
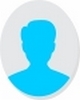
- Open Access
- Authors : Mahesh K , Chandrashekar Vaddatti , Hema Sree Chintada
- Paper ID : IJERTV10IS110162
- Volume & Issue : Volume 10, Issue 11 (November 2021)
- Published (First Online): 04-12-2021
- ISSN (Online) : 2278-0181
- Publisher Name : IJERT
- License:
This work is licensed under a Creative Commons Attribution 4.0 International License
Topology Optimization of an Aero Engine Part
Mahesh K Cyient Ltd, Hyderabad
Chandrashekar Vaddatti Cyient Ltd, Hyderabad
Hema Sree Chintada Cyient Ltd, Hyderabad
Abstract The selection of material and design for the component is a very important topic within the aero engine industry to supply sustainable and competitive products. As efficiency of the system is directly associated with the load of the components in this system, the aero engine parts must be light in weight at the identical time strong enough to face up to the masses meaning that the strength to weight ratio should be high. With the available materials like Titanium and Nickel, geometry optimization methodologies (like topology optimization) is essential to cut back the load of the aero engine part thereby contributing for the reduction of overall weight of the aircraft. Topology optimization method that employs mathematical tools to optimize material distribution in every part to be designed. This research paper focuses on a design approach with a case study on the redesign of aero engine bracket by developing a strategy with regard to topology optimization and comparing analysis results with the baseline. The structural optimization work is done out in commercial software Altair solidThinking (Inspire) and ANSYS. The study results of structural analysis show that topology optimization could be a powerful design technique to scale back the load of a product while maintaining the look requirements.
-
INTRODUCTION
Most of the aero engine companies are working on the technologies which can improve efficiency of the gas turbine engine. The improved efficiency can be achieved either by developing new technology like, GTF technology and by possible weight reduction (in the aerospace industry weight is of great importance to the engineering design) of the legacy engine components and also under development engine components.
The manufacturing lead time for aero engine component is the major emphasis for meeting the incorporation date for gas turbine engines. Twenty first century has seen rapid revolution in terms of improved manufacturing processes in the aerospace industry. The weight reduction of any aircraft/aero engine part increases the fuel efficiency of the engine and reduces the emission. Hence, the main task in the designing aero engine parts is to reduce the weight while maintaining the structural capability and functioning of the part. Though weight optimization has always been the prime consideration while designing the aero engine parts, the techniques used are improving every day. Size optimization focuses on the finding the right size (length, width, height etc.) of any component and shape optimization focuses on finding the optimized shape of the part whereas topology optimization technic focuses on finding the right size and shape of the component. Topology optimization technics use the CAD, FEA concepts and different algorithms to find the optimum size by keeping the loading conditions and boundary conditions constant.
Manufacturing optimized and complex shaped parts was a difficult, time consuming and costly process in the past. With new manufacturing technologies like Additive
Manufacturing becoming more and more practical every day, the manufacturing of complex geometries has become relatively easier. The conventional manufacturing processes have limitations and these must be taken care while designing the parts. The additive manufacturing technology gives more flexibility to the engineers where they can design complex shaped parts without considering the limitations that are to be addressed in case of conventional manufacturing processes. With the new manufacturing machines allowing the use of metal powders in additive manufacturing, metal parts with complex geometries can be manufactured. Conventional process of casting followed by machining needs the part to be designed to avoid any kind of casting defects like cracks, pores, discontinuities etc. Then the critical features need to identified and machined in order to obtain good surface finish adding to the cost of the part.
-
TOPOLOGY OPTIMIZATION OF A STRUCTURE Optimization is nothing but selecting the best possible option out of few options that are practically feasible. The decision of selecting the best option depends on the values that are defined by design data. These values are called target functions. There may be multiple target functions. For example, the aircraft engines design requires that maximum reliability, minimum materials consumption and maximum payload volume (or load-lifting capacity) be provided simultaneously.
