
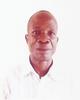
- Open Access
- [post-views]
- Authors : Akwukwaegbu Isdore Onyema , Anumaka Michael Chukwukadibia , Agubor Cosmas Nkemmdirim
- Paper ID : IJERTV10IS030178
- Volume & Issue : Volume 10, Issue 03 (March 2021)
- Published (First Online): 30-03-2021
- ISSN (Online) : 2278-0181
- Publisher Name : IJERT
- License:
This work is licensed under a Creative Commons Attribution 4.0 International License
Transient Configuration of A Photovoltaic-Diesel Energy Sources for Electric Power Production in Multi-Engineering Complex of Federal University of Technology, Owerri, Nigeria
1Akwukwaegbu Isdore Onyema, 2Anumaka Michael Chukwukadibia, Agubor Cosmas Nkemmdirim3
1,3 Department of Electrical Electronic Engineering, Federal University of Technology, P.M.B. 1526, Owerri, Imo State, Nigeria.
2 Department of Electrical and Electronic Engineering, Imo State University, Owerri, Imo State, Nigeria.
Abstract: The work covers transient configuration of the grid connected photovoltaic-diesel power production in multi- Engineering building complex of Federal University of Technology, Owerri (FUTO), Nigeria. The electric power shortage in Nigeria and the global drive towards exploring new energy sources have facilitated the consideration of the grid connected photovoltaic-diesel power generation, as a viable solution to poor energy supply system in multi-Engineering complex of FUTO, Nigeria. The work is achieved through estimation of complexs daily average load profile in a consecutive number of ten hours, complex`s component selection and sizing of solar panels and solar PV modules, inverter without battery storage capacity, diesel generator capacity, transient configuration and modeling using Matlab/Simulink Sim scape Tool. The same tool is deployed for the transient configuration simulation of the developed system. The performance evaluation of the simulation results revealed that the active and reactive powers recorded permissible elongated transient duration period ranging from 0 to 3 seconds when the diesel generator is supplying the set load alone. However, when PV and diesel generator are connected to the building complex load without the grid, the transient optimum operation ranging from 0 to 2 seconds is recorded. The estimated load for the complex is approximated as 150kW, and this load operates at an average duration of 10 hours daily to produce approximately a total daily energy for the complex as 2,000KWh per day throughout the lifetime of the system design, which is shared among the PV-diesel power plant configuration at the ratio of 60%:40% daily. The PV system would supply 60% of the total daily power and energy demand of 89.616kW and 1,176.384KWh per day whereas, the diesel generator supplies 40% of the total daily power and energy demand of 59.744kW and 784.256KWh per day, so as to reduce the daily cost of fuel consumption.
Keywords: Matlab/Simulink Simscape Tool, PV Energy Source and Diesel Generator, Inverter without Battery Storage Capacity, FUTO Multi-Engineering Building Complex, Total Daily Power and Energy Demand
-
INTRODUCTION
The power shortage in Nigeria has facilitated the need for new energy sources(the grid connected photovoltaic- diesel systems), which would supply adequate and continuous electric power into the multi- Engineering building complex of Federal University of Technology, Owerri, Nigeria for effective learning and research. A photovoltaic-diesel system
has a photovoltaic array (with an inverter to convert dc to ac) operating alternatively or in parallel with a conventional diesel engine driven alternator. The diesel engine-alternator supplies the load when solar insolation is not available. Moreover, this system is necessary when the total load requirement is more than that which can be supplied by photovoltaic system alone [1].
Electricity is obtained from the PV-diesel system (array-diesel generator) most efficiently during sunny daytime hours. At night or during cloudy periods, storage batteries are used to supply electricity.
When a PV-diesel system (array-diesel generator) is connected to the grid, it becomes part of the grid and electricity is provided without battery storage requirements [1], [2], [3], [4]. The grid or diesel generator acts as the battery to supply electricity when the PV system cannot supply at night or during cloudy periods. Production of electricity from the PV-diesel generator grid support system without battery storage will reduce capacity cost, operation and maintenance costs.
