
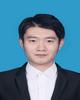
- Open Access
- Authors : Zhu Qiang , Tie-Gang Wang
- Paper ID : IJERTV9IS120114
- Volume & Issue : Volume 09, Issue 12 (December 2020)
- Published (First Online): 17-12-2020
- ISSN (Online) : 2278-0181
- Publisher Name : IJERT
- License:
This work is licensed under a Creative Commons Attribution 4.0 International License
Toughening Mechanism of the Metal Nitride Coating
Zhu Qiang1, Tie-Gang Wang1*
1Tianjin Key Laboratory of High Speed Cutting and Precision Manufacturing,
Tianjin University of Technology and Education Tianjin, China
AbstractThe coating with high hardness can effectively improve the wear resistance of cutting tools and greatly improve the service life and processing efficiency of cutting tools. In order to improve the service life of the coating, toughening treatment is needed,The results show that the amorphous nanocomposite structure can increase the number of two -phase interfaces in the coating, which is helpful to improve the toughness of the coating. The multilayer structure can inhibit the grain growth and increase the interface of the coating, and increase the resistance of dislocation movement, which is helpful to improve the toughness of the coating. The introduction of "disordered" alloy coating by chemical method, The toughness and Tribology of the coating have been greatly improved with the high entropy effect, lattice distortion effect, hysteresis diffusion effect and "cocktail" effect. The stress distribution of the coating can be improved by adjusting the composition of the coating.
Key wordsMetal nitride coating; toughening; nanocomposite structure; multilayer structure; high entropy alloy coating; gradient structure
I INTRODUCTION
Nowadays, with the rapid development of science and technology, the vigorous promotion of economic globalization, people gradually focus on the mechanical manufacturing technology, cutting tools as the "teeth" of machine tools, its status is self-evident. At present, China is vigorously developing the advanced fields such as aerospace, nuclear power, shipbuilding, etc., and the demand for a large number of difficult to machine materials such as superalloy, cemented carbide, titanium alloy and so on is increasing rapidly, which puts forward higher requirements for the mechanical, friction and cutting performance of coated tools. However, a hard coating with high wear resistance can effectively improve the cutting efficiency and quality of cutting tools[1,
2]
At present, a variety of hard coatings emerge as the times require, and most of them are composed of covalent bond elements or compounds composed of carbon, nitrogen, boron, etc. to greatly improve the hardness of the tool and then improve the wear resistance of the tool.As we all know, the higher the hardness of the coating, the greater the brittleness. When facing the external impact, cracks are easy to appear inside the coating, which reduces the tool life of the coating, and the performance of the surface coating can not be brought into full play. Therefore, it is imperative to toughen the coating. Among them, toughness is the ability of material to absorb plastic deformation work and fracture work, and the plastic deformation work is the energy consumed in the process of plastic flow; The fracture work is mainly the energy consumed by the surface energy needed to form a new surface energy. Through a large number of experiments, related researchers have made great progress in the field of coating toughening. This paper mainly introduces four common toughening technologies of metal nitride coating.
II DISCUSS
-
Toughening of Nanocomposite Structure
The introduction of hard nano phase into ceramic materials can greatly improve the strength and toughness of materials. This is due to the small size of nanocrystals, which helps to increase the number of grain boundaries in the material. This concept can be extended to coating preparation technology to deposit amorphous phase coated nanocrystalline nanocomposites. Wang et al .[3] prepared Al-Cr-Si-N coatings by high power pulsed magnetron sputtering, the microstructure of the coating is uniform and compact. The prepared Al-Cr-Si-N coating has higher hardness (19.4Gpa) and adhesion strength (77N), and the prepared coating H3/E*2 is higher, which indicates that the toughness of the coating is improved. This is attributed to the formation of nanocrystalline (Al, Cr) N embedded in the amorphous Si3N4 nanocomposite structure. The specific toughening mechanism is that dislocation can not be formed in the fine nanocrystals, the thin amorphous layer between grains can effectively block the grain boundary sliding, and a large number of two-phase interfaces increase the resistance of microcrack propagation. Zhang Jiaojiao et al. [4] prepared Zr-B-N coatings by high power pulse and DC composite magnetron sputtering. From the cross-section TEM, it can be seen that in the Zr-B-N coating, there are amorphous BN encapsulated in ZrB2, ZrN and other nanocrystals. The highest hardness and adhesion strength of the coating are 36.76Gpa and 43.85N, respectively. The wear marks of the coating are smooth and the wear resistance and toughness are excellent.
-
Toughening of multilayer structure
Fig. 1 TEM of cross section of Zr-B-N film [4]
Because the multilayer composite film can concentrate the excellent characteristics of each material, give full play to the synergistic effect, so as to improve the toughness and hardness, improve the friction performance and high temperature oxidation resistance, and meet the high-efficiency processing of modern difficult to machine materials. In recent years, research has been gradually warming up. On the one hand, in the process of depositing multilayer structure coating, the working target is opened alternately, which helps to reduce the temperature of the molten pool on the target surface, and thus helps to improve the compactness of the coating; On the other hand, alternate growth between the inner layers of the coating can effectively inhibit the grain growth of the coating, which is helpful to improve the hardness of the coating, which is in accordance with the hall page principle. In addition, the multilayer structure can effectively inhibit the growth of particles in the coating, inhibit the diffusion of cracks in the coating during processing, so as to effectively improve the toughness of the coating. Zhang Wenyong et al. [6] used magnetron sputtering technology to prepare CrAlN/ZrN multilayer coatings by changing the modulation period. The results show that, when the modulation period is reduced to 8nm, the hardness and adhesion strength of the coating are 20.4Gpa and 18N respectively, and the toughness coefficient (CPR) of the coating is the largest, which indicates that the toughness of the coating is the best. However, the mechanical properties of the coating decreases when the modulation period is further reduced. The reason is that the thickness of the single layer is too thin to inhibit the grain growth, the crystallinity of the coating is too low and the amorphous is too much, which leads to the obvious degradation of the coating performance. Fandi et al. [7] prepared WB2/CrN multilayer coating on the surface of silicon and stainless steel by DC magnetron sputtering. The structure of the prepared coating is uniform and dense. Since the target works independently, co-sputtering is avoided. The layered structure of the coating is obvious. The specific cross-section appearance is shown in Fig. 2. The hardness of the coating is relatively high, with the highest value of 2930HV, which is due to the crack deflection at the interface of the multilayer film when subjected to external load, resulting in a shallow indentation depth. The adhesion strength of the coating is high, with the highest value of 32.5N.
