
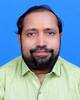
- Open Access
- Authors : Narayanan. N. I , Sauvik Banerjee , Akshay Prakash Kalgutkar , T. Rajanna
- Paper ID : IJERTV10IS070251
- Volume & Issue : Volume 10, Issue 07 (July 2021)
- Published (First Online): 28-07-2021
- ISSN (Online) : 2278-0181
- Publisher Name : IJERT
- License:
This work is licensed under a Creative Commons Attribution 4.0 International License
Vibration Analysis of FG Plate
Narayanan. N. I 1,2,* , Sauvik Banerjee1, Akshay Prakash Kalgutkar1, T. Rajanna3 1Department of Civil Engineering, Indian Institute of Technology, Bombay 400076, India 2 Government College of Engineering, Kannur, Kerala -670563, India
3 B.M. S. College of Engineering, Bengaluru, Karnataka-560019, India
Abstract-In this article, vibration response of func- tionally graded material(FGM) plates are investigated by finite element formulation. By applying the Hamiltons principle, the governing equations of the FGM plates are derived based on the first-order shear deformation the- ory. The FGM plate is modelled by using 9-noded heter- osis element by incorporating the effect of rotary inertia and shear deformation. 9- noded heterosis plate element is used to formulate the elastic stiffness matrix and mass matrix. The results are also extracted from Abaqus CAE by using S8R5 shell elements. Free vibration analysis is done to obtain the different modes as well as the frequen- cies. Harmonic sine load is applied at the centre of the FGM plate to obtain a forced vibration response. Im- pulse forces of rectangular, triangular, and half-cycle sine shapes are applied on the top of the plate at the cen- tre and the Response spectra of C-Si C FGM plate is plot- ted.
Keywords-FGMs, Finite element method, heterosis plate element, Response spectra
-
INTRODUCTION
The diverse and potential applications of FGMs in aero- space, medicine, defence, energy, and other industries have attracted a lot of attention recently. The concept of function- ally graded materials (FGMs) were first demonstrated by a group of scientists in Japan in 1984during a space plane pro- ject[1]. Combination of materials used here served the pur- pose of a thermal barrier system capable of withstanding a surface temperature of 2000 K with a temperature gradient of 1000 K across a 10 mm thick section (Jha et al. [2]). Later, its applications have been expanded to also the components of chemical plants, solar energy generators, heat exchangers, nu- clear reactors, and high-efficiency combustion systems. The concept of FGMs has been successfully applied in thermal barrier coatings where requirements are aimed to improve thermal, oxidation and corrosion resistance. FGMs can also find application in communication and information tech- niques. Abrasive tools for metal and stone cutting are other important examples where the gradation of the surface layer has improved performance.
It has been found from the literature that not many studies are done to the vibration analysis of functionally graded plates.
B. Sidda Reddy et al. [3] carried out the free vibration analysis of functionally graded plates. The variations of the volume
fractions through the thickness are assumed to follow a power-law function. The Reissener-Mindlin first-order shear deformation theory is very much appropriate for thick plates [4]. It was taken to analyze the behaviour of the plate sub- jected to free and forced vibration. They have developed ana- lytical formulations and solutions for the free vibration anal- ysis of functionally graded plates using higher-order shear de- formation theory (HSDT). The principle of virtual work was used to derive the equations of equilibrium and boundary con- ditions. Naviers technique was used to obtain the solutions for FGM plates. Jyoti Vimal et al. [5] have studied the free vibration analysis of functionally graded skew plates using the finite element method. The first-order shear deformation plate theory is used to consider the transverse shear effect and rotary inertia. The properties of functionally graded skew plates are assumed to vary through the thickness according to a power law. It is found that when the length to thickness ratio of functionally graded skew plates increases beyond 25, the variation in the frequency parameter is very negligible and also found that a volume fraction exponent that ranges be- tween 0 and 5 has a significant influence on the frequency. M.
N. Gulshan Taj et al. [6] carried out a free vibration analysis of functionally graded material (FGM) skew plates subjected to the thermal environment. It was concluded that the volume fraction index and skew angle plays an important role in pre- dicting the vibration of FGM skew plate subjected to thermal load.
