
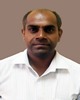
- Open Access
- Authors : Venkat , Dr. S. Ranganatha
- Paper ID : IJERTV9IS120246
- Volume & Issue : Volume 09, Issue 12 (December 2020)
- Published (First Online): 16-01-2021
- ISSN (Online) : 2278-0181
- Publisher Name : IJERT
- License:
This work is licensed under a Creative Commons Attribution 4.0 International License
Vibration Analysis of Rectangular Plate with and without Through Crack in Clamped Clamped Free Free (CCFF) Boundary Condition
Venkat
Microwave Tube Research and Development Centre DRDO, Bangalore, India
and
Research Scholar UVCE, Bangalore University Bangalore
Dr. S. Ranganatha
Mechanical department
Universuty Visvesvaraya College of Engineering Bangalore University
Bangalore, India
Abstract The engineering structures in general will have a plate as one of the component. The plate structures are found to have defects due to manufacturing process, in raw material and during service loading. These defects are called discontinuities and alter the dynamic response of the structures. One of the major problems faced in aerospace industries is fatigue effect which may results in catastrophic failure. Understanding of the dynamic response of the plate structure with discontinuities is most desired area of research for scientists. The researchers have attempted both experimental and numerical approach for understanding the dynamic response of plate with material discontinuity.
In the present investigation experiments have been carried out using vibration shaker and rectangular plate with and without crack in clamped-clamped-free-free (CCFF) boundary condition. The plate was subjected to forced vibration with frequency in the range varying 20-2000Hz. The monitored response parameters were amplitude, modal frequency, phase angle and damping factor. The experiment result showed that the magnitude of amplitude at resonance was found to be dependent on mode numbers. The magnitude of amplitude at given mode was found to be dependent on presence of through crack and its orientations. The modal frequencies were found to be dependent on mode numbers. The damping factor in mode 1 and 2 was found to vary in case of through cracks and its orientation.
Keywords Through crack, modal frequency, amplitude, damping factor,phase,crack incliation, vibration.
-
INTRODUCTION
The engineering structures in general will have a plate as one of the major components. The aerospace engineering, automobile engineering, civil and marine are few applications where plates are extremely used. The plates used in aerospace and automobile industries are subjected to dynamic loading. The response of plate structures in engineering system, more particularly in aerospace industries demands proper understanding when dynamic loads are present. The plate structures are found to have defects due to manufacturing process, in raw material and during service loading. These defects called discontinuities alter the dynamic response of plate structures. One of the major problems faced in aerospace industries is fatigue effect which results in catastrophic failures. The frequency of disturbing force introduced by aero-engine; if matches the natural frequency of the flight, leads to resonance. Under resonance, the resonance of flight wings leads to difficulty in maneuvering
which leads to catastrophic failure. Understanding the dynamic response of the flight, in particular natural frequency is most desired data for flight designer.
Understanding the dynamic response of plate structures with discontinuity is most desired area for scientists. The researchers have attempted both experimental and numerical approach for understanding the dynamic response of the plate with material discontinuity.
Huang et al using Ritz method made attempts for determining frequencies and mode shapes of a thick rectangular plate having two types of cracked configuration. The crack configuration was side and internal cracks. The researchers proposed a new set of admissible functions which represented true solutions along the cracks. These new set of solutions were used in Ritz-method which enhanced for stress singularity around crack tip, discontinuities of transfer displacements and bending rotations across the crack. The obtained solutions monotonically converged to upper bound if number of admissible functions increased. The results obtained were compared with results based on classical plate theory. The method also extends the utility in investigating effect of crack length, location and orientations, in case of simply supported and cantilever cracked rectangular plates [1]. Joshi et al made attempts in applying analytical model for understanding nonlinear dynamic response of rectangular cracked plate. The researchers considered plate with single and two perpendicular internal cracks at the centre of the plate. The equation of plate theory using line spring model modified to accommodate the effects of internal cracks. Accounting in plane forces using Bergers approach yielded nonlinear model. Gelerkins method with three different boundary conditions, converted the equations with time dependant modal functions. Natural frequencies were calculated for different crack length for both single crack and different crack length ratio in case of two cracks. The crack compliance coefficients were made use in identifying the effect of location of part through crack on natural frequency. The results shows that the natural frequency were affected to larger extent when cracks were through thickness and symmetrical about the mid plane of the plate for all three boundary conditions. The effect of influence on natural frequencies is less for surface cracks. The dynamic response of the plate depends on configuration of the crack with respect to larger and shorter edges of the plate. Finite element model also carried out [2]. Cornwell et al made attempts to
detect and locate discontinuity in plate. The attempt was carried out using measured modal parameters. The try out method for locating discontinuity in plate requires modal properties before and after damage and these methods requires correlated FE model are mass normalized modal configurations. The present model uses the changes in the strain energy. The model is extended to two dimensional curved structure i.e. plate. The developed model was used in both comparing results of simulated and experimental data [3]. Ali Beigi et al attempted in understanding the effect of parameters like length, position and angle of cracks on free vibration of plate using finite element method. The crack was assumed as a material discontinuity and running through the thickness of the plate. The influences of the crack growth were neglected. The result shows that the crack parameters influence the stiffness and natural frequency affecting the modal shapes and stress intensity. The thickness and mechanical properties of plate did not influence the different response of cracked and intact plate [4]. Banerjee and Mazumdar made attempts in identifying methods for obtaining solutions for