
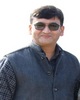
- Open Access
- Authors : Surinder Kumar , Dr. Varinder Kr. Kanwar
- Paper ID : IJERTV10IS010068
- Volume & Issue : Volume 10, Issue 01 (January 2021)
- Published (First Online): 16-01-2021
- ISSN (Online) : 2278-0181
- Publisher Name : IJERT
- License:
This work is licensed under a Creative Commons Attribution 4.0 International License
Wastocrete & Wastoricks: A Study to Conserve Environment by Utilizing TPIS as Construction Material as Partial Replacement of Cement, Sand and Clay
Mr. Surinder Kumar2 , FIE Research Scholar,
Chitkara University, HP
Dr. Varinder Kr. Kanwar1 , FIE VC-cum- Professor,
Chitkara University, Himachal Pradesh, India
Abstract Cement and Sand are the main component of Concrete which widely used around the world. Cement as mentioned above one of the basic major gluing materials used by construction industry mainly for concrete in large volumes. Its production leads to significant emission of carbon-dioxide; production of one ton of cement emits approximately one ton of carbon-dioxide. The sources of good quality river sand is also depleting very fast. Sand is now being extracted at a rate far greater than their renewal. Clay is the main component of bricks, which is another major building construction materials. There is environmental problem due excessive use of topsoil in brick manufacturing. Loss of topsoil from agriculture land is also an important environmental concern. On the other hand Tooth Paste manufacturing industries generate sludge (TPIS) in large quantity. Despite having high amount of calcium carbonate, as per present practices, such sludge are being used for filling low- lying areas or being burnt in cement kiln along with other toxic sludge. This paper presents an experimental investigation carried out to analyze the feasibility of using TPIS in partial replacement of cement , sand and clay. From experimentation, it is observed that TPIS can be used in replacement of sand upto 15% to meet compressive strength requirements for M20 grade and clay can be replaced upto 20% in class-I bricks. The concrete so approved is named as Wastoncrete and bricks as Wastoricks.
Keywords: Concretes, Bricks, Green House Effect, Global Warming, Toothpaste Industrial Sludge, TPIS, Compressive Strength, Wastocrete, Wastoricks.
-
INTRODUCTION
Various studies indicate that, out of the total constructed area existing in India in 2030, about 70% would have been constructed between 2010 and 2030. Building construction in India is estimated to grow at a rate of 6.6% per year during the period 2005 to 2030. The building stock is expected to multiply five times during this period (Figure-1.1), resulting in a continuous increase in demand for building materials. To cope up with this infrastructure & housing necessity, the country needs to build thousands of units of houses at least for the next 10 years. Housing is the primary need of every human being. As for the human body, carbons are the building block, cement concrete & bricks are the building blocks of a house. There is great demand for construction and thus increasing pressure for use of natural resources causing their acute shortage.
Figure-1.1: Projected Increase in Building Area in India [3]
This rapid industrialisation and urbanisation which is always associated with the problem of environmental degradation. With the advent of pollution control technologies, the industries are able to combat air and water pollution.
However, the treatment of industrial effluents invariably results in the generation of large volume of the sludge transferring pollutants from liquid phase to solid phase. Under the guidelines for Management and Handling of hazardous wastes, land fill disposal is recommended for inorganic sludge from wastewater treatment plants (MoEF, 1991). Besides collection, transport and storage of wastes, construction of secured land fill sites pose problems of land acquisition, high land and construction cost, closure of site, environmental monitoring etc. Therefore, it is now a global concern to find a socio, techno-economic and eco-friendly solution to dispose industrial solid wastes. The recycling of industrial solid wastes as substitute for building materials is not only environment friendly but also cost effective alternative way to sustain a cleaner and greener environment.
Concrete, the single most widely used building material around the globe is a heterogeneous composite that consists of combination of readily available basic building materials including cement, water, coarse aggregate, fine aggregate. The reason behind the enormous use of concrete in the construction sector lies in its versatile, reliable and sustainable nature, because of its strength, rigidity, durability, mouldability, efficiency and economy. Humans have been using concrete in their pioneering architectural feats for millennia.
Brick is one of the most important and widely used building material all over the world. India is the second largest
producer in the world producing around 240 billion bricks annually. There are around 140,000 brick kilns operating in India which contribute more than 10% to the total brick production of the world (Source:SAARC Report [7] ) The brick-clay industry employs around 10 million people in India. It is estimated that in India 180 billion tons of common burnt clay bricks are consumed annually approximately 340 billion tons of clay about 5000 acres of top layer of soil dug out for bricks manufacture, soil erosion, emission from coal burning or fire woods which causes deforestation are the serious problems posed by brick industry(Source:Sahu [9] ).