An inverter is used as an interface between the PV- diesel system (array-diesel generator) and the grid. The inverter converts dc into ac so that PV-diesel system output is synchronized with the grid. The PV-diesel grid support system will feed power directly into the distribution network by means of a grid interactive or line synchronized DC/AC power converter (inverter) at the tie in points. The PV-diesel grid support system is a two way power flow system.
When excess solar insolation is available, the PV- diesel system feeds the distribution network (33KV) or transmission network (132KV). When PV-diesel power is insufficient, the grid feeds the distribution network or transmission network.
The PV-diesel grid support system supports the overloaded portion of the distribution network, which may be experiencing daytime capacity limitations due to peak demand from commercial and air-conditioning loads, and also support the weak portion of the transmission network, which may be experiencing voltage drop due to long distances. A PV-diesel system connected to the grid at the distribution level is one form of distributed generation [1].
The advantages of the PV-diesel grid support system are as follows: savings on expenditures on transmission and
distribution equipments, reduced fuel consumption or fossil fuels conservation, lower operating costs, lower maintenance power generation cost, lower generation capacity with minimum load reserve requirements, reduced emissions of greenhouse gases, reduced emission control investments, environmentally sound, better voltage profile and improved reliability.
In grid connected PV-diesel system, it is necessary to disconnect the PV system from the grid in the event of loss of diesel generator supply or failure of distribution network supply or transmission network supply. A bad technical condition arises when the grid is intentionally or accidentally disconnected from the distribution system, but the PV-diesel system continues to feed the local load. This condition is called islanding. This condition may pose danger to maintenance personnel, public safety, and the equipment in the distribution system, customers in the distribution system etc. When the grid is reconnected, transient overcurrents may flow through the PV-diesel system; inverter and protective equipment may maloperate or be demerged. The special precautions that are needed to avoid such conditions include installation of over/under voltage detection equipment, where the inverter is shut down, when the grid voltage tends to deviate from the set value, and installation of the phase jump detection equipment, where the phase of inverter current is synchronized at zero, crossing with phase of voltage via a phase lock loop circuitry [1].
The configurations of a photovoltaic-diesel system are series PV-diesel configuration, switch PV-diesel configuration and parallel configuration of PV-diesel energy sources. Both the PV array and diesel alternator generator feed the dc bus in a series PV- diesel configuration. The inverter is fed from dc bus and converts dc to ac for supplying the load. The power output of diesel generator is fed to battery charger which feeds the dc bus. The conversion losses are high because two conversions (ac to dc and then dc to ac) are being done. The output of battery charger can be used to charge the battery bank to keep if fully charged. The solar controller prevents overcharging of battery [1].
In a switched PV-diesel configuration, the load can be fed ither from PV array or diesel engine, depending on the requirement and availability of solar insolation. The system has dc and ac buses. The diesel engine output feeds the ac bus, which feeds the load directly. Alternatively, the load can be supplied by PV array-inverter combination. Since the load is supplied directly by the diesel generator, the system efficiency is high during off-peak periods, the diesel engine is switched off and load is fed by PV array and the battery. Hence, there is a momentary interruption of power to the load when change-over switch is operated to transfer load from one source to the other [1].
However, parallel configuration of PV- diesel energy sources can supply the off peak load by PV array or diesel engine. The peak load can be supplied from combined sources by synchronizing the output of diesel generator with inverter output. The bi-directional inverter can operate in rectifier mode when it changes the battery from diesel engine output, as well as inverter mode, when it feeds the load from PV array or battery. The solar controller prevents overcharging of battery. This system can meet the load
demand in optimal way by maximizing the efficiency. However, automatic control is required to ensure reliable operation [1].
