
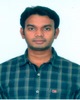
- Open Access
- Authors : T J Prasanna Kumar , K Venkata Rao , Ch Lakshmikanth , P Gopala Krishnaiah
- Paper ID : IJERTV9IS120253
- Volume & Issue : Volume 09, Issue 12 (December 2020)
- Published (First Online): 02-01-2021
- ISSN (Online) : 2278-0181
- Publisher Name : IJERT
- License:
This work is licensed under a Creative Commons Attribution 4.0 International License
Vibration Analysis on Sandwich Beams & Plates using Finite Element Technique
T J Prasanna Kumar
Assistant Professor, Department of Mechanical Engineering PVP Siddhartha Institute of Technology
Vijayawada, India
K Venkata Rao
Assistant Professor, Department of Mechanical Engineering PVP Siddhartha Institute of Technology
Vijayawada, India
Ch Lakshmikanth
Assistant Professor, Department of Mechanical Engineering PVP Siddhartha Institute of Technology
Vijayawada, India
P Gopala Krishnaiah
Assistant Professor, Department of Mechanical Engineering PVP Siddhartha Institute of Technology
Vijayawada, India
AbstractSandwich panels comprising composite face sheets and a lightweight core, such as polymer foams or balsa wood, are extensively employed in marine structures as they provide superior quasi-static bending stiffness and strength to monolithic beams. The present work deals with static and dynamic response of sandwich beams and sandwich plates consisting of a viscoelastic core layer and face layers subjected to two different boundary conditions. The problem is analysed using three- dimensional finite element methods and is modelled in ANSYS software. Static and dynamic response of the beam is studied by varying the parameters of the core layer such as its geometry. The sandwich plate subjected to point load is analysed statically and dynamically using finite element method under two different boundary conditions, simply supported and clamped- clamped conditions.
Static analysis of sandwich beams is performed by varying the thickness of core layer (t2/h) and varying the face layer material properties (isotropic, orthotropic) under simply supported and clamped- clamped boundary conditions subjected to line loading. From the analysis it is observed that the static deflection of sandwich beam with isotropic face layers is increasing with the increase in t2/h value under both boundary conditions, whereas the beam with composite face layers decreasing with increase in t2/h value. The dynamic response of the sandwich beam is obtained under same conditions. The mode frequency is also affected by t2/h value with isotropic as well as composite face layers. The sandwich plate subjected to point load is analysed by varying thickness of core layer (t2) with isotropic face layer subjected to clamped-clamped boundary conditions. The present study is carried out by varying the arrangement of core layer and face layers. The static deflection is varied with the thickness of the face layer. The damping coefficient has great effect on dynamic response of the sandwich plate.
The present work is useful in selecting the materials and their arrangement for safe design of sandwich structures in view of strength, stiffness, sufficient damping to control the harmonic response.
KeywordsStatic; dynamic; mode shape; ANSYS; sandwich
-
INTRODUCTION
-
SANDWICH STRUCTURES IN GENERAL
Sandwich structures are composite constructions of alloys, plastics, wood or other materials consisting of a core laminated and glued between two hard outer sheets (skins). The core is in general lightweight foam or solid core, honeycomb, web core, tubular or corrugated/truss core. Foams are usually plastic or ceramic, even the foamed metal; honeycomb, web or corrugated cores are metals or glass-reinforced plastic. Synthetic organic adhesives (epoxies, phenolic or polyesters) are employed to assemble sandwich components. Facing sheets are usually made from high- strength materials. In all cases of construction, the primary loads are carried by the outer sheets, and the transverse shear loads by the core.
Figure 1.1: 3-layer sandwich beam
Most sandwich structures have superior structural performance. The core separates and stabilizes the outer sheets against buckling under edgewise compression, torsion or bending. Other considerations such as heat resistance or electrical requirements dictate the choice of suitable materials. Sandwich structures have a high ratio of flexural stiffness to weight, resulting in a higher buckling resistance, lower lateral deformations, and higher natural frequencies.