Topology and shape optimization technics are very useful in the early stage of development of any aero engine part as it reduces the number of iterations and ultimately reduces the time-to-market and cost of the part. The parameters like thickness and radius are reduced by applying shape optimization on a structure.
-
Formulation of topology and shape optimization problem The structural optimization problem can be formulated by using an objective function, design variables and state variables. The objective function (g) represents an objective that could either be minimized or maximized. Object function should have associated with design domain and the state variables. Design variable (y) describes the design of the structure, it may represent the geometry. The state variable (z) describes the structural response, which can be an example as stress, strain or displacement. Furthermore, a state variable depends on design variables z(y).
minimization of y g(y,z(y))
(1)
A state function h(z) represents the state variable that can be introduced. For example, displacement in a particular direction. For a finite element problem, nodal displacements are solved for:
(2)
Where K is the global stiffness matrix, g is the global load vector. Therefore, the optimization problem can be expressed in a nested formulation where equilibrium constraints are taken care of by the state function formulation.
minimization of y g(y)
Subject to h(u(y)) 0 (3)
The Equation is solved by evaluating derivatives of g and h with respect to y. In Topology Optimization (TO) problems, the design variable y represents the connectivity of the domain. It involves features such as the number and sizes of holes in the design domain. In TO, we need an optimal placement of material points where the reference domain is portioned into voids and solid elements by finite element discretization. In mathematical, , where is an available design domain. The design variable y is now represented by the density vector containing elemental densities , the local stiffness tensor E can by formulated by incorporating as an integer formulation.
Another possibility is to minimize the volume:
(8)
Where is the initial volume. Two common solution methods to solve the topology optimization problem are Optimality criteria method and Method of moving asymptotes.
-
Redesign of aero engine bracket using structural optimization (Case Study)
In this paper, an aero engine bracket is considered as subject for optimizing the weight by meeting all the design and structural requirements of the part. The component is redesigned using topology optimization keeping the loading and boundary conditions same. Altair solidThinking (inspire) commercial software was used in this study. The initial geometry of the bracket is shown in Figure 1. The material Properties of Titanium are considered in this study as this is an aero engine bracket,material properties are listed in Table 1.
And a volume constraint,
(4)
(5)
V is the volume of the initial design. When = 1 we consider an element to be filled whereas an element with = 0 is considered to be a void element. To use gradient- based solution strategy, integer problem need to be formulated as a continuous function. The most common method to relax the integer problem is SIMP (Solid Isotropic Material with Penalization).
Therefore, , ,
Where p is a penalizing factor that penalizes elements with intermediate densities to approach 0 or is the lower density value limit to avoid singularities. Form literature, for = 0.3, it is recommended to use p 3.
The optimization problem can be rewritten as, minimization of y g() (6)
Two common objectives of an optimization problem are to minimize compliance and volume. The compliance is the equivalent strain energy of the FE solution which yields higher stiffness when minimized. Compliance is defined as:
Figure 1: Baseline geometry of the bracket
The strength, deformation, modal analysis results and life of the component are used for determining the design of any component. In this study, the scope is limited to static analysis. Kinematic couplings are used between bolt holes with reference point in order to simulate bolts and at the clevis location in order to apply the load, refer Figure 2. Bolt holes are constrained in all DOF as shown in Figure 3. Equal loading of 8000 lbf is applied in all three directions, global X, global Y and global Z as shown in Figure 4.
Table 1: Material properties of Titanium
Property
Value
Young's modulus
16500 ksi
Poisson's ratio
0.342
Density
0.16
Tensile strength, Ultimate
138 ksi
Tensile Strength, Yield
128 ksi
Property
Value
Young's modulus
16500 ksi
Poisson's ratio
0.342
Density
0.16
Tensile strength, Ultimate
138 ksi
Tensile Strength, Yield
128 ksi
(7)
K() u = f
is the elemental stiffness matrix with the initial stiffness tensor . To prevent the optimized structure from ending up with the full design volume as a result when searching for its maximum structural stiffness, we need to impose a volume constraint.
