
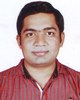
- Open Access
- Authors : Pravin B Bhorkade , Dr. A. B. Kakade
- Paper ID : IJERTV9IS060934
- Volume & Issue : Volume 09, Issue 06 (June 2020)
- Published (First Online): 07-07-2020
- ISSN (Online) : 2278-0181
- Publisher Name : IJERT
- License:
This work is licensed under a Creative Commons Attribution 4.0 International License
Tribological behavior of Clutch Plate Material in Laboratory Simulated Conditions
Pravin B Bhorkade1
1P.G Student (Mechanical Design Engineering) Department of Mechanical Engineering NDMVPS KBT COE, Nashik,
Pune University, Pune, Maharashtra, India
Dr. A. B. Kakade2
2 Professor, Department of Mechanical Engineering NDMVPS KBT COE,Nashik, Maharashtra, India. .
Savitribai Phule Pune University, Pune, Maharashtra, India.
Abstract- A Clutch is a machine member used to connect the driving shaft to a driven shaft, so that the driven shaft may be started or stopped at will, without stopping the driving shaft. While riding the clutch, it simply means keeping the clutch pedal, fully, or partially pressed down. Hence, the pressure on the pad is creating a huge amount of friction which will very quickly produces the wearing in Clutch plate material. The concept is to understand material behavior and wear and friction criteria. The clutch plate is made of material usually of Grey Cast Iron with Asbestos used as Friction Lining Material. In this research, an attempt is made to try out Composite material clutch plate. Composite are of polymer, ceramic and metal matrix type. The use of composites is motivated because of good friction co-efficient and wear resistant properties. The aim of this present work is to identify a heat resistant clutch material for optimum friction coefficient (µ) and to decide a perfect composite material which has low wear rate at different temperature, load and velocity conditions. The Clutch Plate is modelled and analyzed using Creo and FEA software. The Experimental investigation of plate is done by Pin on Disc Apparatus for validation of wear rate and Friction Co-efficient.
Key words: Clutch Plate, Wear Rate Analysis, Pin on Disc Setup.
-
INTRODUCTION
Wear is damage to a surface as a result of relative motion with respect to another substance. One key point is that wear is damage and it is not limited to loss of material from the surface. However, loss of material is definitely one way in which apart can experience wear. In the older definitions of wear there used to be a greater stress on the loss of material
Wear causes an enormous annual expenditure by industry and consumers. For some industries such as agriculture, as many as 40% of the components replaced on equipments have failed by wear. Estimates of direct cost of wear to industrial nations vary from 1% to 4 % of GNP and it is estimated that 10% of all energy generated by man is dissipated in various friction processes. Thus the magnitude of losses caused to mankind (which can be expressed in percentage points of GDP) makes it absolutely
necessary to study ways to minimize it. Thus minimizing wear, affects the economics of production in a major way
A clutch mainly consists of two parts, i.e. friction plates and separator plates. These plates engage and disengage to transmit speed and torque. The transmitted torque is proportional to the overall friction coefficient of the clutch plates. The friction behavior of clutch plates is critical for overall performance of the transmission and it depends on the
sliding velocity, the normal pressure, the lubrication, the temperature and the surface topography of the clutch plates. It is necessary to investigate the effect of surface topography on the friction behavior of the clutch plates. Study of various research paper, the surface characteristics of clutch plate materials have been investigated since it is closely related to friction[1]. describes Engagement characteristics of a friction pad for commercial vehicle clutch system[2]. analyze the effect of different material composition on friction & wear of Clutch Plate material[3]. the effect of load, Velocity of sliding and sliding distance on friction and wear of materials made of Polytetrafluoroethylele (PTFE) and PTFE composites[11].
In the present work the wear behavior of various clutch materials at different operating conditions is carried out using pin on disc apparatus. Additionally, the wear volume is calculated and hardness was carried out. Further finite element analysis of clutch plate was carried out.
-
EXPERIMENTAL DETAILS
Wear is a process of removal of material from one or both of two solid surfaces in solid state contact. As the wear is a surface removal phenomenon and occurs mostly at outer surfaces, it is more appropriate and economical to make surface modification of existing alloys than using the wear resistant alloys.[1]
Pin on disk wear testing is a method of characterizing the coefficient of friction, frictional force and rate of wear between two materials. As a particularly versatile method for testing wear resistance, pin on disk can be configured in multiple scenarios depending on the goals of your project.