-
VIBRATION PROBLEM AND EVOLUTION OF PASSIVE DAMPING TECHNOLOGY
The lack of damping in structural components has led to numerous mechanical failures over a seemingly infinite multitude of structures. For accounting the damping effects, lots of research and efforts have been done in this field to suppress vibration
and to reduce the mechanical failures. Since it was discovered that damping materials could be used as treatments in passive damping technology to structures to improve damping performance, there has been a flurry of on-going research over the last few decades to either alter existing materials, or develop entirely new materials to improve the structural dynamics of components to which a damping material could be applied. Vibration control of machines and structures incorporating viscoelastic materials in suitable arrangement is an important aspect of investigation. The use of viscoelastic layers constrained between elastic layers is known to be effective for damping of flexural vibrations of structures over a wide range of frequencies. The energy dissipated in these arrangements is due to shear deformation in the viscoelastic layers, which occurs due to flexural vibration of the structures. Multi- layered cantilever sandwich beam like structures can be used in aircrafts and other applications such as robot arms for effective vibration control. These members may experience parametric instability when subjected to time defendant forces. Viscoelastic materials are generally polymers, which allow a wide range of different compositions resulting in different material properties and behavior. Thus, viscoelastic damping materials can be developed and tailored fairly efficiently for a specific application.
-
Viscoelastic materials
Viscoelastic damping is exhibited in many polymeric and glassy materials and this internal damping mechanism is very important for damping augmentation to reduce vibration and noise in structures. The damping arises from relaxation and recovery of the polymer network after it has been deformed. Because viscoelastic materials exhibit both viscous and elastic characteristics, they hold unique properties. For example, in addition to undergoing an instantaneous displacement, when subjected to a constant force, they also undergo creep over a period of time. Alternatively, the force required to maintain a given deformation decreases over a period of time. This phenomenon is called relaxation.
The relaxation function is the stress response to a unit- step strain input.The stress-strain relationship for a viscoelastic material under cyclic loading takes on the form of an ellipse shown in Figure 1.2
Fig 1.2 Stress-Strain hysteresis loop for linear viscoelastic material (Jones, Handbook of Viscoelastic Damping, 2001).
-
Modelling of viscoelastic materials
Unlike structural components which exhibit fairly straight- forward dynamic response, viscoelastic materials are somewhat more difficult to model mathematically. Because most high load bearing structures tend to implement high strength metal alloys, which usually have fairly straight- forward stress-strain and strain-displacement relationships, the dynamics of such structures are simple to formulate and visualize. An engineer or analyst need only take into account the varying geometries of these structures and the loads which are applied to them to accurately model the dynamicsbecause the material properties of the structure and its components are generally well known. However, difficulty arises when viscoelastic materials are applied to such structures. This difficulty is mainly due to the strain rate (frequency), temperature, cyclic strain amplitude, and environmental dependencies between the viscoelastic material properties and their associated effect on a structures dynamics (Jones, 2001, Sun, 1995). Additionally, many viscoelastic materials and the systems to which they are applied exhibit nonlinear dynamics over some ranges of the aforementioned dependencies, further complicating the modeling process (Jones, 2001).
-
Typical applications and viscoelastic material characteristics
Many polymers exhibit viscoelastic behavior. Viscoelasticity is a material behavior characteristic possessing a mixture of perfectly elastic and perfectly viscous behavior. An elastic material is one in which there is perfect energy conversion, that is, all the energy stored in a material during loading is recovered when the load is removed. Thus, elastic materials have an in phase stress-strain relationship. Figure 1.6a illustrates this concept. Contrary to an elastic material, there exists purely viscous behavior, illustrated in Figure 1.6b. A viscous material does not recover any of the energy stored during loading after the load is removed (the phase angle between stress and strain is exactly /2 radians). All energy is lost as pure damping. For a viscous material, the stress is related to the strain as well as the strain rate of the material. Viscoelastic materials have behavior which falls between elastic and viscous extremes. The rate at which the material dissipates energy in the form of heat through shear, the primary driving mechanism of damping materials, defines the effectiveness of the viscoelastic material. Because a viscoelastic material falls between elastic and viscous behavior, some of the energy is recovered upon removal of the load, and some is lost or dissipated in the form of thermal energy. The phase shift between the stress and strain maximums, which does not to exceed 90 degrees, is a measure of the materials damping performance. The larger the phase angle between the stress and strain during the same cycle (Figure 1.3), the more effective a material is at damping out unwanted vibration or acoustical waves.