It is now a serious concern, to find a social, techno- economic, environmentally sustainable solution to find the alternative to clay bricks.This problem natural materials can be tackled by using some waste material to replace some part of the primary component which in turn can also solves the disposal problem of the waste material. This will also help in economizing the resources. It will help in conservation of resources and reducing pollution. Also, there will be reduction in construction cost. One such material is toothpaste industry sludge. Huge amount of dry toothpaste sludge is produced on daily basis. There are two ways to solve the problem. Research problem and objectives expressing need as well as solution have been indicated below in figure-1.2(a & b).
Figure-1.2(a): Present Scenario-Problem Tree
Figure-1.2(b): Proposed Scenario-Solution Tree
Few studies have been performed on utilizing sludge materials in the process of concrete making. Pitroda et. al (2013) [4] conducted an experimental study for the innovative use of hypo sludge in concrete formulations as a supplementary cementitious material was tested as an alternative to traditional concrete. The cement has been replaced by waste paper sludge accordingly in the range of 0% (without hypo sludge), 10%, 20%, 30% & 40% by weight for M-25 & M-40 mix. Ms. Monica C. Dhoka (2013) [6] studied application of industrial waste such as marble powder, quarry dust, wood ash, paper pulp, etc. to reduce consumption of natural resource and energy and pollution of the environment. Use of such waste material saves 14%-20% amount of cement.
Abhishek Jain et al., (2013), [1] has proposed that the experimental studies on mortar containing flyash as a partial replacement of sand by weight as well as by volume were carried out to quantify its utilization. So, we decided to replace dry toothpaste sludge as soil. Experiments have been performed to study the effect of 10-50% clay replacement with toothpaste sludge. The flyash mortar mix 1:1:5 (cement : flyash : Sand) by weight consumes about 20% less quantity of cement and overall consumption of flyash is also less. Further Akshay C. Sankh et al. (2014) [2], states in his paper foundry sand which is very high in silica is regularly discarded by the metal industry. Currently, there is no mechanim for its disposal, but international studies say that up to 50 percent foundry sand can be utilized for economical and sustainable development of concrete. Bilgin et al.(2012)[3] experimented and analysed the possible utilization of waste marble powder in brick industry. They found that addition of marble dust addition has positive effects on physical, chemical, and mechanical strengths of the produced industrial bricks.
Experimental and analytical work on possible utilization of various industrial by-products/ waste is widely reported in 2003, Weng et al. [10] explored the possible utilization of dewatered and oven dried sludge as brick materials. Results show the satisfactory addition of as much as 20% sludge at 960°C to 1000°C, although the optimum addition of 10% sludge with 24% moisture content in a moulded mix and firing temperature of 880°C to 960°C. Alaa.A.Shakir et al.(2013) [8] in his review paper, reviewed recycling various waste material in bricks production. The effects of those wastes on the bricks properties as physical, mechanical properties will be reviewed and recommendations for future research as out comings of this review will be given. This reviewed approach on bricks making from waste is useful to provide potential and sustainable solution.
So, it was decided to replace dry toothpaste sludge as soil. Experiments have been performed to study the effect of 10- 50% clay replacement with toothpaste sludge. Similarly, it was decided to use dry toothpaste sludge as partial replacement of cement and sand. Experiments have been performed to study the effect of 5-25% cement and sand replacement with toothpaste sludge (TPIS).
-
MATERIALS AND PROPERTIES
A. Research Methodology:
Keeping all this in view, the objective of study, the methodology was decided to study the waste and behaviour of concrete while adding of waste with different proportions in concrete mix i.e 0%, 5%, 10%, 15%, 20% & 25% by replacing cement in Case-A , replacing sand in Case-B and in Case-C clay was replaced with TPIS as 0%, 10%, 20% , 30%, 40% & 50% then testing for compression strength, water absorption, etc. as shown below.
B. Materials Used:
Materials used in the study i.e. TPIS, Cement, Sand, Coarse aggregates and Clay were locally procured. The toothpaste sludge was taken from a local toothpaste making factory. The sludge was kept in containers. It was available in powdered form Figure- 2.1. The physical properties of sludge were as per Table-2.1. The chemical composition was calculated from XRF/XRD tests. The composition of TPIS is described as below in Figure- 2.2 and Table 2.2(a&b).