dynamic response of plates which are though linear in nature turns out to be involving geometrical nonlinearities or other difficulties. The geometrical nonlinearity and other factors leads in obtaining approximate solution in case of linear dynamic response of the plate [5]. Aksu and Ali used finite difference formulation for obtaining dynamic response of rectangular plate with cut-outs. The method used variation principle along with finite difference techniques. Interlacing grid concept was used to obtain the strain energy of nodal sub-domains which were used to divide the plate. The interlacing grid techniques was made use in case of internal and boundary nodes. The natural frequency and mode shapes with one and two cut out in rectangular plates were estimated and estimated parameters were experimentally verified [6]. Kiran and Mali et al used cosine series for displacement of a perforatd rectangular plate with two boundary conditions, clamped edge and support conditions. The perforation shape was considered as circular holes. The perforated plate was modeled as plate with uniform distributed mass. The circular holes or perforations are represented by concentrated negative mass. The Galerkin method was used in the analytical procedures. The finite element results were used to validate the analytical model. The comparison showed that analytical model predicted comparable results for holes of small sizes [7]. Bhat studied the dynamic response of polygonal shaped plate using orthogonal polynomials in two variables. The deflection of polynomial plate is expressed in terms of characteristics orthogonal polynomials with two variables. The assumed deflection function was used in Rayleigh-Ritz method to obtain natural frequency and mode shapes. Orthogonal polynomial sets were constructed according to Gram-Schmidt orthogonalization method. First six natural frequencies and mode shapes were numerically estimated for triangular plate with different configurations. The estimated results were compared with existing results obtained from the other experimental methods [8]. Hoon and Jhung studied analytically the free vibration of partially perforated circular plates with triangular hole and clamped boundary conditions. The results of finite element method for material properties of
plate with circular holes are used for analysis of dynamic loading. The method used was to minimize the Rayleigh quotient that is ratio between potential energy to the total kinetic energy for finding out natural frequency. The circular plate was modeled into solid outer annular region and central perforated region. The reduction in mass and stiffness of the perforated region was considered as function of ligament efficiency. The results of the present model were compared with existing finite element results [9]. Liew et al analytically studied free vibration of rectangular plates using orthogonal plate functions with different boundary conditions involving free edges. The Gram-Schmidt was adopted in generating the plate functions. The researchers used the orthogonal plate functions in Rayleigh-Ritz method to find out the dynamic response of the plate. The researchers obtained natural frequency and compared with results reported in literature and found them to be comparable [10]. Leissa attempted an analytical solution for free vibration of rectangular plates with possible combinations of boundary conditions namely clamped, simply supported and free edge. The combinations of boundary conditions were; two opposite sides were simply supported which resulted in six different cases and exact characteristics equations were developed. Existence of solutions for various characteristics equations was identified. The combinations of other boundary conditionss resulted in fifteen more different cases and Ritz method was used with 36 terms containing the product of beam functions to obtain the dynamic response. The effect of aspect ratio and poissons ratio were studied. The problems of
15 cases were compared with Warburton approximate formulae [11]. Mizusawa analytically studied natural frequency of rectangular plate with free edges. The method involved was use of B-spline function in Rayleigh-Ritz method. The analysis considered the influence of aspect ratio, boundary conditions and poissons ratio. The results obtained by present method were compared with results of existing numerical method and found to be comparable [12]. Rice and Levy analyzed the static response of a plate containing surface crack in a plate when subjected to tensile and bending moment. The model used two dimensional generalized plane stress and Kirchhoff approximate bending theory replacing the surface crack as a continuous line spring. The line spring was one which resisted both tensile load and bending moment. The compliance co-efficient of spring was taken to match the compliance of an edge cracked strip in plain strain. The analytical formulation reduced to two coupled integral equation for thickness average force and moment per unit length along cracked section. The problem was solved numerically and compared with approximate closed form solution. The stress intensity factors at the mid-point of surface crack were estimated when tensile and bending loads existed on plates is removed. The results showed that the stress intensity factor was less compared to a similarity loaded plate with a through crack of same length [13]. Young et al modeled the free vibration of thick rectangular plates with defects like depressions, grooves or cut-outs. The plate was modeled as parallelepiped. The inclusions are treated by subtracting by their contribution to the strain and kinetic energy expressions. The deflection was modeled with simple algebraic polynomials which satisfies the boundary
conditions. These polynomials were used in Ritz method for analyzing dynamic responses. The strain and kinetic energy excluding the contribution from inclusion is used in minimizing the functional. The developed analytical method as used in analyzing thick plates with cylindrical groove, depression or cylindrical cut-out [14]. Dimarogonas reviewed the dynamic response of cracked structure. The existence of crack in structures alters the dynamic response of the structure due to the local flexibility of the crack. The presence of crack also leads the systems to be nonlinear. Many times existence of crack results in coupled system. Existence of crack introduced new harmonic in the spectrum. In case of rotating shaft where second harmonic of rotations and sub-harmonics of critical harmonic speed were found. The presence of crack in shaft gives rise to two more harmonics mainly higher harmonic of rotating speed and longitudinal and torsional harmonics [15].
The literature describes large amount of information on analytically solution for rectangular plate with varied type of discontinuities and their configuration with the geometry of the plate. The literature shows inadequate information on experimental results of dynamic response for a plate with through crack configured differently.