Figure 1.3: a) Elastic stress-strain behavior. b) Viscous stress- strain behavior. c) Viscoelastic stress-strain behavior
-
-
FINITE ELEMENT MODELLING
The Finite Element Method is essentially a product of electronic digital computer age. Though the approach shares many features common to the numerical approximations, it possesses some advantages with the special facilities offered by the high speed computers. In particular, the method can be systematically programmed to accommodate such complex and difficult problems as non-homogeneous materials, nonlinear stress-strain behavior and complicated boundary conditions. It is difficult to accommodate these difficulties in the least square method or Ritz method and etc. an advantage of Finite Element Method is the variety of levels at which we may develop an understanding of technique. The Finite Element Method is applicable to wide range of boundary value problems in engineering. In a boundary value problem, a solution is sought in the region of body, while the boundaries (or edges) of the region the values of the dependent variables (or their derivatives) are prescribed.
-
Finite element approaches
There are two differential Finite element approaches to analyze structures, namely
Force method
The number of forces (shear forces, axial forces & bending moments) is the basic unknown in the system of equations Displacement method
The nodal displacement is the basic unknown in the system of equations. The fundamental concept of finite element method is that is that a discrete model can approximate any continuous quantity such as temperature, pressure and displacement. There are many problems where analytical solutions are difficult or impossible to obtain. In such cases finite element method provides an approximate and a relatively easy solutions. Finite element method becomes more powerful when combined rapid processing capabilities of computers.
The basic idea of finite element method is to discretize the entire structure into small element. Nodes or grids define each element and the nodes serve as a link between the two elements. Then the continuous quantity is approximated over each element by a polynomial equation. This gives a system of
equations, which is solved by using matrix techniques to get the values of the desired quantities.
The basic equation for the Static analysis is:
[K] [Q] = [F] (2)Where [K] = Structural stiffness matrix
[F] = Loads applied [Q] = Nodal displacement vectorThe global stiffness matrix is assembled from the element stiffness matrices. Using these equations the model displacements, the element stresses and strains can be determined.
-
-
PROBLEM STATEMENT AND METHODOLOGY Selection of materials in designing the structural and/or mechanical components play an important role and is fixed based on the strength, stiffness, cost and other mechanical properties such as hardness, toughness, wear resistance etc.. Materials selected in view of the above requirements may not have internal damping capacity. When the structures are subjected to harmonic loads of high frequencies, conventional damping techniques such as providing external dashpots, arranging dynamic vibration absorbers may not have control on the dynamic response of the structures resulting in failure at
resonance frequencies.
Arrangement of soft-core material that requires more energy to deform provides internal damping of structures known as sandwich treatment. Sandwich treatment will reduce the amplitude of oscillation depending upon the location, volume and Mechanical properties of the core layer in the structure. It is also important to study the effect of sandwich treatment on static response of the structure in order to confirm the safe design.
The objective of the present research problem is to study the static and dynamic response of sandwich beam, consisting of a viscoelastic core layer and face layers, (where in one case the face layers are structural steel which is an isotropic material and in the other case the analysis is carried out for carbon epoxy composite material) with a) simply supported and b) clamped-clamped boundary conditions. Static and dynamic response of the beam is studied by varying the parameters of the core layer such as its geometry and damping coefficient.
The analysis is also carried out for sandwich plates, where structural steel and viscoelastic materials are used. The layer arrangement is done in two different ways. In one arrangement the core layer is viscoelastic material with 0.02×0.02m slot at its center, the top and bottom faces and the slot of viscoelastic layer are structural steel. In the next arrangement the viscoelastic material of 0.02×0.02m is positioned at the center of the middle layer. For both the arrangements, Static and dynamic response is studied by varying the parameters of the core layer such as its geometry and damping coefficient.
-
Finite Element Analysis
-
The problem is analyzed using 3-dimensional Finite Element Method and is modeled in ANSYS software.
-
Static and dynamic response of the beam is studied by varying the parameters of the core layer such as its thickness and damping ratio and varying the boundary conditions of the beam.
-
Static and dynamic response of the plate is studied by varying the parameters of the core layer such as its thickness and damping ratio.
-
-
Problem modelling
The present analysis the following assumptions are made for the present analysis
-
There is perfect bondingbetween face layers and core.
-
Loads are uniformly distributed throughout the layers.
-
Fibers are uniformly distributed in the matrix.
-
Fibers are perfectly aligned.
-
There is perfect bonding between fibers and matrix.
-
The composite lamina is free of voids and other irregularities.
-
All loads are within the elastic limit.
-
The plane cross section remains plane during and after loading.
-
The stress and strain relations are linear.
