties of the material will be changed so that the part will be deformed. It will lose its natural properties like high strength.
As per the analysis done in the ansys 19.2 version the material properties in the temperature range of optimal conditions which are: 4240C,4940C and 5090C of the aluminium alloy remains same and the results are same. While if the material is heat treated beyond the temperature it will be melted and deformed completely. As the melting point of Aluminium is 660.30C, the heat treatment above that temperature will leads to the distortion of the part and it will be rejected. The heat over the part will be transmitted at maximum value and it will lead to melting of the alloy.
So, the experimental value range of heat treatment process and computational values of the heat treatment process are similar.
-
FUTURE SCOPE
As we know that the aluminium alloy is the most used component in many industries. So for the perfect analysis of the aluminium at heavy loads the heat treatment process is carried in optimal condition. The future scope in this is, the composition of aluminium alloy AMS 4078/7075-T75 can be improvised in such a manner that time taking for the artificial ageing can be reduced by using different methods. The optimal temperature range of heat treatment process can be increased with improvised techniques.
-
REFERENCES
-
J.R. Davis1 et.al, Corrosion of Aluminum and Aluminum Alloys, ASM International, 1999.
-
J.R. Davis1 et.al, ASM Specialty Handbook: Aluminum and Aluminum Alloys , ASM International, 1993.
-
J.R. Davis1 et.al, Aluminum and Aluminum Alloys, in Metals Handbook Desk , 2nd edition, ASM International, 1998, p 417505.
-
D.G. Altenpohl1, Aluminum: Technology, Applications, and Environment, 6th edition, The Aluminum Association Inc. and TMS, 1998.
-
J.E. Hatcp, Aluminum: Properties and Physical Metallurgy, Ed., American Society for Metals, 1984.
-
F Vina1, A.M.P. Pinto2, H.M.C Santos3, A.B Lopes4 et. al. Journel of material processing Technology Vol 92-93 (1999).
-
Bharathesh TP, Ramesh CS, Keshavamurthy R, Verma SM. , 2 Materials Today: Proceedings (4-5), 2015, pp.2005
-
Dieter GE. Mechanical Metallurgy, McGraw Hill Book Company (UK), London, 1988.
-
Jin-feng NIE, Fang WANG, Yu-sheng LI, Yan-fang LIU, Xiang-fa LIU, Yong-hao ZHA.Trans. Nonferrous Met. Soc. China, 27, 2017, pp. 2548.
-
Ezatpour HR, Sajjadi SA, Sabzevar MH, Chaichi A, Ebrahimi GR. Trans. Nonferrous Met. Soc.China, 2017; 27. pp. 1248.
-
Ezatpour HR, Torabi-Parizi M, Sajjadi SA. 23, 2013, pp. Trans. Nonferrous Met. Soc. China,1262.
-
Gregory A.W. Sweet, Amirkhiz BS, Bruce W. Williams, Alan Taylor, Rich L. Hexemer, IanW. Donaldson and Donald PB.Materials Characterization, 151, 2019, pp. 342..cn