Pin on disk testing can simulate multiple wear modes, including unidirectional, bidirectional, omnidirectional and quasi-rotational wear. Our equipment allows us to test virtually any combination of materials to determine the effect of wear on a medical device.[3]
In this experiment, the test was conducted with the following parameters:
-
Load
-
Speed
-
Distance
Parameters
Values
Specimen pinsize
Dia 12mm & 30mm height
Wear Disc Size
Dia. 165 mm, 8 mm thick
Disc rotation
1000 rpm
Sliding speed
0.5 to 10 m/s
Normal load
5N to 200N, In steps of 5N
Parameters
Values
Specimen pinsize
Dia 12mm & 30mm height
Wear Disc Size
Dia. 165 mm, 8 mm thick
Disc rotation
1000 rpm
Sliding speed
0.5 to 10 m/s
Normal load
5N to 200N, In steps of 5N
TABLE 6 SPECIFICATIONS OF SETUP
Figure 2 Pin on Disk Setup
-
Pressure plate:-
The Pressure plate is generally made from grey cast iron (FG 300).Because of its high heat and wear resistant but its cost is too high.
In this Experiment use Pressure plate Grey Cast iron Material properties & Chemical composition given Below.[2]
TABLE 1 MATERIAL PROPERTIES OF GREY CAST IRON
Material and Properties
Value
Ultimate Tensile Strength (MPa)
1015
Ultimate Yield Strength (MPa)
979
Young's Modulus (MPa)
2e5
Poisson's Ratio
0.29
Density (kg/m3)
7850
Elongation (%) [EL]
<1
Hardness (BHN)
160 to 210
Crack growth resistance (MPa m)
11-19
TABLE 2 CHEMICAL COMPOSITION OF GREY CAST IRON
No.
Material
Composition
1
Carbon
0.4%
2
Silicon
1.1%
3
Phosphorus
0.68%
4
Manganese
4.2 %
5
Copper
0.5%
6
Chromium
0.07%
7
Nickel
0.02%
8
Molybdenum
0.007%
-
Materials :-
Figure 1. Specimen Sample of Different Pins
Al6061:
It has Good Strength in terms if Impact, Fatigue and Shearing. Good Machinability and Weldablity. The material can be casted into desired shape and hence good actability. Good Corrosion resistant to corrosive environment. Good surface finish and wear resistant
TABLE 3 CHEMICAL COMPOSITION OF AL6061
No.
Material
Composition
1
Aluminium Al
90.2499 94.9999
2
Copper Cu
3.9 5.0
3
Silicon Si
0.5 1.2
4
Manganese Mn
0.4 1.2
5
Magnesium Mg
0.2 0.8
6
Iron Fe
0.0 0.7
7
Titanium Ti
0.0 0.15
8
Chromium Cr
0.1
Al7075:
Aluminum Alloy 7075 is one of the highest strength alloys available. It has Good thermal Shock resisting capacity, good impact and fatigue strength. It Good Corrosive to resistant.
TABLE 4 CHEMICAL COMPOSITION OF AL7075
No.
Material
Composition
1
Silicon Si
0.40
2
Iron Fe
0.50
3
Copper Cu
1.2-2.0
4
Manganese Mn
0.30
5
Magnesium Mg
2.1-2.9
6
Chromium Cr
0.18-0.28
7
Zinc Zn
5.1-6.1
8
Titanium Ti
0.20
-
S-GlassFiber:
-
-
lass is generally used for polymer matrix composites include, High production rates, improved mechanical properties compared to E-glass., High strength, High stiffness. Relatively low density, Non-flammable, Resistant to heat.
TABLE 4 CHEMICAL COMPOSITION OF S-GLASS FIBER
No.
Material
Composition
1
Silicon dioxide SiO2
65wt%
2
Aluminum Oxide Al2O3
25wt%
3
Magnesium oxide MgO
10wt%
-
CarbonFiber :
The use of this as the reinforcement material in polymer matrix composites is extremely common. Optimal strength properties are gained when straight, continuous fibers are aligned parallel in a single direction.
TABLE 4 CHEMICAL COMPOSITION OF CARBON FIBER
No.