J. N. Reddy [7] have studied theoretical formulation and FEM model based on TSDT for FGM plate. The formulation ac- counted for thermo-mechanical effects combining change with time and geometric nonlinearity. In this higher-order the- ory, transverse shear stress was expressed as a quadratic func- tion along with the depth. Hence this theory requires no shear correction factor. The plate was considered as the homoge- nous and material composition was varied along with the thickness. The Young's modulus was assumed to vary as per rule of the mixture in terms of the volume fractions of the ma- terial constituents. Hughes and Cohen [8] developed the het- erosis element and elemental equation. They derived lumped positive definite mass matrix, element matrix and load vector and method for finding critical time step. High-accuracy finite element for thick and thin plate bending is developed, based upon Mindlin plate theory.
It has been found from the literature survey that not many re- searchers attempted to the vibration analysis of functionally graded plates. Further, we observed that many authors could
model such problems with a stepped variation in material properties instead of continuous variation. This would have happened because of the limitations of the commercial soft-
x
x
x
x
ware available. In this context, we felt that MATLAB code could be used for tailoring the continuous variation in material
y
y
y
(3)
properties in FE Modelling. Hence MATLAB code was de- veloped for vibration analysis of FG plate. The analysis was carried out for C-Si C FGM plate with different volume frac- tion indices. The results are compared with Abaqus CAE by using S8R5 shell elements.
-
PROBLEM FORMULATION
First-order shear deformation theory is used for plate for- mulation. Displacement variation is linear, across the plate thickness. But there is no change in plate thickness during de- formation. A further assumption is that the normal stress across the thickness is neglected. Properties are graded through the thickness direction which follows a volume frac- tion power-law distribution. The different elements of the plate are expected to undergo translational and rotational dis- placement. In the present work 9- noded heterosis element is used to discretize the plate.
-
Strain-Displacement Relations
The displacement field at any arbitrary distance z from the midplane based on the first-order shear deformation plate the- ory is given by
up (x, y, z), vp (x, y, z), wp (x,y,z) u0 (x, y), v0 (x, y), w0 (x, y) z x (x, y), y (x, y), 0
(1)
where, u p, v p, w p are displacements in x, y and z directions respectively, u0, v0 and w0 are the associated midplane dis- placements along x, y and z axes respectively. and x and y are the rotations about y and x-axes respectively.
The linear strain displacement relations are given by
xl u0,x zx
yl v0,y zy
xy x y
y x
The strain-displacement field at any distance z as shown i Figure.1.
zx
u
A
x
z B A
C B w
D
C y
D
Figure 1. Deformed and un-deformed beam
-
Finite element formulation
In the current work, the FGM plate has been discretized using 9-noded heterosis element with 5-degree of freedom (dofs) at all the edge nodes and 4 dofs at the internal node as shown in the Figure 2. The serendipity shape functions have been used for the transverse dofs, w, and Lagrange shape function are used in the remaining dofs, u, v, x, and y
8-N SE 9-N HE 9- N LE
Node with u, v, w, x, and y degrees of free-
dom
Node with u, v, x, and y degrees of freedom
Figure 2. Nodal configuration of the plate element
-
Resultant Forces and moments.
xyl u0,y v0,x zxy
xzl w0,x x
(2)
The analysis of FG plate is carried out to establish the relation between the forces and strains by considering transverse shear
yzl w0,y y
terms.
Constitutive matrix of the isotropic plate is
where, xl, yl and xyl are the linear in-plane normal and
Q11 Q12 0
shear strains, xzl and xzl are transverse shear strains, z is the
Q Q Q 0
(4)
distance of any layer from the middle plane of the plate and are the curvatures.
12 11
0 0 Q66
where,
Q11
E 1 2
, Q12
E 1 2
, Q66
21
The different participating element-level matrices such as elastic stiffness matrix ke , and consistent mass matrix me
E
E
The material properties PZ (Elastic constants E, , density) at distance, z from the middle surface of the plate is
have been derived using corresponding energy expression. The element elastic stiffness matrix and element mass matrix are derived using the following relations
P P P P (z / h) 0.5n P P P Vf (5) 1 1
z b t b b t b
where, h is the plate thickness, t and b denotes the top and the bottom surface z / 2 ,n is material volume fraction
index, Vf is volume fraction.