The sun as the major source of mechanical energy, converts 6x1011Kg of mass into energy each second, which is equivalent to 1023KW of electric power [1]. The sun`s great energy release is the result of an elaborate chemical process in the sun`s core known as a process of thermonuclear fusion like the reaction in a hydrogen bomb. At the tremendous heat of more than 45×106 0F in the interior of sun, the hydrogen atoms fuse with helium atoms to produce the energy that powers the planet [1]. Solar energy travels in small particles called photons, which when converted at a very low efficiency can result in more energy that could conceivably be harnessed or utilized for power generation.
The amount of solar energy expressed as solar constant with the acceptable value of 1.376kW per m2, is the total energy that falls on a unit area exposed normally to the rays of the sun at the average sun-earth distance. The solar energy is transmitted mostly in a relatively narrow wavelength band from 0.2 to 2.0 or in a frequency range from 1.5x 1014Hz to 1.5x 1015Hz. A number of scattering and absorption processes in the atmosphere reduce the maximum heat flux reaching the earth`s surface to around 1kW per m2. The heat flux reaches the earth`s surface by direct and diffuse modes. It is only the direct heat energy collected through a collector, can be utilized for solar power generation since substations could cover only a very small fraction of the earth. The ratio of direct to total heat energy varies from place to place and depends on the atmospheric conditions, such as dust, smoke, water vapour and other suspended matter [1].
The quantity of solar energy received at any given point on the Nigerian surface of the earth depends on the geographical location, the time of the year, the time of the day and local weather conditions [5]. In Nigeria, the direct conversion of solar energy to electricity is time dependent and on an average of 10 hours per day [6]. Since there is no sunshine at night, rainy and cloudy conditions, adequate arrangement should be made for energy to be used at such times by storage when conditions are favourable. In Nigeria, variation during the year in the distance between the sun and the earth lead to annual variations in the solar constant of
±3.5(about 50W/m2). Solar constant is highest in Nigeria during the dry season (December-February time period) and coldest during the rainy season (May-August time period).
Nigeria is well endowed with solar energy due to its geographical location between latitudes 40 and 140 North of the equator [5], [6]. The solar energy variation due to geographical location is due to the angle that the sun makes with a horizontal plane on the surface of the earth. The solar radiation level on a horizontal surface in Nigeria ranges from 3.7kWhm-2day-1 to 7.0kWhm-2day-1[5]. A greater percentage of Nigeria receives the average solar radiation level of about 5.5kWhm-2day-1[5], [7], [8], [9], [10]. The solar radiation is attenuated during the harmattan period and during the rainy season. Nigeria receives about 5.081x102kWh of energy per day from the sun with more than 2000 hours sunshine per year. The use of solar powered system with 10 percent efficiency to cover1percent of the Nigeria`s surface could
generate energy output equivalent to about 10 million barrels of oil per day. This is about eight times the present level of oil production in Nigeria [5], [11], [12].
Solar energy is converted directly into electric energy by photovoltaic process, which is the generation of an electromotive force (emf) as a result of the absorption of ionizing radiation. Energy conversion devices, called photovoltaic cells or solar cells are used to convert sunlight to electricity by photovoltaic effect. These energy conversion devices are transducers which convert the sun`s radiant energy directly into electricity, and are basically semiconductor diodes capable of developing a voltage of 0.5 to 1 volt and a current density of 20 to 40mA per cm2 depending on the materials used and the sunlight conditions. The solar cells are connected in series and parallel and incorporated in several modules, which are interconnected to comprise a solar array. Since a solar array consists of a number of modules, the size of the array can be adjusted to suit the requirement [1].
The basic components of the grid connected photovoltaic-diesel electric power systems are the grid and its electrical equipment, solar modules, inverter without battery storage capacity and power conditioning equipment, racking system, connecting wires and diesel plant equipment comprises of fuel system(fuel storage tanks, pumps, strainers, oil filters, meters, heaters, piping), air-intake system( air filters, ducts, super charger), engine cooling system( pumps, spray-pond, heat-exchanger, water-treatment, piping), engine lubricating system(oil tanks, oil pumps, relief valves, filters, purifiers, coolers, piping), exhaust system(connecting ducts, silencers, mufflers, waterheaters), alternators with exciters, instrumentation, and switchgear and control equipment [1], [13 ], [14 ], [15 ].