Figure- 2.1: Lime sludge from the toothpaste Industry(TPIS)
Table-2.1: Physical Properties of Material Used
Figure- 2.2: Percentage concentration of elements present in the toothpaste sludge(XRF studies)
Composition
Percentage
O
50.15%
Ca
20.61%
Si
20.55%
C
7.23%
Na
0.64%
S
0.39%
Mg
0.26%
Al
0.07%
Cl
0.03%
P
0.03%
Fe
0.02%
Sr
0.01%
K
53ppm
Cu
14ppm
Zr
5ppm
Composition
Percentage
O
50.15%
Ca
20.61%
Si
20.55%
C
7.23%
Na
0.64%
S
0.39%
Mg
0.26%
Al
0.07%
Cl
0.03%
P
0.03%
Fe
0.02%
Sr
0.01%
K
53ppm
Cu
14ppm
Zr
5ppm
Figure-2.3: XRD pattern of Toothpaste Waste Table-2.2a: Chemical composition of toothpaste sludge
Sr.no.
Element Oxides
Toothpaste Samples Mass (%)
1.
SiO2
28.9
2.
Al2O3
0.962
3.
Fe2O3
0.116
4.
TiO2
2.16
5.
CaO
59.3
6.
MgO
0.476
7.
Na2O
0.34
8.
K2O
0.839
9.
SO3
3
10.
P2O5
3.68
11.
MnO
0.0138
12.
PbO
0
13.
ZnO
2.71
14.
S2O2
0.123
Sr.no.
Element Oxides
Toothpaste Samples Mass (%)
1.
SiO2
28.9
2.
Al2O3
0.962
3.
Fe2O3
0.116
4.
TiO2
2.16
5.
CaO
59.3
6.
MgO
0.476
7.
Na2O
0.34
8.
K2O
0.839
9.
SO3
3
10.
P2O5
3.68
11.
MnO
0.0138
12.
PbO
0
13.
ZnO
2.71
14.
S2O2
0.123
Table-2.2b: XRD analysis for Compound study in toothpaste samples
Material
Specific Gravity
Fineness Modulus
Toothpaste Sludge
2.38
1.51
The clay soil was taken from a nearby locally based brick kiln. Table-2.3 below presents the tabulation of the chemical composition for clay calculated from XRF tests.
Table-2.3: Chemical Composition of Clay
S.No.
Component
Percentage
1
SiO2
67
2
Al2O3
26
3
Fe2O3
3
4
Na2O
1
5
MgO
1
6
P2O5
Trace
7
SO3
0.5
8
K2O
2
9
CaO
0.1
10
Cr2O3
Trace
11
MnO
Trace
12
NiO
Trace
13
CuO
Trace
14
ZnO
Trace
15
Cl
Trace
-
Mixing and Proportions:
In this study wastocrete, 11 mixes (including different Cement and Sand replacement mixes) were evaluated to study their engineering properties and to find out their behavior. Crushed & powdered TPIS was partially replaced for the Cement and fine aggregate (sand) in different replacements. The materials, work designs, and all tests are explained in this chapter.
Mix Constituents
For one cum of concrete (Kg)
Cement
348.33
Water
191.58
Fine aggregate
651.24 at 1.8% moisture (i.e. SSD condition)
Coarse aggregate
1201.10 kg-SSD condition i.e. 0.8% moisture
20mm = 600.55 kg 10mm = 600.55 kg
Admixture
3.4
Water cement ratio
0.54
Workability in mm after 45 min
85
3days average compressive strength (N/mm2 )
9.3
7days average compressive strength (N/mm2 )
14.3
28days average compressive strength (N/mm2 )
29.0 N/mm2
Table: 2.4- Mix Proportion Quantities M20 concrete
Finally a mix of concrete of proportion M20 (1:1.85:3.50) was adopted for the present study (Table 2.4). The first mix MC is control mix having only cement as binder. The second mix TPSC series had toothpaste waste (powder-TPIS) as replacement of cement. The Third mix TPSS series had toothpaste waste (powder-TPIS) as replacement of Sand. The compressive strength tests were conducted to monitor the strength development of concrete containing upto 20% of this pozzolana as cement and Sand replacement.
For case-C i.e. wastoricks, casting of specimen bricks (230mm x100mm x70mm) with varying proportions of constituent materials. Optimum mix proportion for preparing base mix (BM) was decided as per the commercially available brick kiln manufactured bricks.
Table 2.5- Description of Mixes
Set No.