In the present investigation a set of experiment were carried out using a rectangular plate with through crack, configured differently to longitudinal axis of the plate, subjected to dynamic loading.
-
EXPERIMENTAL SETUP
The experiments were conducted for solid plate and plate with through crack oriented with respect to longitudinal axis of the plate at 00, 200, 400, 600 and 900 respectively.
The forcing frequency is varied from 20-2000Hz. The amplitude, phase angle were monitored with respect to the forcing frequency. The experiment for a given set of parameters was repeated for thrice. The results of three experiment trials were used for estimating average values of parameters; magnitude of amplitude, modal frequency, phase angle Q-factor and damping factors.
The experiments were conducted using a 4-channel vibration controller and vibration shaker with accelerometer. The schematic experimental setup is shown Fig. 1.
Fig. 1. Schematic of electrodynamics vibration set up
The details of the equipment and subsystems are tabled in Table I.
TABLE I. SPECIFICATION OF SHAKER AND SUBSYSTEM
Subsystem
Model number
Parameter
Specification
Electro dynamic Shaker
SEV 060
Rated force
600 Kgf (Peak Sine)
Digital
power amplifier
DAS 3K6
Operating frequency
5 Hz to 3000 Hz
Vibration controller
Spandon
Stroke
30 mm (p-p)
Piezo electric accelerometers
M353B04
Acceleration bare Table
75 g
RSTD package
Maximum velocity
1.5 m/sec
Moving platform diameter
180 mm
The solid rectangular plate and plate with through cracks are shown in Fig. 2 and Fig. 3.
Fig. 2. Solid plate
Fig. 3. Plate with through crack inclined 0°
The fixture used for clamped-clamped-free-free boundary condition in three dimensional view is shown in Fig. 4
Fig. 4. Assembly of fixture with specimen
The drawing of fixture for imposing the boundary conditions is shown in fig.5
Fig. 5. 2 D drawing of vibration fixture The complete expermental set up is shown in Fig. 6
Fig. 6. Vibration shaker with plates for CCFF boundary condition
The experiments were conducted with rectangular plates having differently oriented through cracks. The different orientations of the crack with respect to longitudinal axis were;
-
Through crack at 00 with longitudinal axis
-
Through crack at 200 with longitudinal axis
-
Through crack at 400 with longitudinal axis
-
Through crack at 600 with longitudinal axis
-
Through crack at 900 with longitudinal axis
Experiments were also conducted with solid plate to compare the results with through cracked plates.
-
-
RESULTS AND DISCUSSION
-
Solid plate
Rectangular plates with and without through crack were subjected to forced vibration with clamped-clamped- free-free (CCFF) boundary condition. Each experiment was repeated for three times and average values of parameters; magnitude of amplitude, modal frequency, phase angle and damping factors were estimated from the experimental results.
-
Amplitude on forcing frequency.
-
Phase on forcing frequency.
The dependency of amplitude, phase angles are shown in Fig. 8 and Fig. 9
Fig. 8. Dependency of amplitude with excitation frequency for solid
plate
The Fig. 8 shows the dependency of amplitude on exciting frequency. The amplitude at resonance frequencies at different modes are shown in Fig. 8. The magnitude of amplitude and modal frequencies were rounded to full number.
Fig. 9. Dependency of phase angles with modal frequency for solid plate
The Fig. 9 shows the dependency of phase angles on exciting frequency. The phase angle at resonance frequencies at different modes are shown in Fig. 9. The magnitude of phase angles and modal frequencies were rounded to full number.
The damping factor () was found from the Q-factor using the formulae; =1/2Q. The amplitude at resonance, the resonance frequency at different modes, phase angles at resonance frequencies and estimated damping factors are tabulated in Table II.
TABLE II. AMPLITUDE, MODAL FREQUENCY, PHASE, Q-FACTOR AND DAMPING FACTOR FOR SOLID PLATE
Solid plate
Mode No.
Amplitude (g/g)
Modal Frequency (Hz)
Phase Angle (0)
Q-Factor
Damping factor
()
1
70
188
-90
49
0.02
2
2
292
-165
55
0.02
3
1
522
171
24
0.04
4
49
661
67
63
0.02
5
3
715
-129
148
0.01
6
5
954
119
14
0.07
7
25
1065
61
25
0.04
8
30
1132
-60
89
0.01
Solid plate
Mode No.
Amplitude (g/g)
Modal Frequency (Hz)
Phase Angle (0)
Q-Factor
Damping factor
()
1
70
188
-90
49
0.02
2
2
292
-165
55
0.02
3
1
522
171
24
0.04
4
49
661
67
63
0.02
5
3
715
-129
148
0.01
6
5
954
119
14
0.07
7
25
1065
61
25
0.04
8
30
1132
-60
89
0.01
A typical plot for solid plate for showing the dependency of amplitude and phase angles with respect to forced frequency for one of the trial experiment is shown in Fig. 7.