ke
T
T
1 1
1 1
BT CBJ dd
(11)
Stress-strain relationship is
Q
(6)
me N IN J dd
1 1
(12)
x y xy 0
x y xy 0
where, = , , T , = z
The in-plane resultant forces and moments in the kth layer are evaluated as
N zk
In which, [I] is the inertia matrix
-
Computer coding and Implementation
A computer program is developed using MATLAB to imple- ment the finite element formulation and include all the neces- sary parameters to investigate the vibration behaviour of the
N, M = 1, z dz
k 1 zk1
(7)
FGM plate. In the present code, selective integration scheme is incorporated for the generation of the element stiffness ma-
Resultant Transverse Shear Force on the kth layer is given by
trix. The 3×3 Gauss quadrature rule is adopted to get the bend- ing terms and 2×2 Gauss rule is used to solve shear terms to
Q N zk N zk Q Q
xz xz
xz xz
avoid possible shear locking. The mass matrix is evaluated by
dz
44 45 xz
using 3×3 Gauss rule [12].
dz
dz
Qyz
k1 z
yz k1 z Q45
Q55 yz
(8)
k1 k1
2z hk
-
Formulation of Dynamic problems
Stiffness matrix is validated by bending problems and mass
Q44 G13t G13b
2h
G13b
matrix is validated through vibration problems. In order to
2z hk
validate the formulation of mass matrix, one has to solve a free vibration problem by incorporating the validated elastic
Q55 G23t G23b
2h
G23b
stiffness matrix. The standard governing equation in matrix
Q45 0
(9)
form for the deflection problem is
Ke q F
(13)
The constitutive relation for FGM plate is given by
F is the nodal load vector, Ke is the system elastic stiff-
N
C
(10)
ness matrix. For a given set of loads, the displacement q
Where,
N Nx, Ny, Nxy, Mx, My, Mxy, Qxz, QyzT rep- resents the in-plane stress resultants (N), out of plane bending moments (M) and shear resultants (Q). Here, [C] is the con- stitutive matrix [9] of the FGM plate. To compensate for the parabolic shear stress variation across the thickness of the
plate, a correction factor of 5/6 is used in the shear-shear cou-
can be
determined using the above equation. If the displacement vector is validated, it ensures the correctness of formulation and coding of the stiffness matrix.
The standard governing equation in matrix form for the free vibration problem is
pling components of the constitutive matrix [10]. Using
Mq Ke q F
(14)
Green-Lagranges strain-displacement expression [11], the linear strain-displacement matrix[B] have been worked out.
The standard governing equation in matrix form for the force vibration problem is
Mq Cq Ke q F
(15)
M ,Ke and C represents global mass matrix, global
Table2. Variation of fundamental frequency with n values Cantilever FGM plate-comparison
stiffness matrix and damping matrix respectively.
C M Ke
n
9-NHE
Simulation
He 2001)
0
25.37
27.21
25.58
0.2
29.14
31.45
29.87
0.5
32.27
33.86
32.84
1
33.90
36.79
35.33
5
38.48
42.14
40.97
15
42.16
45.34
43.97
100
45.64
48.12
46.12
1000
46.08
48.94
46.55
n
9-NHE
Simulation
He 2001)
0
25.37
27.21
25.58
0.2
29.14
31.45
29.87
0.5
32.27
33.86
32.84
1
33.90
36.79
35.33
5
38.48
42.14
40.97
15
42.16
45.34
43.97
100
45.64
48.12
46.12
1000
46.08
48.94
46.55
(16)
where, and are the Rayleigh damping coefficients. From
this, we can solve the forced vibration problem. From this, we can solve the force vibration problem using Newmark-beta method.
-
RESULTS AND DISCUSSION
The properties of FGM plates are graded through the thick- ness direction according to a volume fraction power law dis- tribution (Figure 3).
-
Free vibration analysis
The heterosis element is used in the code for free vibration analysis. For validation of the present code, the data available for the functionally graded plate aluminium oxide titanium alloy of size 0.4m x 0.4m x 0.005m available in the literature of He et al.[13] is used. In numerical simulation by Abaqus, S8R5 element has been used. Table 1. shows the material properties. Table 2. validated the code with literature and sim- ulation.
Table1. Material properties of Aluminium Oxide Titanium alloy FGM plate
Material
E(N/m2)
(kg/m3)
Ti-6A1-4V
(ceramic)
122.56 x 109
4429
0.2884
Aluminium
oxide
349.55 x 109
3750
0.26
Figure 3. Variation of volume fraction with the non-dimensional thick- ness
The present code is validated with results of He et al. (2001). The simulation results are also in good agreement with results obtained from FEM coding. This ensures the correctness of the formulation of the stiffness and mass matrix.