Designations
Mix Description
1
MC
Mix with Cement and natural aggregates (Control Mix)
2
TPSC-1
Mix with Cement and natural Aggregates with 5% partial replacement of Cement with TPIS
TPSC-2
Mix with Cement and natural Aggregates with 10% partial replacement of Cement with TPIS
TPSC-3
Mix with Cement and natural Aggregates with 15% partial replacement of Cement with TPIS
TPSC-4
Mix with Cement and natural Aggregates with 20% partial replacement of Cement with TPIS
TPSC-5
Mix with Cement and natural Aggregates with 25% partial replacement of Cement with TPIS
3
TPSS-1
Mix with Cement and natural Aggregates with 5% partial replacement of Sand with TPIS
TPSS-2
Mix with Cement and natural Aggregates with 10% partial replacement of Sand with TPIS
TPSS-3
Mix with Cement and natural Aggregates with 15% partial replacement of Sand with TPIS
TPSS-4
Mix with Cement and natural Aggregates with 20% partial replacement of Sand with TPIS
TPSS-5
Mix with Cement and natural Aggregates with 25% partial replacement of Sand with TPIS
Attempts were made to study and analyse the effect of partial replacement of brick clay with TPIS, in order to observe the effect of replacement along with maximum utilization of waste. After incorporating the changes in the Base Mix( BM) , it was made the reference to compare the performance. Efforts were also made to study and analyse the effect of the addition of TPIS with an aim to improve the compressive strength of brick while minimizing water absorption and weight density. In all 250 specimen bricks (the 40 bricks for each mix) were burnt in the kiln.
Set No.
Designa- tion
Cementitious Material (Kg)
Fine Aggregates (Kg)
Coarse aggreg ate (Kg)
W/C Ratio
Cement
TPIS
Sand
TPIS
1
MC
15.00
—
27.50
—
52.50
0.54
2
TPSC-1
14.25
0.75
27.50
—
52.50
0.54
TPSC-2
13.50
1.50
27.50
—
52.50
0.54
TPSC-3
12.75
2.25
27.50
—
52.50
0.54
TPSC-4
12.00
3.00
27.50
—
52.50
0.54
TPSC-5
11.75
3.25
27.50
—
52.50
0.54
3
TPSS-1
15.00
—
26.13
1.37
52.50
0.54
TPSS-2
15.00
—
24.75
2.75
52.50
0.54
TPSS-3
15.00
—
23.36
4.14
52.50
0.54
TPSS-4
15.00
—
22.00
5.50
52.50
0.54
TPSS-5
15.00
—
20.63
6.87
52.50
0.54
Water (lts)
8.10
The size of test specimens was 230x100x70mm with a percentage of TPIS as 0%, 10%, 20% , 30%, 40% & 50%.
TPIS is mixed properly in the ingredients of brick in desired proportion. Sample prepared from all these mixes were compared and tested for several strength parameters.
Figure-2.4: Photographs Showing Mixing of Ingredients
-
Preparation, Procedure of Mixing and Curing:
The proportioning of quantity of both cement and aggregate is done by weight as per the concrete mix design. The water and the admixture are measured by volume. All measuring equipments were maintained in clean serviceable condition with their accuracy periodically checked. The workability tests are carried out immediately after mixing of concrete using the slump cone test. The specimens are used according to the specification laid down in IS 516:1959. Standard cast iron cube moulds of size 150x150x150mm are used in the preparation of test specimens. The specimens are cured for 28 days marked then completely immersed in city water until the time of testing.
Brick specimens of 230x100x70cm were prepared with a forming pressure.
Figure-2.5: Brick Specimens with varying % age of TPIS
The specimens were de-moulded and sundried for 3-4 days. Samples were stacked as shown in Figure-2.6 and then were fire burnt in the kiln. More than 250 successful brick specimen were prepared for carrying out various tests.
Figure-2.6: Stacking of various Brick Specimens
Bricks are burnt at high temperature . All the water is removed at the temperature of 650 degrees but were burnt at a temperature of about 1100 degrees, because the fusing of sand and lime takes place at this temperature and chemical bonding takes between these materials after the temperature is cooled down resulting in a hard and dense mass.
-
-
RESULTS AND DISCUSSIONS
The experimental results of this study concerned with concrete properties are presented and discussed for the fresh properties, unit weight tests were conducted, while for the hardened properties, compressive strength.
The results and properties of various mixes tested are shown below.
Figure-3.1: Tests on Brick Specimens
A. Unit Weight of Concrete:
The fresh unit weight for all concrete mixes was determined and plotted in Figure- 3.2.
3000
2000
30
mpressive Strength N/mm2
mpressive Strength N/mm2
25
20
15
10
5
0
Figure-3.3
The compressive strength with age for the control mix and mixes containing 5, 10,15,20 and 25% of TPIS as partial replacements of Cement & sand and the comparison between the values of the compressive strength for the same mixes are plotted and show in figures-3.3.