Fig. 7. Experimental results for solid plate for CCFF condition
The Fig. 7 shows different resonances magnitude of amplitudes, resonance frequencies, phase angles and Q- factors at different modes. The data in Fig. 7 is used for showing the dependency of;
The vibration parameters; amplitude, modal frequency, phase, Q-Factors and damping factors were considered up to eighth mode. The amplitude of 70g/g was found to be maximum for mode 1 and minimum of 1g/g for mode 3. The modal frequencies are found to be 188,292, 522,661, 715,
954, 1065 and 1132 Hz for mode 1 to mode 8. The maximum in-phase angle was found to be 1710 for mode 3 and maximum out-of-phase 1650 for mode 2. The Q-factors was found to be maximum and is 148 for mode 5 and
minimum found to be 14 for mode 6. The damping factor ranged over 0.01 to 0.07.
-
-
Through crack at 00 with longitudinal axis
A typical plot for through crack at 00 with longitudinal axis for showing the dependency of amplitude and phase angles with respect to forced frequency for one of the trial experiment is shown in Fig. 10.
Fig. 10. : Experimental results for through crack at 00 for CCFF conditions
The Fig.10 shows different resonances magnitude of amplitudes, resonance frequencies, phase angles and Q-factor sat different modes. The data in Fig.10 is used for showing the dependency of ;
-
Amplitude on forcing frequency.
-
Phase on forcing frequency.
The dependency of amplitude, phase angles are shown in Fig.11 and Fig.12
Fig. 11. : Dependency of amplitude with excitation frequency for through
crack at 00
The Fig.11 shows the dependency of amplitude on exciting frequency. The amplitude at resonance frequencies at different modes are shown in Fig.11. The magnitude of amplitude and modal frequencies were rounded to full number.
Fig. 12. Dependency of phase angles with excitation frequency for
through crack at 00
The Fig.12 shows the dependency of phase angles on exciting frequency. The phase angle at resonance frequencies at different modes are shown in Fig.12. The magnitude of phase angles and modal frequencies were rounded to full number.
The damping factor () was found from the Q-factor using the formulae; =1/2Q. The amplitude at resonance, the resonance frequency at different modes, phase angles at resonance frequencies and estimated damping factors are tabulated in Table III
TABLE III. AMPLITUDE, MODAL FREQUENCY, PHASE AND Q-FACTOR FOR THROUGH CRACK AT 00
Through crack at 00 withlongitudinal axis
Mode No.
Amplitude (g/g)
Modal Freq.(Hz)
Phase (0)
Q-Factor
Damping Factor ()
1
103
186
-86
41
0.01
2
3
276
141
45
0.01
3
21
634
77
89
0.01
4
7
666
-72
89
0.01
5
17
1109
-74
45
0.01
6
6
1319
-70
44
0.01
7
26
1434
-96
63
0.01
8
48
1824
-162
32
0.02
The vibration parameters; amplitude, modal frequency, phase, Q-Factors and damping factor were considered up to eighth mode. The amplitude of 103g/g was found to be maximum for mode 1 and minimum of 3g/g for mode 2. The modal frequencies are found to be 186,276, 634,666, 1109,
1319, 1434 and 1824 Hz for mode 1 to mode 8. The maximum in-phase angle was found to be 1410 for mode 2 and maximum out-of-phase 1620 for mode 8. The Q-factors was found to be maximum and is 89 for mode 3 and 4 and minimum found to be 32 for mode 8. The damping factor ranged over 0.01 to 0.02.
-
-
Through crack at 200 with longitudinal axis
A typical plot for through crack at 200 with longitudinal axis for showing the dependency of amplitude and phase angles with respect to forced frequency for one of the trial experiment is shown in Fig.13.
Fig. 13. : Experimental results for through crack at 200 for CCFF
conditions
The Fig.13 shows different resonances magnitude of amplitudes, resonance frequencies, phase angles and Q- factors at different modes. The data in Fig.13 is used for showing the dependency of ;
-
Amplitude on forcing frequency.
-
Phase on forcing frequency.
The dependency of amplitude, phase angles are shown in Fig.14 and Fig.15
Fig. 14. Dependency of amplitude with excitation frequency for through
crack at 200
The Fig.14 shows the dependency of amplitude on exciting frequency. The amplitude at resonance frequencies at different modes are shown in Fig.14. The magnitude of
amplitude and modal frequencies were rounded to full number.
Fig. 15. Dependency of phase with excitation frequency for through crack
at 200
The Fig.15 shows the dependency of phase angles on exciting frequency. The phase angle at resonance frequencies at different modes are shown in Fig.15. The magnitude of phase angles and modal frequencies were rounded to full number.
The damping factor () was found from the Q-factor using the formulae; =1/2Q. The amplitude at resonance, the resonance frequency at different modes, phase angles at resonance frequencies and estimated damping factors are tabulated in Table IV
TABLE IV. AMPLITUDE, MODAL FREQUENCY, PHASE AND Q-FACTOR FOR THROUGH CRACK AT 200
Through crack at 200 with longitudinal axis
Mode No.
Amplitude (g/g)
Modal Freq.(Hz)
Phase (0)
Q-
Factor
Damping factor ()
1
12
177
-84
8
0.06
2
2
273
-88
111
0.00
3
2
355
-148
7
0.08
4
35
560
62
74
0.01
5
0
603
8
32
0.02
6
0
672
-177
222
0.00
7
47
1030
68
148
0.00
8
7
1453
-117
89
0.01
The vibration parameters; amplitude, modal frequency, phase, Q-Factors and damping factors were considered up to eighth mode. The amplitude of 47g/g was found maximum for mode 7 and minimum amplitude of zero for mode 5 and
-
-
The modal frequencies are found to be 177, 273, 355, 560, 603, 672, 1030 and 1453 Hz. for mode 1 to mode 8. The maximum in-phase angle was found to be 620 for mode 4 and maximum out-of- phase 1770 for mode 6. The Q-factors was found to be maximum and is 222 for mode 6 and minimum found to be 7 for mode 3. The damping factor ranged over 0.01 to 0.08.
