
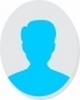
- Open Access
- [post-views]
- Authors : Ananthula Sandeep , Kudaru Ujwal
- Paper ID : IJERTV12IS030208
- Volume & Issue : Volume 12, Issue 03 (March 2023)
- Published (First Online): 06-04-2023
- ISSN (Online) : 2278-0181
- Publisher Name : IJERT
- License:
This work is licensed under a Creative Commons Attribution 4.0 International License
Wave Spring in DTH Hammers
Ananthula Sandeep[1], Kudaru Ujwal [2] [2]National Institute of Technology Delhi
Abstract:- Down-the-hole (DTH) Hammers are used in vertical drilling applications, which involve drilling holes for the bore wells and extraction in the oil natural gas industry and many other industrial applications that operate at higher speeds and pressure. The components in the Hammer are designed to overcome specific high forces and rates depending on their Applications. Out of all the elements in the Hammer, the spring plays a crucial role in allowing high-pressure compressed air into the Hammer so we can drill the hole. A helical spring is used in Regular DTH Hammers to guide the movement of the check valve. To replace the helical spring, a Wave spring is developed, which reduces the axial space, improves the cost efficiency, and helps in better performance of the Hammer. Wave spring depends on factors like Load, Number of waves, Number of turns, Working Height, etc. A new wave spring is designed by considering the above parameters. Structural analysis has been done to prove that wave springs can replace Helical springs in DTH hammers for vertical drilling.
Key Words: DTH Hammer, Wave spring, Helical spring, Deformation, Analysis
INTRODUCTION
DTH hammers are also known as pneumatic down-the-hole hammers, which are vastly used in drilling deep holes for bore wells and for the exploration of petroleum and geological cores, along with extractions in the oil and natural gas industries. In conventional DTH drilling, the Hammer is usually fixed onto the bottom of the drill string, which provides motion to the Hammer by sending rotational torques and axial pressures[1]. Compressed air enters the Hammer by releasing check valve with the help of a Helical spring. The action of converting pressure into kinetic energy of the piston takes place along with the transfer of impact energy onto Bit, which provides a path for drilling and breaking rocks. All the power conversions and the Hammer's working occur if the check valve is opened fully. This is only possible when the spring is compressed by maintaining its specific stiffness[2]. Although the helical spring provides proper deflections, there has been damage to it during the drilling process, which has become a severe problem for DTH hammers. This can be rectified if the spring model is drafted correctly, or we can also try to change the spring type, which has added advantage
compared to a helical spring. One such adjustment is the introduction of Wave spring into DTH Hammer.
Fig1.Application of Wave spring in Earth breakers[3] |
The wave spring concept was introduced way back two decades. Wave springs are compression springs made up of flat rectangular wire[2] rather than circular ones. Due to the increased ease of manufacturing and technology, it can be manufactured easily by coiling on the edges, known as edge winding.
The appearance of the spring itself is enough for its naming as it contains multiple waves per turn rather than a plane face. Wave springs come in different types. It provides the same spring rate as any traditional spring could offer but with a reduction of the operating height and, therefore, the assembly height. Significant cost savings can be done with smaller measurements.
With the increasing ease of manufacturing nowadays, it is being used in many applications, which include aeronautical[4], Rockets, Preload bearings, Automobiles, and many more, where axial space can be reduced for better performance and efficiency. DTH hammers are provided with highly compressed air and heavy torques. Their values depend on the type of application it is being used, whether it is drilled in the soft or hard formation rock, and the kind of bit face we use for the drilling process. Considering all these parameters, we have designed and analyzed a wave spring suitable for a DTH hammer.
MODELING OF WAVE SPRING
Fig 3. Crest to trough wave spring[4] |
To design a wave spring, we have to consider specific parameters, including the Number of waves, Number of turns, Working height, and thickness of the coil[4]. The operating stress of the spring also plays a prominent role in designing a spring. To develop a wave spring, first, we have to decide the thickness of the rectangular coil.
To decide the thickness of the wave spring, we have Compared the cross sections of Round and Rectangular beams, which lie at the heart of the contact spring. The equations for the cantilever beam with round and rectangular cross-sections paved the way to determine the thickness of the spring.
3E . t rectangular = 2. L2 |
(1) |
3E . D round = 2. L2 |
(2) |
E. w. t3 Frectangular = 4. L3 |
(3) |
3E. D4 Fround = 64. L3 |
(4) |
Here Represents the stress acting on the beam, E is the material's elastic modulus, and L refers to the length of the beam. In our discussion, it is referred to as the length of a single coil in the spring, is the deflection, t is the thickness of the rectangular strip, and d is the Diameter of the round wire which is also the wire diameter for our spring
Fig 4.Rectangular cross-section Beam |
Fig 5.Round Cross-section Beam |
Fig 2 .Schematic diagram of DTH hammer with Helical Spring |
Figure 4 above defines the terms used in the following discussion. To determine the thickness of the wave spring, contact force comes into play because as the contact force area increases, stress on the materials would decrease, and ultimately the component can be designed for greater loads. The equations that are used to calculate the maximum surface stress for the above beams are mentioned.