Various properties of the bricks produced after replacement of clay with TPIS has been discussed in following heads.
-
Weight of the Brick after Formation
The weight of a few samples of each type was taken and then average weight was found out to get the desired standard weight. The average weight of each type is given
Unit Weight Kg/m3
1000
0
5% 10% 15% 20% 25%
below in Table-3.1.
Table-3.1: Weight of Bricks
S.No.
Brick type
Weight(kg)
1
BM
2.920
2
B10
2.228
3
B20
1.950
4
B30
1.831
5
B40
1.765
6
B50
1.313
S.No.
Brick type
Weight(kg)
1
BM
2.920
2
B10
2.228
3
B20
1.950
4
B30
1.831
5
B40
1.765
6
B50
1.313
Figure- 3.2: Graphs showing trends of reduction in Unit Weight w.r.t %age Replacement
The results indicate that the using of TPIS led to the density of the concrete mixes decreasing as compared with the control mix. This is because of the lower specific gravity of the TPIS as compared with Cement and Sand. The Mixes with Cement and natural Aggregates with partial replacement of Cement with TPIS indicated lower densities relative to Mixes with
partial replacement of Sand with TPIS. This decrease is due to 4
the lower specific gravity of sand compared to cement. However, densities as compared with control mix. This behavior may be exhibited to the advantage of the reduction of 2
weight in concrete mix due to the using of TPIS.
B. Compressive Strength Test on Concrete:
The compressive strength results (IS: 516-1959 (RA 2013)) for all mixes at ages of 3, 7, 14 and 21days are shown in Figur-3.3.
4
Modified Clay Bricks-Weigh
Figure- 3.4(a)
Modified Clay Bricks-Weigh
2
0 Figure- 3.4(b)
Figure- 3.4(a) & (b): Graphs showing Weight of Modified Bricks
-
Compressive Strength Test on Bricks
The result of compressive strength shows that, the compressive strength of brick has increased on addition of sludge to a limited quantity of 10% and 20% i.e. B10, B20, but the compressive strength of brick mix will decrease on excess addition of sludge i.e. more than 20%. Figure-3.5 shows the comparative study of compressive strength test results of various mixes.
S.no.
Bricks type
Compressive strength ( N/mm2 )
1
BM
12.02
2
B10
12
3
B20
11.57
4
B30
7
5
B40
6
6
B50
4.5
S.no.
Bricks type
Compressive strength ( N/mm2 )
1
BM
12.02
2
B10
12
3
B20
11.57
4
B30
7
5
B40
6
6
B50
4.5
Figure-3.5a: Compression Test on UTM Table-3.2: Compressive Strength of Bricks
Figure-3.6: SEM of Bricks without and with TPIS
-
Efflorescence Test
The bricks were tested as per IS: 3495 (Part-III) for efflorescence by placing them in tray in vertical position and adding 25cm water twice. Then physical examination was done.
S.no.
Brick type
Efflorescence
1
BM
Slight
2
B10
Slight
3
B20
Slight
4
B30
Moderate
5
B40
Moderate
6
B50
Heavy
S.no.
Brick type
Efflorescence
1
BM
Slight
2
B10
Slight
3
B20
Slight
4
B30
Moderate
5
B40
Moderate
6
B50
Heavy
Table-3.3: Efflorescence of Bricks
Compressive Strength N/m
15
10
5
Figure-3.5: Compressive Strength of Bricks
Microscopic image of standard brick without TPIS mix and the bricks with TPIS mix(20% replacement) is shown in Figure-3.6, respectively.
-
Soundness Test
Two bricks of same type were taken and struck against each other. If it does not break and a metallic ringing sound forms then the bricks are considered sound. Table-3.4 below shows the details of soundness of samples.
Table-3.4: Soundness of Bricks
S.no
Brick type
Soundness
1
BM
Satisfactory
2
B10
Satisfactory
3
B20
Satisfactory
4
B30
Not Satisfactory
5
B40
Not Satisfactory
6
B50
Not Satisfactory
-
Water Absorption
The bricks of each type were dipped in water tank and water absorption was found out on a period of 24 hours (Water Absorption of Brick – IS:3495-Part 2-1992). The Table-3.5 below shows the weight of each type and the percentage of water absorption after standard time.
Table-3.5: %age Absorption after 24 hours
Sr.No.