Material
Composition
1
Silicon Oxide SiO2
54wt%,
2
Aluminium Oxide Al2O3
14wt%
3
Calcium Oxide CaO + Magnesium Oxide MgO
22wt%
4
Boron Oxide B2O3
10wt%
5
Sodium Oxide Na2O + Potassium Oxide K2O
2wt%
TABLE 5 PROPERTIES OF MATRIX COMPOSITES
Parameter
AL6061
AL7075
Carbon
S-glass
sy (MPa)
310
560
1100
4587
yt(MPa)
270
207
900
3250
E (MPa)
69e3
1.93e5
0.5e3
8.69e5
µ
0.33
0.31
0.25
0.28
(kg/m3)
2700
3000
1600
2480
-
Loading Conditions : Load in Kg (W) = 2kg
-
The Load has been considered just to verify the suitability of trials on the different composite materials. The Composites are lighter in weight hence considering the same point the load has been considered.[3]
Hence Normal Force can be said as, Normal Force (FN) = 19.62 N
Disc Rotation (N) = 1000Rpm.
The Speed of the disc has been selected on the basis of regular speed of engine clutch. The Regular speed is about 1000-2000 Rpm. The Engagement speed is 2000 Rpm hence to ensure the safety, 1000 Rpm speed has been considered.[4]
Sliding Velocity:
The Sliding Velocity can been given as , VS= (DsN)/(60*1000)
Where.
Ds = Sliding phase diameter = 100mm
Hence,
VS = 5.23 m/s
-
Experimental Calculations :
-
Volume loss (V): The volume loss is actually the remaining material of pin which is left after the worn out of the pin. The Volume is the loss material of the pin which can be mathematically given as,[7]
Volume loss = Cross sectional Area x Height loss
V= A/H2 mm3 (1)
-
Wear rate: The wear rate per unit sliding distance in the transient wear regime decreases until it has reached a constant value in the steady-state wear regime. Hence the standard wear coefficient value obtained from a volume loss versus distance curve is a function of the sliding distance.[7]
Wear rate = Volume loss / Sliding distance mm3/Nm (2)
-
Wear resistance: When material generally offer good resistance to sliding and impact abrasion, increases the hardness and toughness of the steel, making it an ideal material for applications that require high impact or high abrasion resistance.[7]
Wear resistance = 1/ Wear rate (3)
-
Specific wear rate: At each loading condition, the wear rate is different. Hence the wear rate at particular loading condition is called as the Specific Wear rate. In can be defined as the ratio of wear rate to acting load. It can be given as,[7]
Specific wear rate = Wear rate/load (4)
-
Coefficient Of Friction: The coefficient of friction is ratio of frictional force to normal load.[7] = F / FN
-
-
Experimental Process :
Clean and dry specimen and disc using solvent. Weight Specimen and disc individually on weighing scale having accuracy 0.1 mg .Insert disc on fixture and tightens screws from sides to clamp, ensure the perpendicularity within +1 dig to the axis of rotation. Insert Specimen to jaw holder,insure it is sitting properly and tighten two jaws to hold ball and tighten jaws to specimen holder .Switch on controller, allow 5 min for normalizing the display on controller. Press test start push button on controller after setting 10 min time on timer display, rotate speed knob till 60 rpm is displayed, ensure the speed is constant at 60, then press stop button.Press zero button of normal load
frictional force and wear on controller.Open software on pc, select a new file, enter test parameters and sample id on screen and click on start icon to activate screen to receive data. Add 2 kg dead weight on loading pan to apply normal load .Set timer to 30min to achieve 1000mt sliding distance. Begin test by pressing on start push button, record the room temperature and relative humidity. Test stop after completion of test duration. Remove specimens , clean off loose wear debris , note the existence of feature on or near thee wear scar such as ;protrusions , displaced metal , discolorations, micro cracking or spotting Weight the specimen and record the loss in weight .The loss in weight is negligible , alternately volume loss may be measured On the bottom disc no wear is observed
Figure 4: Experimental Process
Normal Load = 2 kg = 19.62N
Time Interval = 30 min
-
-
RESULTS AND DISCUSSION
-
Wear Volume :
Wear Volume is the volume which is lost by the material after rubbing of pin. This is actual weight lost by the material.[14]
Wear Volume canbe determined as by, Vw= (W1- W2)/Density
Hence for all the materials, wear can be determined as,
So as to determine the volume rate in mm3, the densities of materials are converted to g/mm3.