Fig. 2 cross section morphology of WB2/CrN multilayer coating [7]
-
Toughening of high entopy alloy coating
Ye Junwei et al. [8] got rid of the traditional alloy preparation concept and creatively prepared high entropy alloy with a variety of alloy elements as components. It is a kind of alloy formed by introducing chemical disorder, and its performance test results show that it is obviously higher than that of traditional alloy. The enhancement mechanism includes high entropy effect in thermodynamics, lattice distortion effect in structure, hysteresis diffusion effect in dynamics and cocktail effect in performance. However, the preparation of high entropy alloy is very expensive. Researchers proposed to prepare high entropy alloy coating on
the surface of application equipment to improve the performance and reduce the cost. Chia Han Lai et al. [9] prepared multi- element (AlCrTaTiZr)N high entropy alloy coatings by reactive radio frequency magnetron sputtering. The analysis of the test results shows that the hardness and elastic modulus of the coatings are 36 Gpa and 360 Gpa respectively, when the bias voltage is
-150V, the toughness of high entropy alloy coating is the highest, with the least indentation crack and the highest H/E value, which is attributed to the substitution doping of various alloy elements and solution strengthening effect.
-
Gradient structure toughening
Gradient structure is a kind of high performance coating whose composition or structure changes continuously or step by step with space and gradient coating is usually prepared by controlling the process parameters to obtain the ideal coating with gradual composition and structure from substrate to coating surface. Gradient coating can generally eliminate the macro interface, reduce stress concentration, and improve the bonding strength and toughness of the coating. Wang Peng et al. [10] prepared TiAlSiN gradient coatings with different Si gradient structures by multi arc ion plating and the experimental results show that TiAlSiN gradient coating is composed of (Ti, Al)N and AlN phases. The microstructure of the coating is gradient distribution, showing excellent cutting performance. Its gradient structure is shown in Fig. 3.
Fig. 3 structural design of TiAlSiN coating with gradient change [10]
III SUMMARY
In this work, the toughening technology of coatings in recent years and the toughening effect of coatings obtained by various researchers through corresponding technologies are compared. At present, nanocomposite structure coating, multi-layer composite coating, high entropy alloy coating and different gradient structure coating have been vigorously promoted. As a new coating system, its function design and process optimization have great room for improvement. With the continuous scientific research, the coating system with lower cost and better performance will be developed in the near future.
REFERENCES
-
Qixun Yu, Jingying Zhang. Development and application of tool coating technology[J]. Aviation manufacturing technology, 2007(07):36-39.
-
Luo Yucheng. The Development of Tool Coating Technology[J]. CEMENTED CARBIDE (4):252-257.
-
Wang Tiegangl, Li Baisong, Zhang Jiaojiaol. Influence of Deposition Temperature on Microstructures and Mechanical Properties of the Al-Cr-Si-N Coatings Deposited by HiPIMS Technique[J]. RARE METAL MATERIALS AND ENGINEERING, 2018, 47(08):308-314.
-
Zhang Jiaojiao, Wang Tiegang, Yan Bing. Synthesis and Troblogical Properties of Zr-B-N Coatings by High Power Impulse and Pulsed DC Magnetron Sputtering[J]. CHINESE JOURNAL OF VACUUM SCIENCE AND TECHNOLOGY, 2018, 038(006):479-486.
-
J. LLin, JJ. Moore,J. Wang,W.D. Sproul, Thin Solid Films 517(2011)2402-2408. YJ.Kim, TJ.Byun, J.G.Han, Surf.Coat.Technol.203(2008)790-793.
-
ZHANG Wen-yong, SUN De-en, PEI Chen-rui. Effect of Modulation Period on Toughness of CrAlN/ZrN Nano-multilayer Films[J].SURFACE TECHNOLOGY2016, 45(01):55-61.
-
FAN Di, LEI Hao, GUO Chao-qian, GONG Jun. Effects of Modulation Period on Mechanical Properties of Magnetron Sputtered WB2/CrN Multilayer Films[J].SURFACE TECHNOLOGY, 2017(6).
-
GAO Jia-cheng, L I Rui. The development of studies in high-entropy alloy [J].Functional materials, 2007, 39 (7): 1059-1061.
-
Lai C H , Lin S J , Yeh J W , et al. Effect of substrate bias on the structure and properties of multi-element (AlCrTaTiZr)N coatings[J]. Journal of Physics D Applied Physics, 2006, 39(21):4628.
-
WANG Peng, Xu Changqing, CAI Fei. Preparation and Cutting Performance of Multi-arc Ion Plating TiAlSiN Gradient Coating[J].CHINA SURFACE ENGINEERING, 2019, 032(002):34-43.
-