Brick Type
Initial Weight
24 hours weight
% weight after absorption
1
BM
3.008
3.480
15.70
2
B10
2.232
2.600
16.50
3
B20
1.878
2.201
17.20
4
B30
1.763
2.161
22.60
5
B40
1.712
2.237
30.70
6
B50
1.363
1.908
41.20
Figure-3.7 below shows the pictures of water absorption process in which each brick was dipped in separate container containing water.
24 hrs absorption
50
Figure-3.7: Water Absorption after Standard Time
-
pH Test
pH is a measure of the acidity or basicity of an aqueous solution. Solutions with a pH less than 7 are said to be acidic and solutions with a pH greater than 7 are basic or alkaline. Pure water has a pH very close to 7. It is generally determined using a buffer solution and a PH meter which indicates the value once the electrode is dipped in the solution whose pH is to be determined. pH of water in which bricks were dipped was tested for a period of 7 days, 21 days and 28 days and compared with fresh water. The Table-3.6 below shows the value for pH test.
Table-3.6: pH Test of Water Contained Bricks
9
8
7
Figure-3.9: pH Test of Bricks
-
Thermal Conductivity Test
Samples prepared were also tested for conductivity after 28 days after burning process. Below mentioned Table-
3.8 shows conductivity of samples.
Table-3.8: Conductivity Test of Bricks
S. no.
Brick type
W/mK
1
BM
0.901
2
B10
0.851
3
B20
0.833
4
B30
0.805
5
B40
0.773
6
B50
0.703
Figure-3.10 below shows the thermal conductivity
28 day
1
0.5
0
S.
no.
Brick type
Fresh Water
7 day
21 Day
28 Day
1
BM
7.3
7.31
7.78
8.58
2
B10
7.3
7.68
7.79
8.59
3
B20
7.3
7.68
7.82
8.61
4
B30
7.3
7.83
7.92
8.69
5
B40
7.3
7.71
7.81
8.65
6
B50
7.3
7.84
7.92
8.71
S.
no.
Brick type
Fresh Water
7 day
21 Day
28 Day
1
BM
7.3
7.31
7.78
8.58
2
B10
7.3
7.68
7.79
8.59
3
B20
7.3
7.68
7.82
8.61
4
B30
7.3
7.83
7.92
8.69
5
B40
7.3
7.71
7.81
8.65
6
B50
7.3
7.84
7.92
8.71
Figure-3.10(a)
Modified Clay Bricks
1
Figure-3.8: pH meter
0.5
0
Figure-3.10( a & b): Conductivity Test of Bricks
If compared to tested common commercial brick by considering thermal conductivity with BM , it has reduced with increase in TPIS, the optimum low thermal conductivity can be proposed was 0.700W/mK which has 30% TPIS as partial clay replacement. The normal thermal conductivity of brick in range of 0.7 to 0.9 W/mK .
The thermal conductivity of the brick decreases due to the presence of TPIS, which has low thermal conductivity. In the long run, it can attract the potentials for development
most tropical areas where desirable of low thermal conductivity construction materials to optimize the load of cooling or heating within the space of the building.
-
Hardness Test
This test was done to know the hardness of bricks. In this test, scratches are made on the surface of the brick by a hard thing. If it does not leave any impression on the brick surface then it will be considered as good quality bricks. Further in structure test a brick is fractured and firmly investigated. If any flaws, holes or cracks are seen inside the broken brick, then it is considered as poor quality brick.
Table-3.9: Soundness of Bricks
S.no
Brick type
Soundness
1
BM
Satisfactory
2
B10
Satisfactory
3
B20
Satisfactory
4
B30
Satisfactory
5
B40
Not Satisfactory
6
B50
Not Satisfactory
-
Dimensional Accuracy
The bricks so produced were tested for shape and size accuracy. It was found that upto 20 to 30% TPIS replacement, bricks have maintained shape and size as per class-I brick standards but afterwards it starts crumbling from edges and also looses shape.
DISCUSSION:
The following observations can be drawn from these figures of test results for case-A& B:
-
The using of TPIS has a highly negative effect and reduction on the compressive strength at all ages of the test in set no.2 mixes (MCTPSC) i.e. partial replacement of cement with different % of TPIS. This effect increases relatively with the increase of TPIS replacement. This behavior may be because of lower or inert behaviour or non-cementitious properties between the TPIS and cement paste, mainly attributed to the non-reaction of TPIS. At initial replacement of 5 to 10% there has been decrease in strength with in permissible limits but on higher replacement it had been substantially high. An exception to this trend at initial replacement, which shows compressive strength with in lesser than those for mixes MCTPSC -3 to MCTPSC -5, may be that this increment is due to the effect of pozzolanic activity (very fine TPIS particles) prevailing over the inert effect of TPIS. Figure-3.3 clearly indicates the continuous fall in strength with increase in replacement percentage in comparison to the strength of control mix.
