
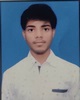
- Open Access
- Authors : Prashant Singh , Abhishek Kumar , Shushant Singh , Rajeev Rajput, Chhabi Lal Singh
- Paper ID : IJERTV9IS090423
- Volume & Issue : Volume 09, Issue 09 (September 2020)
- Published (First Online): 29-09-2020
- ISSN (Online) : 2278-0181
- Publisher Name : IJERT
- License:
This work is licensed under a Creative Commons Attribution 4.0 International License
Use of Plastic Waste in Flexible Pavement-Green Highway
Prashant Singp, Abhishek Kumar2, Shushant Singp, Rajeev Rajput4
1,2,3,4 M. Tech
Department of Civil Engineering
J.S. University, Shikohabad, Firozabad, India
Chhabi Lal Singp 5Assistant Professor
Department of Civil Engineering
-
University, Shikohabad, Firozabad, India
AbstractToday, plastic waste and its disposal Such as wrappers of chocolate, chips, carry bags, cold drink bottles and all other forms of plastic create significant environmental and economic problems. These forms of plastic consume massive energy-depleting in the environment in various ways. So manufacturing firms and construction industries, the use of plastic is a priority to handle and pack things comfortable due to its lightweight, effectiveness cost, and strength. The plastic waste used is poly-ethylene, poly-styrene, poly-propylene, the temperature varying between 120ºc – 160ºc gives the softening point of these plastics. The plastic waste is shredded & coated over the aggregate and mixed with hot bitumen and the resulted mix is used for pavement construction this mix will not only strengthen the pavement and also increases its durability. The main objective of this paper is to discuss the importance of plastic in terms of cost reduction, increases the strength and durability when these plastics are heated and coated upon the aggregates to reduce the air voids with plastic and binds with aggregate to provide stability. Its economical and eco-friendly.
KeywordsFlexible pavement, aggregate, plastic waste, plastic modified bitumen and plastic modified aggregate
-
INTRODUCTION
In India have many problems with the disposal of plastic waste and its very dangerous for human health and animals also, the availability of the waste plastics is enormous, as the plastic materials have become a parcel of daily life. If it is not recycled, their present disposal is either by land filling or by incineration. Then both these processes have a certain impact on the environment. So we got an idea the plastic waste is used in road construction. India is using waste plastic in road construction is relatively new. The laboratory tests have shown positive results when a small amount (5 to 10% by weight of plastic is incorporated in bituminous mixes asphalt), resulting in improvement pavement stability, strength, and durability. Plastic can be divided into two major categories- thermoses & thermoplastics. Thermoses have high durability and strength because it solidifies irreversibly when heated, henceforth can be used primarily in construction application. Plastic is a non-degradable waste, causes the greenhouse effect and global warming. The different experiments have been carried out whether the waste plastic can be reused productively. The various literature indicated that the waste plastic when added to hot aggregates, will form a fine coat of plastic over the aggregate, and such aggregates when mixed with a binder is found to have higher strength, higher resistance, and better performance over some time. It is economical and eco-friendly. India has promoted the use of
waste plastic in flexible pavement mixes for the construction of its National Highways and Rural roads and has approved it as a default mode of periodic renewal with a hot mix for roads within 50km periphery of urban areas with more than 50000 Population (Government of India, 2015; National Rural Road Development Agency, 2019). The Indian Road Congress (2013) has published guidelines for the use of waste plastic in hot bituminous mixes while National Rural Road Development Agency.
-
LITERATURE REVIEW
The use of plastic waste in flexible pavements would open up a solution for the disposal issues regarding plastics wastes. Many research works have been done in the area of use of plastic waste in bituminous road construction.
Dr. R. Vasudevan (2007) is an Indian scientist who has worked mainly in waste management. This method will help in making roads very faster and also will save the environment from dangerous plastic waste. He is also visited mahatma school on 15 April 2008. The road also shows greater resistance to damage caused by heavy rains. His road construction method is now widely used to construction Roads in the rural area. Dr. R. Vasudevan was awarded Indias fourth-highest civilian Honour Padma Shri.