-
Through crack at 400 with longitudinal axis
A typical plot for through crack at 400 with longitudinal axis for showing the dependency of amplitude and phase angles with respect to forced frequency for one of the trial experiment is shown in Fig.16.
Fig. 16. Experimental results for through crack at 400 for CCFF
The Fig.16 shows different resonances magnitude of amplitudes, resonance frequencies, phase angles and Q- factors at different modes. The data in Fig.16 is used for showing the dependency of ;
-
Amplitude on forcing frequency.
-
Phase on forcing frequency.
The dependency of amplitude, phase angles are shown in Fig.17 and Fig.18
Fig. 17. Dependency of amplitude with excitation frequency for through
crack at 400
The Fig.17 shows the dependency of amplitude on exciting frequency. The amplitude at resonance frequencies at different modes are shown in Fig.17. The magnitude of amplitude and modal frequencies were rounded to full number.
Fig. 18. Dependency of phase with Excitation frequency for through crack
at 400
The Fig.18 shows the dependency of phase angles on exciting frequency. The phase angle at resonance frequencies at different modes are shown in Fig.18. The magnitude of phase angles and modal frequencies were rounded to full number.
The damping factor () was found from the Q-factor using the formulae; =1/2Q. The amplitude at resonance, the resonance frequency at different modes, phase angles at resonance frequencies and estimated damping factors are tabulated in Table V.
TABLE V. AMPLITUDE, MODAL FREQUENCY, PHASE AND Q-FACTOR FOR THROUGH CRACK AT 400
Through crack at 400 with longitudinal axis
Mode No.
Amplitude (g/g)
Modal Freq.(Hz)
Phase (0)
Q-Factor
Damping factor ()
1
12
174
-78
8
0.06
2
2
271
-48
89
0.01
3
2
355
-147
7
0.08
4
82
567
46
111
0.00
5
0
608
9
22
0.02
6
1
664
-163
148
0.00
7
41
1023
90
11
0.00
8
1
1267
-16
16
0.03
The vibration parameters; amplitude, modal frequency, phase, Q-Factors and damping factors were considered up to eighth mode. The amplitude of 82g/g was found to be maximum for mode 4 and minimum for mode 5. The modal frequencies are found to be 174, 271, 355, 567,608, 664,
1023 and 1267 Hz for mode 1 to mode 8. The maximum in-
phase angle was found to be 900 for mode 7 and maximum out-of-phase angle 1470 for mode 3. The Q-factors was found to be maximum and is 148 for mode 6 and minimum found to be 7 for mode 3. The damping factor () ranged over 0.01 to 0.08.
-
-
Through crack at 600 with longitudinal axis
A typical plot for through crack at 600 with longitudinal axis for showing the dependency of amplitude and phase angles with respect to forced frequency for one of the trial experiment is shown in Fig.19.
Fig. 19. Experimental results for through crack at 600 for CCFF boundary
The Fig.19 shows different resonances magnitude of amplitudes, resonance frequencies, phase angles and Q- factors at different modes. The data in Fig.19 is used for showing the dependency of ;
-
Amplitude on forcing frequency.
-
Phase on forcing frequency.
The dependency of amplitude, phase angles are shown in Fig.20 and Fig.21
Fig. 20. Dependency of amplitude with excitation frequency for through
crack at 600
The Fig.20 shows the dependency of amplitude on exciting frequency. The amplitude at resonance frequencies at different modes are shown in Fig.20. The magnitude of amplitude and modal frequencies were rounded to full number.
Fig. 21. Dependency of phase angles with excitation frequency for
through crack at 600
The Fig.21 show the dependency of phase angles on exciting frequency. The phase angle at resonance frequencies at different modes are shown in Fig.21. The magnitude of
phase angles and modal frequencies were rounded to full number.
The damping factor () was found from the Q-factor using the formulae; =1/2Q. The amplitude at resonance, the resonance frequency at different modes, phase angles at resonance frequencies and estimated damping factors are tabulated in Table VI.
TABLE VI. AMPLITUDE, MODAL FREQUENCY, PHASE AND Q-FACTOR FOR THROUGH CRACK AT 600
Through crack at 600 with longitudinal axis
Mode No.
Amplitude (g/g)
Modal Freq.(Hz)
Phase (0)
Q-Factor
Damping factor
1
14
173
-83
10
0.05
2
6
510
-138
74
0.01
3
33
574
82
74
0.01
4
47
596
-109
148
0.01
5
0
663
-138
111
0.01
6
2
870
115
40
0.01
7
36
1028
79
111
0.01
8
3
1250
-57
49
0.01
The vibration parameters; amplitude, modal frequency, phase, Q-Factors and damping factors were considered up to eighth mode. The amplitude of 47g/g was found to be maximum for mode 4 and minimum zero for mode 5. The modal frequencies are found to be 173, 510, 574, 596, 663, 870, 1028 and 1250 Hz for mode 1 to mode 8. The maximum in-phase angle was found to be 1150 for mode 6 and maximum out-of-phase 1380 for mode 2 and 5. The Q- factors was found to be maximium and is 148 for mode 4 and minimum found to be 10 for mode 1. The damping factor ranged over 0.01 to 0.05.