-
MCTPSS (Set No.-3) mixes show a significant maintenance in strength with age. It can be observed that the percentage of compressive strength with age relatively maintained with the increment of TPIS replacements of sand with the strength of Control Mix (Figures-3.3) for MCTPSS upto replacement of sand by 15% i.e. MCTPSS-3. For example, compared with compressive strength of control mix average percentage compressive strength for mixes MCTPSS-
1, MCTPSS-2 and MCTPSS-3 are 99.79, 98.80 &
96.90% i.e. very negligible fall in strength i.e. -0.22,
-1.20 & -3.10 % respectively. This behavior refers to the pozzolanic activity as well as filler attribute of TPIS with very fine sand particles, as previously mentioned in the literature section. Figure-3.3 clearly indicates the overlapping of graph lines of compressive strength with increase in replacement percentage upto 15% in comparison to the strength of control mix graph lines.
-
But for mix MCTPSS-4 & 5 i.e. replacement of sand by 20 % & 25% of TPIS there has been substantial decrease in strength in comparison to results of control mix (Figures-3.3) i.e. -13.31% & -25.45%. Figure-6.4 indicated the segregation of graph lines of 20% & 25% from control mix & replacement of sand upto 15% which clearly indicates the continuous fall in strength with replacement percentage beyond 15% in comparison to the strength of control mix and replacement of sand below 15%.
-
The following observations can be drawn from these figures of test results for case-C:
-
The weight results show (Table-3.1) that all the bricks are light in weight as compared to the standard brick BM which does not contain any quantity of TPIS. So, all the bricks are light weight, which is an advantage in construction being lighter especially for seismic sensitivity (Figure-3.4(a)&(b).
-
B10 & B20 mix proportions show a significant maintenance in strength. It can be observed that the percentage of compressive strength relatively maintained with the increment of TPIS replacements of clay with the strength of Control Mix (Table-3.2) upto replacement of clay by 20% i.e. B20. For example, compared with compressive strength of control mix average compressive strength for mixes BM, B10 and B20 are 12.02, 12.0 &11.57 respectively i.e. very negligible fall in strength. This behavior refers to the pozzolanic activity as well as filler attribute of TPIS. Figure-3.5 clearly indicates the flattening of graph lines of compressive strength with increase in replacement percentage upto 20% & parallel to the strength of control mix graph lines.
-
According to the Indian standards (As per the IS 1077
: 1992, Common Burnt Clay Building Bricks – Specification) , the bricks – class I and class II, when tested in accordance with the procedure laid down in IS 3495 ( Part 2) : 1992 after immersion in cold water for 24 hours, water absorption shall not be more than 20 percent by weight. The result of water absorption shows that the samples BM, B10 and B20 have absorption under standard value and hence acceptable. But the rest of the samples have a greater amount of absorption. Table-3.5 and Figure-3.7 show the comparison of initial and final weight and percentage of water absorption respectively.
-
According to IS: 3495(Part-3)-1992, When there is no perceptible deposit, efflorescence is NIL, but there is slight efflorescence when 10% of exposed area has
thin deposit of salts. In our specimens, samples with 0, 10 and 20% sludge have nil efflorescence but the rest have slight efflorescence (Table-3.3).
-
A brick is sound only if it does not break and ringing sound is produced. The bricks with 10% and 20% sludge are quite sound and can be used for construction (Table-3.4).
-
According to Indian standards, the samples with greater pH have low risk of corrosion. So, all our samples have pH greater than 7 and thus are less prone to corrosion. Table-3.6 & Figure-3.8 above shows chart of pH value of different samples at different days.
-
The thermal conductivity of the brick decreases due to the presence of TPIS, which has low thermal conductivity. In the long run, it can attract the potentials for development most tropical areas where desirable of low thermal conductivity construction materials to optimize the load of cooling or heating within the space of the building(Table-3.8 & Figure-
3.10 a&b).
-
When compared to BM i.e. 0% sludge, we see that bricks of B10 and B20 both have almost same hardness which is near to BM and thus are acceptable.
-
Dimensional, shape & size accuracy is better as required for class-I bricks upto 20% replacement.
11. Bricks with waste have better micro-structure particle matrix showing better binding & strength as is evident from Figure-3.6.