The grid connected PV-diesel systems will utilize the energies from the grid, the solar and the diesel generator as the power sources and transfer the daily power and energy into Multi-Engineering FUTO building complex load without the solar battery capacity through conditioning by power electronics. Due to electric power shortage and high transmission lines per Km cost from the national grid system to power effectively the learning equipment in the multi- Engineering building complex of the institution, the paper proposed the design, transient configuration, modeling and sizing of the grid connected PV-diesel generator systems for a reliable electric power supply in the complex`s laboratories, offices, lecture theatres, lecture halls and auditorium applications in terms of cost effectiveness and efficiency. The work is achieved through estimation of complexs daily average load profile, complex`s component selection and sizing without solar battery storage capacity, transient configuration and modeling using Matlab Simulink Simscape tool. The grid connected PV-diesel generator systems would eradicate completely energy supply deficit and create more room for energy availability and adequacy in Multi- Engineering FUTO building complex.
-
OVERVIEW OF MULTI-ENGINEERING BUILDING COMPLEX OF FUTO RESULTS AND
DISCUSSION
The Federal University of Technology Owerri (FUTO) is located at a Latitude 5, Longitude 7, 511 ft (above sea level) and 18km south from the Owerri capital Territory. It is surrounded by Ihiagwa, Eziobodo, and Obinze autonomous communities [16]. The institution has been confronted with power shortage for man years now, owing to the ever increasing population growth of the university community and the deterioration of the existing electric power facilities. With the high level of sunshine in the institution, the grid connected solar photovoltaic – diesel generator systems are feasible to supply the set daily power and energy demand for the Multi-Engineering building FUTO complex, also known as the School of Engineering and Engineering Technology (SEET) building complex.
-
Materials and Methods
Load Forecasting of Multi-Engineering Building FUTO Complex
The load forecasting is provided on day-ahead by the system operator which depends on the previous load data weather forecasts [17]. A load survey and inventory of the existing load profile and the electrical facilities are achieved by estimating and summing up the total daily load and energy demanded for the duration of ten hours per day. The procedures involved sizing of the grid photovoltaic-diesel electric power systems for powering multi-Engineering building FUTO complex include the acquisition of the load data of the major appliances needed in the complex, such as air conditioners, lighting loads, desktop computers, photocopiers and fans, and summing up to estimate daily complex`s total load and energy demanded.
The load survey data acquired from site visit, indicated that multi-Engineering building FUTO complex comprises of six identical departmental engineering buildings, one auditorium, two canteens, the dean`s apartment, several walkways and general offices. The deans apartment occupies a two storey building, whereas two conference rooms, two rest rooms and two offices are seen on the ground floor. The first floor contains three offices, a computer laboratory and a rest room whereas, the second floor, which is the last floor, has the deans office, 5 other offices, deans conference room and one general restroom.
Each of the identical departmental engineering buildings has six offices, four restrooms and two lecture halls on the ground floor, two lecture halls, one computer laboratory, three offices and four restrooms, on the first floor and nineteen offices and one conference room on the last floor. The load demands available in the complex offices are grouped into class-A, class-B and class-C offices respectively. Hence, the overall classes of load demands in the multi-Engineering building complex are grouped into the lecture halls, conference rooms, class-A offices, class-B offices, class-C offices, Auditorium, Canteen and Computer laboratory.
The power points and lighting fixtures, their arrangements and the consequent load on the multi-Engineering building
FUTO complex comprise of 70W ceiling fans, 13A socket outlets powering 45W laptops, 5W phones, 60W projectors, 100W and 50W television(smart), 50W printer, 60W desktop computer, 600W photocopier, 70W public address system, 150W refrigerator, 1200W microwave, 15A socket outlets powering 1.5HP air conditioner and lighting points powering 40W energy saving bulbs as shown in tables 1 to 8 and figures 1 to 3 respectively.