-
Free Vibration Analysis of C-Si C Plate
The analysis is done for C-Si C plate (0.5×0.5×0.001m). Ma- terial properties are given in Table 3. Convergence results are shown in Figure 4. First four mode of vibration shown in Figure. 5 by Abaqus using S8R5 shell element .Frequency of Vibration is minimum for carbon plate as shown in Table 4.
Table3. Material Properties C-Si C FGM plate
Material
E(G
Pa)
(Kg/m3)
Si-C (Ce-
ramic)
320
0.3
3220
C(Metal)
28
0.3
1780
-
Forced vibration analysis
Forced vibration analysis was carried out at the centre of the plate using harmonic sine loading and different impulse load- ings.
-
Harmonic Sine Wave Loading.
A harmonic force P(t)= P0 sin( t ) load is applied at the centre
of the plate(Figure6(a)-6(b), where P0 is the amplitude or peak value of the force and is the forcing frequency.
T 2/ is the forcing period of the FGM plate P0 =1N and
= 2f where is circular frequency and f is natural fre-
quency of the Plate.. Table 5 compares the un-damped and damped cases. Figure 6(c) for simply supported plate. The maximum displacement at the center of the fixed plate as shown in Figure 6(d) is less than that of simply supported plate. Fig. 6 shows that maximum displacement at the centre of the plate increases with the material index (n value)
Figure 4. Convergence of fundamental frequency of simply supported C-Si C FGM plate for first 4 modes (n=2)
Figure 5. First 4 mode shapes of simply supported C-Si C FGM plate (n=2)-Simulation
Table 4. Variation of the natural frequencies (Hz) of FGM simply supported Square Plate for different k values. 22×22 mesh-Heterosis element(FEM)
Table5. Displacement of simply supported C-Si C plate for differ- ent n values
Power-law in- dex
Maximum Displacement at Centre(m)
CCCC
SSSS
Undamped
Damped
Undamped
Damped
n=0 (Si C)
4.759x
10-5
4.73x
10-5
1.165 x 10-4
1.006 x 10-4
n=2
1.722 x10-
4
1.71 x 10-4
3.142 x 10-4
3.035 x 10-4
n=15
2.796 x10-
4
2.68 x 10-4
5.222x
10-4
5.201x
10-4
n=1000(C)
5.442 x10-
4
5.41 x 10-4
1.229×10-3
1.199x
10-3
Mode no
k=0 Si C
n=2
k=15
k=1000
Carbon
1
37.91
27.39
22.2114
15.08
2
94.77
60.84
51.9549
37.7
3
94.77
60.84
51.9549
37.7
4
151.63
98.77
83.7656
60.33
5
189.55
121.26
103.718
75.41
6
189.55
123.04
104.522
75.41
7
246.41
158.98
135.449
98.03
8
246.41
158.98
135.449
98.03
9
322.27
202.97
174.955
128.21
10
322.27
202.97
174.955
128.21
Figure 6. Response of C-Si C FGM plate for different k values using heterosis element.
-
Impulse loading
-
A very large force that acts for a very short time but with a time integral that is finite is called an impulse force. Impulse forces of rectangular, half-cycle sine, triangular shapes each with the same value of maximum force 1N is applied at the centre of the plate. The response behavior of FGM plate is studied for material index(k) value=2. td is pulse duration. The Response spectra of the FGM plate with material index n=2 is shown in Figure 7. Tn is the natural time period of vibration of the plate and u st0 is the static deflection of the plate. Static deflection is 1.438e-4m and Natural time period is 0.0365 sec. Table 6 presents the variation of deformation response factor (Rd) with td/T n values (n=2).The present results are in good agreement with the available literature [14].