-
-
CONCLUSION
After the experimental investigation of use of toothpaste sludge in following conclusions were made: According to the obtained test results & specific findings with respect to concrete and fired clay bricks developed in this study lead to the following final conclusions:
-
Wastocrete: Sand content in the concrete can be reduced by 15% as suggested by the present study. This will help the environment from excessive exploitation of natural resources.
-
Wastoricks: The bricks so developed by replacing clay by 20% with TPIS directly save the top fertile soil by 20%. This will help the environment from excessive exploitation of natural resources. Being low thermal conductivity construction materials it is beneficial to optimize the load of cooling or heating within the space of the building.
-
Also new concrete & brick mix have been developed with non-bio degradable waste material; TPIS. This will also help the safe disposal of non-biodegradable waste.
-
Since the industrial waste can be utilized locally or adjacently by adopting outcomes of present research, hence there are more chances of it being implemented or adopted practically.
REFRENCES
-
Abhishek Jain ,(2013) Use of Fly ash as Partial Replacement of Sand in Cement, International Journal of Innovative Research in Science, Engineering and Technology Vol. 2, Issue 5, pp. 1323-1332.
-
Akshay C. Sankh, (2014) Recent Trends in Replacement of Natural Sand With Different Alternatives, IOSR Journal of Mechanical and Civil Engineering e-ISSN: 2278-1684, p-ISSN: 2320-334X PP 59-66.
-
Bilgin, N., Yeprem, H. A., Arslan, S., Bilgin, A., Günay. E., and arsoglu, M. (2012). Use of waste marble powder in brick industry Construction and Building Materials, Vol. 29, pp. 449457.
-
Jayeshkumar Pitroda,L.B.Zala ,F.S.Umrigar (2013) Innovative Use of Paper Industry Waste (Hypo Sludge) in Design Mix Concrete, International Journal of Advanced Engineering Technology /Vol. IV/ Issue I/Jan.-March., /31-35
-
McKinsey & Co, (2009), Environmental and Energy Sustainability: An Approach for India.
-
Monica C. Dhoka , (2013), Green Concrete: Using Industrial Waste of Marble Powder, Quarry Dust and Paper Pulp, International Journal of Engineering Science Invention Volume 2 Issue 10, pp. 67-70.
-
Sameer Maithe, (2013), Final Report on Evaluating Energy Conservation Potential of Brick Production in India, SAARC Energy Centre,
Greentech Knowledge Solutions Pvt Ltd., New Delhi
-
Shakir Alaa. A. , Siva kumar Naganathan, Kamal Nasharuddin Bin Mustapha, (2013), Development of Bricks from Waste material: A Review Paper, Australian Journal of basic and Applied Sciences, vol.7(8), pp. 812-818.
-
Vaishali Sahu , V. Gayathri, (2013), The Use of Fly Ash And Lime Sludge as Partial Replacement of Cement in Mortar, International Journal of Engineering and Technology Innovation/vol. 4, no. 1,pp. 30- 37.
-
United Nations Environment Program (UNEP) Report, (2010), Greening Cement Production has a Big Role to Play in Reducing Greenhouse Gas Emissions, published in UNEP Global Environmental Alert Service (GEAS), www.unep.org/ GAES/.
-
United Nations Environment Program (UNEP) Report, (2014), Sand- rarer than one thinks, published in UNEP Global Environmental Alert Service(GEAS), www.unep.org/GAES/.
-
Weng, C. H., Lin, D. F., and Chiang. P. C. (2003). Utilization of sludge as brick materials. Advances in Engineering Research, Vol.7, pp. 679- 685.
Abbreviations
TPIS: Toothpaste Industrial waste; Wastoncrete: Concrete from toothpaste industry waste
Authors Contribution
Kanwar being supervisor for this research planned the overall methodology, outlined the procedure & concept and improved the ICA method and programmed its algorithm for the analysis used in the research. All the test were conducted in the Civil Engineering Department of Chitkara University . Kanwar and Vashisht conducted experimental studies, outlined the structure of the paper and drafted the manuscript. All the participated in the review and verification of the proposed methods in this paper and drafting the manuscript. All authors read and approved the final manuscript.
Author Details
1 Vice Chancellor, Chitkara University and Professor, Civil Engineering Department, Atal Shiksha Kunj-Kalujhanda, Baddi District-Solan Himachal Pradesh, INDIA ,PIN 174103,vc@chitkarauniversity.edu.in 2 Research Scholar for Ph.D in Department of Civil Engineering and Superintending Engineer-HIMUDA, Dharamshala, Himachal Pradesh, INDIA
,PIN 176215,
Acknowledgements
This research is financially supported by himcoste.
Competing Interests
The authors declare that they have no competing interests.