
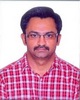
- Open Access
- Authors : Ankur C Bhogayata , Shemal V Dave
- Paper ID : IJERTV10IS100006
- Volume & Issue : Volume 10, Issue 10 (October 2021)
- Published (First Online): 05-10-2021
- ISSN (Online) : 2278-0181
- Publisher Name : IJERT
- License:
This work is licensed under a Creative Commons Attribution 4.0 International License
Utilization of Taguchi Method of Optimization in the Mix Design Development of High Strength Alkali Activated Concrete
Ankur C. Bhogayata Department of Civil Engineering Marwadi University
Rajkot Gujarat, India
Shemal V. Dave
Department of Civil Engineering Marwadi University Rajkot Gujarat, India
Abstract A rapid growth of the infrastructural development has witnessed increased consumption of Ordinary Portland Cement (OPC) in making of the high strength mixes and the environmental challenges due to the higher carbon footprints of OPC. Eventually, as an alternative the high strength-alkali activated concrete (HSAAC) has been recognized globally with the potential to mitigate energy consumptions and as a sustainable option. The Taguchi method is one of the methods to fulfil the requirement and not explored to an extent in the field of concrete mix design also. Therefore, in the present work, the Taguchi method has been employed to obtain the HSAAC with the design target strength of more than 50 MPa. Several design mixes have been proposed and the selection process of the most effective combination has been established. All the necessary levels of the method have been utilized and suggested. The analysis helped to understand the individual contribution by the major components in the strength gaining mechanism that is another novelty of the work presented here. The observations confirmed the potential of Taguchi method in predicting the design mix proportions of the HSAAC.
KeywordsGeopolymer, Taguchi Method, Optimization, Mix designof concrete
-
INTRODUCTION
Modern construction composites, such as Alkali Activated Concrete (AAC), have gained maximum momentum in the past few years. It is unequivocally true that AAC has proved to be an effective alternative of OPC-based concrete owing to its special characteristics such as early strength gain, longevity and lower carbon footprint [1]. On the other hand, however, despite all the merits of AAC, its application is still very rare due to the unavailability of standard mix design [2]. Ergo, the rational mix design for the AAC has remained an area of detailed investigation. Furthermore, looking at the current demand for civil engineering structure, high strength concrete has become a paramount area for detailed investigation. To develop high strength concrete, a huge amount of cement is required, which can significantly impact global environment. Thus, it is required to develop high strength-sustainable concrete composite such as AAC which can mitigate the negative ramifications of cement concrete. Mix design of High strength Alkali Activated Concrete (HSAAC) is quite conundrum task as it depends upon multiple variables [3]. To exemplify, rheological, mechanical and durability properties of HSAAC are influenced by concentration of sodium hydroxide (NaOH) and its proportion with sodium silicate (Na2SiO3) [4], temperature
for curing [5], liquid to binder ratio [6], concentration of Al and Si in ingredients [7]. The HSAAC has been found very sensitive towards the variation of the chemical compositions and proportions of the constituents also. The other challenge is to find the optimum proportion and combination of all the constituents to prepare HSAAC. There are several mix designs available for the HAAC concrete but rare of them focus on the mix design of constituents based on the target mean strength. The reason is, it requires good number trials to find the effects of each ingredient on the fresh and hardened properties of HSAAC. The reason is, it requires good number trials to find the effects of each ingredient on the fresh and hardened properties of HSAAC. Therefore, there is a need felt to devise a method for the mix design of HSAAC capable of reducing the time, efforts, resources and energy. The Taguchi method is one of the optimization tools which can be successfully utilized for the mix design of the composites, including the cement-based concretes [8]. In the current experimental investigation, efforts are made to employ the Taguchi method to obtain the optimum proportions of the constituents for the specific mix design of the HSAAC. The input parameters have been selected based on the degree of influence on the target properties of HSAAC in the fresh and hardened state. The IS: 10262-2019 code is referred to initiate the mix design, and the results of the mix prepared as per the Taguchi method are utilized to compare the effectiveness of the Taguchi method for the HSAAC mix design.