Figure 7. Response spectra of simply supported C-Si C FGM Plate (material index n=2)
Table7. Variation of deformation response factor (Rd) with td/T n values (n=2)
Rd= u0/ u st0 |
|||
td/T n |
Rectangular Loading |
Half Sine Loading |
Trian- gular Loading |
0 |
0 |
0 |
0 |
0.5 |
1.569 |
0.982 |
0.863 |
0.75 |
1.876 |
1.469 |
1.3 |
1 |
1.901 |
1.701 |
1.52 |
1.5 |
1.901 |
1.5 |
1.298 |
2 |
1.901 |
1.25 |
0.93 |
2.5 |
1.901 |
1.071 |
0.996 |
3 |
1.901 |
1.15 |
1.148 |
3.5 |
1.901 |
1.111 |
1.103 |
4 |
1.901 |
1.108 |
1.003 |
4. CONCLUSIONS
In the present study, an FE solution is obtained for free and forced vibration analysis of FG plates using heterosis element. The analysis is carried out by developing a computer program in MATLAB. A 9- noded heterosis element is used to model the FGM plate. The heterosis element exhibits improved char- acteristics as compared to the 8- noded serendipity and 9- noded Lagrange elements. It offers a high level of accuracy for extremely thin plate configurations. Convergence study has been carried out for ensuring the convergence of the nu- merical results. The results are also extracted from Abaqus CAE by using S8R5 shell elements andare in very good agreement with the developed elements. Free vibration anal- ysis is done to study the different modes as well as frequen- cies. It is observed that free vibration response is minimum
for carbon and maximum for Silicon carbide plate. The cen- tral deflection of the plate increases with increase in volume fraction index for all types of boundary conditions. From the Response spectra, it is clearly understood that if the pulse du- ration (td) is longer than Tn/2, the overall maximum defor- mation occurs during the pulse. Then the pulse shape is of great significance. For the larger value of td/Tn, the overall maximum deformation is influenced by the rapidity of the loading. The rectangular pulse in which the force increases suddenly from zero to maximum show the large deformation. The triangular pulse in which the increase in the force is ini- tially slowest among the three pulses produces the smallest deformation. The half-cycle sine pulse in which the force ini- tially increases at an intermediate rate causes deformation that for many values of td/Tn is larger than the response of the tri- angular pulse. Sufficient duration steep loading produces a magnification factor of 2 and gradual loading increase results in a magnification factor of 1.
REFERENCES
-
Koizumi M .The Concept of FGM Ceramic Transactions. Function- ally Gradient Materials, 34: 3-10(1993)
-
Jha, D.K., Kant, T., Singh, R.K.: A critical review of recent research on function ally graded plates. Composite Structures (96), 833-849 (2013)
-
Reddy, B. S., Kumar, J. S., Reddy, E. C., Reddy, K. V. K.: Free Vibration Behaviour of Functionally Graded Plates Using Higher- Order Shear Deformation Theory. Journal of Applied Science and Engineering, 17(3), 231-241 (2014)
-
Wang, C.M., Reddy, J.N., Lee, K.H.: Shear Deformable Beams and Plates Relationships with Classical Solutions. ELSEVIER (2000)
-
Vimal, J., Srivastava, R. K., Bhatt, A. D., Sharma, A. K.: Free vibra- tion analysis of moderately thick functionally graded skew plates. Engineering Solid Mechanics. (2), 229-238 (2014)
-
Gulshan, M. N. A., Chakrabarti, A., Prakash, V.: Vibration Charac- teristics of Functionally Graded Material Skew Plate in Thermal Environment, World Academy of Science, Engineering and Tech- nology. International Journal of Mechanical and Mechatronics Engi- neering (8), 142-153 (2014)
-
Reddy, J. N.: International Journal for Numerical Methods in Engi- neering. Int. J. Numer. Meth. Engg. (47), 663-684(2000)
-
Thomas Hughes, J.R, Martin Cohen.: The heterosis finite element for plate bending. Computers and Structures. (9), 445-450(1978)
-
Reddy, N.: Mechanics of Laminated Composite Plates. CRC Press (1996).
-
Lal, R., Saini, R.: Buckling and Vibration of Non-Homogeneous Rectangular Plates Subjected to Linearly Varying In-Plane Force. Shock Vib 20(5), 879894(2013)
-
Bathe, K. J.: Finite Element Procedures. Prentice-Hall, Engle-wood Cliffs (1996).
-
Cook, R. D.: Concepts and Applications of Finite Element Analysis. John Wiley & Sons (2007).
-
He, X.Q., Ng, T.Y., Sivashanker, S., Liew, K.M.: Active control of FGM plates with integrated piezoelectric sensors and actuators. In- ternational Journal of Solids and Structures (38), 1641-1655 (2001)
-
13. Chopra, A. K.: Dynamics of Structures, Theory and Applications to Earthquake Engineering. Pearson Education South Asia, New Delhi (2007).