Amit Gawande (2012) The concept of utilization of waste plastic in the construction of flexible road pavement has been done since 2000 in India. In the construction of flexible pavements, bitumen plays the role of coating over the aggregate and binding the aggregate together. It also helps to improve the strength and life of road pavement. But its resistance towards water is poor. It is a method to enhance the quality of bitumen by modifying the chemical properties of bitumen by blending with synthetic polymers. The use of plastic waste in the bitumen is similar to polymer-modified bitumen.
-
SCOPE
-
To eradicate potholes.
-
To minimize global warming, greenhouse gases, and pollution.
-
The lifespan of the roads can be increased.
-
Eco-friendly in nature.
-
-
OBJECTIVES
This study is conducted with the main objective.
-
Reducing the plastic waste present in our environment and making solid waste management better.
-
To carry out the soil test.
-
To reduce the cost of road construction.
-
To design the flexible pavement.
-
To increasing the various properties of road materials.
-
To design the asphalt pavement with the aggregate- plastic-bitumen mix.
-
To prepare a statistical model for the optimum utilization of plastic waste.
-
To coat the aggregate with plastic and incorporate titanium dioxide.
-
-
METHODOLOGY
-
Use of Materials
-
Bitumen – 60/70,80/100 grade bitumen was used for the present study the important quality of bitumen which has made bitumen a popular material is its excellent binding property and get soften when heated. The bitumen for bituminous mixes for wearing course with waste plastic shall comply with the Indian Standard Specifications for viscosity graded paving bitumen IS 73. Guidelines for selection for the grade of viscosity graded paving bitumen shall be under the IRC:111-2009.
TABLE I. VISCOSITY OF 80-100, 60-70 AND PG 76 GRADED NEAT ASPHALT BINDER
Type of asphalt
Viscosity, cP
Ratio of Viscosity 0 0
135 C/165 C
At 0
135 C
At 0
165 C
80-100
268.7
106
3.47
60-70
425
150
2.83
PG 76
1600
675
2.37
-
Aggregate – The aggregate is one of the important materials used for flexible pavement construction. The property selected and graded aggregates are mixed with bitumen to form hot mix asphalt (HMA) pavement. Two types of aggregate are used like course & fine and size used 20mm and 10mm.
Fig. 1. 10mm course aggregate
Fig. 2. 20mm course aggregate
Fig. 3. Fine aggregate
-
Filler – The filler for dense graded mixes shall comply with IRC :111-2009. 6mm and stone dust & lime Used as filler.
Fig. 4. 6mm filler
-
The plastic waste shall conform to the size passing 2.36 mm sieve and retained on 600 micron sieve.
-
Dust and other impurities shall not be more than 1 percent.
-
To make out the ability of plastic to mix with the binder, the melt-flow value shall be tested as per
Waste plastic – Plastic is one of the materials which enhanced its binding property when softened, Hence, this softened plastic material can be used as an effective binder in bitumen.
ASTM D 1238-2010, for which the range shall be as follows:
For LDPE: 0.14-58 gm/10 min For HDPE: 0.02-9.0 gm/10 min
TABLE II. WASTE PLASTIC AND ITS SOURCE
Waste Plastic
Origin
Low-Density Polyethylene (LDPE)
Carry bags, sacks, milk pouches, bin lining, cosmetic, and detergent bottles.
High-Density Polyethylene (HDPE)
Carry bags, bottle caps, household articles, etc.
Polyethylene Terephthalate (PET)
Drinking water bottles etc.
Polypropylene (PP)
Bottle caps and closures, wrappers of detergent, biscuit, wafer packets, microwave trays for the readymade meal, etc.
Polystyrene (PS)
Yogurt pots, clear egg packs, bottle caps. Foamed Polystyrene: food trays, egg boxes, disposable cups, protective packaging, etc.
Polyvinyl Chloride (PVC)
Mineral water bottles, credit cards, toys, pipes and gutters; electrical fittings, furniture, folders and pens, medical disposables; etc.
-
-
Design Mix
-
Dense graded mixes – The properties for dense graded mixes are indicated in table-III.