The restroom has as a total load of 120W from three numbers of 40W energy saving bulbs and the walkway recorded a total load of 13, 360W from 334 numbers of 40W fluorescent lamps. Table 9 presents the comprehensive load forecasting for the entire multi-Engineering building complex of the institution with the total daily electric power and energy as 149.36KW and 1,960.64KWh operating for the duration of 10 hours per day. Only the walkways and future expansion operate 24 hours daily.
-
Thermal Fatigue Test
The thermal fatigue test was done in a thermal cyclic furnace. The specimens were tested at 6000C highest temperature. Heating and cooling time were kept as 10 minutes. When the samples were cooled to the ambient temperature, they were taken out, dried and put into the high temperature furnace again, repeating the same process. More than 90% of the cracked regions of the surface of TBC systems were adapted as the criterion for the failure of the coating. The weight changes of the samples were measured to a precision of 0.5 mg by an analytical balance. Three number of specimens were tested and average was considered for analysis.
-
-
RESULTS AND DISCUSSION
-
TBC system Composition of
Microstructure of TBCoated alluminium alloys after thermal cycling till failure is shown in Fig. 1 (a and b). The failure of TBC coated surface on aluminium alloys under thermal fatigue conditions was found be in a cracking mode, which induces from coated compressive loads and more frequent thermal shock than their aircraft counterparts. In addition, many of these TBCs must cope with the contaminates found in lower-grade fuels. The difference between aircraft TBCs and diesel TBCs are often ignored by coating applicators. Thermal barrier coatings can be applied on gas turbines, automotive engines and diesel equipment. The use of TBC on diesel components such as valves, pistons and fire decks insulates the metal substrates from high- temperature oxidation and corrosive environments. As a thermal barrier, it reduces metal temperatures as well as bond coat. The micro-columnar grains encircled in Fig.2. was observed, which were solidified from the melted fraction of YSZ top coat powder.
-
Thermal Fatigue behaviours of TBCs systems
Square specimen were selected to consider the effect in practical application of thermal barrier coating (TBC) system, such as edges and corners in internal combustion (IC) engine piston. It can be seen from Fig. 1 compressive loads and more frequent thermal shock than their aircraft
counterparts. In addition, many of these TBCs must cope with the contaminates found in lower-grade fuels. The difference between aircraft TBCs and diesel TBCs are often ignored by coating applicators. Thermal barrier coatings can be applied on gas turbines, automotive engines and diesel equipment. The use of TBC on diesel components such as valves, pistons and fire decks insulates the metal substrates from high-temperature oxidation and corrosive environments. As a thermal barrier, it reduces metal temperatures not occur. After 52 cycles, gradual weight loss was observed indicating thermal degradation of coated specimens. After 97 cycles, the sudden weight loss of samples was observed, which implied the coating damage via the cracking mode.
Fig.1. (a & b) Optical Micrograph of Fractured plasma sprayed TBC specimens with thickness of 250µm after TF testing
Fig.2. FESEM micrograph of the fractured surface of as-sprayed YSZ TBC.
Fig.3. Weight Change as a function of cycle number YSZ TBCs during thermal fatigue testing.
CONCLUSIONS
Thermal fatigue behavior of plasma sprayed YSZ TBC system on 2024 AA was studied and major conclusions are as follows:
-
In all cases, the initial cracks were initiated at the edge/corner of the square specimens.
-
The failure of YSZ TBCs systems on 2024AA were observed due to the multiple cracks mode only. The results show four types of cracks formed in TBCs systems on 2024 AA, i.e., vertical cracks, horizontal crack, propagating crack, and penetrating crack [16]. In this article, vertical cracks and propagating cracks (or horizontal crack) emerged in YSZ based TBCs systems for 2024AA. The penetrating vertical cracks started penetrate from top coat to the substrate surface at 6000C.