-
-
Element Type
The present problem is modeled in ANSYS software. The element used for the present work is SOLID185. SOLID185 is used for 3-D modeling of solid structures. It is defined by eight nodes having three degrees of freedom at each node: translations in the nodal x, y, and z directions. The element has plasticity, hyper elasticity, stress stiffening, creep, large deflection, and large strain capabilities. It also has mixed formulation capability for simulating deformations of nearly incompressible elasto-plastic materials, and fully incompressible hyper elastic materials. SOLID185 Structural Solid is suitable for modeling general 3-D solid structures. It allows for prism and tetrahedral degenerations when used in irregular regions. Various element technologies such as B-bar, uniformly reduced integration, and enhanced strains are supported.
-
Sandwich beam of complete viscoelastic core layer
TYPE-A beam: A Three layered sandwich beam of 1m length, 0.05m wide and 0.1m height is modeled in ANSYS software using 8 node brick element SOLID185. The thickness of the core layer is varied as per t2/h ratio (0.05, 0.10, 0.15, 0.20,
0.25 & 0.3). Where t2 is core layer thickness and h is the total height of the beam. The core layer is located at the mid height of the beam. The finite element model of sandwich beam with the above mentioned geometry is shown in Figure 3.2.
Fig.3.2: Finite element Model of sandwich beam-TYPE-A
-
Sandwich beam with material continuity
TYPE-B beam: A sandwich beam of 1m length, 0.05m wide and 0.1m height is modeled in ANSYS software using 8 node brick element SOLID185. The thickness of the core layer is varied as per t2/h ratio of TYPE-A beam and through calculations in order to maintain the same volume of core layer k2. Where k2 is viscoelastic layer thickness of Type-B beam and h is the total height of the beam. The model of sandwich beam with the above mentioned geometry is shown in Figure 3.3.
Fig 3.1: SOLID185 Element Geometry
D. Geometry
The considered problem is modeled with the following geometrical properties.
Sandwich beam with two different arrangements of viscoelastic layer are modeled. TYPE-A beam: complete viscoelastic core layer.
TYPE-B beam: beam having material continuity of face layers. TYPE-A plate: the core layer is viscoelastic material with 0.02×0.02m slot at its center, the top and bottom faces and the slot of viscoelastic layer are structural steel.
TYPE-B plate: the viscoelastic material of 0.02×0.02m is positioned at the center of the middle layer of the plate.
Fig.3.3: Geometric Model of sandwich beam-TYPE-B
G. Sandwich plate
TYPE-A plate: A square sand wich plate of 1m length, 1m wide and 0.1m height is modelled in ANSYS software using 8 node brick element SOLID185. The thickness of the core layer of 0.02×0.02m dimensions is varied as (0.01, 0.02 and 0.03) keeping the total height of the plate constant.The core layer is viscoelastic material with 0.02×0.02m slot at its center, the top and bottom faces and the slot of viscoelastic layer are structural steel. The modelled plate with the above mentioned geometric parameters is shown in Figure. 3.4.
Fig.3.4: TYPE-A sandwich plate geometric model TYPE-B plate: square sandwich plate of 1m length, 1m wide and 0.1m height is modeled in ANSYS software using 8 node brick element SOLID185. The thickness of the core layer of 0.02×0.02m dimensions is varied as (0.01, 0.02 and 0.03) keeping the total height of the plate constant. The viscoelastic material of 0.02×0.02 m is positioned at the center of the middle layer of the plate. The finite element model of the plate with TYPE-B geometric properties is shown in Figure 3.5.
Fig.3.6: TYPE-A sandwich beam with Simply Supported Boundary Conditions and line load at the top center nodes of the beam.
-
Material properties
The analysis is done by choosing the following material properties for the face layers and core layer.
Face Layer:
-
Structural steel
The face layers of the plate are chosen as structural steel and
One case of the analysis of beams is done by taking the face layers as structural steel. The material properties of structural steel are:
Ex= 207e9 Pa = 0.3
=7850 kg/m3
Fig.3.5: TYPE-B sandwich plate FEM model
-
LoadingConditions
-
A line load of 1000KN is applied at the top center nodes of the beam shown in Figure. 3.2 And Figure.
3.3 after meshing
-
A point load is applied at the top center node of the plate for both the TYPE-A and TYPE-B plates. (Figures- 3.4, 3.5)
-
-
Boundary conditions
Analysis of sandwich beams is carried out for two boundary condition cases
-
Simply supported boundary conditions
-
Clamped-clamped boundary conditions
The above mentioned boundary conditions are applied for both the TYPE-A and TYPE-B beams.