-
-
Through crack at 900 with longitudinal axis
A typical plot for through crack at 900 with longitudinal axis for showing the dependency of amplitude and phase angles with respect to forced frequency for one of the trial experiment is shown in Fig.22.
Fig. 22. Experimental results for through crack at 900 for CCFF boundary
conditions
The Fig.22 shows different resonances magnitude of amplitudes, resonance frequencies, phase angles and Q- factors at different modes. The data in Fig.22 is used for showing the dependency of ;
-
Amplitude on forcing frequency.
-
Phase on forcing frequency.
The dependency of amplitude, phase angles are shown in Fig.23 and Fig.24
Fig. 23. Dependency of amplitude with excitation frequency for through crack at 900
The Fig.23 shows the dependency of amplitude on exciting frequency. The amplitude at resonance frequencies at different modes are shown in Fig.23. The magnitude of amplitude and modal frequencies were rounded to full number.
Fig. 24. Dependency of phase angles with excitation frequency for
through crack at 900
The Fig.24 show the dependency of phase angles on exciting frequency. The phase angle at resonance frequencies at different modes are shown in Fig.24. The magnitude of phase angles and modal frequencies were rounded to full number.
The damping factor () was found from the Q-factor using the formulae; =1/2Q. The amplitude at resonance, the resonance frequency at different modes, phase angles at resonance frequencies and estimated damping factors are tabulated in Table VII.
TABLE VII. : AMPLITUDE, MODAL FREQUENCY, PHASE AND Q-FACTOR FOR THROUGH CRACK AT 900
Through crack at 900 with longitudinal axis
Mode No.
Amplitude (g/g)
Modal Freq.(Hz)
Phase (0)
Q-Factor
Damping Factor ()
1
12
190
-79
9
0.06
2
2
344
-142
6
0.08
3
15
554
95
63
0.01
4
10
573
-38
74
0.01
5
15
652
50
148
0.00
6
1
878
154
22
0.02
7
34
1119
88
111
0.00
8
3
1290
-44
64
0.01
The vibration parameters; amplitude, modal frequency, phase, Q-Factors and damping factors were considered up to eighth mode. The amplitude of 34g/g was found to be maximum for mode 7 and minimum for mode 6. The modal frequencies are found to be 190, 344, 554, 573,
652, 878, 1119 and 1290 Hz for mode 1 to mode 8. The maximum in-phase angle was found to be 1540 for mode 6 and maximum out-of-phase 1420 for mode 2. The Q-factors was found to be maximum and is 148 for mode 5 and
minimum found to be 6 for mode 2. The damping factor ()
ranged over 0.01 to 0.08.
-
-
Estimated average magnitude of amplitudes
The estimated average magnitudes of amplitude of solid plate and through crack inclined from 00 to 900 are tabulated in Table VIII.
Average Amplitude (gg)
Solid plate
Through cracks
Mode No
–
00
200
400
600
900
1
92
103
12
12
14
12
2
1
3
2
2
6
2
3
4
21
2
2
33
15
4
34
7
35
82
47
10
5
4
17
0
0
0
15
6
2
6
0
1
2
1
7
10
26
47
41
36
34
8
5
48
7
1
3
3
Average Amplitude (g/g)
Solid plate
Through cracks
Mode No
–
00
200
400
600
900
1
92
103
12
12
14
12
2
1
3
2
2
6
2
3
4
21
2
2
33
15
4
34
7
35
82
47
10
5
4
17
0
0
0
15
6
2
6
0
1
2
1
7
10
26
47
41
36
34
8
5
48
7
1
3
3
TABLE VIII. : AVERAGE AMPLITUDE RESPONSE OF SOLID & ARBITRARY ORIENTED THROUGH CRACKS
The maximum value of amplitude was found to be 103g/g for 00 oriented through crack plate. The minimum magnitude of amplitude zero was found for through crack oriented at 200, 400 and 600.
The average magnitudes of amplitudes tabulated in Table VIII are used for drawing bar chart and shown in Fig.25.
Fig. 25. Average magnitude of amplitude with modal number of solid &
arbitrary oriented through cracks
The bar charts shows that the maximum amplitude of 92g/g was found for solid plate in mode 1 and the amplitude for other plates with through cracks oriented at 200,400, 600 and 900 were found to be comparable in the range of 12 to 14g/g except at 00. The magnitude of amplitude found to be comparable for solid and differently orientated through crack and in the range of 1 to 6 g/g for mode 2.The magnitude of amplitude was comparable for through crack orientated at 00 and 600 in the range of 21 to 33g/g for mode 3. The magnitudes of amplitude of mode 4 were found maximum 82g/g at 400. The minimum value for mode 4 was found to be 7g/g for a plate with through crack inclined at 00. The magnitude of amplitude for mode 5 were comparable for crack inclined at 00 and 900 and in the range of 15 to 17g/g. The magnitudes of amplitude were found minimum for other plate condition and in the range of zero to 4g/g. The magnitudes of amplitude for mode 6 were found to be comparable and in the range of 1 to 6g/g. The magnitudes of amplitude were comparable for all plate except solid plate at mode 7. The magnitude of amplitude for solid plate is 10g/g and for rest of the plate were in the order of 26 to 47g/g. The magnitude of amplitude for solid plate and through crack at
200, 400, 600 and 900 , except 00 in mode 8, were found in the range of 1 to 7g/g and plate with through crack for 00 was 48g/g.