TABLE III. REQUIREMENTS FOR WASTE PLASTIC MODIFIED DENSE GRADED BITUMINOUS PAVEMENT LAYERS
Minimum stability (kN at 60°C)
12.0
Minimum flow (mm)
2
Maximum flow (mm)
4
Marshall Quotient (KN/mm)
2.5-5
Compaction level (Number of blows)
75 blows on each of the two faces of the specimen
Percent air voids
3 – 5
Retained stability (%)
98
ITS (min) MPa
0.9
VMA
16
VFB
65-75
Quantity of waste plastic % by weight of plastic
6 to 8 depending on low rainfall or high rainfall areas
-
Open graded mixes – Waste Plastic 6 to 8 percent of the weight of the bitumen can be used for Open-Grade Premix Surfacing and Mix Seal surfacing mix. The quantity of bitumen can be reduced correspondingly. An open graded cold mix is a coarse aggregate mix (very small amount of fine aggregate) with a large number of air voids to allow for water to drain. These mixes can be used as a surface course and show excellent resistance to fatigue, reflection cracking, rutting, and shoving. Open-graded mixes are useful for restoration at varying depths, either mixed in place or stockpiled
-
-
Manufacturing of Bituminous Mix Using Waste Plastic
Bituminous hot mixes using waste plastic for road construction are manufactured using either a dry process or a wet process. The dry process is considered to be simple, economical, and environmentally friendly, while the wet
process requires more investment and machinery, and hence is not commonly used.
The scope of the present guidelines is restricted to the dry process only for the following reasons;
-
Plastic is coated over stones improving the surface property of aggregates.
-
The coatings easy & the temperature required is the same as road layingtemp.
-
Use waste should be 6-8 percent by weight of bitumen depending on the climatic conditions of high and low rainfall areas.
-
Flexible films of all types of plastics can be used.
-
Doubles the binding property of aggregates.
-
No new equipment is required.
-
Bitumen bonding is stronger than normal.
-
The coated aggregates show increased Stability of the mixes.
-
Better performance after construction is based on the experience gained for medium-level city traffic.
-
No evolution of any toxic gases as maximum temperature is 180°C.
-
Dry process – In the dry process, the processed waste plastic is shredded and added to the hot aggregate (in figure- 6, when lines a, b and d are opened, keeping c and eclosed). The Indian Road Congress and National Rural Roads Development Agency. indicate that the shredded waste plastic size should preferably be 2-3 mm for better spread and coating on the aggregate. Dust and other impurities should not exceed 1%. The shredded waste plastic is then added to the aggregates that are heated to 170ºC. The shredded waste plastic softens and melts to form a coating around the aggregates (Sahu and Singh, 2016). The bitumen is also heated to 160ºC, then the plastic-coated aggregates are mixed with bitumen and used for road construction.
In order to ensure that the quality of the finished waste plastic product is consistent the following process must be adhered to before considering its use in bituminous construction:
-
Collection of waste plastic.
-
Cleaning and shredding of waste plastic.
-
Shredding Machine.
-
Mixing of shredded plastic waste, aggregate and bitumen in central mixing plant.
-
-
Wet process – In the wet process, the processed waste plastic in powder form is added to the hot bitumen (in figure 6, when lines c and e are opened, and a, b and d are closed).
The powdered waste plastic is directly mixed with bitumen before adding them to the aggregates. It has to be ensured that there is an even mix of plastic and bitumen, and the temperature range for this method is 155ºC to 165ºC. Sahu and Singh (2016) suggest a 6-8% of waste plastic powder within the bitumen mix
-
Process Details –
-
Collection of waste plastic :- Waste plastic is collected from roads, garbage trucks, dumpsites or compost plants, or from school collection programs, or by purchase from rag- pickers or waste-buyers
Fig. 5. Collection of waste plastic
Fig. 6. Sketch of the wet and dry processes in an asphalt plant
-
Cleaning and shredding of waste plastic :- Plastic waste litter in the form of thin-film carry-bags, use-and-throw cups, PET bottles, etc. these are sorted, de-dusted, washed if necessary.
Fig. 7. Cleaning and shredding of waste plastic
-
Shredding machine :- Plastic waste which is cleaned is cut into a size between 2.36 mm and 600 microns and of maximum size 2.36 mm length and 2.00 mm width using a shredding machine.