For the analysis of sandwich plates clamped boundary conditions are applied i.e. all areas representing the height of the plate are fixed. This clamped-clamped boundary condition is applied to both the cases of plates.
Second case of the analysis of beams is carried out by varying the face layer material.
Carbon/EpoxyAS4/3501-6 composite layers are chosen as the face layers. The material properties of the Carbon/EpoxyAS4/3501-6 composite are:
Ex
1.47E+11 Pa
Ey
1.03E+10 Pa
Ez
1.03E+10 Pa
xy
2.70E-01
yz
5.40E-01
zx
2.70E-01
Gxy
7.00E+09 Pa
Gyz
3.70E+09 Pa
Gzx
7.00E+09 Pa
1600kg/m3
-
-
Core layer
-
Linear viscoelastic material model is introduced by Herrmann and Peterson. The model assumes the deviatoricbehavior:
In the model, elastic bulk behavior is assumed when calculating the incrementally integrated pressure from the volume, V: p = K ln V. The parameters, G, G0, K (Bulk modulus) and are required to define the linear viscoelastic material model.
Viscoelasticity is similar to creep, but part of the deformation is removed when the loading is taken off. A common viscoelastic material is glass. Hence the analysis is carried out by taking the viscoelastic material as glass with properties as mentioned below.
Density = 2390 kg/m3 Go= 27.4e9 (Pa)
Bulk modulus = 60.5e9 (Pa) 1/ = .53
-
-
RESULT ANALYSIS AND DISCUSSIONS
-
Analysis of beams
The Static deflections of beams and dynamic response of the beams are predicted by imposing simply supported and clamped-clamped boundary conditions. The beam is modeled in two different ways by changing the arrangement of core layer. TYPE-A and TYPE-B beams are modeled with one case as isotropic face layers and single complete viscoelastic core layer and the other case is performed by varying face layers as composite face layers.
Static Analysis of beam under simply supported boundary conditions
The effect of thickness of the core on the static deflection is presented. Fig.4.1. sows the variations of static deflection with t2/h value for TYPE-A beam with isotropic face layers. It is observed that the static deflection is increasing with the increase in t2/h value because beam stiffness is decreasing. Fig.4.2. shows the variation of static defection with respect to t2/h for TYPE-A beam and having composite face layers. In this case the static deflection decreased with increasing with the t2/h value due to increase in the stiffness of the structure as the face layer material is the composite.
Fig.4.1: Static deflection vs. t2/h for TYPE-A beam with isotropic face layers
Fig.4.2: Static deflection vs. t2/h for TYPE-A beam with composite face layers
Fig.4.3 & 4.4 show the variation of static defection with t2/h value for TYPE-B beam with isotropic as well as orthotropic composite face layers. Static deflection of t2/h for simply supported beam with discontinuous viscoelastic core layers and isotropic face layers having material continuity is observed to be increasing with t2/h values. And for simply supported beam with discontinuous viscoelastic core layers and composite face layers having material continuity the static deflection is decreasing with t2/h values and a sudden fall in the static deflection is observed at t2/h value is equal to 0.2.
Fig.4.3: Static deflection vs. t2/h for TYPE-B beam with isotropic face layers
Fig.4.4: Static deflection vs. t2/h for TYPE-B beam with composite face layers
Static Analysis of beam under clamped-clamped boundary conditions
The static deflection of beam with respect to t2/h value with single complete viscoelastic core layer and isotropic face layers under clamped boundary conditions are obtained from the finite element based software ANSYS. A linear variation of static deflection with respect to the t2/h value with increasing trend is observed Fig.4.5. When the face layers are taken as a composite material a decreasing trend is observed with t2/h value Fig.4.6. The same graphs are plotted for discontinuous viscoelastic core layer Fig. 4.7 & 4.8.