Hence forth the wear volume can be seen as follows,
TABLE 12 CALCULATION FOR WEAR VOLUME
Material
Initial Weight W1(gm)
Final Weight W2
(gm)
Wear Volume (mm3)
Al6061
19.62
18.97
240.7407
AL7075
18.64
17.23
470
Carbon Fiber
10.22
10.10
95
S-Glass
10.91
10.80
45.83333
Graph 05 Wear vs. Material
The wear Volume for Carbon Fiber and S-Glass Fiber are comparatively low. Due their low density and good wear resistant property, the gives less wear out during the experimental test.
-
Co-Efficient of Friction :
The Graph 05, shows the behavior of co-efficient of friction for different materials under different interval of time. The Carbon fiber which shows the lower wear rate possess the coefficient of friction which slightly varies with respect to deeper wear testing. The Friction coefficient for S-Glass Fiber remains constant throughout the test, which shows that the wear behavior will remain constant after a certain period of time. The aluminum composites of 6061 shows the lowest amount of friction rate whereas the friction co-efficient of 7075 decreases with respect to time. After an interval of time, the Friction co-efficient of 7075 continuous to be constant.[14]
Graph 06 Time Vs. Co-Efficient of Friction
From the experimentation results, it is clear that the polymer matrix composites shows better results as that of Aluminum Composites. The Aluminum Composites, also show better results. The Aluminum and polymer composites can be used as replacement for other friction lining materials so as to reduce the wear rate and also to increase the life of friction pads in case of clutch plates.
-
Hardness Analysis
The wear system is very important; the presence of corrosion or impact can have large influence on the relation between hardness and wear resistance. The relation between hardness and wear is actually inversely proportional. The Harder the material goes, the less the wear volume.[14]
TABLE 13
HARNDESS ANALYSIS OF MATERIAL
No.
Material
HardnessSh.D
1
AL6061
81.8
2
AL7075
82.9
3
S-Glass Fiber
92
5
Carbon Fiber
95
Hence from the table above, S-glass Fiber has highest amount of hardness amongst all and so the wear rate of S-glass fiber is less. So on if Aluminum composites are considered, it possess less hardness and hence the wear rate of aluminum composites are high.
-
Discussions :
-
As per the experimentation, the wear rate of Carbon fiber and S-glass Fiber are the least. As well as the Aluminum composites are also up to better performance.
-
The Wear Volume for Carbon fiber is validated for experimentation as well as the simulation.
-
From experimentation as well as simulation, the difference in the results obtained are about 8%.
-
Simulation always shows the results without considering any of the losses, hence it shows the theoretical results.
-
The Experimentation knows the practical disabilities and hence shows the practical-actual results considering all the losses
-
-
SIMULATION APPROACH
-
Finite Element Analysis :
Simulation approach consists of considering the same test in Analysis software. For the Same Purpose, Ansys Version
18.1 is used. The analysis is done on Carbon Fiber Pin which is Rub on plate of Grey Cast Iron.
Figure 5 Pin on Disk Setup Created in Ansys Design Moduler
Figure 6Fine Mesh Setting
-
Validation with Experimental Results :
According to Simulation,
The Deformation in the Length of Pin is 1.39mm. Consider it as,
Deformed Length, Ld = 1.39 mm Diameter of Pin, d = 10 mm
In such case, the Deformed Volume which is also the wear volume can be calculated as,
Vw = (/4) x d2 x Ld
Henceaccording to Simulation, the wear volume can be stated as,
Vw= 109.115 mm3
V CONCLUSIONS
In the present work the investigations of wear and friction characteristics of aluminum matrix and polymer matrix material for clutch plate is carried out on pin on disk apparatus under different testing conditions.
It is observed that AL6061 shows very less coefficient of friction but wear volume is very high. As per requirement of clutch plate material S glass fiber shows significantly higher coefficient of friction i.e. about 0.2 and also it shows very less wear volume ie. 45 mm3 compared to aluminum matrix. So it can be concluded that S Glass fiber can be used for clutch plate material.
Figure 7Pre Analysis Setting
ACKNOWLEDGMENT
The report is outcome of guidance, moral support and devotion bestowed on me throughout my work. For this I acknowledge and express my profound sense of gratitude and thanks to everybody who have been a source of inspiration during the experimentation. The consistent guidance and support provided by Dr A.B Kakade thankfully acknowledged and appreciated for the key role played by him in providing me with his precious ideas, suggestions, help and moral support that enabled me in shaping the experimental work.