-
MATERIALS AND METHODOLOGY
-
Materials
For this experimental work, low calcium class F Flyash (FA) conforming to the requirements of ASTM C618-08 was utilized as the primary alumino-silicate binder. The FA was purchased from the Wanankbori thermal power plant, Gujarat, India. Along with FA, two other pozzolanic binders namely grounded granulated blast furnace slag (GGBFS) and silica fumes (SF) were added to cure the HSAAC at ambient temperature and refine the matrix at smaller level. It was observed that the CaO content presents in GGBFS can help to accelerate polymerization process by liberating heat after reacting with water. Furthermore, the CaO content produces C-S-H gel along with N-S-H/N-A-S-H gel produced by FA
[8] (Refer Figure 1). On the flip side, however, higher fraction of GGBFS can lead to development of shrinkage cracks due to early polymerization. Therefore, it is requiredto find optimum dosage of GGBFS in HSAAC. On the contrary, the micro particles of SF react more quickly with the alkaline solution and initiate the early polymerization process to form a denser and refined matrix. As far as aggregates are concerned, the natural sand belonged to zone 3 as per IS: 383:2016 was used in surface saturated dry (SSD) condition as a fine aggregate. The specific gravity of sand was measured as 2.75 and the water absorption rate was approximately 1%. The coarse aggregates were of size 20mm with 2.75 specific gravity, and 0.6% water absorption rate and 10mm with 2.7 specific gravity and 0.6% water absorption rate. The superplasticizer was added to enhance the early workability of AAC. To activate above mentioned pozzolanic binders, sodium-based alkaline solutions were used. To prepare the solution a combination of sodium hydroxide (NaOH) in pellet form and sodium silicate (Na2SiO3) of A 53 grade (Na2O = 14.7%, SiO2 = 29.4% and H2O = 55.9% by mass) in viscous liquid form was used. The pellets of sodium hydroxide were dissolved in distilled water as per required molar content and mixture was steered until the pellets get dissolved in water. Lastly, the liquid sodium silicate was added to prepare an alkaline solution.
Figure 1 SEM image of AAC mixture
-
Methodology
The design guidelines of IS 10262:2019 was adopted to develop different trial mixes of HSAAC. IS 10262:2019 contains most of the provisions which affects rheological and mechanical properties of HSAAC such as target mean strength, the maximum size of aggregate, exposure condition, fineness of binders, required workability, method of concreting, specific gravity and water absorption rate of coarse and fine aggregate, a zone of sand and so on. Conversely, the code does not provide calculations for other strength governing parameters such as binder fraction, alkaline solution to binder ratio, sodium silicate to sodium hydroxide ratio and finally curing condition adopted. Thus, the Taguchi method was used to fix the optimum combination of different factors and their levels for M50 grade of concrete composite. Four different factors that are binder combination, Alkaline solution to binder rato, sodium silicate to sodium hydroxide ratio, and curing techniques have been selected. Each factor was varied at three different levels. Dr. Taguchi has proposed many orthogonal arrays based on several factors and their levels. However, for this
experimental work, L9 orthogonal array was selected (refer table 1) as there are only four parameters that vary at three different levels. The molarity of sodium hydroxide was kept constant as 16M for all 9 trial mixes. All the factors and their respective levels are mentioned in Table 2.