Fig4.5: Static deflection vs. t2/h havingclamped-clamped boundary conditions for TYPE-A beam with isotropic face layers
Fig4.6: Static deflection vs. t2/h withclamped-clamped boundary conditions for TYPE- Abeam with composite face layers
Fig4.7: Static deflection vs. t2/h havingclamped-clamped boundary conditions for TYPE-B beam with isotropic face layers
Fig4.8: Static deflection vs. t2/h having clamped-clamped boundary conditions for TYPE- B beam with composite face layers
-
Dynamic Analysis of beam
the dynamic analysis is performed on the beam under simply supported loading conditions and clamped boundary conditions subjected to line load at the top center nodes of the beam. The beam is modeled with single complete viscoelastic core layer with isotropic face layers and single complete viscoelastic core layer with composite face layers. The effect of thickness of the core on the mode frequencies is presented. The first five natural frequencies are shown below. It is observed that mode frequency is increased with t2/h value in all modes for simply supported beam with single complete viscoelastic core layer and isotropic face layers Table 4.1. For simply supported beam with single complete viscoelastic core layer and composite face layers the frequency is high in all modes at t2/h value at 0.1 Table.4.2.
Table 4.1: First five mode frequencies for simply supported boundary conditions on TYPE-A beam with isotropic face layers
Table 4.2: First five mode frequencies for simply supported boundary conditions on TYPE-A beam with composite face layers
The dynamic behavior of beam is also obtained for simply supported beam with discontinuous viscoelastic core layer and isotropic face layers having material continuity. The mode frequency is observed to be increasing with t2/h value shown in Table 4.3. Table 4.4: shows the first five mode frequencies for simply supported beam with discontinuous viscoelastic core layer and composite face layers having material
continuity is presented. The model frequencies also obtained for clamped boundary conditions. Table 4.5-Table 4.7
Table4.3: First five mode frequencies with simply supported boundary conditions for TYPE- B beam with isotropic face layers having material continuity
Table 4.4: First five mode frequencies with simply supported boundary conditions for TYPE- B beam with composite face layers having material continuity
4.5: First five mode frequencies for clamped-clamped boundary conditions for TYPE-A beam with isotropic face layers
Table 4.6: First five mode frequencies for clamped-clamped boundary conditions for TYPE-A beam with composite face layers
Table 4.7: First five mode frequencies for clamped-clamped boundary conditions for TYPE-B beam with isotropic face layers having material continuity
Table 4.8: First five mode frequencies for clamped-clamped boundary conditions for TYPE-B beam withcomposite face layers having material continuity
-
Mode shapes for the above natural frequencies
The first five mode shapes of the beam are captured for all the cases and Figures 4.9 (a-e) represent the contour plots of first five mode shapes for simply-supported TYPE-A beam with isotropic face layers and core layer of thickness 0.1.
Fig.4.9(a) First mode shape; Fig. 4.9(b) Second mode shape
Fig. 4.9.(c) Third mode shape; Fig. 4.9.(d) Fourth mode shape
Fig. 4.9.(e) Fifth mode shape
-
-
ANALYSIS OF SANDWICH PLATE
In the present analysis, the Static deflections of plate are predicted by imposing clamped boundary conditions i.e. all the sides of the plate is fixed and point load of 1N is applied at top face center of the plate. The plate is modelled in finite element software ANSYS.The analysis of sandwich plate is carried out, where structural steel and viscoelastic materials are used. The layer arrangement is done in two different ways. In one arrangement the core layer is viscoelastic material with 0.02×0.02m slot at its center, the top and bottom faces and the slot of viscoelastic layer are structural steel. In the second arrangement the viscoelastic material of 0.02×0.02m is positioned at the center of the middle layer. For both the arrangements, Static and dynamic response is studied by varying the parameters of the core layer such as its geometry and damping coefficient. Figure 5.1 shows the sandwich plate geometric model with clamped-clamped boundary conditions.
Fig.5.1: Sandwich plate geometric model with clamped- clamped boundary conditions
-
Static Analysis of Plate results
The finite element mesh is refined until the results are satisfactory and then static, modal and harmonic analyses are performed on sandwich plate. Fig. 5.2 show the static deformation of the plate with inner core layer having 0.01thickness. Variation of static deflection with respect to t2 is plotted in Fig. 3 & 4. It is observed that there is a linear increase of the deflection with respect to t2, which is due to the reduction in stiffness of the structure.
Fig. 5.2 Contour plot for Static deflection of TYPE-B sandwich plate
Fig. 5.3 Static deflection of TYPE-B plate subjected to clamped-clamped boundary conditions
Fig. 5.4 Static deflection of TYPE-A plate subjected to clamped-clamped boundary conditions
-
Modal Analysis on Sandwich plate
Natural frequencies of the sandwich plate for the first five modes are obtained and data is provided in tables 5.1 & 5.2 against various values of t2. There is an increase in frequency with mode number and decreasing trend with respect to t2 is observed. Increase in t2 causes for the reduction in stiffness of the structure resulting in decreasing the natural frequencies.