To determine the thickness of the spring, we have the value of contact force, which is the amount of pressure the hammer receive. It is nearly equal to 500 psi that is converted in terms of newton for the force calculations. Contact force is directly proportional to the area moment of inertia which is directly proportional to the Diameter of the wire for the round cross- section and thickness for the rectangular cross-section. If the Diameter and thickness are identical, then the contact force of a rectangular beam would be 70% more than a circular cross- section; subsequently, the stress would be reduced on the material, so to maintain the same contact force, thickness can
be reduced to 60% of diameter of round wire and along with its width can also be controlled in the cross-section of the rectangle as long as the width of the rectangle is at least 58.9% of thickness it would be an advantage to eliminate the round cross-section. Considering the above conditions, we have designed a proper rectangular coil wire suitable for DTH hammers. To increase the efficiency and strength of the flat wire, waves are introduced in the flat coil such that the bending stress comes into action more than the torsional stress and allows the spring to provide fewer deflections, creating more significant time delays, and stiffness would be increased accordingly. Rather than a Flat face, a curved face would give usbetter results
b
P
L
Fig6. Bending behaviour of rectangle strip
Stress for the flat and curved beams can be calculated by using the following equations. Out of all the values from the equations, we can find the stress value for the curved face, which would give us the stress and wave springs.
6Et Bending Stress = L2 |
(5) |
SL2 Deflection = = 6Et |
(6) |
2Sbt2 Load = 3L |
(7) |
3 = 422 |
(8) |
Another critical parameter for the design of a Wave spring is operating stress, whose value should be maintained at 50 % of the minimum tensile strength of the material. Usually, in DTH Hammers, springs are made from a spring steel material with a minimum tensile strength of 430- 540 MPa. This would help determine the wave spring's number of waves per coil.
Substituting the spring's thickness, Load, Stress, and Diameter, we can calculate the number of waves per spring turn. wave springs designed for DTH hammers should include spring rate, deflection, Diameter, width, and height. These five spring parameters have to be selected to meet the requirements.
There is a formula to measure the deflection and, subsequently, the stiffness of the spring along with it. For that, we require a number of waves which can be achieved by calculating through the above stress formulas, or an analysis method could also pave the way. In DTH hammers, we have been using a Helical spring for the hammers. An existing Helical spring in a Hammer series is taken as a reference, and a new wave spring is designed to replace the helical spring in the Hammer. The first constraint we are considering is the Working height of the spring. Introducing a wave spring can eliminate 50% of the height for the same stiffness as a helical spring. To eliminate the helical spring, we
8 3 = = 4 |
(9) |
4 = = = 83 |
(10) |
must find its deflection and spring rate in the DTH hammer, which can be calculated using the following formulas.
Fig7. Helical spring Model |
Where F is the Load applied on the spring in newton, D is the Diameter of the spring, N represents the number of turns, G is the Rigidity modulus, and d will be the wire diameter by calculating the above formulas with the available values of the spring which is being used in the DTH hammer. A design model for the helical spring is made in CREO SOFTWARE, which helps design, draft, and dimension the components.
After designing the model, an analysis is conducted on the helical spring in the ANSYS software to get the analytical value for the deformation by giving pressure load onto the spring in which the DTH hammer is operated. Certain constraints like mesh size and faces on which force is applied were considered, and the same analysis was later conducted on wavy spring by taking these parameters into reference. Analysis has been done on the spring by varying mesh sizes, and the nearest theoretical deformation value was achieved at 1.8mm mesh size, which has significantly less error.
Fig8. Deformation Analysis of Helical spring |
DESIGN AND ANALYSIS OF WAVE SPRING
Helical spring deformations and parameters have been noted, and accordingly, a wave spring is designed for the same parameters. The dimensions of the wave spring are calculated using the above formulae. The parameters like height and Diameter of wave spring are considered by taking the helical spring into reference. The height of the wave spring is reduced to half the height of the helical spring, and a design of it is made in the CREO software
Fig11.Wave spring with 3.5 waves |
by using specific formulas and parameters like the number of waves per turn and the number of turns.
r=id/2 |
(11) |
Theta = t x 360 x turns |
(12) |
Z= t x height |
(13) |
Helical curves are drawn in a cylindrical coordinates system, which is driven by equations
sd5=(((height/turns)-sd4)/2) *cos(trajpar*360*turns*(waves)) |
(14) |
sd4 = thick |
Where r is the radius of the curve id and od are outer and inner Diameters, respectively, and theta is the angle at which the curve rotates, representing the number of coils, t is the thickness, and height is the spring height. Using all the above equations, a curve is generated, and to give the wave structure to the coil, a helical sweep feature is selected and a rectangle with the desired thickness and breadth is drawn and swept throughout the curve surface. To guide the rectangular section in the waveform, a formula is given in the relations, which defines the wave structure and path of the section to sweep
Fig9.Wave Spring with 2.5 waves |
After giving these formulas, we can alter the number of waves, thickness, and height of the spring by changing the values in the parameters section. All the wave springs are designed accordingly for 2.5,3.5, and 4.5 waves and a height of 60 mm with a thickness of 1.7mm, and they are analyzed to attain the deformation values.