Fig. 8. Shredding machine
-
Mixing of shredded waste plastic,aggregate and bitumen in central mixing plant :- The aggregate mix is heated to 135-170°C in a Central mixing plant. The requisite percentage of plastic waste to the weight of bitumen is injected with a pipe under compressed air in the drum of a drum mix plant through a pipe at 2/3 length of the drum or through an opening over the pugmill in the case of a batch mix plant. The waste plastic initially coats the heated aggregates. In the next stage, bitumen is added to the aggregates, the temperature of the binder shall conform to the temperature depending on the grade of binder and the type of mix. The plastics waste coated aggregate is mixed with hot bitumen for 15 secs and the resulting mix transported for road construction. The central mixing plant helps to have better control of temperature and mixing of this material thus helping to hav a uniform coating and heated bitumen is also sprayed.
Fig. 9. Central mixing plant
-
Pavement and laying of bituminous mix :- The road laying temperature is between 110°C to 120°C for the waste plastic bituminous mix. The roller used, may be of any specified capacity.
Fig. 10. Sketch of the wet and dry processes in an asphalt plant
-
-
-
-
RESULT AND DISCISSION Dry process (Lab test-D.B.M II Grade)
-
Plastic wastes are cleaned and dried (For ex: disposed carry bags, glasses etc) with a thickness of 60 microns is shredded into small pieces (2.36 mm – 4.75 mm size).
-
Aggregate are weighed as shown in Figure 2 and are heated to 160C in a pan.
Designation
Test result
Permissible limit
Test method
Specific gravity of bitumen
1.025
0.99 min
IS: 1202 –
1978
Softening point of bitumen
54.35C
47 C (min)
IS: 1205 –
1978
Flash point of bitumen
272C
220 C (min)
IS: 1209 –
1978
Fire Point of Bitumen
300C
270 C (min)
IS: 1209 –
1978
Bitumen Penetration Test
50 mm
45 (min)
IS: 1203 –
1978
Ductility test
94 cm
100
IS: 1208 –
1978
Designation
Test result
Permissible limit
Test method
Specific gravity of bitumen
1.025
0.99 min
IS: 1202 –
1978
Softening point of bitumen
54.35C
47 C (min)
IS: 1205 –
1978
Flash point of bitumen
272C
220 C (min)
IS: 1209 –
1978
Fire Point of Bitumen
300C
270 C (min)
IS: 1209 –
1978
Bitumen Penetration Test
50 mm
45 (min)
IS: 1203 –
1978
Ductility test
94 cm
100
IS: 1208 –
1978
TABLE IV. PHYSICAL PROPERTIES OF BITUMEN AS IS 73 : 1992
TABLE V. SIEVE ANALYSIS
Sieve size
Upper limits
Lower limits
Mid limits
Result
37.5
100
100
100
100.00
26.5
100
90
95
100.00
19
95
71
83
93.89
13.2
80
56
68
71.29
4.75
54
38
46
42.69
2.36
42
28
35
29.41
0.3
21
7
14
10.53
0.075
8
2
5
4.18
TABLE VI. AGGREGATE TEST RESUL
Designation
Test result
Permissible limit (Morth Specification)
Test method
Aggregate Impact Value Test
23.80
Max 30%
IS: 2386 Part IV
Specific Gravity of Aggregates (20 mm)
2.68
IS: 2386 Part III
Specific Gravity of Aggregates (10 mm)
2.71
IS: 2386 Part III
Specific Gravity of Aggregates (6 mm)
2.69
IS: 2386 Part III
Specific Gravity of Aggregates (stone dust)
2.74
IS: 2386 Part III
Stripping Value of Aggregates
45%
5%
Physical appearance
Water Absorption
0.40
Max 2%
IS: 2386 Part III
-
Marshall Sampling Mould
The specifications of the Marshall sampling mould and hammer are given in table 7
TABLE VII. DIMENSIONS OF MARSHALL SAMPLING MOULD AND HAMMER
Apparatus
Value
Working tolerance
Mould
Average internal diameter, mm
101.2
0.5
Hammer
Mass, kg
4.535
0.02
Drop height, mm
457
1.0
Foot diameter, mm
98.5
0.5
Fig. 11. Marshall sampling mould
Fig. 12. Marshall hammer
Fig. 13. Marshall sample
Fig. 14. Closer view of a marshall sample
-
-
CONCLUSION
-
-
Use of waste plastic in flexible pavements shows good result when compared with conventional flexible pavements.
