
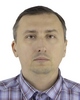
- Open Access
- Authors : Dmytro V. Ivanchenko, Mykhailo M. Yamshinskij
- Paper ID : IJERTV10IS100024
- Volume & Issue : Volume 10, Issue 10 (October 2021)
- Published (First Online): 08-11-2021
- ISSN (Online) : 2278-0181
- Publisher Name : IJERT
- License:
This work is licensed under a Creative Commons Attribution 4.0 International License
Treatment of An Aluminum Casting Alloy of the Al-Si-Cu-Mg System with Zirconium Entered from its Compounds
Dmytro V. Ivanchenko
Assistant, Department of Foundry,
National Technical University of Ukraine «Igor Sikorsky Kyiv Polytechnic Institute»,
Kyiv, Ukraine, Peremohy av., 37
D.Sc. Mykhailo M. Yamshinskij
Senior Professor, Department of Foundry,
National Technical University of Ukraine «Igor Sikorsky Kyiv Polytechnic Institute»,
Kyiv, Ukraine, Peremohy av., 37
The choice of a flux that contains zirconium and is intended to harden the aluminum casting alloys has been justified. The microstructure and mechanical characteristics of an aluminum casting alloy of the Al-Si-Cu-Mg system, reinforced with zirconium, have been investigated.
INTRODUCTION
There is a method of production Al-Zr ligatures from zirconium dioxide [1] based on interactions in the systems ZrO2- KF-AlF3, ZrO2-NaF-AlF3-KCl due to the formation of potassium and sodium fluorozirconates, followed by the reduction of zirconium with aluminum.
Moreover, thanks to [2], it was established that the sequence of chemical reactions occurring at high temperatures between pure aluminum and K2ZrF6 can be represented by the following equations:
3K2ZrF6 + 4Al K3AlF6 + 3KAlF4 + 3Zr (1)
3Zr + 9A1 3Al3Zr (2)
In addition, in their experimental results, Rocher et al. [3] noted that when aluminum and K2ZrF6 powders are mixed in a stoichiometric ratio that corresponds to the equation (2) and are heated at 700 ° C (either in air or under vacuum), X-ray diffraction analysis confirms the appearance of KAlF4, K3AlF6, and Al3Zr in the products reactions.
Taking into account the above mentioned, the choice of the composition of the flux consists of the selection of such components and their ratio, which made it possible to obtain the highest possible zirconium yield from its fluoride or oxide into the aluminum melt at a minimum cost. For further research, a system containing ZrF4 was selected.
Elements of the group 4A, to which zirconium also belongs, form very strong chemical compounds with fluorine. Zirconium tetrafluoride, when added to an aluminum melt, despite the thermodynamic possibility of reduction with aluminum, does not dissociate, and does not saturate the aluminum melt with zirconium at temperatures of 650-950 °C. Consequently, it becomes necessary to select such components of the flux and their ratio in the melt, which will allow to reduce zirconium in the medium of liquid aluminum. In order to select such components, the NaF-LiF-ZrF4 system was considered. The diagram of the corresponding system is shown in Fig. 1.
The ratio between the components of the flux is selected in such a way as to ensure the minimum melting point of the strengthening mixture, and the presence of such a compound in the slag melt as Li2ZrF6 (Na2ZrF6).
Fig. 1 – State diagram of NaF-LiF-ZrF4 [4]
The diagram shows that one of the most promising options for saturation of an aluminum melt with zirconium is a mixture, the ratio between the components of which at a temperature of 436 ° C is – LiF – 26 mol. %, NaF – 37 mol. %, ZrF4 – 37 mol. %. Thus, the formation of compounds Li2ZrF6 and Na2ZrF6 is possible due to eutectic transformations.
METHEDOLOGY
In order to study the microstructure and mechanical properties of the cast alloy of the Al-Si-Cu-Mg system, treated with compound flux containing zirconium tetrafluoride, the AK8M3h alloy was chosen. One of the tasks of the work was to find a replacement for beryllium, used as an alloying component of this alloy. The closest analogues of this alloy are alloys A 380.0 (US ASTM standard), SG 84 A (US B85 standard) and G-AlSi9Cu3 (German DIN 1725T.2 standard). Taking into account the high chemical activity of aluminum and magnesium, which are used in the preparation of the alloy, the contamination of the alloy with solid and gaseous non-metallic inclusions should be expected at all stages of the technological process. To prevent contamination of the melt, preparation of equipment, working tools and materials is carried out. The crucible is visually inspected and its suitability for melting is determined. The crucible is cleaned of dirt and slag, painted with a protective paint based on zinc oxide. The ladle and mold are also painted. When carrying out the preparation works, the use of tool made of titanium is recommended. harge materials cleared of dirt, oils and oxides are loaded into the furnace. Firstly, large pieces of the charge are placed on the bottom of the crucible, and then the space between them is filled with small pieces.