ACKNOWLEDGMENTS
TBC on diesel components such as valves, pistons and fire decks insulates the metal substrates from high- temperature oxidation and corrosive environments. As a thermal barrier, it reduces metal temperatures (Scientist G), Head of Mechanical Behaviour Group Defence Metallurgical Research Group Lab, pistons and fire decks insulates the metal substrates from high-temperature oxidation and corrosive environments. As a thermal barrier, it reduces metal temperatures (Scientist G), Head of Mechanical Behaviour Group Defence MetallurgicalResearch Group Lab (DMRL, Hyderabad) for their cooperation.
REFERENCES
-
C.R.C. Lima, J.M. Guilemany, Adhesion improvements of Thermal Barrier Coatings with HVOF thermally sprayed bond coats, Surface and Coatings Technology, vol.201,no.8,pp.46944701,15 January 2007,.
-
Esfahanian, A. Javaheri, and M. Ghaffarpour, Thermal analysis of an SI engine piston using different combustion boundary condition treatments, Applied Thermal Engineering,vol.26,p Esfahanian, A. Javaheri, and M. Ghaffarpour, Thermal analysis of an SI engine piston using different combustion boundary condition treatments, Applied Thermal Engineering,vol.26,pp.277-287,2006., Surface and Coatings Technology,vol. 203, pp. 91-98, 2008.
-
Anna Gilbert, Esfahanian, A. Javaheri, and M. Ghaffarpour, Thermal analysis of an SI engine piston using different combustion boundary condition treatments, Applied Thermal Engineering,vol.26,pp.277-287,2006., Surface and Coatings Technology,vol..202,pp.2152-2161,2008.
-
T. Hejwowski, and A. Weronski, The effect of thermal barrier coatings on diesel engine performance, Vacuum,vol.65, pp.427- 432, 2002.
-
E. Buyukkaya, Thermal analysis of functionally graded coating Al- Si alloy and steel pistons, Surface and Coatings Technology,vol.202,pp. 3856-3865, 2008.
-
E. Esfahanian, A. Javaheri, and M. Ghaffarpour, Thermal analysis of an SI engine piston using different combustion boundary condition treatments, Applied Thermal Engineering,vol.26,pp.277- 287,2006.,pp.398-402,2007.
-
M. Cerit, V. Ayhan, A. Parlak, and H. Yasar, Thermal analysis of a partially ceramic coated piston: Effect on cold start HC emission in a spark ignition engine, Applied Thermal Engineering,vol. 31,no. 2 3,pp.336-341,2011.
-
Michael Anderson Marr, An Investigation of Metal and Ceramic Thermal Barrier Coatings in a Spark-Ignition Engine, M.S thesis, Mechanical and Industrial Engineering, University of Toronto, 2009.
-
V. Esfahanian, A. Javaheri, and M. Ghaffarpour, Thermal analysis of an SI engine piston using different combustion boundary condition treatments, Applied Thermal Engineering,vol.26,pp.277-287,2006.
-
Muhammet Cerit, Thermo mechanical analysis of a partially ceramic coated piston used in an SI engine, Surface & Coatings Technology,vol.205, pp. 3499-3505,2011.
-
Daniel W Parker, Thermal barrier coatings for gas turbines, automotive engines and diesel equipment, Materials & Design, Vol. 13,no. 6,pp. 345-351,1992.
-
-
C. Giolli, A. Scrivani, G. Rizzi, F. Borgioli, G. Bolelli, and L. Lusvarghi, Failure mechanism for thermal fatigue of thermal barrier coating systems, Journal of Thermal Spray Technology,vol.18,pp.223230,2009.
-
C. Zhou, Q. Zhang, and Y. Li, Thermal shock behavior of nanostructured and microstructured thermal barrier coatings on a Fe- based alloy, Surface & Coatings Technology,vol.217,pp. 70 75,2013.