0.25
0.2
0.15
0.1
0.05
0
Deformation(mm) |
Fig12.Deformations of spring respective to turns(3.5 waves) |
3.5 waves
13 14 15 16 17
Number of turns
Deformation (mm) |
Fig10 Deformations of spring respective to turns(2.5 waves) |
Theoretical values for different number of turns have been done for spring which is containing 2.5 waves and the graph for the deflected values give us clear idea of their behaviour
2.5 waves
Analysis of the wave spring is done in the Ansys where the model created in Creo is exported in it and the properties of material is given in the engineering data column and static structural analysis have been done the spring ,By fixing one of the ends and applying pressure on the other end a Finite analysis on each and every node which are formed by meshing of the spring with a suitable mesh size of 1.8mm .Deformations for the wave spring spring were obtained theoretically and they are compared with helical springs
1
0.8
0.6
0.4
0.2
0
13 14 15 16 17
Number of turns
Fig13.Wave spring with 4.5waves |
Deflection(mm) |
Fig14.Deformations of spring respective to turns(4.5 waves) |
Deflection(mm) |
Fig15 .Changes in deflection with increase in number of waves |
Theoretical deflection of wave spring
0.7
0.6
0.5
0.4
0.3
0.2
0.1
0
2.5 3.5 4.5
Number of waves
Deflection(mm) |
Fig16 .Changes in deflection with increase in number of turns |
Helical Spring deflection
0.09
0.08
0.07
0.06
0.05
0.04
0.03
0.02
0.01
0
4.5 waves
30
25
20
15
10
5
0
13 14 5 16 17
Number of turns
13
Num
14 15 16 17
f Turn
By considering all the above graphs and deflection values for
ber o s
different number of turns of the waves a new wave spring can be designed for DTH hammer. To eliminate the existing helical spring we are considering a wave spring with 13 turns and 2.5 waves which is analysed in the ANSYS for its deformation
Results
The values of deformations for the helical spring and wave spring are compared with the help of graph and the results showed that the wave spring provides less deflection compared to helical spring that to with 50% reduction of height and since deflections are small consequently stiffness would be more and elastic property of the spring is providing a better movement of spring and check valve in the DTH Hammer is released with ease which also reduces the axial space with which we can also reduce the assembly size and the cost of the manufacturing can be reduced subsequently which is advantage for the DTH hammers
Fig17.Analysis of wave spring for 2.5 waves in a turn |
The deflections for the Helical and wave spring are quite different which proved us that a wave spring is useful in DTH hammer and it can also reduce the assembly cost which makes it a better replacement for helical spring
Waves spring (vs) Helical spring
23.13
24.64
30
18.6
20.11
21.62
0.79 |
||||
0.744 |
||||
0.604 |
0.6514 0.697 |
25
20
15
10
Deflection(mm)
5
0
13 14 15 16 17
Number of turns
Wave spring Helical spring
Fig18.Comparison of helical and wave spring
FUTURE SCOPE :
A Design model for the wave spring for different number of wave springs is provided by taking it reference, analysis can be conducted on the wave spring by altering number of waves and the results would be helpful to develop new wave springs for different applications .If the dimensions of the elements in the DTH hammer associated with spring are known accurately it will give rise to the new size of the elements in hammer which will enable us to know the performance of the Hammer and it can be used for different Hammer series in DTH, Proper analysis on the assembled part of the wave spring with hammer would also be beneficial
REFERENCES
[1] Z. Zhao, Y. Meng, Y. Li, X. Shi, and C. Xiang, Effects of Working Angle on Pneumatic Down-the-hole Hammer Drilling, Rock Mech. Rock Eng., vol. 48, no. 5, pp. 21412155, 2015, doi: 10.1007/s00603-014-0667-9. [2] E. Dragoni, A contribution to wave spring design, J. Strain Anal. Eng. Des., vol. 23, no. 3, pp. 145153, 1988, doi: 10.1243/03093247V233145. [3] P. M. Wave and S. Applications, Wave Spring Applications, pp.2932.
[4] R. W. Steele, Ask the expert wave spring FAQ, Pediatr. Nephrol., vol. 8, no. 3, p. 269, 1994.