-
Estimated average magnitude of modal frequency
The estimated average magnitudes of modal frequency of solid plate and through crack inclined from 00 to 900 are tabulated in Table IX.
TABLE IX. : AVERAGE MODAL FREQUENCY OF SOLID & ARBITRARY ORIENTED THROUGH CRACKS
Average Modal frequency |
||||||
Solid plate |
Through cracks |
|||||
Mode No |
– |
00 |
200 |
400 |
600 |
900 |
1 |
188 |
186 |
177 |
174 |
173 |
190 |
2 |
303 |
276 |
273 |
271 |
510 |
344 |
3 |
504 |
634 |
355 |
355 |
574 |
554 |
4 |
651 |
666 |
560 |
567 |
596 |
573 |
5 |
696 |
1109 |
603 |
608 |
663 |
652 |
6 |
835 |
1319 |
672 |
664 |
870 |
878 |
7 |
1004 |
1434 |
1030 |
1023 |
1028 |
1119 |
8 |
1110 |
1824 |
1453 |
1267 |
1250 |
1290 |
The modal frequency in general found to increase with mode shape. The minimum was found to be in the order of 180 Hz for all plates in mode 1. The maximum modal frequency found to be the order of 1500 Hz for mode 8.
The average magnitudes of modal frequencies tabulated in Table IX are used for drawing bar chart and shown in Fig.26.
.
Fig. 26. Average magnitude of modal frequency of solid & arbitrary
oriented through cracks
The modal frequency was found to be comparable for all configurations of the plates up to mode 4. At mode higher than 4 plates with 00 inclination behaved differently when compared to all other plates. The modal frequency is a measure of the rate of change of the potential energy to kinetic energy. The plate with through crack inclined at 00 was found to have higher rate of converting kinetic energy to potential energy and vice versa.
In general expect plate with through crack at 00 was found to have comparable modal frequencies at different modes.
TABLE X. AVERAGE PHASE ANGLE OF SOLID & ARBITRARY ORIENTED THROUGH CRACKS
Average phase angles |
||||||
Solid plate |
Through cracks |
|||||
Mode No |
– |
00 |
200 |
400 |
600 |
900 |
1 |
-87 |
-86 |
-84 |
-78 |
-83 |
-86 |
2 |
-56 |
141 |
-88 |
-48 |
-138 |
141 |
3 |
39 |
77 |
-148 |
-147 |
82 |
77 |
4 |
5 |
-72 |
62 |
46 |
-109 |
-72 |
5 |
-93 |
-74 |
8 |
9 |
-138 |
-74 |
6 |
111 |
-70 |
-177 |
-163 |
115 |
-70 |
7 |
112 |
-96 |
68 |
90 |
79 |
-96 |
8 |
32 |
-162 |
-117 |
-16 |
-57 |
-162 |
The forcing frequency was found to results in-phase angle and out-phase angle response . The maximum in-phase angle was found to be 1410 at mode 2 for through crack inclined at 00 and 900.The maximum out-of- phase angle were found to be 1770 at mode 6 for through crack inclined at 200.
The average magnitudes of phase angles are tabulated in Table X are used for drawing bar chart and shown in Fig.27
Fig. 27. : Average magnitude of phase angles of solid & arbitrary oriented
through cracks
The bar chart showed that number of response with out of phase for a plate with through crack and its different orientations were found to be more when compare numbers of responses with in-phase angle.
J. Estimated average magnitude of damping factor
The estimated average values of damping factor () for solid plate and the through crack at 00 to 900 are tabulated in Table XI.
TABLE XI. AVERAGE MAGNITUDE OF DAMPING FACTOR OF SOLID &
Average Damping factor |
||||||
Solid plate |
Through crack |
|||||
Mode No |
– |
00 |
200 |
400 |
600 |
900 |
1 |
0.01 |
0.01 |
0.06 |
0.06 |
0.05 |
0.06 |
2 |
0.04 |
0.01 |
0.00 |
0.01 |
0.01 |
0.08 |
3 |
0.01 |
0.01 |
0.08 |
0.08 |
0.01 |
0.01 |
4 |
0.01 |
0.01 |
0.01 |
0.00 |
0.00 |
0.01 |
5 |
0.01 |
0.01 |
0.02 |
0.02 |
0.00 |
0.00 |
6 |
0.02 |
0.01 |
0.00 |
0.00 |
0.01 |
0.02 |
7 |
0.01 |
0.01 |
0.00 |
0.00 |
0.00 |
0.00 |
8 |
0.03 |
0.02 |
0.01 |
0.03 |
0.01 |
0.01 |
Average Damping factor |
||||||
Solid plate |
Through crack |
|||||
Mode No |
– |
00 |
200 |
400 |
600 |
900 |
1 |
0.01 |
0.01 |
0.06 |
0.06 |
0.05 |
0.06 |
2 |
0.04 |
0.01 |
0.00 |
0.01 |
0.01 |
0.08 |
3 |
0.01 |
0.01 |
0.08 |
0.08 |
0.01 |
0.01 |
4 |
0.01 |
0.01 |
0.01 |
0.00 |
0.00 |
0.01 |
5 |
0.01 |
0.01 |
0.02 |
0.02 |
0.00 |
0.00 |
6 |
0.02 |
0.01 |
0.00 |
0.00 |
0.01 |
0.02 |
7 |
0.01 |
0.01 |
0.00 |
0.00 |
0.00 |
0.00 |
8 |
0.03 |
0.02 |
0.01 |
0.03 |
0.01 |
0.01 |
ARBITRARY ORIENTED THROUGH CRACKS
The above behavior could be attributed to strain energy distribution due to configuration of the crack with respect to longitudinal axis of the plate.