-
The polymer coated on aggregates reduces the voids and moisture absorption.
-
The plastic pavement can withstand heavy traffic and also durable than flexible pavement.
-
The use of plastic mix will reduce the bitumen content by 10% and increases the performance and strength of the road.
-
It shows that with the increase of plastic waste in bitumen increases the properties of aggregate and bitumen.
-
This technique is very eco-friendly as it uses the waste plastic which is being disposed in oceans, landfills etc.
ACKNOWLEDGEMENT
This piece of work would never be accomplished without God Almighty. For it is under his grace that I Live, learn and flourish. This report owes its existence to help, support and inspiration of our guide Amit Kumar Yadav, Assistant Professor & Head, Department of Civil Engineering, J.S. University Shikohabad, Firozabad and Chhabi Lal Singh, Assistant Professor, Department of Civil Engineering, J.S. University Shikohabad, Firozabad.
I am also thankful to Devashish Chandra, Assistant Professor of Civil Engineering for their valuable suggestion, supports and encouragement during the course of my project work.
I am thankful to all staff members of Geotechnical Engineering Laboratory For their assistant and co- operation during the course of experimentation.
Also, thanks to The help and encouragement received from my friends, Salil, Abhishek, Sandeep, Devendra regarding the concepts and experimentations.
Last, but not the least, I would like to thank my loving parent for their encouragement and co-operation during the time of working through this project.
REFERENCES
Marshall Stability value
MarshallStabilityvalue(kN)
MarshallStabilityvalue(kN)
20
18
16
14
12
10
8
6
4
2
0
0 1 2 3
Polythene content (%)
4 5 6
-
Vasudevan, R., Nigam, S.K., Velkennedy, R., Ramalinga, A., Sekar, C. and Sundarakannan, B. (2007) Utilization of Waste Polymers for Flexible Pavement and Easy Disposal of Waste Polymer.
-
Vasudevan, R. (2004). "Use of plastic waste in construction of tar road." Enviromental information system (Envis), Indian Centre for Plastics in the Environment.
-
Indian Road Congress (2013). Guidelines for the Use of Waste Plastic in Hot Bituminous Mixes (Dry Process) In Wearing Courses. India.
-
"Rheology and storage stability of modified binders with waste polymers composites." Road Materials and Pavement Design 20(4): 773-792.
-
Utilization of Waste Plastic in Asphalting of Roads. Scientific Reviews & Chemical Communications, 2, 147-157.
-
L.R Schroceder, The Use of Recycled Materials in Highway construction, Public Roads, Vol 58(Issue 2), 1994.
-
Bahia, H.U. and Anderson, D.A., Strategic highway research program binder rheological parameters: Background and comparison with conventional properties. Transport. Res. Rec. 1488, 1995, 32, 39.Vasudevan R., Nigam S.K., Velkennedy R., Ramalinga Chandra Sekar A., Sundarakannan B.
Fig. 15. Marshall stability value vs. polythene content
-
Shankar, A., K. Koushik and G. Sarang (2013). "Performance studies on bituminous concrete mixes using waste plastics." Highway Research Journal 6(1).
-
SaurabhTayde, Utilization Of Waste Plastic In Asphalting Of Roads, Department of Chemical Engineering College of Engineering and Technology, NH-6, Murtizapur Road, Babhulgaon (Jh) AKOLA
444104 (M.S.) INDIA Department of Civil Engineering College of Engineering and Technology, NH-6, Murtizapur Road, Babhulgaon (Jh) AKOLA 444104 (M.S.) INDIA.
-
AvulaVamshi, Use of waste plastic in construction of Bituminous road, Journal of Engineering (JOE) ISSN: 2325-0224.