Table 5.1: First five mode frequencies of differnent inner core thicknesses of TYPE-B plate and clamped-clamped boundary conditions
Table 5.2: First five mode frequencies of differnent core thicknesses of TYPE-A and clamped-clamped boundary conditions
The First five mode shapes of the beam for t2=0.01 are shown in Figs. 5.5(a-e)
Fig. 5.5 (a) First mode shape; Fig. 5.5 (b) Second mode shape
Fig. 5.5 (c) Third mode shape; Fig. 5.5 (d) Fourth mode shape
Fig. 5.5 (e) Fifth mode shape
-
-
CONCLUSIONS
-
Analysis of beam with isotropic face layer complete core layer
The static deflection () is increasing with t2/h value for beam subjected to clamped- clamped and simply supported boundary conditions for same loading.
The model frequency values of the beam increased with t2/h value.
-
Analysis of beam with composite face layer complete core layer
The static deflection () is decreasing with t2/h value for beam subjected to clamped- clamped and simply supported boundary conditions for same loading.
The model frequency values of the beam decreased with t2/h value
-
Analysis of beam with isotropic face layer having material continuity
The static deflection () is increasing with t2/h value for beam subjected to clamped- clamped and simply supported boundary conditions for same loading.
The model frequency values of the beam increased with t2/h value.
-
Analysis of beam with composite face layer having material continuity
The static deflection () is decreasing with t2/h value for beam subjected to clamped- clamped and simply supported boundary conditions for same loading.
The model frequency values of the beam decreased with t2/h value.
-
Analysis of plate with Type- A arrangement
In type A arrangement the core layer is viscoelastic material with 0.02×0.02m slot at its center, the top and bottom faces and the slot of viscoelastic layer are structural steel. The following conclusions are obtained.
Static deflection of plate with inner core layer subjected to clamped-clamped boundary conditions is observed to be increasing with t2.
The model frequency is increased with t2 value.
-
Analysis of plate with Type- B arrangement
In the type-B arrangement the viscoelastic material of 0.02×0.02m is positioned at the center of the middle layer. The following conclusions are obtained.
Static deflection of plate with inner core layer subjected to clamped-clamped boundary conditions is observed to be increasing with t2.
The model frequency is increased with t2 value.
-
-
REFERENCES
-
Kar, R.C. and Hauger,W., Stability of a sandwich beam subjected to a nonconservative force Computer and structures 46 (1993), pp. 955- 958.
-
Ray,K. and Kar, R.C., Parametric instability of a sandwich beam under various boundary conditions, Computers and structures 55 (1995), pp. 857-870.
-
Ray,K. and Kar, R.C., The parametric instability of partially covered sandwich Beams, Journal of Sound and Vibration 197 (1996), pp. 137-152.
-
Ray,K. and Kar, R.C., Parametric instability of a dual cored sandwich beam, Computers and structures 61 (1996), pp. 665-671.
-
Ray,K. and Kar, R.C., Parametric instability of a symmetric sandwich beam with higher order effects, Computers and structures 60 (1996), pp. 817-824.
-
Lin, C.Y., and Chen, L.W., Dynamic stability of a rotating beam with a constraineddamping layer, Journal of sound and vibration 267 (2002), pp. 209-225.
-
Trompette, P., Boillot, D., and Ravanel, M.A., The effect of boundary conditions on the vibration of a viscoelsticlly damped cantilever beam, Journal of Sound and Vibration 60 (1978), pp. 345- 350.
-
Mace, M., Damping of beam vibrations by means of a thin constrained viscoelastic layer: Evaluation of a new theory, Journal of sound and vibration 172 (1994), pp. 577-591.
-
Gorrepati, M. and Rao, M.D., Analysis of modal parameters of adhesively bonded double-strap joints by the modal strain energy method, Journal of Vibration and Acoustics, Trans of ASME 118 (1996), pp. 28-35.
-
Chen, Q. and Chan, Y.W., Integral finite element method for dynamical analysis of elastic-viscoelastic composite structures, Computers and structures 74 (2000),pp. 51- 64.
-
Nayfeh, S.A., Damping of flexural vibration in the plane of lamination of elsticviscoelastic sandwich beams, Journal of Sound and Vibration 276 (2004), pp. 689-711.