-
Estimated average magnitude of Phase angle
The estimated average magnitudes of phase angle of solid plate and through crack inclined from 00 to 900 are tabulated in Table X
The average damping factor () was found to be minimum of 0.01 for most of the plate and through configuration expect being 0.08 for plate with 900 orientation at mode 2 and for plate with 200 and 400 orientation in mode 3.
The average magnitudes of phase angles are tabulated in Table XI are used for drawing bar chart and shown in Fig.28.
Fig. 28. Average magnitude of damping coefficient of solid & arbitrary
oriented through cracks
The bar chart shows that damping factor () was considerable only in mode 1, 2 and 3. The damping factor () was found to be not significant and of the order 0.06 for other higher modes. This could be attributed to different configurations of mode shapes at different modes.
-
CONCLUSION
The percentage of variation for amplitude, modal frequency, phase angles and damping factor was found to be in the order of 2%, 7%, 3% and 8% respectively
The magnitude of amplitude of vibration at resonance was found to be depend on modes numbers. The magnitude of amplitude for all through crack angle orientation and solid plate found to be comparable in mode 7. The magnitude of amplitude was found to be maximum for a plate with through crack inclined at 00. The magnitude of amplitude at given mode was found to be dependent on through crack and its orientation.
The modal frequency was dependent on mode numbers. The modal frequency at given mode shape was found to be depend on through crack and its orientation. The system response was found to be out-of-phase angle in more number of cases when compared to number of cases with in-phase angle response to forcing frequency.
The damping factor () was found to be varying for different orientation in mode 1 and mode 3. The damping factor () was found to be comparable and of the order 0.01 for all configuration of through crack orientation at higher modes.
-
Kiran D. Mali and Pravin M. Singru, Determination of the Fundamental Frequency of Perforated Rectangular Plates: Concentrated Negative Mass Approach for the Perforation, Advances in Acoustics and Vibration, Volume2013, Article ID972409, 6 Pages.
-
R. B. Bhat, Flexural vibration of polygonal plates using characteristic orthogonal polynomials in two variables. J. Sound and vibration (1987) 114(1), 65.71.
-
Kyeong-Hoon Jeong and Myung-Jo Jhung, Free vibration analysis of partially perforated circular plates, X International Conference on Structural Dynamics, EURODYN 2017
-
K. M. Liew, K.Y. Lam and S.T. Chow, Free vibration analysis of rectangular plates using orthogonal plate functions. Computers and structures, Vol.34, No.1.pp.79-85, 1990
-
A.W. Liessa, The free vibration of rectangular plates, Journal of Sound and Vibration, (1973) 31(3), 257-293.
-
T. Mizusawa, Natural frequencies of rectangular plates with free edges, Journal of sound and vibration, (1986) 105(3), 451-459.
-
Rice, J.R., and Levy, N., 1972. The Part through Surfae Crack in an Elastic Plate ASME Journal of applied mechanics, 3, pp. 185-194.
-
P. G. Young J. Yuan and S. M Dickinson, Three-Dimensional Analysis of the Free Vibration of Thick Rectangular Plates With Depressions, Grooves or Cut-Outs, Journal of vibration and acoustics.
-
Andrew D. Dimarogonas, Vibration of Cracked Structures: A State of the Art Review, Engineering Fracture Mechanics Vol. 55, No. 5, pp. 831-857, 1996
-
-
REFERENCES
-
-
C.S. Huang, A.W. Leissa, R.S. Li, Accurate vibration analysis of thick, cracked rectangular plates, Journal of Sound and Vibration 330 (2011) 2079 2093
-
P.V. Joshi, N.K. Jain, G.D. Ramtekkar, Analytical modelling and vibration analysis of internally cracked rectangular plates. Journal of Sound and Vibration 333 (2014), 58515864.
-
P. Cornwell , S.W.Doebling and C.R. Farrar, Application of The Strain Energy Damage Detection Method to Plate like Structures,
Journal of Sound and Vibration (1999) 224(2), 359-374
-
Ali beigi, Pedram Edalat.Mohamamad Reza Khedmati, Manouchehr Fadhavi, 2014, A numerical investigation into the crack effects on the natural frequency of the plates, international journal of maritime technology Vol.2/Summer 2014(29-41).
-
M. M. Banerjeea and J. Mazumdar, A Review of Methods for Linear and Nonlinear Vibration Analysis of Plates and Shells, 12th International Conference on Vibration Problems, ICOVP 2015
-
G. Aksu and R. Ali, Determination of dynamic characteristics of rectangular plates with cut outs using a finite difference formulation.