TABLE 1 L9 ORTHOGONAL ARRAY
Trial
Factor A
Factor B
Factor C
Factor D
T1
1
1
1
1
T2
1
2
2
2
T2
1
3
3
3
T4
2
1
2
3
T5
2
2
3
1
T6
2
3
1
2
T7
3
1
3
2
T8
3
2
1
3
T9
3
3
2
1
TABLE 2 INFLUENCING PARAMETERS AND LEVELS
Factor
Level 1
Level 2
Level 3
A: Binder Content
B1*
B2*
B3*
B: Solution/ Binder ratio
0.55
0.5
0.45
C: Na2SiO3/NaOH ratio
3
2.5
2
D: Curing Technique
Ambient
Oven
Hot water
B1 = 60% GGBFS, 30% FA, 10% SF, B2= 50% FA, 40% GGBFS, 10% SF, B3 = 40%FA, 50%GGBFS, 10% SF
-
-
RESULTS AND DISCUSSION
-
Mechanical Properties of HSAAC
To evaluate the mechanical strength of HSAAC, compressive, splitting tensile and flexural strength were conducted as per the procedure mentioned in IS 516:1959 and IS 5816:1999. All the test were conducted at the age of 7day of casting. The results are mentioned in Table 3. The results were analysed as per Taguchi mechanism in Minitab software considering signal to noise ratio as higher is better. The outcome is represented in Figure 2.
Figure 2 signal to noise ratio: Higher is better based
TABLE 3 AVERAGE STRENGTH RESULTS
ACKNOWLEDGMENT
The researchers are thankful to the department of civil engineering and Marwadi University, Rajkot, Gujarat, India for providing all the laboratory facilities and support with every possible means to conceptualize and carry out the experimental and analytical work required for the present study.
-
-
CONCLUSION
After experimental investigation of physical and mechnical properties of HSAAC, following conclusion can be drawn:
-
Binder content B2 showed better mechanical strength.
-
Solution to binder ratio = 0.55 showed better mechanical strength.
-
Silicate to hydroxide ratio = 2 showed better mechanical strength.
-
Oven curing showed better mechanical properties.
In all the cases silicate to hydroxide ratio proved to be most influencing parameter. From the study, it was also observed that the microstructural bonding characteristics were largely influecned by the presence of the content of the hydroxide and the strength of the alkaline activators. The strength of the alkaline activtors were inflenced by the molar content of the sodium hydroxide. The solution of the activators plays a key role and therefore the balanced ratio of the sodium silicate and sodium hydroxide must be investigated with utmost care and stury of the relevant other research works as presented and dicussed in the study.
REFERENCES
-
Duxson, P. et al., (2007) Geopolymer technology: the current state of the art. Journal of materials science 42(9): 2917-2933. https://doi.org/10.1007/s10853-006-0637-z
-
Reed, M., Lokuge, W. and Karunasena, W., (2014) Fibre- reinforced geopolymer concrete with ambient curing for in situ applications. Journal of materials science 49(12):4297-4304. https://doi.org/10.1007/s10853-014-8125-3
-
Nath, P. and Sarker, P.K., (2014) Effect of GGBFS on setting, workability and early strength properties of fly ash geopolymer concrete cured in ambient condition.
Construction and Building Materials 66:163-171. https://doi.org/10.1016/j.conbuildmat.2014.05.080
-
Yang, K.H., Song, J.K. and Song, K.I., (2013) Assessment of CO2 reduction of alkali-activated concrete. Journal of Cleaner Production 39: 265-272.
https://doi.org/10.1016/j.jclepro.2012.08.001
-
Palomo, A., Grutzeck, M.W. and Blanco, M.T., (1999) Alkali- activated fly ashes: a cement for the future. Cement and concrete research 29(8):1323-1329. https://doi.org/10.1016/S0008- 8846(98)00243-9
-
Kumar, S. and Kumar, R., (2011) Mechanical activation of fly ash: Effect on reaction, structure and properties of resulting geopolymer. Ceramics International 37(2):533-541. https://doi.org/10.1016/j.ceramint.2010.09.038
-
Alomayri, T., Shaikh, F.U.A. and Low, I.M., (2014)Mechanical and thermal properties of ambient cured cotton fabric-reinforced fly ash-based geopolymer composites. Ceramics International 40(9):14019-14028. https://doi.org/10.1016/j.ceramint.2014.05.128
-
Nath, P. and Sarker, P.K., (2015) Use of OPC to improve setting and early strength properties of low calcium fly ash geopolymer concrete cured at room temperature. Cement and concrete composites,55:205-214. https://doi.org/10.1016/j.cemconcomp.2014.08.008