Figure 2: Boundary Conditions 1
Figure 3: Boundary Conditions 2
The analysis results of the baseline model are shown in Figure 5. Maximum principal stresses in all 3 loading conditions are at observed at the bolt holes, highest stress concentration is observed at the clevis bolt hole location. The stress at clevis bolt hole location is 40.31 ksi and the yield strength of the material is 128 ksi, so there is a factor of safety of 3.17. This high-stress concentration will initiate the crack which is prone to have fatigue failure. The blue area shown in Figure 5 is low stress area. The low stress is where the insufficient usage of material exist and there is scope for optimization in this area.
Figure 4: Loading Conditions
Figure 5: Stress Plots for baseline geometry
The first step in topology optimization is to divide the part into design space and non-design space. Design space is where there is scope for removal of material and optimization. As our recommendation is to use additive manufacturing for manufacturing the redesigned part, there is flexibility to redesign the part without considering the limitations of conventional manufacturing processes. In this case, the bolt holes and the area close to the bolt holes is non- design space as there is no scope for optimization. All the remaining area in the part is design space. Based on the stress and deformation calculated by the topology optimization tool, the areas that are not contributing for the strength of the part are removed and an optimized geometry is created. Figure 6 shows the optimized geometry of the bracket.
The next step is to create the FE model and carry out analysis to find out whether the redesigned part meets the design requirements are not. The same loading and boundary conditions are used for analyzing the optimized geometry and FE analysis is carried out. Analysis results are shown in Figure 7. The maximum stress concentration is observed at the connecting geometry between the base bolt holes and the clevis bolt holes. The maximum stress at that location is
116.8 ksi and the yield strength of the material is 128 ksi, so there is still a factor of safety of 1. The new design shape dimensions derived from topology optimization are approximate. Therefore, local shape improvements are still necessary.
Figure 6: Optimized Geometry
Figure 7: Stress plots for Optimized geometry
-
-
CONCLUSION
The aerospace industry is one of the most competitive industry as fuel savings, noise and emission reduction are the integral parameters to be considered along with basic design requirements. Aerospace industry is quickly adapting to the game changing technologies like advanced materials, advanced manufacturing technics, AR/VR solutions, Industry
4.0 standards etc. This research shows that the topology optimization technics can be very beneficial in the early phase of the product development cycle where preliminary designs are being made. During preliminary design, multiple iterations are made to arrive at the optimum geometry. By using topology optimization technics, the number of iterations can
be reduced thereby reducing the overall cost of the part. This paper has given an insight on the significance of topology optimization in weight reduction which is an integral part of design of aero engine components. This study also elaborates the software used (Inspire) for optimization and suitability of the products for additive manufacturing process with a case study. The weight of the part is reduced by 70% (6.8 lbs to 2.0 lbs) whereas the maximum principal stresses are kept within the yield strength of the material.
REFERENCES
-
Bendsoe, M.P. and Kikuchi, N., Generating Optimal Topologies in Structural Design Using a Homogenization Method, Computer Methods in Applied Mechanics and Engineering 71(2):197-224, 1988.
-
Hailu, S.G., Dereje Engida, W., and Fakhruldin Mohd, H., A Comparative Study on Stress and Compliance Based Structural Topology Optimization, IOP Conference Series: Materials Science and Engineering 241(1):012003, 2017, IOP Publishing.
-
http://asm.matweb.com/search/SpecificMaterial.asp?bassnum=mtp641
-
https://www.aggressivehydraulics.com/parts/clevis-bracket-double- lugs/
-
Patel, N.M., Tillotson, D., Renaud, J.E., Tovar, A. et al., Comparative Study of Topology Optimization Techniques, AIAA Journal 46(8):1963-1975, 2008.
-
Yang, R.J. and Chuang, C.H., Optimal Topology Design Using Linear Programming, Computers & Structures 52(2):265-275, 1994.