REFERENCES
Figure 8 Results of Maximum Deformation at Load of 2kg
Figure 9 Results of Maximum Stress and Strain Produced at Load of 2kg
-
QianZouet.al., Investigation of surface characteristics and tribological behavior of clutch plate materials, Elsevier Publication, Wear 302, 2013.
-
AravindVadiraj Engagement characteristics of a friction pad for commercial vehicle clutch system, Indian Academy of Sciences, Vol. 35, Part 5, pp. 585595, October 2010.
-
A. Mr. Dattatray B. Jondhale, B. Prof. Vishnu S. Aher, Experimental Evaluation of Clutch Plate Material by Tribological Properties Using Trobometer, International Engineering Research Journal.
-
Miss Kaveri. S. Kadam, Tribological Investigation of Ferodo Lining Material Embedded with Copper and SiC particles Fo Clutch plate International Engineering Research Journal Page No 1810-1816.
-
G.Kannan, K.Krishnamoorthy, K.Loheswaran, Review on Different Materials Utilized in Clutch Plate, South Asian Journal of Engineering and Technology Vol.2, No.23, Pg. 135 142 ,2016.
-
S. Gouseseema begum, A. Balaraju, Design and Analysis of Friction Clutch Plate using Ansys, International Journal of Advanced Engineering Research and Science (IJAERS) , Vol-2, Issue-5, May- 2015.
-
Virendrakumarpatel et.al. . Review on Wear Analysis of Different Types of Clutch Material, International Journal of Research in Advent Technology, Vol.3, No.11, November 2015.
-
Ravikiran M. Tate, Design and Analysis of Clutch Plate for Automatic Single Plate Clutch, IJSRD – International Journal for Scientific Research & Development, Vol. 3, Issue 09, 2015.
-
B. Nivas et.al. Design and Analysis of Clutch Plate Using Steel Material [En Gjs-400 -15steel], IOSR Journal of Dental and Medical Sciences (IOSR-JDMS), Volume 13, Issue 5, PP 76-78, May. 2014.
-
J Joy Mathavan and Amar Patnaik, Analysis of wear properties of aluminium based journal bearing alloys with and without lubrication, IOP Conf. Series: Materials Science and Engineering, 2016.
-
Sandip B. Chaudhari et.al. Wear Analysis of Polytetrafluoroethylene (PTFE) and its Composites under Wet Conditions, IOSR Journal of Mechanical and Civil Engineering (IOSR-JMCE), Volume 8, Issue 2,Pg 07-18 Jul. – Aug. 2013.
-
K.C.Lathiya, et.al. A Literature Review on Failure in Single Plate Clutch System, IJSRD – International Journal for Scientific Research & Development, Vol. 2, Issue 10, 2014.
-
Mamta G. Pawar, Monarch K. Warambhe, Gautam R. Jodh, Design and Analysis of Clutch Using Sintered Iron as a Friction Material, International Journal of Innovative Technology and Exploring Engineering (IJITEE), Volume-3, Issue-7, December 2013.
-
Zeyaullah Ansari, Investigation of Stresses of Friction Clutch Plate on Different Material, International Journal of Innovative Research in Science, Engineering and Technology, Vol. 6, Issue 3, March 2017.
-
N. A. Barve, Analysis of Single Plate Friction Clutch Using Finite Element Method, International journal of advance scientific research and engineering trends, Volume 2, Issue 11, JUNE 2017 .
-
P. Anusha Lakshmi, Design and Material Optimization of Mahindra XYLO E6 Clutch, International Journal of Advanced Technology and Innovative Research, Vol.09, Issue.07, Pages: 1040-1045, June-2017.
-
Avital Gabriel de Almeida Rosaa, JéfersonAparecidoMoreto, Study on Friction and Wear Behavior of SAE 1045 steel, reinforced Nylon 6.6 and NBR Rubber Used in Clutch Disks Journal of Materials Research, Volume 17(6), Page 1397-1403, 2014.
-
T. Vijayarajet.al., Design and structural Analysis of Conventional Clutch and flywheel Assembly, International Journal of Advance Research and Innovative Ideas in Engineering, Vol-3 Issue-5 2017.
-