It is known that the addition of silicon to an aluminum melt significantly reduces the amount of zirconium, which can be dissolved in liquid aluminum and prevents the saturation of aluminum with zirconium (Fig. 2).
Fig. 2 – Limit of areas of primary crystallization in the Al-Zr-Si system [5]
Aluminum grade A6 is melted in a resistance furnace, or in an induction furnace preheated to 750 ° C. Next, zirconium tetrafluoride mixed with lithium fluoride and sodium fluoride is introduced into liquid aluminum. The mixture is applied to a thoroughly cleaned aluminum surface and mixed into the melt until complete dissolution, after which manganese chloride is applied to the melt surface in order to prevent aluminum waste and the melt is kept at the above temperature for 15 minutes.
Later, the required amount of the aluminum-silicon casting alloy AK8M3ch is added to the aluminum processed in the above way and thoroughly mixed for 2 minutes. Then, copper M00 (GOST 859-2001), primary magnesium Mg90 (GOST 804-93), zinc C0 (GOST 3640-94) are dissolved into the melt, slag is removed and the melt is poured.
MICROSTRUCTURE AND MECHANICAL PROPERTIES OF ALUMINUM-SILICON CASTING ALLOY AK8M3CH, TREATED WITH A FLUX, CONTAINING ZIRCONIUM TETRAFLUORIDE
It is known that, among other elements, zirconium is also used to grind the grains of -phase (silicon solution in aluminum) and -phase (Si) of hypoeutectic and eutectic silumins. When zirconium interacts with an aluminum melt, a compound Al3Zr is formed, but the zirconium-aluminum intermetallide with its parameters of the crystal lattice does not fit the Dankov- Konobeyevsky principle of dimensional and structural correspondence in relation to the analogous parameters of the -phase and
-phase [6]. Therefore, zirconium cannot act as a modifier of the nucleating action during the crystallization of hypoeutectic and eutectic silumins. The hardening effect of zirconium is partly explained by the formation of a refractory compound together with silicon, which can block the growth of the -phase nuclei, which, in accordance with the classical modification theory, leads to the refinement of silicon. However, it remains unknown why zirconium grinds only eutectic silicon, and has a weak effect on primary silicon. The microstructure of a cast alloy type is shown in Figure 3.
Fig. 3 – Microstructure of the AK8M3ch aluminum-silicon alloy treated with zirconium in the cast state. |
Rather coarse structure is observed, consisting of a solution of silicon and copper in aluminum and dark needles of silicon and phases that have Zr, Cu, Fe, Ti, Zn in their content concentrated along the grain boundaries. The strength of the alloy in the cast state is 253 MPa, the relative elongation is 2.3%. Due to the addition of titanium, boron and zirconium, the structure is fine- grained. However, the presence of needle-like components and phases that contain iron in their omposition contributes to a decrease in the strength of the alloy in the cast state. The chemical composition of the structural components of the AK8M3ch alloy are shown in Table 1.
Table 1. Chemical composition of the aluminum-silicon casting alloy AK8M3ch
Research point |
The elements, % |
||||||||
Al |
Mg |
Si |
Ti |
Fe |
Mn |
Cu |
Zn |
Zr |
|
1 |
96,94 |
– |
1,28 |
0,06 |
0,1 |
– |
0,68 |
0,93 |
– |
2 |
44,73 |
0,03 |
19,08 |
0,27 |
33,3 |
0,7 |
1,36 |
0,37 |
0,16 |
3 |
37,87 |
0,17 |
20,86 |
0,27 |
38,61 |
0,64 |
1,36 |
– |
0,22 |
4 |
23,57 |
0,42 |
1,35 |
0,22 |
0,4 |
– |
73,31 |
0,61 |
0,12 |
The microstructure of the cast alloy is a solution of copper, silicon and zinc in aluminum. Along the grain boundaries, there is a network of Mg2Si phase and phases containing zirconium, iron, copper, boron, and titanium. Despite the fine-grained
structure, the precipitations are concentrated at the grain boundaries and have rather coarse, often needle-like structure, which does not allow, despite the presence of such modifiers as titanium, boron and zirconium, to significantly increase the strength of the alloy, which fluctuates in the range 240-253 MPa. It should also be noted that the brighter color of the structural component corresponds to the heavier metal that forms it.
After heat treatment [7], the silicon content in the solution is significantly reduced. The number of areas of the solution increases, and its composition changes. Namely, we actually observe a solution of copper and zinc in aluminum. The network- like phase Mg2Si (63.2% Mg; 36.8% Si), which was present in the cast alloy is absent. Instead, a phase was formed containing almost 78% Si in the shape of rounded grains concentrated along the grain boundaries of the -solution. Zirconium is presented in the form of a triple compound with silicon and aluminum, which also concentrates in the form of plates along the grain boundaries. The change in the shape and size of the phases containing silicon and zirconium makes it possible to increase the strength of the alloy to 363 MPa after heat treatment. The structure of the heat-treated alloy is shown in Figure 4.
Fig. 4. – Microstructure of the AK8M3ch aluminum-silicon alloy, reinforced with zirconium in the heat-treated state. |
The chemical composition of the AK8M3ch aluminum-silicon alloy, hardened with zirconium in the heat-treated state at points 1 – 4, is presented in Table 2.
Table 2. Chemical composition of the AK8M3ch aluminum-copper casting alloy after heat treatment
Research point |
The elements, % |
||||||||
Al |
Mg |
Si |
Ti |
Fe |
Mn |
Cu |
Zn |
Zr |
|
1 |
94,4 |
– |
0,51 |
0,17 |
– |
– |
3,52 |
1,29 |
0,1 |
2 |
20,85 |
0,11 |
77,9 |
0,26 |
– |
– |
0,64 |
0,24 |
– |
3 |
7,2 |
– |
29,95 |
17,78 |
– |
– |
0,56 |
0,5 |
43,98 |
4 |
71,73 |
– |
5,19 |
18,1 |
– |
– |
4,13 |
0,85 |
– |
CONCLUSIONS
It has been established that the addition of zirconium to the AK8M3ch aluminum casting alloy instead of beryllium makes it possible to preserve the mechanical properties at the same level and to exclude the use of beryllium in the technological process of the production of this alloy.
REFERENCES
-
V. I. Moskvitin. Thermodynamic foundations of aluminothermic reduction of zirconium from ZrO2 in chloride-fluoride salt melts / V.I. Moskvitin, D.
-
Popov, S. V. Makhov // Non-ferrous metals. – 2012. – No. 4. – p. 4346;
-
-
Rocher, J. P. – Quenisset, J M. – Naslain, R.: J. Mater. Sci., 24, 1989, p. 2697;
-
J.P. Rocher, J.M. Quenisset, R. Naslain. Wetting improvement of carbon or silicon carbide by aluminium alloys based on a K2ZrF6 surface treatment: application to composite material casting, Journal of Materials Science. 24 (1989) 26972703;
-
D. F. Williams. Assessment of candidate molten salt coolants for the advanced high-temperature reactor (AHTR) / D. F. Williams, L. M. Toth, K. T. Clarno // Tennessee: Oak Ridge, 2006. . 86. Bibliogr.: p. 62 66;
-
N. A. Belov. The influence of zirconium on the structure and mechanical properties of microalloyed alloys of the Al-Fe-Si system. / N. A. Belov, V.
V. Istomin-Kastrovsky, A. N. Alabin // Izvestiya vuzov. Series: Non-ferrous metallurgy – 2003. – No. 4. – p. 54-60;
-
V. Yu. Stetsenko. On the fundamental principle of the theory of modification of alloys / V. Yu. Stetsenko // Casting and metallurgy – 2009. – 4. – p. 68-71;
-
V.V. Grinin. Study of weldability of dissimilar aluminum alloys [Electronic resource] / V. V. Grinin, V. V. Ovchinnikov, V. I. Lukin, E. N. Ioda // VIAM / 988-200180 / All-Russian Institute of Aviation Materials ("VIAM" SSC RF). M.: 1988.- 9 p.: access mode: http://docplayer.ru/46393091- Issledovanie-svarivaemosti-raznoimennyh-alyuminievyh-splavov.html